Home>Finance>Two-Bin Inventory Control: Definition, How It Works, And Example
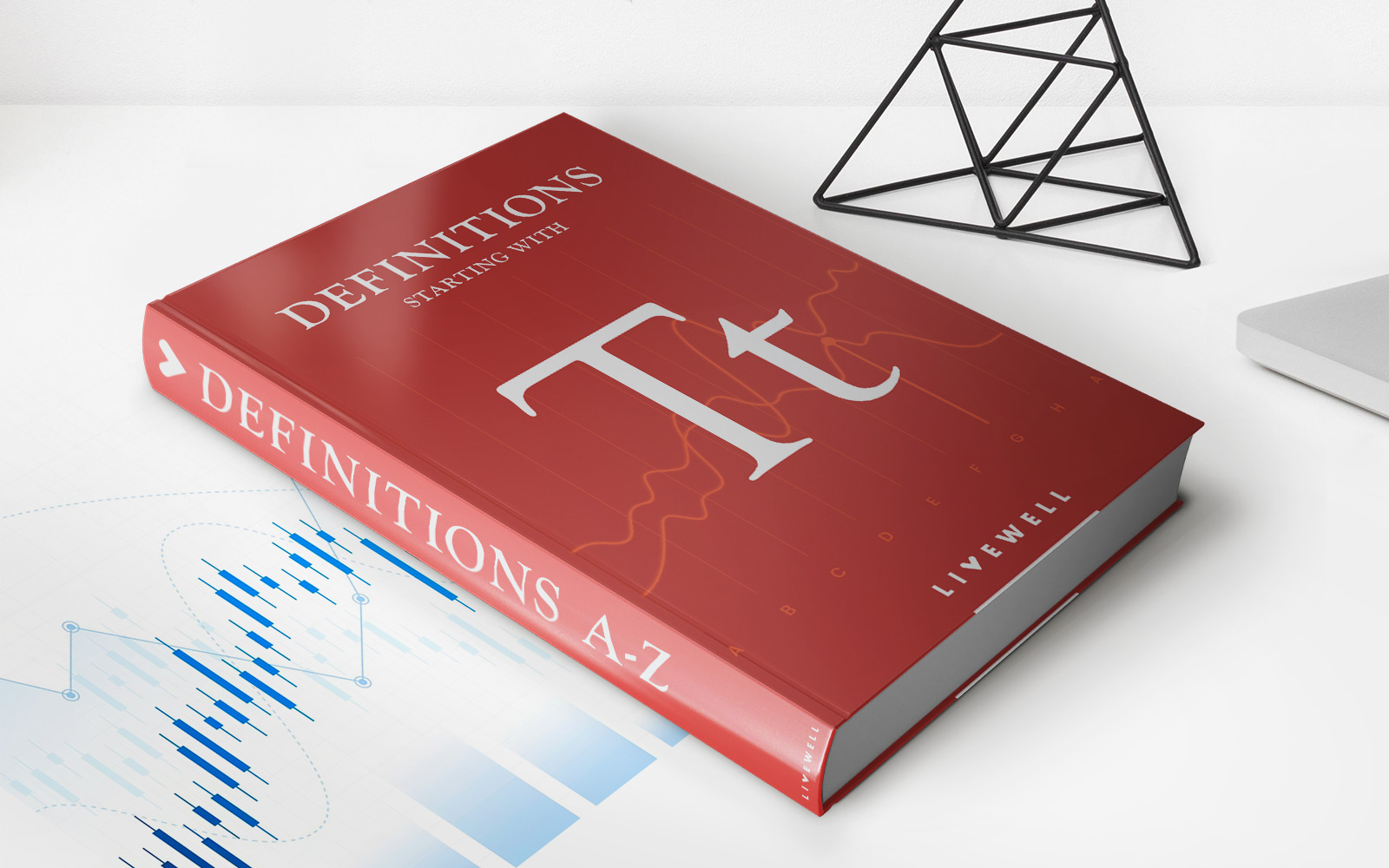
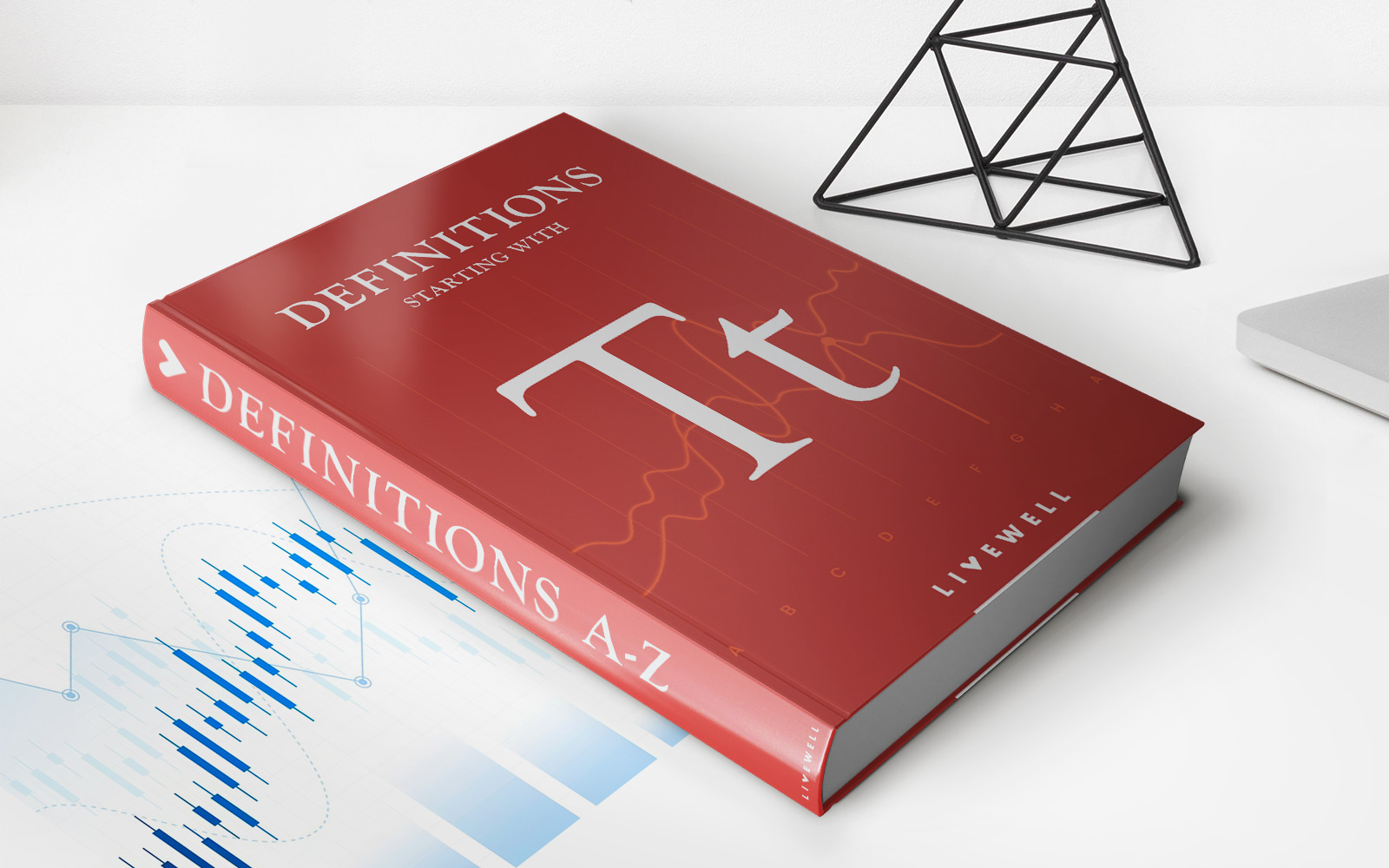
Finance
Two-Bin Inventory Control: Definition, How It Works, And Example
Published: February 12, 2024
Learn about two-bin inventory control in finance, including its definition, how it works, and an example to help streamline your inventory management process.
(Many of the links in this article redirect to a specific reviewed product. Your purchase of these products through affiliate links helps to generate commission for LiveWell, at no extra cost. Learn more)
Two-Bin Inventory Control: Definition, How It Works, and Example
Welcome to our latest blog post in the “FINANCE” category! Today, we’re going to dive into the world of inventory control and explore a popular method called Two-Bin Inventory Control. If you’ve ever wondered how businesses effectively manage their inventory and ensure they have enough stock on hand, you’re in the right place. In this article, we’ll cover the definition, how it works, and provide an example to help you understand the practical application of this inventory control technique. So, let’s get started!
Key Takeaways:
- Two-Bin Inventory Control is a method used by businesses to manage their inventory levels more efficiently.
- It involves using two bins or containers to store items, with the first bin representing the stock currently in use and the second bin acting as a backup when the first bin is empty.
What is Two-Bin Inventory Control?
Two-Bin Inventory Control is a simple yet effective method used by businesses to manage their inventory levels. It works on the concept that having a backup or reserve stock readily available can ensure smooth operations and prevent stockouts. The process involves dividing the inventory into two bins or containers, where the first bin contains the stock currently in use, and the second bin acts as a replenishment or backup stock.
Here is a step-by-step breakdown of how Two-Bin Inventory Control works:
- Identification and Division: Firstly, the items in the inventory are identified and divided into two groups.
- First Bin: The first bin holds the stock that is currently in use. As items are consumed or sold, the quantity is recorded and continually monitored.
- Replenishment Trigger: When the first bin is empty or reaches a predefined minimum quantity, it triggers the need to replenish the stock from the second bin.
- Second Bin: The second bin acts as the backup or reserve stock. It contains an adequate quantity of items to meet the demand until the next replenishment. As the first bin is emptied, stock from the second bin is transferred to maintain the required level.
- Replenishment Process: Once the second bin is used up, it signals the need to reorder or resupply the stock. This process can be automated or manual, depending on the business’s inventory management system.
- Restocking: Once the new stock arrives, it is distributed into the second bin, ready to be used when needed.
Two-Bin Inventory Control Example
Let’s say you run a small retail store, and one of your best-selling products is a specific brand of shoes. Using Two-Bin Inventory Control, here’s how you could manage your inventory:
- First Bin: You keep a bin near the cash register with a certain quantity of shoes that are ready for immediate sale.
- Second Bin: In your stockroom, you have another bin filled with additional shoes to replenish the first bin when needed.
As customers purchase shoes, you record the sales while monitoring the quantity in the first bin. When it reaches a predetermined minimum level, you know it’s time to transfer shoes from the second bin to restock the first bin. This way, you always have a ready supply of shoes available for sale, preventing any potential stockouts and keeping your customers happy.
In conclusion, Two-Bin Inventory Control is a valuable technique that helps businesses manage their inventory efficiently. By dividing inventory into two bins and keeping a backup supply, businesses can avoid stockouts and ensure they meet customer demand. So, whether you’re a retailer or an online store owner, consider implementing Two-Bin Inventory Control as part of your inventory management strategy!