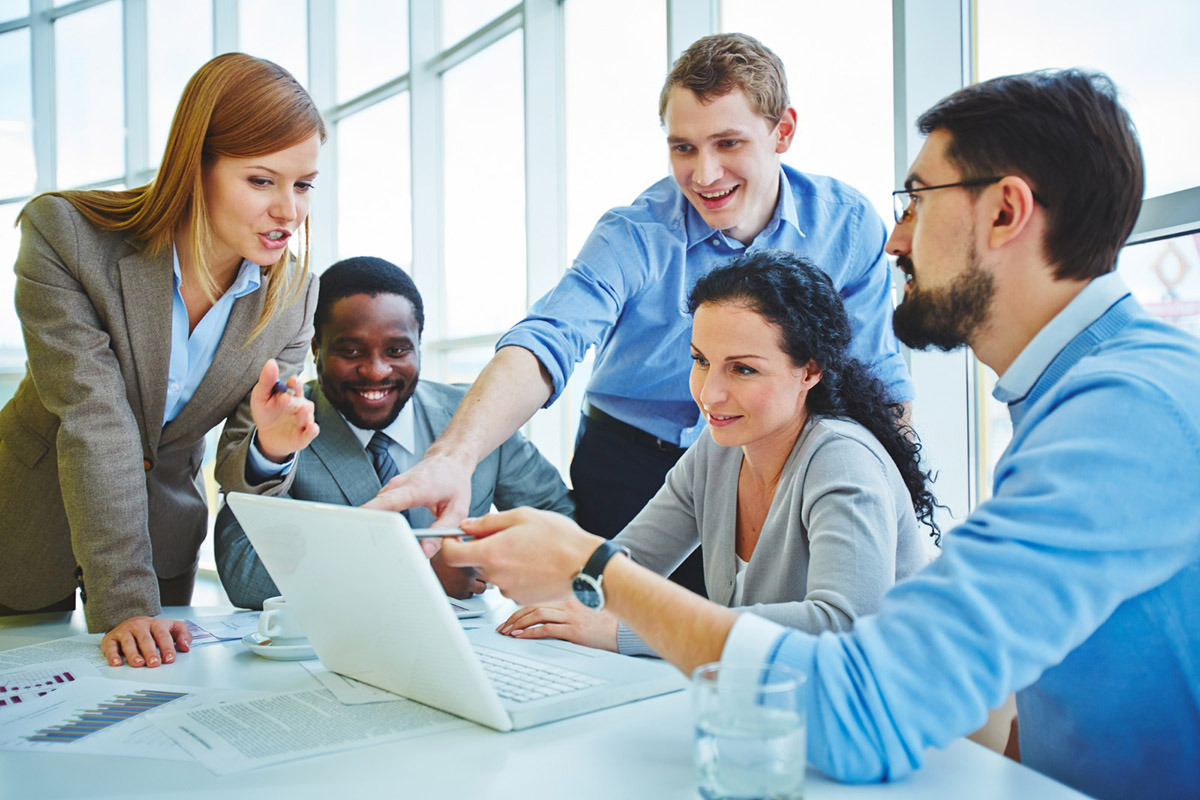
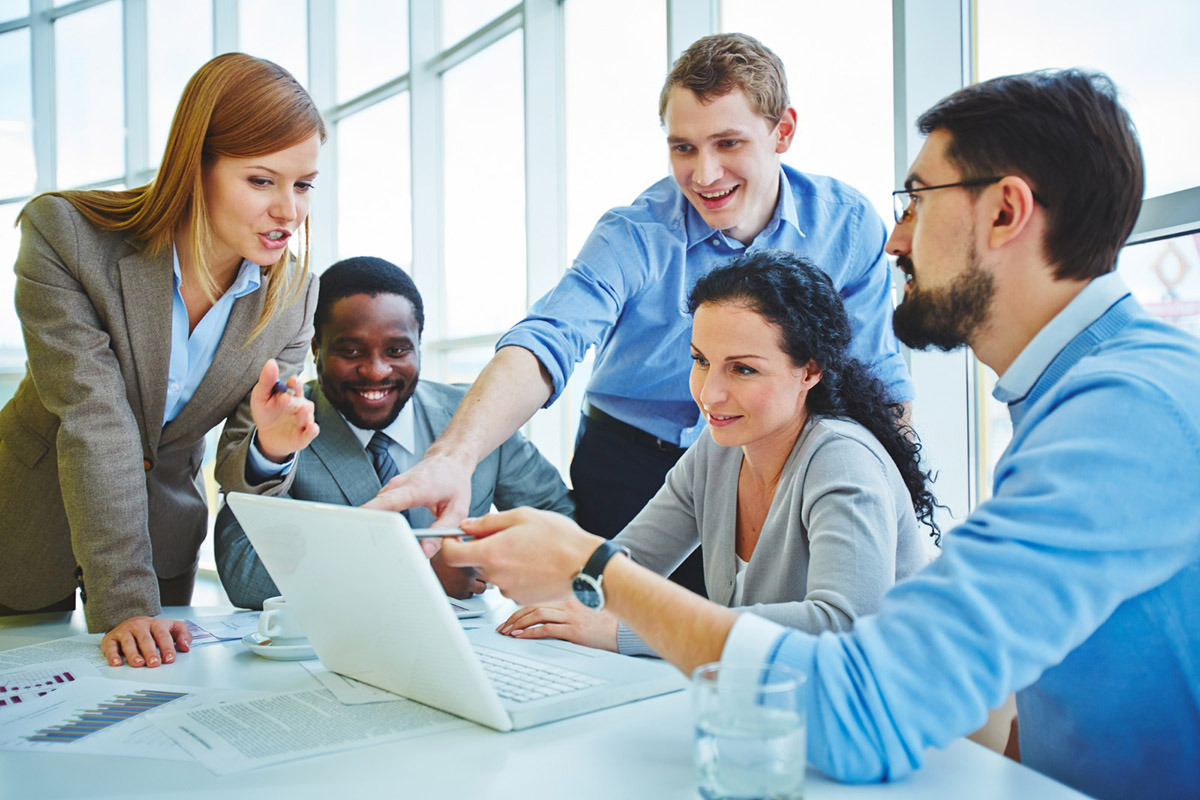
Finance
What Is An Integrated Supply Chain?
Published: October 19, 2023
Learn how an integrated supply chain can optimize finance operations and improve overall business performance. Discover the benefits of integrating financial processes with supply chain management.
(Many of the links in this article redirect to a specific reviewed product. Your purchase of these products through affiliate links helps to generate commission for LiveWell, at no extra cost. Learn more)
Table of Contents
- Introduction
- Definition of an Integrated Supply Chain
- Benefits of Implementing an Integrated Supply Chain
- Key Components of an Integrated Supply Chain
- Importance of Collaboration and Communication in an Integrated Supply Chain
- Challenges in Implementing an Integrated Supply Chain
- Examples of Successful Integrated Supply Chain Practices
- Conclusion
Introduction
Welcome to the world of supply chain management, where the efficient flow of products and services is crucial for the success of any business. In today’s fast-paced and competitive market, companies are constantly looking for ways to optimize their supply chain operations and gain a competitive edge. One approach that has gained significant attention and proven to be effective is the implementation of an integrated supply chain.
An integrated supply chain is a strategic approach that aims to streamline and coordinate all aspects of the supply chain, from procurement and production to distribution and customer service. It involves the seamless flow of information, materials, and resources across all functional areas, both within the company and with external partners, such as suppliers and logistics providers.
By integrating various functions and processes within the supply chain, companies can achieve greater visibility, control, and efficiency, resulting in improved customer satisfaction, reduced costs, and increased profitability. The concept of an integrated supply chain has gained traction in recent years, as businesses realize the potential benefits it can bring to their operations.
In this article, we will explore the definition of an integrated supply chain, its key components, the benefits of implementing it, as well as the challenges involved. We will also provide examples of successful integrated supply chain practices to highlight its real-world applications. So, let’s dive in and discover how an integrated supply chain can revolutionize the way businesses operate.
Definition of an Integrated Supply Chain
An integrated supply chain refers to the seamless coordination and collaboration of all activities involved in the flow of goods, services, and information, from the sourcing of raw materials to the delivery of finished products to the end customer. It involves the integration of key functions like procurement, production, logistics, and customer service, both within the company and across external partners, to create a cohesive and efficient supply chain ecosystem.
At its core, an integrated supply chain aims to break down silos and eliminate redundancies by connecting different stages of the supply chain and enabling smooth communication and coordination among all stakeholders. This integration allows for real-time visibility and control over the entire supply chain, leading to improved decision-making, enhanced responsiveness to customer demands, and minimized delays and disruptions.
An integrated supply chain relies heavily on advanced technologies and robust information systems to facilitate the exchange of data and enable seamless collaboration. It leverages tools like enterprise resource planning (ERP) systems, supply chain management software, and communication platforms to ensure that all relevant parties have access to accurate and timely information.
In addition to technological integration, an integrated supply chain requires a culture of collaboration and trust among all participants. It involves building strong relationships with suppliers, distributors, and other partners, fostering open communication channels, and aligning goals and objectives for mutual benefit.
By implementing an integrated supply chain, companies can achieve a wide range of benefits, such as:
- Improved visibility and control over the entire supply chain network
- Enhanced responsiveness to customer demands and changing market trends
- Reduced lead times and improved on-time delivery
- Increased agility and flexibility to adapt to disruptions and market fluctuations
- Optimized inventory management and reduced stockouts
- Lower costs through streamlined processes and reduced waste
- Enhanced collaboration and trust among supply chain partners
Overall, an integrated supply chain is a proactive approach that enables organizations to achieve operational excellence, drive customer satisfaction, and gain a competitive advantage in today’s dynamic business landscape.
Benefits of Implementing an Integrated Supply Chain
Implementing an integrated supply chain offers numerous benefits to businesses across various industries. Let’s explore some of the key advantages of adopting this strategic approach:
1. Improved Efficiency and Cost Reduction: An integrated supply chain optimizes the flow of materials, information, and resources, resulting in improved operational efficiency. By eliminating redundancies, streamlining processes, and reducing lead times, companies can achieve significant cost savings. Efficient inventory management also helps minimize carrying costs and reduce stockouts, ensuring that products are available when and where they are needed, thereby reducing lost sales opportunities.
2. Enhanced Customer Satisfaction: With an integrated supply chain, businesses can better anticipate and meet customer demands. Improved visibility into the entire supply chain allows for faster response times, reduced order processing times, and improved on-time delivery. This results in higher customer satisfaction, repeat business, and potentially increased market share.
3. Increased Agility and Flexibility: Today’s volatile business environment requires companies to be agile and adaptable. An integrated supply chain enables organizations to quickly respond to changes in customer preferences, market trends, and disruptions. With real-time visibility and coordination, companies can make faster decisions, adjust production schedules, and find alternative suppliers or transportation routes when needed.
4. Enhanced Collaboration and Communication: Collaboration is essential in supply chain management, and an integrated approach fosters better collaboration among all stakeholders. By sharing information, forecasts, and plans in real-time, companies can work together to resolve issues, optimize processes, and align goals. Effective communication improves relationships with suppliers, distributors, and customers, enabling better coordination and problem-solving.
5. Improved Quality and Sustainability: An integrated supply chain ensures greater control and traceability of materials and processes, leading to improved quality control. By optimizing processes and reducing waste, companies can also contribute to sustainability efforts by minimizing their environmental footprint and supporting responsible sourcing practices.
6. Competitive Advantage: Implementing an integrated supply chain can provide a significant competitive advantage in the market. Streamlined operations, improved customer service, and cost savings can create differentiation and attract customers. It also enhances resilience, as organizations can better navigate disruptions and adapt to changing market conditions.
Overall, implementing an integrated supply chain enables businesses to operate more efficiently, meet customer demands, reduce costs, and gain a competitive edge. It is a strategic approach that leverages technology, collaboration, and streamlined processes to drive success in today’s complex and fast-paced business environment.
Key Components of an Integrated Supply Chain
An integrated supply chain consists of several key components that work together to ensure the seamless flow of goods, services, and information. Let’s explore these components:
1. Demand Planning and Forecasting: Accurate demand planning and forecasting are crucial to align production and inventory levels with customer demand. By analyzing historical data, market trends, and customer insights, companies can optimize their production and procurement processes, reducing the risk of stockouts or excess inventory.
2. Procurement and Supplier Management: The procurement function involves sourcing and managing suppliers to ensure the timely availability of raw materials and components. An integrated supply chain involves building strong relationships with reliable suppliers, implementing efficient procurement processes, and leveraging technology to streamline supplier management.
3. Production and Operations Management: This component focuses on optimizing the manufacturing and operations processes. It includes activities such as production planning, scheduling, capacity management, and quality control. Integration across different production stages enables efficient resource allocation, reduced cycle times, and improved product quality.
4. Inventory Management: Effective inventory management is crucial to balance supply and demand and minimize holding costs. With an integrated supply chain, companies gain real-time visibility into inventory levels and can optimize inventory replenishment based on customer demand, production schedules, and lead times.
5. Logistics and Transportation: Smooth and efficient movement of goods is vital in an integrated supply chain. It involves coordinating transportation modes, optimizing routes, and managing logistics partners. Real-time tracking and communication systems ensure timely delivery, reduce transportation costs, and minimize order fulfillment errors.
6. Information Systems and Technology: Advanced technology and information systems play a crucial role in integrating the supply chain. This includes enterprise resource planning (ERP) systems, supply chain management (SCM) software, and other tools that enable data sharing, collaboration, and real-time visibility across the supply chain network.
7. Collaboration and Communication: Collaboration is essential in an integrated supply chain. It involves effective communication and coordination among all stakeholders, including suppliers, distributors, and customers. Sharing accurate and timely information optimizes decision-making, resolves issues proactively, and aligns goals and strategies.
8. Performance Measurement and Continuous Improvement: Implementing performance metrics and measurement systems helps track the efficiency and effectiveness of the integrated supply chain. Continuous improvement initiatives, such as lean principles or Six Sigma, ensure ongoing optimization and adaptation to changing market conditions.
By integrating and aligning these key components, companies can achieve greater efficiency, responsiveness, and visibility throughout their supply chain, resulting in improved customer satisfaction and increased profitability.
Importance of Collaboration and Communication in an Integrated Supply Chain
Collaboration and communication are vital elements in the success of an integrated supply chain. In today’s interconnected business environment, where supply chains span multiple organizations and geographical regions, effective collaboration and communication are essential for seamless coordination and efficient operations. Let’s explore the importance of collaboration and communication in an integrated supply chain:
1. Improved Visibility and Information Sharing: Collaboration and communication enable real-time visibility into the supply chain network. By sharing accurate and timely information across all stakeholders, companies can gain insights into demand patterns, production capacities, inventory levels, and delivery schedules. This visibility allows for better planning, decision-making, and performance tracking throughout the supply chain.
2. Enhanced Responsiveness to Changes: In an integrated supply chain, external factors like demand fluctuations, market trends, or supply disruptions can have significant impacts. Effective collaboration and communication mechanisms enable quick response to these changes. By sharing information promptly, companies can adjust production schedules, source alternative suppliers, or adapt transportation routes to minimize disruptions and meet customer demands.
3. Streamlined Processes and Reduced Lead Times: Collaboration fosters the alignment of processes and workflow across different stages of the supply chain. By eliminating silos and establishing seamless coordination, companies can streamline operations, reduce redundancies, and minimize handover delays. This integrated approach reduces lead times, improves efficiency, and ultimately enhances customer satisfaction.
4. Enhanced Problem-Solving and Risk Mitigation: Collaboration and communication foster a culture of shared responsibility and problem-solving. When issues arise within the supply chain, effective collaboration enables stakeholders to work together to identify root causes, propose solutions, and implement corrective measures. By proactively addressing challenges, companies can minimize risks and maintain operational continuity.
5. Better Relationship Management: Collaboration is not limited to internal teams; it extends to external partners like suppliers, distributors, and customers. By maintaining open lines of communication and fostering strong relationships, companies can build trust, ensure transparency, and align their goals and strategies with those of their partners. This collaborative approach leads to improved collaboration in areas such as demand planning, inventory management, and risk management.
6. Innovation and Continuous Improvement: Collaboration within an integrated supply chain often generates new ideas for process improvement, innovation, and cost reduction. By encouraging cross-functional collaboration, companies can tap into the expertise and creativity of different teams, leading to better problem-solving and continuous improvement initiatives. Sharing best practices and lessons learned also helps drive innovation and enhances the overall competitiveness of the supply chain.
Overall, collaboration and communication are key drivers of success in an integrated supply chain. By fostering a culture of collaboration, sharing information, and maintaining strong relationships, companies can achieve greater visibility, responsiveness, and efficiency throughout their supply chain network, ultimately leading to improved customer satisfaction and business performance.
Challenges in Implementing an Integrated Supply Chain
Implementing an integrated supply chain can bring many benefits, but it is not without its challenges. Let’s explore some of the key challenges that organizations may face when embarking on the journey to integrate their supply chain:
1. Cultural Resistance: Implementing an integrated supply chain often requires significant changes to processes, roles, and responsibilities. Resistance to change from employees and stakeholders can hinder progress. Overcoming this challenge requires effective change management strategies, clear communication, and fostering a culture of collaboration and openness to new ways of working.
2. Data Quality and Integration: An integrated supply chain relies heavily on accurate and timely data. However, organizations often face challenges in collecting, cleaning, and integrating data from various sources and systems. Inconsistencies or errors in data can lead to inaccurate decision-making and operational inefficiencies. Investing in robust data management systems and ensuring data integrity are essential to overcome this challenge.
3. Technological Complexity: Integrating different technologies and systems across the supply chain can be complex and challenging. Legacy systems, different data formats, and compatibility issues can create hurdles during the integration process. Organizations need to invest in the right technology infrastructure, including integration platforms, APIs, and data exchange protocols, to enable smooth communication and interoperability between systems.
4. Lack of Standardization: In an integrated supply chain, standardization of processes, metrics, and terminology is crucial for effective collaboration. However, different stakeholders may have their own unique processes and systems in place. Harmonizing these diverse practices and establishing common standards can be a significant challenge. It requires strong leadership, negotiation skills, and a willingness to align processes across all parties involved.
5. Supplier and Partner Collaboration: Collaboration with suppliers, distributors, and other partners is essential for a successful integrated supply chain. However, obtaining buy-in and alignment with external partners may be challenging. Differences in priorities, expectations, and capabilities can hinder effective collaboration. Building strong relationships through trust, open communication, and mutually beneficial agreements is key to overcoming this challenge.
6. Information Security and Privacy: Sharing information across the supply chain network raises concerns about data security and privacy. Protecting sensitive information from unauthorized access or cyber threats is critical. Organizations need robust data security mechanisms, proper access controls, and adherence to data protection regulations to mitigate these risks.
7. Supply Chain Disruptions: Integrating the supply chain may initially expose vulnerabilities and dependencies that were not apparent before. Disruptions, such as natural disasters, geopolitical issues, or supplier failures, can have a cascading effect throughout the integrated supply chain. Implementing strategies for risk mitigation, contingency planning, and supplier diversification is essential to overcome these challenges.
8. Financial Investment: Implementing an integrated supply chain requires significant financial investment in technology, systems, and process reengineering. Organizations need to allocate resources and create a business case to justify this investment. Securing executive sponsorship and demonstrating the potential return on investment is crucial in overcoming financial hurdles.
Despite these challenges, organizations that successfully implement an integrated supply chain can reap significant rewards in terms of cost savings, operational efficiency, customer satisfaction, and competitive advantage. It requires careful planning, stakeholder engagement, and a commitment to continuous improvement to navigate these challenges and fully realize the benefits of an integrated supply chain.
Examples of Successful Integrated Supply Chain Practices
Many companies have successfully implemented integrated supply chains, resulting in improved operational efficiency, cost savings, and customer satisfaction. Let’s examine a few examples of organizations that have adopted successful integrated supply chain practices:
1. Procter & Gamble (P&G): P&G is a consumer goods company known for its effective supply chain management. Through their Collaborative Planning, Forecasting and Replenishment (CPFR) program, P&G collaborates with key retailers to gather sales data and ensure accurate demand forecasting. This collaboration allows for better inventory planning, reduced stockouts, and improved on-shelf availability.
2. Zara: Zara, a fast-fashion retailer, has built an integrated supply chain that enables them to respond quickly to the latest fashion trends. They have implemented a vertical integration model, bringing their design, production, and distribution processes under one roof. This allows Zara to have a short production lead time and a flexible supply chain, rapidly adjusting their product offerings based on customer preferences.
3. Amazon: Amazon has revolutionized the e-commerce industry with its integrated supply chain and sophisticated logistics operations. By leveraging advanced technology, Amazon optimizes its inventory management, order fulfillment, and transportation processes. Real-time visibility and coordination across the supply chain enable them to offer fast and reliable delivery to their customers.
4. Toyota: Toyota is renowned for its lean manufacturing principles, which are an integral part of their integrated supply chain. Toyota’s approach emphasizes waste reduction, continuous improvement, and just-in-time production. By closely collaborating with suppliers, Toyota ensures a smooth flow of materials and minimizes inventory levels while maintaining high production efficiency.
5. Apple: Apple’s integrated supply chain is a key factor in their success. By closely coordinating with suppliers and contract manufacturers, Apple ensures a reliable and efficient supply of components for its iconic products. This enables them to meet customer demand and launch products globally with minimal delays.
6. Dell: Dell’s direct model is a prime example of an integrated supply chain. Through their build-to-order approach, Dell collaborates closely with suppliers to source components and assembles computers based on customer specifications. This streamlined supply chain eliminates the need for excess inventory and reduces lead times, allowing Dell to deliver customized products to customers quickly.
These examples highlight the diverse ways in which organizations have implemented integrated supply chain practices to achieve operational excellence. By aligning processes, information systems, and collaboration efforts, these companies have improved efficiency, reduced costs, and enhanced customer satisfaction.
It’s important to note that successful integrated supply chain practices are highly dependent on individual industry dynamics and organizational goals. Each company needs to assess its unique requirements and tailor its integrated supply chain strategies to meet its specific needs. By learning from these success stories and adapting best practices, organizations can embark on their journey towards a more efficient and effective integrated supply chain.
Conclusion
The implementation of an integrated supply chain is a strategic approach that can transform the way businesses operate. By streamlining processes, improving visibility, and fostering collaboration, organizations can achieve significant benefits such as improved operational efficiency, cost savings, and enhanced customer satisfaction.
An integrated supply chain involves the seamless coordination and integration of all activities, from procurement and production to distribution and customer service. Key components, including demand planning, procurement, production, logistics, and information systems, work together to create a cohesive and efficient supply chain ecosystem.
The importance of collaboration and communication cannot be overstated in an integrated supply chain. Effective collaboration fosters better visibility, responsiveness to changes, streamlined processes, and enhanced problem-solving capabilities. Open communication channels and strong relationships with suppliers and partners enable seamless coordination and improved decision-making across the supply chain network.
While implementing an integrated supply chain brings numerous benefits, it also presents challenges. Cultural resistance, data integration, technological complexity, and supplier collaboration are common obstacles organizations may face. Overcoming these challenges requires effective change management strategies, investment in technology infrastructure, standardization efforts, and proactive risk mitigation strategies.
Successful companies have demonstrated the power of an integrated supply chain through real-world examples. Procter & Gamble, Zara, Amazon, Toyota, Apple, and Dell have leveraged collaboration, integration, and technology to improve their operations, optimize inventory management, and meet customer demands efficiently.
In conclusion, embracing an integrated supply chain approach is vital for organizations aiming to stay competitive in today’s dynamic business landscape. By aligning key components, fostering collaboration, and overcoming challenges, companies can create a responsive, efficient, and customer-centric supply chain that drives success and differentiation in the market.