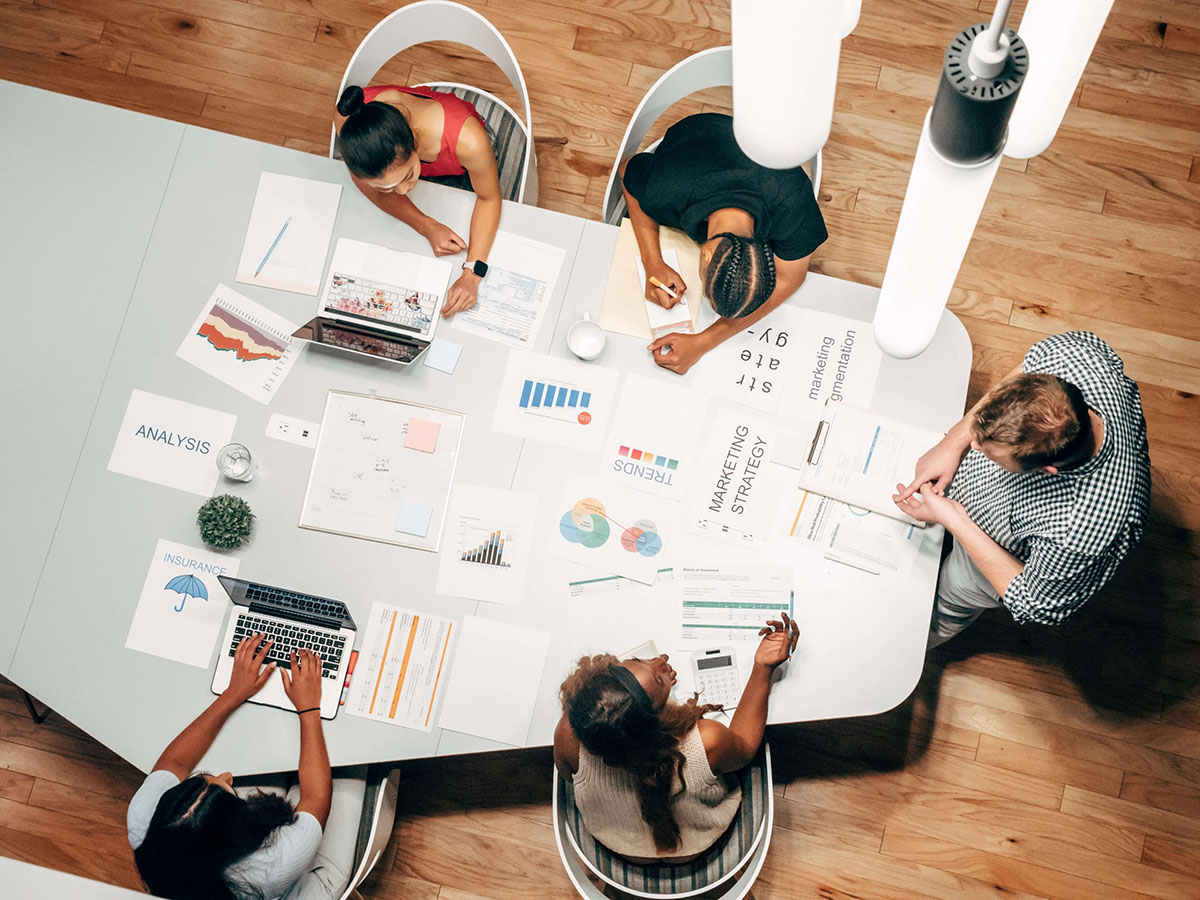
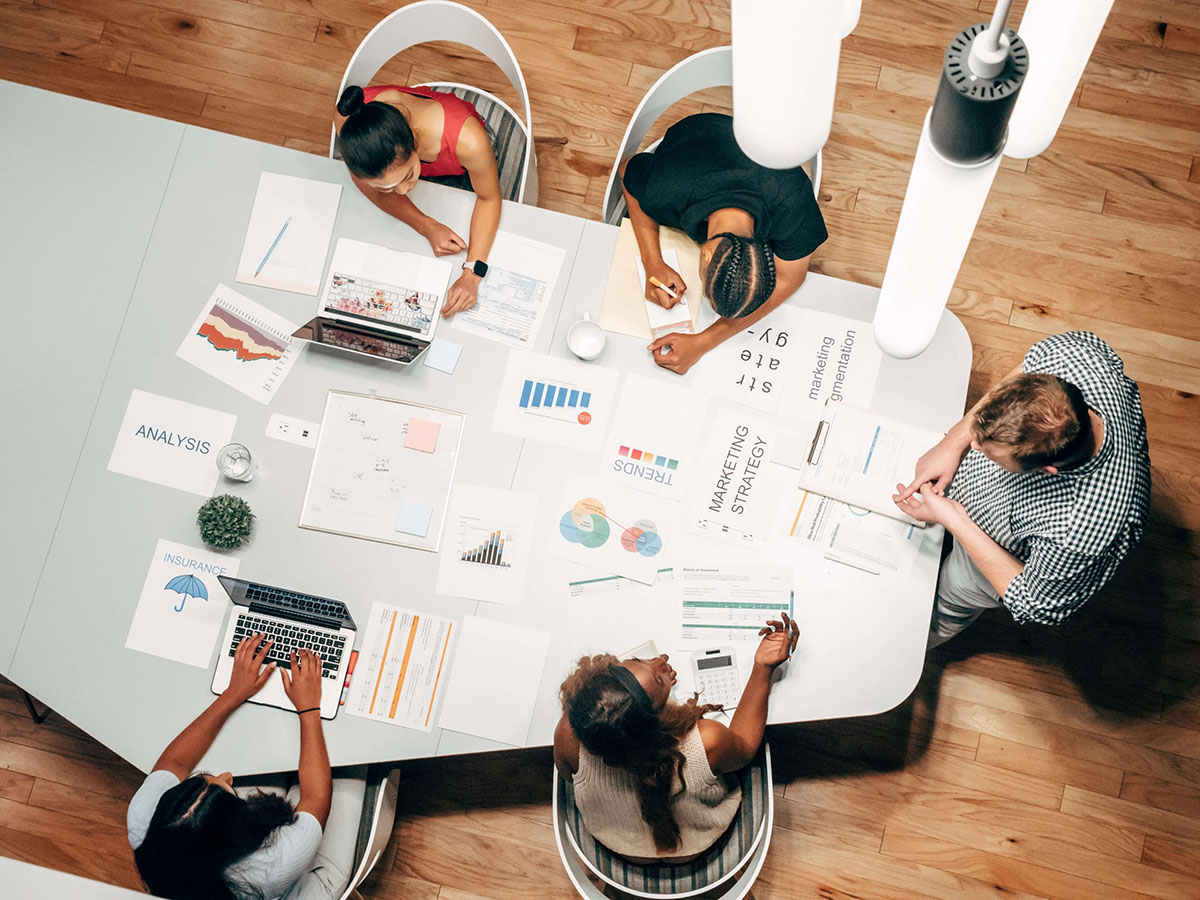
Finance
What Is A Lean Supply Chain?
Published: October 19, 2023
Learn how implementing a lean supply chain can optimize efficiency and reduce costs in your finance department. Gain a competitive edge with lean principles.
(Many of the links in this article redirect to a specific reviewed product. Your purchase of these products through affiliate links helps to generate commission for LiveWell, at no extra cost. Learn more)
Table of Contents
- Introduction
- Definition of a Lean Supply Chain
- Benefits of Implementing a Lean Supply Chain
- Key Principles of a Lean Supply Chain
- Techniques and Tools for Implementing Lean in the Supply Chain
- Case Studies of Successful Lean Supply Chain Implementations
- Challenges and Risks in Implementing Lean Supply Chains
- Future Trends and Innovations in Lean Supply Chain Management
- Conclusion
Introduction
A lean supply chain is a strategically designed and executed system that focuses on efficiency, waste reduction, and continuous improvement within the supply chain processes. It is a concept derived from lean manufacturing principles and is aimed at streamlining all elements of the supply chain, from sourcing raw materials to delivering the final product to the customer.
In today’s highly competitive business landscape, organizations across various industries are recognizing the importance of optimizing their supply chains to drive operational excellence and gain a competitive edge. A lean supply chain enables businesses to eliminate waste, reduce costs, and enhance customer value, ultimately leading to improved profitability and customer satisfaction.
Implementing a lean supply chain requires a holistic approach, involving supply chain leaders, cross-functional teams, and key stakeholders. It involves identifying and addressing inefficiencies, reducing lead times, optimizing inventory levels, and creating a culture of continuous improvement. By doing so, companies can achieve greater agility, flexibility, and responsiveness to the ever-changing market demands.
In this article, we will delve deeper into the concept of a lean supply chain, exploring its definition, benefits, key principles, techniques, case studies, challenges, and future trends. Whether you are an industry professional looking to enhance your understanding of supply chain management or a business owner seeking to improve your company’s supply chain operations, this article will provide valuable insights and guidance.
Definition of a Lean Supply Chain
A lean supply chain is a management philosophy and strategy that aims to eliminate waste, reduce costs, improve efficiency, and enhance customer value throughout the entire supply chain process. It is rooted in the principles of lean manufacturing, which were popularized by Toyota in the 1980s.
At its core, a lean supply chain focuses on delivering the right product to the right place at the right time, with the least amount of waste and resources. It emphasizes the elimination of non-value-added activities, such as excessive inventory, overproduction, transportation delays, and defects.
The key principle of a lean supply chain is the relentless pursuit of continuous improvement. This involves closely analyzing and optimizing each step in the supply chain process to eliminate bottlenecks, reduce lead times, and improve overall efficiency. By doing so, companies can achieve greater operational excellence, cost savings, and customer satisfaction.
A lean supply chain also places a strong emphasis on collaboration and communication among all stakeholders in the supply chain ecosystem. This includes suppliers, manufacturers, distributors, retailers, and customers. Effective collaboration helps to enhance visibility, transparency, and coordination, leading to smoother operations and faster response times to customer demands.
Furthermore, a lean supply chain involves the use of data and analytics to drive decision-making and performance improvements. Through the implementation of modern technologies, such as advanced analytics, artificial intelligence, and Internet of Things (IoT) devices, companies can gather real-time data, analyze it, and make data-driven decisions to optimize their supply chain processes.
In summary, a lean supply chain is a strategic approach to supply chain management that focuses on eliminating waste, improving efficiency, and enhancing customer value. It involves the continuous improvement of processes, collaboration among stakeholders, and the use of data-driven insights to drive operational excellence and business success.
Benefits of Implementing a Lean Supply Chain
Implementing a lean supply chain can yield numerous benefits for organizations across various industries. The following are some key advantages of adopting a lean approach in supply chain management:
- Cost Reduction: Lean principles help to identify and eliminate waste throughout the supply chain process. By reducing unnecessary inventory, minimizing transportation costs, and optimizing production processes, organizations can achieve significant cost savings.
- Improved Efficiency: Lean practices enable streamlined and efficient operations within the supply chain. By eliminating bottlenecks, reducing lead times, and increasing process efficiency, organizations can deliver products faster, meet customer demands promptly, and improve overall operational performance.
- Enhanced Customer Value: A lean supply chain emphasizes meeting customer needs and requirements. By eliminating waste and continuously improving processes, organizations can deliver high-quality products, reduce lead times, and provide superior customer service, thereby enhancing customer satisfaction and loyalty.
- Increased Flexibility and Agility: Lean practices enable organizations to respond quickly to market changes and fluctuations in customer demand. By reducing lead times, increasing productivity, and improving supply chain visibility, companies can adjust their operations and effectively adapt to changing market conditions.
- Higher Productivity: Lean supply chain management focuses on optimizing resources and eliminating non-value-added activities. By streamlining processes, eliminating waste, and empowering employees to contribute to continuous improvement, organizations can achieve higher levels of productivity and employee engagement.
- Improved Supplier Relationships: A lean supply chain encourages strong collaboration and communication among suppliers and other stakeholders. By fostering strong relationships, organizations can improve supplier performance, enhance visibility into the supply chain, and mitigate risks associated with supplier disruptions.
- Reduced Environmental Impact: Lean practices promote sustainability by reducing waste, optimizing energy usage, and minimizing environmental impact. By adopting lean principles, organizations can contribute to a greener supply chain and enhance their reputation as socially responsible businesses.
Overall, implementing a lean supply chain can lead to cost reduction, improved efficiency, enhanced customer value, increased flexibility, higher productivity, improved supplier relationships, and reduced environmental impact. By embracing lean principles, organizations can create a competitive advantage and position themselves for long-term success in today’s dynamic business environment.
Key Principles of a Lean Supply Chain
A lean supply chain is built upon several key principles derived from lean manufacturing. These principles serve as the foundation for creating an efficient and waste-free supply chain. The following are the key principles of a lean supply chain:
- Waste Elimination: The primary principle of a lean supply chain is the identification and elimination of waste. Waste can take various forms, including overproduction, excess inventory, transportation delays, defects, and non-value-added activities. By analyzing each step in the supply chain process, organizations can identify and eliminate these wastes, enhancing efficiency and reducing costs.
- Continuous Improvement: A lean supply chain is characterized by a culture of continuous improvement. This principle emphasizes the need for ongoing evaluation, refinement, and optimization of processes. Continuous improvement involves empowering employees to identify problems, suggest solutions, and implement changes in pursuit of operational excellence.
- Pull System: A lean supply chain adopts a pull-based production system, where products are manufactured based on actual customer demand rather than forecasted demand. The pull system ensures that each step in the supply chain is driven by the needs of the downstream processes, reducing the risk of overproduction and excess inventory.
- Value Stream Mapping: Value stream mapping is a visual tool used to identify and eliminate waste in the supply chain. It involves mapping the entire value stream, from raw materials to customer delivery, and analyzing each step to determine areas for improvement. Value stream mapping helps organizations gain a holistic view of the supply chain and identify opportunities for streamlining processes.
- Standardization: Standardization is essential for creating stability and consistency in the supply chain. It involves developing standardized processes, work instructions, and performance metrics that guide operations. Standardization helps to eliminate variations, reduce errors, and improve overall efficiency.
- Lean Culture: A lean supply chain requires a culture of continuous improvement and employee empowerment. Organizations must foster a collaborative and supportive environment, where employees are encouraged to identify problems, suggest solutions, and actively participate in the improvement process. A lean culture promotes innovation, engagement, and a collective commitment to waste reduction.
By adhering to these key principles, organizations can create a lean supply chain that drives efficiency, eliminates waste, and delivers superior customer value. These principles serve as a roadmap for organizations looking to optimize their supply chain processes and gain a competitive advantage in the market.
Techniques and Tools for Implementing Lean in the Supply Chain
Implementing lean principles in the supply chain requires the use of various techniques and tools to optimize processes and drive continuous improvement. These techniques and tools help identify waste, streamline operations, and enhance overall efficiency. Here are some commonly used techniques in lean supply chain management:
- Value Stream Mapping (VSM): Value stream mapping is a visual tool used to analyze and improve the flow of materials and information throughout the supply chain. It involves mapping the entire value stream, identifying bottlenecks, and streamlining processes to eliminate waste and improve overall efficiency.
- Just-in-Time (JIT): JIT is a key lean technique that focuses on producing and delivering products as they are needed, in the right quantity and at the right time. JIT aims to eliminate excess inventory and reduce lead times to ensure a smooth flow of materials and minimize waste.
- Kanban System: The Kanban system is a visual method used to control inventory levels and manage production. It involves using cards or signals to authorize the replenishment of inventory only when it reaches a predetermined threshold. The Kanban system helps maintain optimal inventory levels, prevent overproduction, and improve flow efficiency.
- Continuous Improvement (Kaizen): Kaizen is a fundamental concept in lean management that promotes continuous improvement. It involves the ongoing evaluation and incremental improvement of processes, products, and services. Kaizen encourages employees to actively participate in problem-solving and innovation to drive continuous improvement in the supply chain.
- 5S Methodology: The 5S methodology provides a structured approach to improve workplace organization and cleanliness. The five steps, Sort, Set in Order, Shine, Standardize, and Sustain, help create an organized and efficient work environment. Implementing 5S ensures that tools, materials, and information are readily available, reducing waste and improving productivity.
- Total Productive Maintenance (TPM): TPM aims to maximize the effectiveness of equipment and minimize downtime. It involves proactive maintenance, employee training, and continuous monitoring to ensure that equipment operates at its optimal performance level. By reducing equipment failures and breakdowns, TPM improves overall supply chain efficiency and productivity.
- Data Analytics and Technology: Leveraging data analytics and technology plays a crucial role in implementing lean practices in the supply chain. Advanced analytics can help identify patterns, forecast demand, optimize inventory, and improve overall decision-making. Technologies such as Internet of Things (IoT) devices, automation, and cloud-based platforms can enhance supply chain visibility, collaboration, and efficiency.
By utilizing these techniques and tools, organizations can optimize their supply chain processes, reduce waste, improve efficiency, and drive continuous improvement. It is essential to select the right combination of techniques and tools that align with the specific needs and goals of the organization.
Case Studies of Successful Lean Supply Chain Implementations
Several organizations have successfully implemented lean supply chain practices to achieve significant improvements in efficiency, customer satisfaction, and financial performance. Let’s explore some notable case studies:
- Toyota: Toyota is often recognized as a pioneer in lean manufacturing and supply chain management. By implementing lean principles such as just-in-time (JIT) production, total quality management (TQM), and continuous improvement, Toyota revolutionized the automotive industry. The company’s lean supply chain practices have enabled it to reduce waste, improve quality, and deliver vehicles to customers in a timely manner.
- Amazon: Amazon, the world’s largest online retailer, has successfully implemented a lean supply chain model featuring advanced technologies and optimization algorithms. The company utilizes predictive analytics and real-time data to optimize inventory levels, streamline order fulfillment, and minimize delivery times. Amazon’s focus on customer-centricity and continuous improvement has allowed it to thrive in the highly competitive e-commerce market.
- Zara: Zara, a fashion retailer, is renowned for its agile and lean supply chain practices. The company maintains a rapid design-to-delivery cycle by producing smaller batches of clothing, closely monitoring consumer trends, and leveraging efficient logistics. Zara’s lean supply chain enables it to quickly respond to customer demands, reduce lead times, and minimize the risk of excess inventory.
- Procter & Gamble (P&G): P&G, a global consumer goods company, implemented a lean supply chain approach called the “Supplier Environmental Sustainability Scorecard.” This scorecard evaluates suppliers based on sustainability factors and encourages them to reduce waste, energy consumption, and greenhouse gas emissions. P&G’s lean supply chain practices have not only improved sustainability but also enhanced supplier collaboration and reduced costs.
- McDonald’s: McDonald’s, the fast-food giant, implemented a lean supply chain model known as the “Made for You” system. This system involves producing food only after the customer places an order, reducing waste and ensuring freshness. Through efficient inventory management and process optimization, McDonald’s can deliver consistent quality and shorten customer wait times.
These case studies highlight the successful implementation of lean supply chain practices across different industries. The common thread among these organizations is a commitment to continuous improvement, customer focus, and the relentless pursuit of waste reduction. By adopting lean principles and tailor-making them to their specific needs, these companies have achieved remarkable results in terms of operational efficiency, customer satisfaction, and business performance.
Challenges and Risks in Implementing Lean Supply Chains
While implementing lean supply chain practices can bring numerous benefits, organizations may encounter several challenges and risks along the way. It is crucial to be aware of these potential obstacles and develop strategies to overcome them. Here are some common challenges and risks in implementing lean supply chains:
- Cultural Resistance: Shifting to a lean mindset and culture requires a significant change in organizational thinking and behavior. Resistance to change from employees and stakeholders can pose a challenge. Overcoming this resistance requires effective change management, clear communication, and engaging employees in the process.
- Supplier Relationships: Implementing lean practices may require closer collaboration and improved communication with suppliers. It can be challenging to align their processes and goals with lean principles. Maintaining strong relationships, setting clear expectations, and providing support to suppliers are crucial in overcoming these challenges.
- Complexity of Implementation: Implementing lean practices across the entire supply chain can be complex. Each step in the process needs to be carefully analyzed and optimized, which requires time, resources, and expertise. It is essential to have a well-structured implementation plan and engage cross-functional teams to ensure successful execution.
- Information and Technology Integration: Lean supply chains rely heavily on real-time information and technology integration. Implementing robust information systems, sharing data across the supply chain, and ensuring compatibility with suppliers and partners can be challenging. Overcoming this challenge may require investing in advanced technologies, data sharing platforms, and standardizing processes across the supply chain ecosystem.
- Change in Work Patterns: Implementing lean practices may require changes in work patterns, job roles, and responsibilities. This can create resistance and disruptions among employees, particularly those who are resistant to change. Involving employees in the change process, providing training and support, and emphasizing the long-term benefits of lean practices can help alleviate these challenges.
- Supply Chain Disruptions: Lean supply chains are designed to operate efficiently, and disruptions, such as natural disasters, supplier failures, or market volatility, can cause significant disruptions. Implementing contingency plans, enhancing supply chain resilience, and developing alternative sourcing strategies can mitigate these risks.
It is important to anticipate and address these challenges and risks when implementing lean supply chain practices. By doing so, organizations can effectively navigate the obstacles and ensure a successful transformation toward a lean and efficient supply chain.
Future Trends and Innovations in Lean Supply Chain Management
As the business landscape continues to evolve, lean supply chain management is also evolving to meet the demands of an increasingly interconnected and dynamic marketplace. Here are some future trends and innovations that are likely to shape the field of lean supply chain management:
- Digitalization and Advanced Analytics: The adoption of advanced analytics tools, big data, and machine learning algorithms will enable organizations to gain deeper insights into supply chain operations. Predictive analytics and real-time data analytics will optimize decision-making, demand forecasting, inventory management, and supply chain visibility. Digitalization will also drive automation and enhance collaboration among supply chain partners.
- Internet of Things (IoT) and Connectivity: The proliferation of IoT devices and connectivity will transform supply chain operations. IoT sensors will provide real-time data on product location, condition, and quality, improving transparency and traceability. Connected devices will enable real-time communication and collaboration between suppliers, manufacturers, logistics providers, and customers, optimizing supply chain processes and enhancing responsiveness.
- Blockchain Technology: Blockchain technology has the potential to revolutionize supply chain management by ensuring transparency, trust, and traceability. Blockchain can enable secure and verifiable transactions, supply chain mapping, and smart contracts, reducing fraud, counterfeiting, and inefficiencies. It will enhance supply chain transparency, reduce paperwork, and create a more reliable and resilient supply chain ecosystem.
- Sustainable and Ethical Supply Chains: The focus on sustainability and ethical practices will continue to grow in the future. Lean supply chains will increasingly incorporate sustainability considerations in areas such as waste reduction, carbon footprint reduction, ethical sourcing, and social responsibility. Organizations will prioritize partnerships with sustainable suppliers and implement circular economy practices to minimize waste and environmental impact.
- Collaborative Robotics (Cobots): Collaborative robots, or cobots, will play a significant role in lean supply chain management. Cobots can work alongside humans, performing repetitive tasks, improving productivity, and reducing errors. They will enhance efficiency in areas such as warehousing, packaging, and order fulfillment, allowing human workers to focus on more complex and value-adding activities.
- Resilient Supply Chains: The COVID-19 pandemic highlighted the need for resilient supply chains that can rapidly respond to disruptions. Lean supply chains will incorporate risk management strategies, diversification of suppliers, and the development of alternative sourcing options. They will also leverage advanced analytics and scenario planning to anticipate and mitigate potential disruptions.
These future trends and innovations in lean supply chain management will enable organizations to further optimize their operations, improve visibility, enhance collaboration, and meet the evolving demands of customers. Embracing these trends will be crucial in staying competitive and achieving long-term success in an ever-changing business environment.
Conclusion
Implementing a lean supply chain is a strategic approach that can drive efficiencies, eliminate waste, and enhance customer value. It involves the continuous improvement of processes, collaboration among stakeholders, and the use of data-driven insights to achieve operational excellence. By adopting lean principles and techniques, organizations can navigate the challenges associated with the modern business landscape and gain a competitive advantage.
The benefits of implementing a lean supply chain are evident in various industries. Companies have experienced cost reduction, improved efficiency, enhanced customer value, increased flexibility, higher productivity, improved supplier relationships, and reduced environmental impact. Lean practices have been successfully implemented by industry leaders such as Toyota, Amazon, Zara, Procter & Gamble, and McDonald’s.
However, organizations should be aware of the challenges and risks involved in implementing lean supply chain practices. These include cultural resistance, supplier relationships, complexity of implementation, information and technology integration, change in work patterns, and supply chain disruptions. Overcoming these challenges requires strong leadership, effective change management, and a holistic approach to implementation.
Looking to the future, there are several trends and innovations that will shape the field of lean supply chain management. The digitalization of supply chain processes, adoption of advanced analytics, Internet of Things (IoT) connectivity, blockchain technology, sustainable and ethical practices, collaborative robotics (cobots), and resilient supply chains will play key roles in optimizing supply chain operations and meeting the changing needs of customers.
In conclusion, embracing lean supply chain practices empowers organizations to optimize their operations, reduce waste, and enhance customer satisfaction. By continuously improving processes, fostering collaboration, embracing technological advancements, and prioritizing sustainability, businesses can create lean and resilient supply chains that drive success in today’s dynamic business environment.