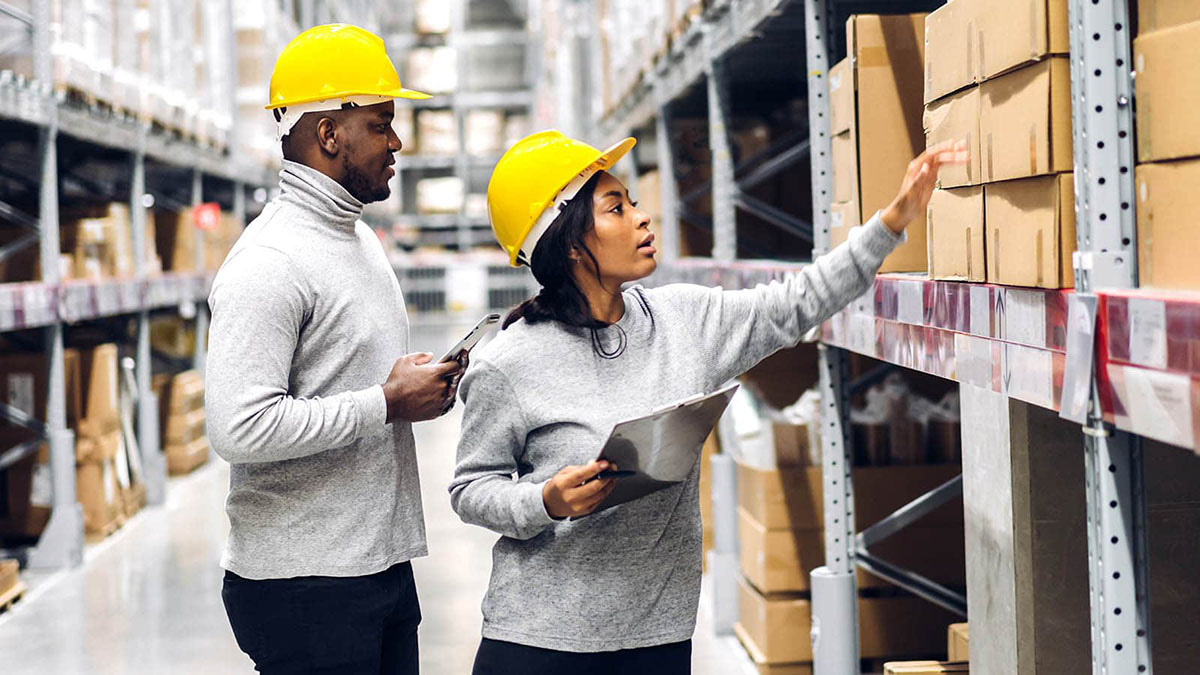
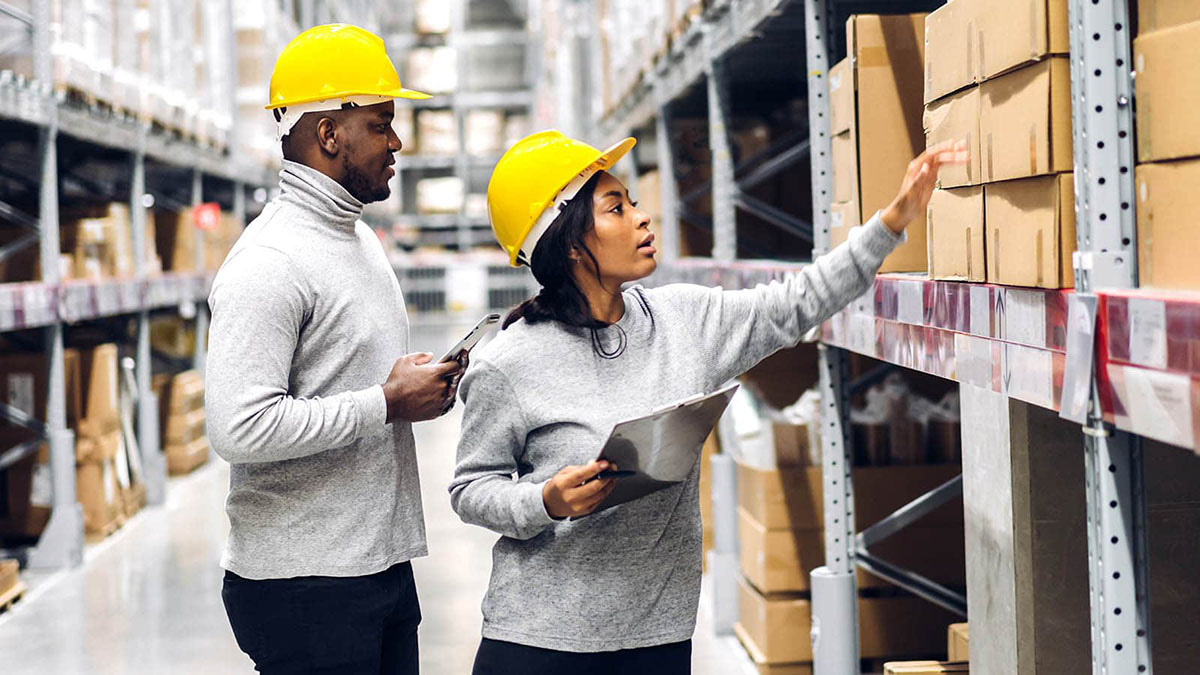
Finance
What Are Supply Chain Metrics?
Published: October 19, 2023
Learn how finance professionals use supply chain metrics to optimize operations and drive profitability. Explore key performance indicators and best practices in supply chain finance.
(Many of the links in this article redirect to a specific reviewed product. Your purchase of these products through affiliate links helps to generate commission for LiveWell, at no extra cost. Learn more)
Table of Contents
- Introduction
- Definition of Supply Chain Metrics
- Importance of Supply Chain Metrics
- Types of Supply Chain Metrics
- Key Performance Indicators (KPIs) in Supply Chain Metrics
- Benefits of Using Supply Chain Metrics
- Challenges in Implementing Supply Chain Metrics
- Best Practices for Measuring Supply Chain Performance
- Conclusion
Introduction
Welcome to the world of supply chain metrics! In the ever-evolving field of finance, understanding and effectively measuring the performance of your supply chain is crucial for success. Supply chain metrics provide valuable insights into the efficiency, effectiveness, and overall health of your supply chain operations.
But what exactly are supply chain metrics? Simply put, they are quantifiable measurements that help organizations track and analyze various aspects of their supply chain performance. These metrics provide a clear and objective view of critical processes, enabling businesses to identify areas for improvement, make informed decisions, and optimize their supply chain operations.
As the world becomes increasingly connected and complex, supply chain metrics have become an indispensable tool for organizations of all sizes across different industries. From manufacturing and logistics to retail and finance, every sector relies on a well-structured supply chain to deliver products and services to customers efficiently and cost-effectively.
By implementing effective supply chain metrics, companies can identify bottlenecks, streamline processes, reduce costs, and enhance customer satisfaction. These metrics go beyond the simple monitoring of outputs and instead focus on measuring key aspects such as quality, delivery time, cost, and customer service, among others.
With a wealth of data available at our fingertips, it’s more important than ever to harness the power of supply chain metrics to gain a competitive edge in the market. Organizations that effectively leverage these metrics can optimize their supply chain performance, enhance their bottom line, and position themselves as industry leaders.
However, it’s important to note that supply chain metrics are not a one-size-fits-all solution. Each organization’s supply chain is unique, and therefore, the metrics used to measure its performance may vary. It is crucial to identify the right metrics that align with your specific business goals, industry requirements, and customer expectations.
In the following sections, we will delve deeper into supply chain metrics, exploring their types, key performance indicators (KPIs), benefits, challenges, and best practices for measuring supply chain performance. So join us as we embark on this journey to unlock the power of supply chain metrics and revolutionize your business operations.
Definition of Supply Chain Metrics
Supply chain metrics are specific measurements that organizations use to evaluate and assess the performance of their supply chain operations. These metrics provide quantitative data and insights into various aspects of the supply chain, allowing businesses to track and monitor key performance indicators (KPIs) and make data-driven decisions.
At its core, supply chain metrics focus on measuring and analyzing different aspects of the supply chain, including inventory management, production efficiency, order fulfillment, transportation costs, customer satisfaction, and much more. These metrics not only help organizations understand how well their supply chain is performing but also pinpoint areas for improvement and identify opportunities for optimization.
Supply chain metrics can include a wide range of measurements, depending on the specific needs and goals of the organization. Some common examples of supply chain metrics include:
- Inventory Turnover: This metric measures how quickly a company’s inventory is being sold or used during a specific period. It provides insights into inventory management efficiency and the overall effectiveness of supply chain operations.
- Order Cycle Time: The order cycle time measures the time it takes for a customer order to be fulfilled, from the moment the order is placed until it is delivered to the customer. This metric helps identify bottlenecks in the order fulfillment process and improve customer satisfaction.
- On-Time Delivery: This metric measures the percentage of customer orders that are delivered on time. It reflects the reliability and effectiveness of the organization’s delivery process and its ability to meet customer expectations.
- Cost per Order: This metric calculates the average cost associated with processing and fulfilling a customer order. It helps organizations identify cost-saving opportunities and optimize their supply chain expenses.
- Perfect Order Rate: The perfect order rate measures the percentage of orders that are delivered without any errors or issues. It considers factors such as accuracy, completeness, and condition of the delivered products, as well as the timeliness of the delivery. This metric is crucial for assessing customer satisfaction and identifying areas for improvement.
These are just a few examples of the numerous supply chain metrics that organizations can utilize. The specific metrics employed will depend on the organization’s industry, business objectives, and the specific areas of the supply chain they wish to evaluate.
By regularly monitoring and analyzing these metrics, organizations can gain valuable insights into their supply chain operations, identify patterns and trends, and make informed decisions to optimize performance and enhance overall efficiency. Supply chain metrics play a vital role in driving continuous improvement and helping businesses stay competitive in an increasingly complex and dynamic marketplace.
Importance of Supply Chain Metrics
Supply chain metrics play a crucial role in the success and profitability of organizations across all industries. They provide valuable insights into the performance of the supply chain, enabling businesses to make data-driven decisions, identify areas for improvement, and optimize their operations. Here are some key reasons why supply chain metrics are of utmost importance:
1. Performance Evaluation:
Supply chain metrics allow organizations to evaluate the performance of their supply chain operations objectively. By measuring key performance indicators (KPIs) such as on-time delivery, inventory turnover, and order cycle time, businesses can assess how well their supply chain is functioning and identify areas that require attention or improvement. This evaluation facilitates the identification of bottlenecks, inefficiencies, and areas for optimization, ultimately leading to enhanced performance and customer satisfaction.
2. Informed Decision-making:
Supply chain metrics provide organizations with accurate and reliable data, helping them make informed decisions. By analyzing metrics related to product quality, delivery time, transportation costs, and other critical aspects, businesses can gain insights that drive strategic decision-making. For example, if a company identifies a high transportation cost metric, they can explore alternative transportation methods or negotiate better rates with carriers. These metrics enable organizations to take proactive measures to reduce costs, improve efficiency, and maintain a competitive edge in the marketplace.
3. Continuous Improvement:
Supply chain metrics are essential for driving continuous improvement within the supply chain process. By consistently monitoring and analyzing these metrics, organizations can identify trends and patterns, spot areas for improvement, and implement targeted measures to enhance performance. Whether it’s reducing lead times, increasing order accuracy, or streamlining inventory management, supply chain metrics provide the necessary insights to implement process improvements and drive efficiency gains.
4. Cost Optimization:
Supply chain metrics enable organizations to identify cost-saving opportunities and optimize their supply chain expenses. By measuring metrics such as cost per order, transportation costs, and inventory carrying costs, businesses can identify inefficiencies and take corrective actions. For instance, if a company’s inventory turnover ratio is low, they can implement strategies to reduce excess inventory and associated carrying costs. This approach allows organizations to streamline their operations, eliminate waste, and improve profitability.
5. Enhanced Customer Satisfaction:
Supply chain metrics directly impact customer satisfaction. By monitoring metrics such as on-time delivery, perfect order rate, and order fulfillment time, organizations can ensure that they meet and exceed customer expectations. Customers value timely and accurate deliveries, and by measuring these metrics, organizations can identify areas where they may be falling short. By focusing on improving these aspects, organizations can enhance their reputation, build customer loyalty, and drive repeat business.
In summary, supply chain metrics are crucial for organizations looking to optimize their supply chain operations. By measuring and analyzing key performance indicators, businesses can evaluate their performance, make informed decisions, drive continuous improvement, optimize costs, and enhance customer satisfaction. Leveraging the power of supply chain metrics is a strategic approach that helps organizations stay competitive, improve efficiency, and achieve long-term success in today’s dynamic business landscape.
Types of Supply Chain Metrics
Supply chain metrics encompass a wide range of measurements that organizations use to evaluate the performance of their supply chain operations. These metrics can be categorized into different types, each focusing on specific aspects of the supply chain. Understanding the different types of supply chain metrics can help businesses gain a comprehensive view of their operations and identify areas for improvement. Here are some key types of supply chain metrics:
1. Cost Metrics:
Cost metrics are focused on measuring the expenses associated with supply chain operations. These metrics help organizations track and analyze costs related to transportation, warehousing, inventory management, and procurement. Examples of cost metrics include cost per order, transportation costs as a percentage of sales, inventory carrying costs, and total landed cost. By monitoring these metrics, businesses can identify cost-saving opportunities, implement cost reduction strategies, and enhance the overall cost efficiency of their supply chain.
2. Time Metrics:
Time metrics measure the speed and efficiency of supply chain processes. These metrics are essential for monitoring the time taken to perform critical activities within the supply chain, such as order fulfillment, delivery, and production cycles. Examples of time metrics include order cycle time, lead time, delivery time variability, and production cycle time. By tracking these metrics, organizations can identify bottlenecks, reduce lead times, improve responsiveness, and enhance overall operational efficiency.
3. Quality Metrics:
Quality metrics focus on measuring the accuracy, reliability, and effectiveness of supply chain processes. These metrics play a crucial role in ensuring that products and services meet or exceed customer expectations. Examples of quality metrics include perfect order rate, product return rate, customer complaints, and defective products per million opportunities (DPMO). By monitoring these metrics, organizations can identify areas for improvement, implement quality control measures, and enhance customer satisfaction through consistent and reliable product and service delivery.
4. Inventory Metrics:
Inventory metrics are used to measure the efficiency and effectiveness of inventory management within the supply chain. These metrics help organizations strike a balance between ensuring product availability and minimizing excess inventory costs. Examples of inventory metrics include inventory turnover, days sales of inventory (DSI), stockout rate, and carrying cost of inventory. By tracking these metrics, organizations can optimize inventory levels, reduce carrying costs, avoid stockouts, and improve overall inventory management practices.
5. Service Metrics:
Service metrics focus on the level of customer service provided by the supply chain. These metrics help organizations evaluate their ability to meet customer demands and expectations. Examples of service metrics include on-time delivery, fill rate, order accuracy, and customer satisfaction score. By monitoring these metrics, organizations can identify areas where service levels can be improved, enhance the overall customer experience, and build long-term customer loyalty.
It’s important to note that these are just some examples of the types of supply chain metrics that organizations can utilize. The specific metrics employed will depend on the organization’s industry, business objectives, and the specific areas of the supply chain they wish to evaluate. By utilizing a combination of these metrics, businesses can gain a comprehensive understanding of their supply chain’s performance and make informed decisions to drive improvements and achieve operational excellence.
Key Performance Indicators (KPIs) in Supply Chain Metrics
Key Performance Indicators (KPIs) are specific metrics that help organizations assess their performance and progress towards achieving their strategic goals. In the context of supply chain metrics, KPIs play a critical role in measuring and monitoring performance levels. They provide businesses with quantifiable data and benchmarks to evaluate the effectiveness and efficiency of their supply chain operations. Here are some key KPIs commonly used in supply chain metrics:
1. On-Time Delivery:
On-time delivery measures the percentage of orders that are delivered to customers within the agreed-upon timeframe. It is an essential KPI for assessing the reliability and responsiveness of the supply chain. Organizations strive for high on-time delivery rates to meet customer expectations, maintain satisfaction, and build strong relationships with customers.
2. Order Fill Rate:
Order fill rate measures the percentage of customer orders that are fulfilled completely from available stock. It reflects the organization’s ability to meet customer demand and optimize inventory levels. A high order fill rate indicates efficient inventory management and a well-functioning supply chain.
3. Inventory Turnover:
Inventory turnover is a critical KPI that measures how quickly a company’s inventory is being sold or used within a specific period. It indicates the efficiency of inventory management and the ability to balance stock levels with customer demand. A high inventory turnover ratio signifies effective inventory control and cost optimization.
4. Perfect Order Rate:
The perfect order rate measures the percentage of orders that are fulfilled without any errors or issues. It takes into account factors such as accuracy, completeness, on-time delivery, and condition of the delivered products. A high perfect order rate indicates a highly efficient and reliable supply chain that consistently meets customer expectations.
5. Supply Chain Cycle Time:
Supply chain cycle time measures the time it takes for a product to move through the entire supply chain, from initial order placement to delivery to the customer. It includes order processing, manufacturing, transportation, and any other relevant activities. Monitoring supply chain cycle time helps identify potential bottlenecks and inefficiencies, allowing organizations to streamline processes and improve overall speed and responsiveness.
6. Transportation Costs as a Percentage of Sales:
This KPI measures the percentage of sales revenue that is spent on transportation costs. It provides insights into the efficiency and cost-effectiveness of transportation operations within the supply chain. Monitoring this metric helps organizations identify cost-saving opportunities and optimize transportation expenditure.
These are just a few of the many KPIs that organizations use to gauge and monitor their supply chain performance. The specific KPIs employed can vary depending on the nature of the business, industry, and strategic goals. It’s important for organizations to carefully select and track KPIs that align with their objectives and provide meaningful insights into their supply chain operations.
By regularly measuring and analyzing these KPIs, organizations can identify areas of improvement, monitor progress towards goals, and make data-driven decisions to optimize their supply chain performance. These KPIs act as valuable benchmarks, helping organizations drive continuous improvement and enhance their competitiveness in the marketplace.
Benefits of Using Supply Chain Metrics
Implementing supply chain metrics offers a multitude of benefits for organizations across various industries. These metrics provide valuable insights into the performance and efficiency of supply chain operations, enabling businesses to make informed decisions and drive continuous improvement. Here are some key benefits of using supply chain metrics:
1. Data-Driven Decision Making:
Supply chain metrics provide organizations with objective and accurate data that can be utilized to make informed decisions. By analyzing the metrics, businesses can identify trends, patterns, and areas for improvement. Data-driven decision-making helps optimize processes, reduce costs, and enhance overall supply chain performance.
2. Performance Evaluation and Monitoring:
Supply chain metrics enable organizations to evaluate and monitor the performance of their supply chain operations. By measuring key performance indicators (KPIs) such as on-time delivery, inventory turnover, and order cycle time, businesses can assess the effectiveness and efficiency of their supply chain. Monitoring these metrics helps identify areas that require attention, allowing for targeted improvement efforts.
3. Continuous Improvement:
Supply chain metrics are essential for driving continuous improvement within the supply chain. By regularly monitoring and analyzing metrics, organizations can identify areas for optimization and implement targeted measures to enhance performance. Continuous improvement efforts result in increased efficiency, reduced costs, and improved customer satisfaction.
4. Cost Optimization:
Supply chain metrics provide insights into the costs associated with supply chain operations. By monitoring cost metrics such as transportation costs, cost per order, and inventory carrying costs, organizations can identify cost-saving opportunities and implement measures to optimize expenses. This leads to increased profitability and competitiveness in the market.
5. Enhanced Customer Satisfaction:
Supply chain metrics play a crucial role in meeting and exceeding customer expectations. By tracking metrics such as on-time delivery, perfect order rate, and order fill rate, organizations can ensure timely and accurate order fulfillment. High levels of customer satisfaction result in increased loyalty, improved reputation, and potential for repeat business.
6. Supply Chain Visibility:
Supply chain metrics provide organizations with increased visibility into their supply chain operations. By measuring metrics related to inventory levels, order fulfillment, and transportation, businesses can gain insights into the flow of goods and services across the supply chain. Improved visibility allows for better planning, coordination, and responsiveness to customer demands.
These are just a few of the many benefits of using supply chain metrics. By utilizing these metrics, organizations can gain a competitive edge, reduce costs, enhance customer satisfaction, and drive overall supply chain improvements. Supply chain metrics help organizations optimize their operations, meet customer demands, and achieve long-term success in the dynamic business environment.
Challenges in Implementing Supply Chain Metrics
While supply chain metrics offer numerous benefits, organizations may encounter several challenges in their implementation. These challenges can arise from various factors, including data availability, organizational structure, and technological limitations. It’s important for organizations to be aware of these challenges and address them to effectively utilize supply chain metrics. Here are some common challenges in implementing supply chain metrics:
1. Data Accuracy and Availability:
One of the foremost challenges in implementing supply chain metrics is ensuring the accuracy and availability of data. Organizations may struggle to collect and aggregate data from various sources within the supply chain, leading to incomplete or unreliable information. Inaccurate or unavailable data can compromise the effectiveness of metrics and hinder decision-making processes. Organizations need robust data management systems and processes to ensure data accuracy, quality, and availability for effective metric implementation.
2. Data Integration and Standardization:
Supply chain operations involve multiple systems and stakeholders, often leading to data fragmentation and inconsistency. Integrating data from disparate systems and standardizing data formats can be a significant challenge. Lack of data integration and standardization can result in incomplete or incompatible metrics, making it difficult to gain a comprehensive view of supply chain performance. Overcoming this challenge requires implementing effective data integration strategies and establishing standardized data capture processes.
3. Alignment with Business Objectives:
Choosing the right supply chain metrics that align with business objectives can be a complex task. Organizations need to clearly define their strategic goals and objectives before selecting the appropriate metrics. Failure to align metrics with business objectives may result in tracking irrelevant or misleading data, leading to ineffective decision-making. Aligning metrics with business objectives requires thorough planning, collaboration, and a deep understanding of the organization’s goals.
4. Organizational Buy-In and Culture:
The successful implementation of supply chain metrics requires organizational buy-in and a supportive culture. Resistance to change, lack of understanding, or skepticism from employees and stakeholders can hinder the adoption and utilization of metrics. An organizational culture that values data-driven decision-making and continuous improvement is crucial. Educating and involving employees in the metric implementation process, providing training, and fostering a culture of transparency and collaboration can help overcome this challenge.
5. Technology Infrastructure:
Inadequate technology infrastructure and systems can hinder effective metric implementation. Organizations need robust IT systems, such as enterprise resource planning (ERP) systems, supply chain management software, and data analytics tools, to collect, analyze, and present supply chain data effectively. Lack of technological capabilities may result in inefficient data processing, limited visibility, and delays in generating meaningful insights. Investing in the right technology solutions and ensuring seamless integration with existing systems is crucial to overcome this challenge.
Addressing these challenges requires careful planning, investment in technology, data management capabilities, and a commitment to overcoming organizational barriers. By proactively identifying and addressing these challenges, organizations can unlock the full potential of supply chain metrics and leverage them to drive continuous improvement and achieve supply chain excellence.
Best Practices for Measuring Supply Chain Performance
Measuring supply chain performance is a critical aspect of supply chain management. By implementing best practices for measuring supply chain performance, organizations can gain valuable insights, identify areas for improvement, and make informed decisions to enhance their operations. Here are some key best practices to consider:
1. Establish Clear Objectives and Metrics:
Start by establishing clear objectives for measuring supply chain performance. Define specific goals that align with your organization’s overall strategy and identify the metrics that will be used to measure progress and success. Ensure that the selected metrics are relevant, measurable, and align with industry standards and best practices.
2. Collect Timely and Accurate Data:
Data is the foundation of effective supply chain performance measurement. Ensure that data is collected in a timely and accurate manner from various sources within the supply chain. This may involve leveraging technology and implementing data integration tools to streamline data collection processes. Additionally, put mechanisms in place to ensure data accuracy and reliability, such as regular data validation and quality checks.
3. Integrate Data and Analytics Systems:
To maximize the value of supply chain performance measurement, integrate data and analytics systems. This allows for seamless data flow and real-time analysis, enabling organizations to monitor performance, detect trends, and make data-driven decisions. Integration of systems can help identify correlations and dependencies between different metrics, providing a holistic view of supply chain performance.
4. Establish Baselines and Target Metrics:
Establish baselines for each metric to provide a benchmark for performance evaluation. Baselines provide a starting point against which progress can be measured. Alongside baselines, set target metrics that indicate the desired level of performance. These targets can be based on industry standards, internal benchmarks, or specific business goals. Regularly track performance against these targets to assess progress and drive continuous improvement.
5. KPI Visualization and Reporting:
Visualize and report key performance indicators (KPIs) in a clear and concise manner. Utilize dashboards, data visualization tools, and intuitive reporting formats that provide a visual representation of key metrics. This facilitates easy interpretation of data and enables stakeholders to quickly identify performance trends, areas for improvement, and areas of success. Sharing these visualizations and reports with relevant stakeholders promotes transparency and alignment across the organization.
6. Continuously Monitor and Evaluate:
Supply chain performance measurement is an ongoing process. Continuously monitor and evaluate metrics to ensure that they remain relevant and aligned with changing business needs. Regularly review the effectiveness of metrics and modify them if necessary. Additionally, conduct periodic performance reviews and analysis to identify areas for improvement and track progress towards goals.
7. Foster Collaboration and Continuous Improvement:
Supply chain performance measurement should not be limited to a single department or individual. Foster collaboration between different stakeholders, such as supply chain teams, finance teams, and operations teams, to promote a holistic and integrated approach to performance measurement. Encourage cross-functional communication and regular collaboration to share insights, discuss challenges, and drive continuous improvement initiatives.
By following these best practices, organizations can effectively measure supply chain performance and make informed decisions to optimize their operations. The continuous monitoring and evaluation of metrics, along with collaboration and a commitment to continuous improvement, will enable organizations to stay agile, competitive, and responsive to changing market dynamics.
Conclusion
Supply chain metrics play a vital role in assessing, monitoring, and optimizing supply chain performance. By implementing comprehensive measurement strategies and utilizing key performance indicators (KPIs), organizations can gain valuable insights into their operations and make data-driven decisions to drive continuous improvement. The importance of supply chain metrics cannot be overstated, as they enable organizations to evaluate performance, identify areas for optimization, and enhance overall efficiency.
Throughout this article, we explored the definition of supply chain metrics and highlighted their significance in modern-day finance. We discussed the different types of supply chain metrics, including cost, time, quality, inventory, and service metrics. We also emphasized the importance of aligning supply chain metrics with business objectives and provided best practices for measuring supply chain performance.
It is essential for organizations to overcome challenges related to data accuracy, availability, integration, organizational buy-in, and technological infrastructure when implementing supply chain metrics. By addressing these challenges, organizations can unlock the full potential of supply chain metrics, enabling them to make informed decisions, enhance operational efficiency, and maximize customer satisfaction.
In conclusion, supply chain metrics are invaluable tools for organizations in the finance industry and beyond. By effectively measuring supply chain performance and utilizing the insights garnered from these metrics, organizations can drive continuous improvement, optimize costs, and maintain a competitive edge in the dynamic business landscape. Embracing the power of supply chain metrics is essential for organizations looking to achieve operational excellence, enhance customer satisfaction, and position themselves as leaders in their respective industries.