Home>Finance>Backflush Costing: Definition And How System Works For Inventory
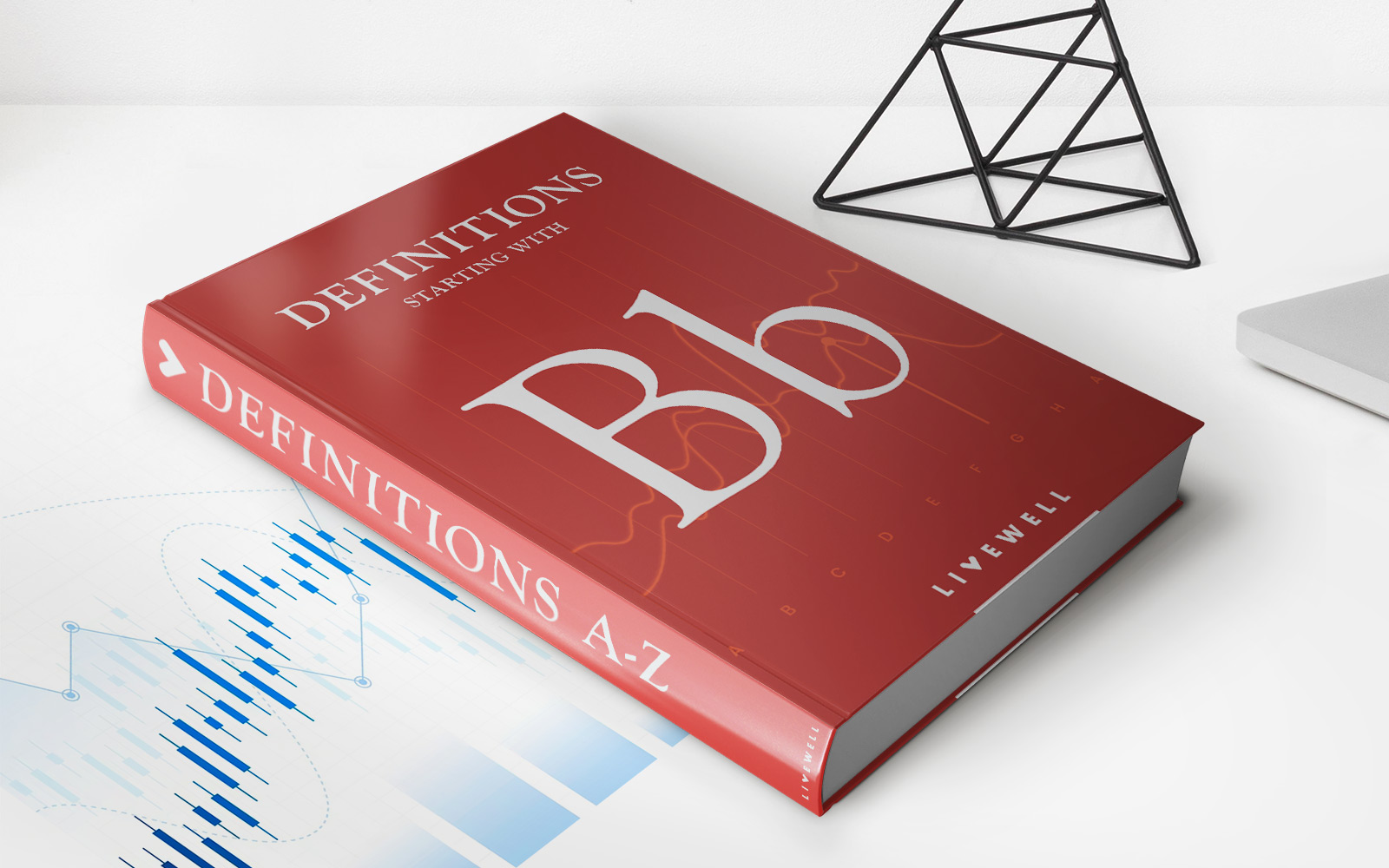
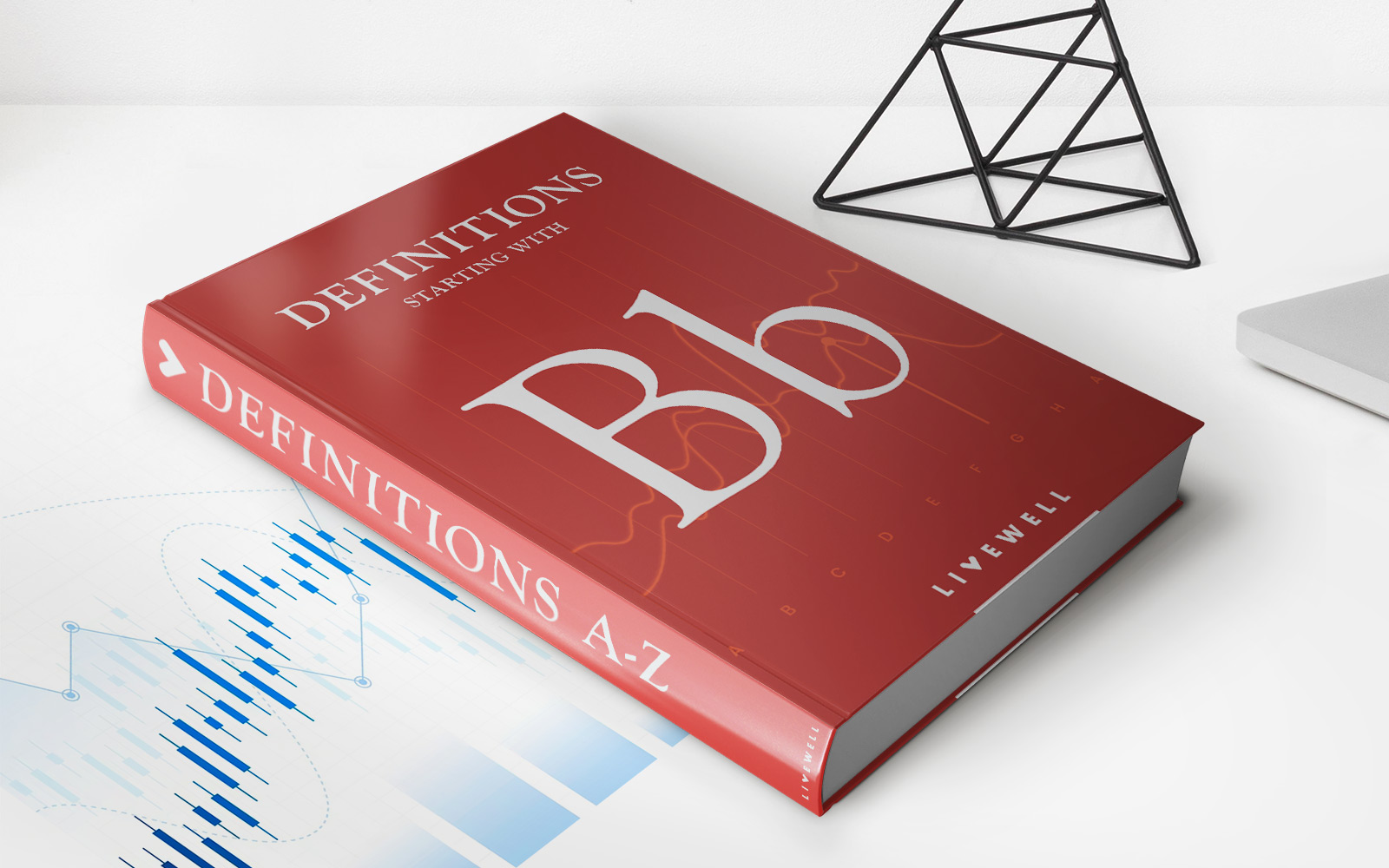
Finance
Backflush Costing: Definition And How System Works For Inventory
Published: October 12, 2023
Learn what backflush costing is in finance and how it works for inventory management. Get a clear definition and understanding to optimize your costing system.
(Many of the links in this article redirect to a specific reviewed product. Your purchase of these products through affiliate links helps to generate commission for LiveWell, at no extra cost. Learn more)
Managing Inventory Costs with Backflush Costing
When it comes to managing inventory costs, businesses often find themselves searching for efficient and accurate methods. One such method is backflush costing, which provides a streamlined approach to accounting for inventory and cost control. In this article, we will delve into the definition of backflush costing and explore how this system works in managing inventory.
Key Takeaways:
- Backflush costing: A cost accounting method that eliminates the need for detailed inventory tracking by allocating costs directly to finished goods.
- Key Benefits: Streamlines accounting processes, reduces administrative tasks, and minimizes errors associated with inventory tracking.
Understanding Backflush Costing
Backflush costing is a cost accounting method that focuses on simplicity and efficiency. Instead of individually tracking and recording the costs associated with each component of the production process, backflush costing allocates costs directly to the finished goods. This eliminates the need for detailed inventory tracking and manual input of cost data.
The backflush costing system operates on a predetermined trigger, such as the sale of finished goods or a specific time period. When the trigger occurs, the system utilizes a predetermined bill of materials and standard costs to calculate the costs associated with the production. These costs are then allocated directly to the finished goods, bypassing the need for individual tracking of materials and labor.
How Backflush Costing Works for Inventory
Implementing a backflush costing system for inventory management involves several key steps:
- Establishing standard costs: Determine the standard costs for each of the components required to produce the finished goods. These costs include materials, labor, and overhead.
- Creating the bill of materials: Develop a detailed bill of materials that outlines the quantity and cost of each component required for the production process.
- Setting triggers: Identify the triggers that will initiate the backflush costing system. This could be the sale of finished goods, reaching a specific production milestone, or a predefined time period.
- Calculating costs: When the trigger occurs, the system automatically calculates the costs based on the standard costs and bill of materials. These costs are then allocated directly to the finished goods in the accounting system.
- Review and analysis: Regularly review and analyze the results of the backflush costing system to ensure accuracy and efficiency, making any necessary adjustments to standard costs or the bill of materials.
Key Benefits of Backflush Costing
Implementing a backflush costing system can bring several benefits to businesses:
- Streamlined accounting processes: Backflush costing eliminates the need for detailed inventory tracking and manual entry of cost data, simplifying the accounting process.
- Reduced administrative tasks: With backflush costing, businesses can save time and resources by minimizing administrative tasks associated with inventory management.
- Minimized errors: Manual tracking of inventory can lead to errors and discrepancies. Backflush costing eliminates these errors by automating the cost allocation process.
The use of backflush costing provides an efficient and accurate method for managing inventory costs. By streamlining accounting processes, reducing administrative tasks, and minimizing errors, businesses can optimize their inventory management systems and focus more on strategic decision-making.