Home>Finance>Just-in-Time (JIT): Definition, Example, And Pros & Cons
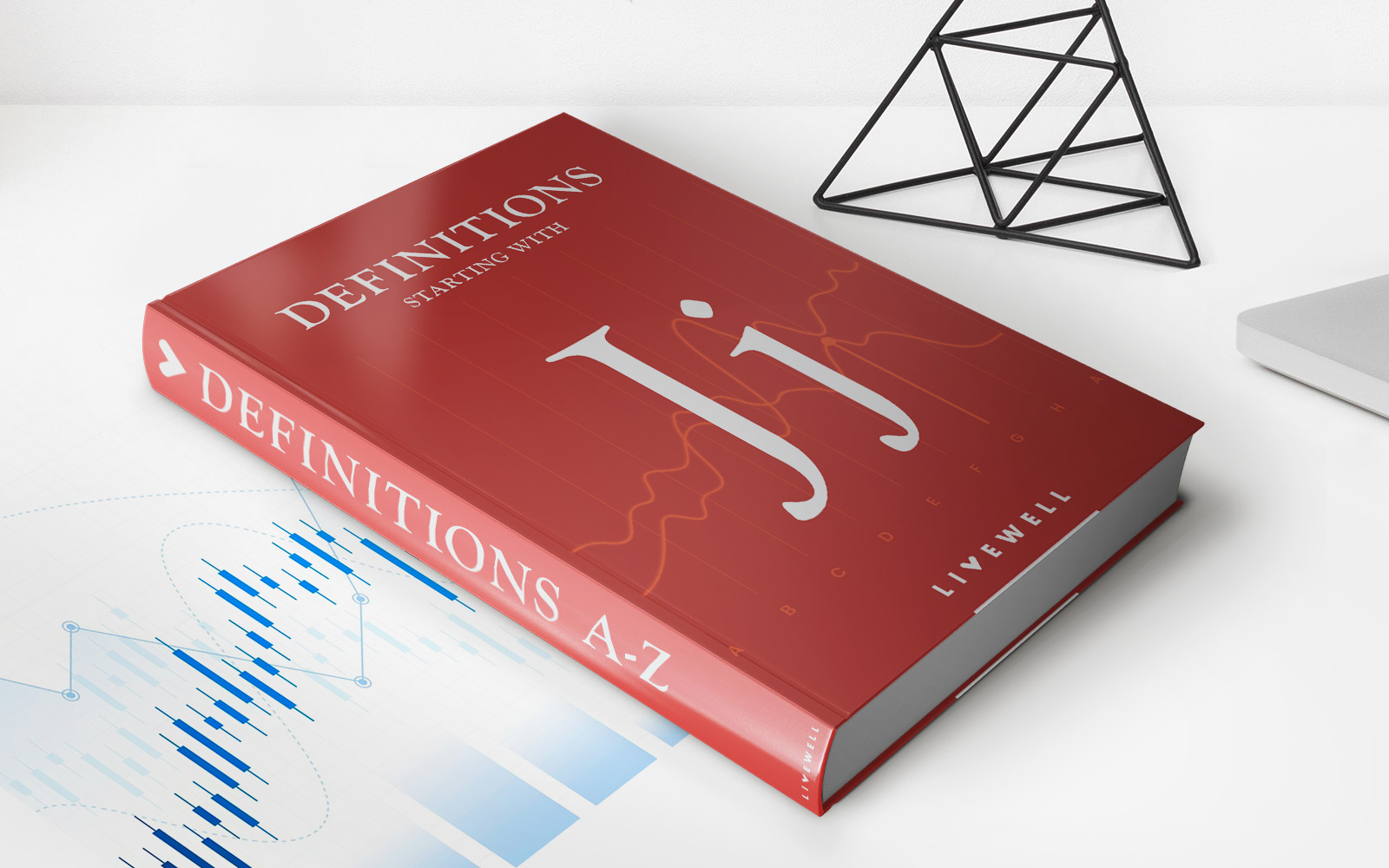
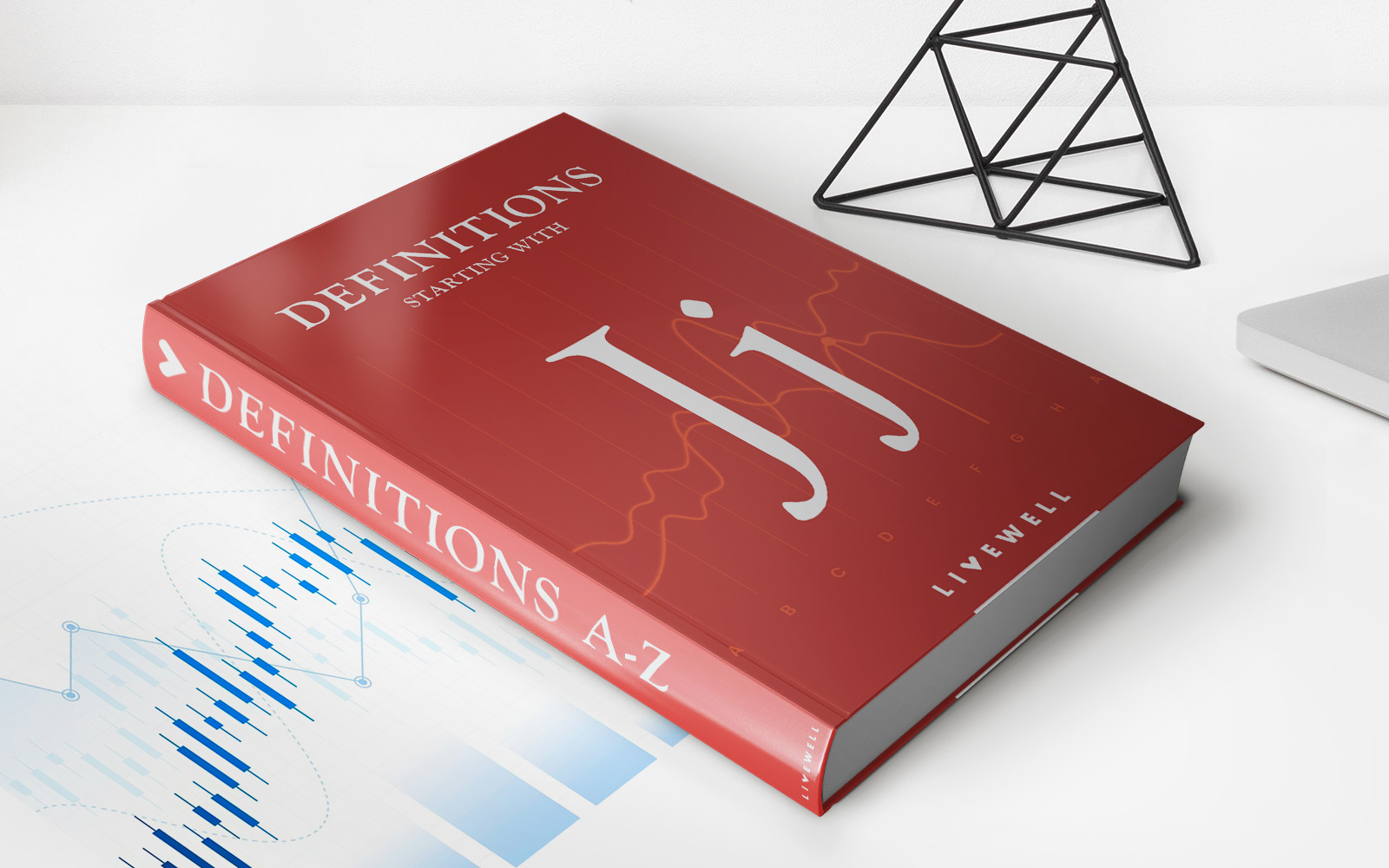
Finance
Just-in-Time (JIT): Definition, Example, And Pros & Cons
Published: December 15, 2023
Learn about the concept of Just-in-Time (JIT) in finance, with examples and the pros and cons of implementing it. Enhance your financial management skills.
(Many of the links in this article redirect to a specific reviewed product. Your purchase of these products through affiliate links helps to generate commission for LiveWell, at no extra cost. Learn more)
Maximizing Efficiency with Just-in-Time (JIT) Inventory Management
Inventory management is a crucial aspect of any business, and one approach that has gained popularity in recent years is Just-in-Time (JIT) inventory management. In this article, we’ll explore the definition of JIT, provide an example to help you visualize its application, and discuss its pros and cons. By the end, you’ll have a clear understanding of JIT and whether it’s a suitable strategy for your business.
Key Takeaways:
- Just-in-Time (JIT) inventory management aims to minimize waste and maximize efficiency by ordering and receiving inventory just in time for production or customer demand.
- JIT can improve cash flow, reduce storage costs, and reduce the risk of inventory obsolescence. However, it requires careful planning, reliable suppliers, and effective communication.
Defining Just-in-Time (JIT)
Just-in-Time is an inventory management strategy that focuses on minimizing waste by ordering and receiving inventory exactly when it is needed for production or to fulfill customer orders. The goal is to minimize inventory holding costs while ensuring a continuous flow of production or order fulfillment.
An Example of Just-in-Time (JIT)
To better understand how Just-in-Time works, let’s consider an example in the context of a furniture manufacturing company. Traditionally, the company would keep a large inventory of raw materials, such as wood, varnish, screws, and upholstery fabric, in their warehouse. This inventory would be used to fulfill orders as they came in, but it would also tie up a significant amount of capital and storage space.
With Just-in-Time inventory management, the furniture manufacturing company takes a different approach. They maintain minimal on-site inventory and instead establish close relationships with reliable suppliers who can deliver raw materials within a short notice period. The company communicates its production needs to the suppliers, and the suppliers ensure a continuous flow of materials, delivering them just in time for production. As a result, the furniture manufacturer can reduce storage costs, improve cash flow, and minimize the risk of inventory obsolescence.
Pros of Just-in-Time (JIT) Inventory Management
- Improved Efficiency: JIT ensures that inventory is available when needed, avoiding unnecessary delays in production or order fulfillment.
- Reduced Costs: By minimizing inventory holding costs, businesses can free up capital that can be invested in other areas, such as research and development or marketing.
- Minimized Waste: JIT helps businesses avoid overproduction, excess inventory, or items becoming obsolete, reducing waste and environmental impact.
Cons of Just-in-Time (JIT) Inventory Management
- Susceptible to Disruptions: Relying on just-in-time delivery requires a high level of coordination and efficiency throughout the supply chain. Any disruptions, such as delays in delivery or sudden increase in demand, can have a significant impact on operations.
- Dependency on Suppliers: Businesses using JIT must have reliable suppliers who can consistently deliver materials on time and in the right quantity.
- Unpredictable Demand: JIT requires accurate demand forecasting, which can be challenging, especially for businesses in volatile markets.
Just-in-Time (JIT) inventory management, when implemented effectively, can be a powerful tool for businesses aiming to streamline operations and maximize efficiency. However, it is essential to weigh the pros and cons and carefully evaluate whether JIT is the right strategy for your business. By considering your specific industry, supply chain capabilities, and customer demand patterns, you can make an informed decision and take a step towards optimizing your inventory management.