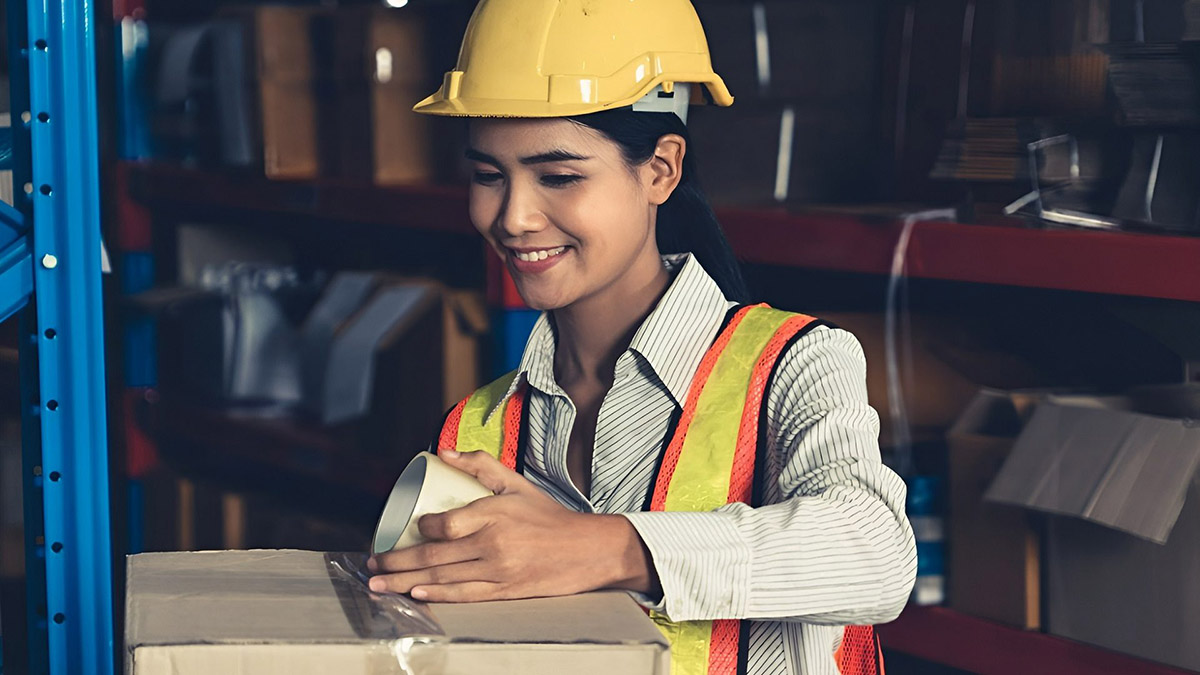
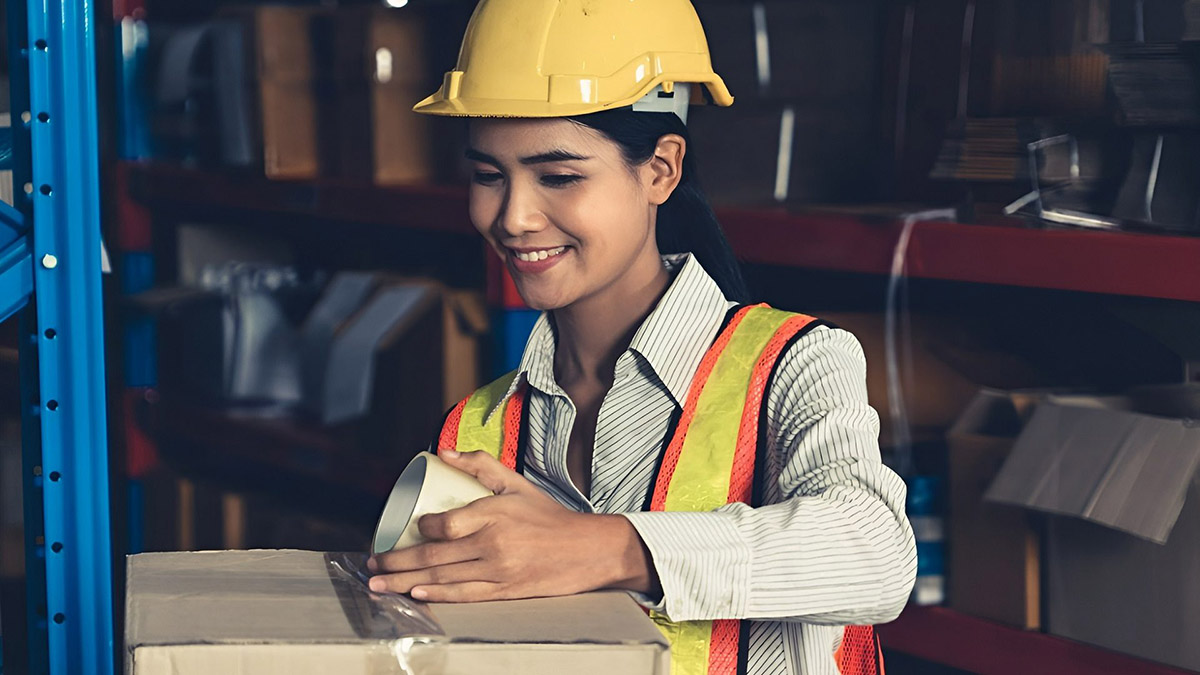
Finance
What Is MRO In The Supply Chain?
Published: November 3, 2023
Learn about MRO in supply chain finance and how it impacts businesses. Explore the significance and benefits of managing Maintenance, Repair, and Operations.
(Many of the links in this article redirect to a specific reviewed product. Your purchase of these products through affiliate links helps to generate commission for LiveWell, at no extra cost. Learn more)
Table of Contents
Introduction
In the world of supply chain management, MRO (Maintenance, Repair, and Operations) plays a crucial role. MRO refers to the materials, equipment, and services necessary to keep the production and operations running smoothly. While it may not receive the same attention as other aspects of the supply chain, such as procurement or logistics, MRO is essential for maintaining the overall efficiency and productivity of an organization.
Whether it’s fixing a broken machine, replacing worn-out parts, or ensuring the availability of critical supplies, MRO activities are indispensable for minimizing downtime and maximizing operational output. From manufacturing plants and warehouses to hospitals and transportation systems, MRO management is a vital element for maintaining operational continuity.
In this article, we will delve into the fascinating world of MRO in supply chain management. We will explore its definition, discuss its importance, examine the key components, and highlight some of the challenges involved in managing MRO in the supply chain. Additionally, we will provide best practices and insights into leveraging technology and automation for efficient MRO management.
By the end of this article, you will have a comprehensive understanding of MRO in the supply chain and how it can drive operational excellence and cost savings for organizations across various industries.
Definition of MRO in Supply Chain
MRO, or Maintenance, Repair, and Operations, encompasses all the activities, materials, equipment, and services required to ensure the smooth functioning and upkeep of an organization’s production and operational facilities. It encompasses everything from regularly scheduled maintenance tasks to emergency repairs and the procurement of necessary supplies.
Maintenance involves the planned and proactive efforts to keep equipment, machinery, and infrastructure in optimal operating condition to avoid breakdowns and minimize downtime. Repair, on the other hand, addresses any unexpected issues or failures in equipment or infrastructure that require immediate attention and restoration. Operations refer to the ongoing activities and processes involved in the day-to-day operation of the organization.
In the context of the supply chain, MRO refers to the management of these maintenance, repair, and operational activities in order to ensure continuous production, minimize disruptions, and optimize overall operational efficiency. It involves identifying the necessary materials, spare parts, tools, and services required to support maintenance and repair activities.
Effective MRO management involves various processes, including inventory management, procurement, vendor management, and maintenance planning and scheduling. It requires a strategic approach to ensure that the right materials are available at the right time to maintain equipment and infrastructure, with the goal of minimizing downtime and reducing maintenance costs.
While MRO components may differ based on the specific industry and organizational requirements, some common examples include spare parts, lubricants, cleaning supplies, safety equipment, and various services such as equipment calibration, repairs, and facility maintenance. These components are crucial for ensuring smooth operations, ensuring compliance with safety regulations, and optimizing the lifespan of assets.
Overall, MRO in the supply chain aims to strike a balance between the costs associated with maintaining and repairing assets and the impact of potential disruptions on productivity. By effectively managing MRO activities, organizations can prevent costly breakdowns, reduce unplanned downtime, and maximize overall operational effectiveness.
Importance of MRO in Supply Chain
The significance of MRO in the supply chain cannot be overstated. It plays a critical role in ensuring the smooth operation of facilities, minimizing downtime, and optimizing overall operational efficiency. Let’s explore some key reasons why MRO is important in the supply chain:
- Maximizing Equipment Efficiency: MRO activities, such as regular maintenance and prompt repairs, help to keep equipment and machinery in optimal working condition. By proactively addressing issues and ensuring preventive maintenance, organizations can reduce the risk of equipment failures, extend the lifespan of assets, and maximize operating efficiency.
- Minimizing Downtime: Unplanned equipment breakdowns can lead to costly downtime, affecting production schedules, customer satisfaction, and profitability. Effective MRO management ensures the availability of critical spare parts, tools, and services required for timely repairs. By minimizing downtime, organizations can maintain smooth operations, meet customer demands, and avoid financial losses.
- Enhancing Safety and Compliance: MRO activities include ensuring the availability of safety equipment, performing necessary inspections, and conducting repairs to maintain a safe working environment. Compliance with safety regulations is essential to protect employees, assets, and the organization from potential liabilities. Proper MRO management ensures the necessary measures are in place to safeguard workers and maintain regulatory compliance.
- Cost Control and Optimization: Inefficient MRO management can lead to excess inventory, duplicate purchases, and unnecessary maintenance costs. By implementing effective inventory management practices, optimizing procurement processes, and leveraging predictive maintenance techniques, organizations can reduce inventory carrying costs, streamline operations, and achieve cost savings.
- Supplier Relationship Management: MRO activities often involve engaging with suppliers and service providers for the procurement of spare parts, maintenance services, and other necessities. Developing strong relationships with reliable vendors not only ensures the timely availability of required materials but also opens avenues for collaboration, negotiation, and cost-saving opportunities.
In summary, proper MRO management in the supply chain provides organizations with the means to maintain equipment efficiency, minimize downtime, ensure safety and compliance, control costs, and foster productive supplier relationships. By prioritizing and optimizing MRO activities, organizations can achieve operational excellence, enhance customer satisfaction, and drive overall business success.
Key Components of MRO in Supply Chain
MRO in the supply chain encompasses various components that are essential for the maintenance, repair, and operation of facilities. These components ensure the availability of the necessary materials, equipment, and services required to keep operations running smoothly. Let’s explore some of the key components of MRO:
- Spare Parts: Spare parts are critical components of MRO. They include items such as replacement parts for machinery, equipment, and infrastructure. Spare parts inventory management is crucial to ensure that the right parts are available when needed to minimize downtime and enable prompt repairs.
- Tools and Equipment: Tools and equipment are necessary for performing maintenance and repair tasks effectively. This includes a wide range of tools, from hand tools to specialized equipment specific to certain industries. Real-time visibility of tool availability, proper maintenance, and tracking are essential for efficient MRO management.
- Maintenance Supplies: Maintenance supplies encompass a variety of consumable items required for upkeep and minor repairs. This can include lubricants, cleaning solutions, adhesives, sealants, and other items that support maintenance activities and ensure equipment longevity.
- Safety Equipment: Safety equipment, such as protective gear, safety signs, fire prevention equipment, and emergency response tools, is crucial for creating a safe working environment. MRO management involves maintaining an adequate supply of safety equipment and ensuring that it is regularly inspected and upgraded as necessary.
- Service Providers: MRO activities often require the expertise of specialized service providers, such as equipment maintenance and repair technicians, contractors, or facility management companies. Effective vendor management and timely engagement with service providers are essential for accessing the necessary expertise and ensuring quality repairs and maintenance.
- Data and Documentation: MRO management involves capturing relevant data and documentation related to maintenance schedules, repair history, warranties, equipment specifications, and compliance records. Having a centralized repository for this information enables easy access, tracking, and analysis, facilitating data-driven decision-making and effective planning.
These components of MRO in the supply chain are interconnected and form the foundation for ensuring continuous operation, minimizing downtime, and optimizing asset performance. Proper inventory management, proactive maintenance planning, reliable supplier relationships, and implementing digital tools and technologies all play a vital role in managing these components effectively.
By understanding the key components of MRO and addressing them efficiently, organizations can streamline their supply chain operations, reduce costs, and enhance overall operational effectiveness.
MRO Categories in Supply Chain
MRO activities in the supply chain cover a broad range of categories, each serving a specific purpose to ensure smooth operations and minimize disruptions. Let’s take a closer look at some common categories within MRO:
- Facility Maintenance: This category includes the maintenance and repair of the physical facilities where the organization operates. It encompasses tasks such as HVAC systems maintenance, plumbing repairs, electrical work, and general upkeep of buildings and infrastructure.
- Production Equipment and Machinery: This category focuses on the maintenance, repair, and replacement of machinery and equipment used in the production process. It includes regular inspections, lubrication, calibration, and any necessary repairs to ensure the machines operate at their optimal capacity.
- Safety and Personal Protective Equipment (PPE): MRO activities related to safety and PPE involve managing the supply and maintenance of safety equipment, such as helmets, gloves, goggles, and protective clothing. This category also covers safety equipment inspections, testing, and compliance with regulatory standards.
- Utilities and Energy Management: MRO activities in this category focus on the management and maintenance of utilities, including electricity, water, gas, and other energy sources. Monitoring energy usage, identifying inefficiencies, and implementing conservation measures are crucial for optimizing energy consumption and reducing costs.
- IT Infrastructure and Systems: MRO activities within IT infrastructure involve managing and maintaining computer systems, hardware, software, and network infrastructure. This includes regular updates, patching, troubleshooting, and responding to IT-related issues to ensure smooth operations of the organization’s technology systems.
- Logistics and Transportation: MRO activities in logistics and transportation focus on the management of fleet vehicles, transportation equipment, and facilities such as warehouses and distribution centers. Regular inspections, maintenance, repairs, and ensuring compliance with safety regulations are vital for efficient logistics operations.
These categories provide a framework for organizing and managing MRO activities in the supply chain. It is important to note that the specific categories may vary depending on the industry and nature of the organization’s operations.
Effectively categorizing and managing MRO activities allows organizations to allocate resources, develop maintenance schedules, and prioritize actions based on criticality and impact. By systematically addressing the different MRO categories, organizations can reduce downtime, enhance productivity, and optimize overall operational efficiency.
Challenges in MRO Management in Supply Chain
While MRO management is essential for ensuring optimal operational efficiency in the supply chain, it comes with its own set of challenges. Let’s explore some of the common challenges organizations face when managing MRO:
- Inventory Management: One of the biggest challenges is maintaining an accurate and well-organized inventory of spare parts, tools, and supplies. Overstocking can tie up capital and storage space, while understocking can lead to delays in repairs and increased downtime. Striking the right balance requires regular inventory assessments, forecasting, and efficient procurement processes.
- Data and Documentation: Managing MRO data and documentation can be challenging, especially when dealing with a large number of assets, vendors, and service providers. Ensuring that records are up-to-date, easily accessible, and organized can require significant effort and proper systems for data management.
- Vendor Management: Engaging and managing multiple vendors for MRO-related services and supplies can be complex. It involves establishing strong relationships, negotiating contracts, monitoring performance, and ensuring timely delivery of materials and services. Quality control and maintaining visibility across the vendor network is crucial for effective MRO management.
- Maintenance Planning: Developing and executing maintenance plans can be challenging, particularly when addressing a large number of assets with different maintenance requirements. Optimizing maintenance schedules, coordinating resources, and ensuring minimal disruption to operations all require careful planning, efficient scheduling tools, and proper allocation of resources.
- Technological Integration: Incorporating and leveraging technology can pose challenges, especially for organizations with legacy systems and manual processes. Integration of maintenance management systems, IoT-enabled asset monitoring, and predictive analytics can improve MRO effectiveness, but it requires investment, training, and the right change management approach.
- Budget Constraints: Balancing the needs of maintenance and repair with budget limitations can be a challenge. Limited financial resources may require organizations to prioritize MRO activities, which can lead to difficult decisions and potential delays in addressing less critical repairs.
Addressing these challenges requires a strategic approach and proactive management. Organizations should invest in digital tools, automation, and data analytics to streamline processes, improve visibility, and enhance decision-making capabilities. Effective communication and collaboration across departments and with vendors are also essential for ensuring smooth MRO management in the supply chain.
By identifying and overcoming these challenges, organizations can optimize MRO operations, reduce costs, minimize downtime, and enhance overall supply chain efficiency.
Best Practices for MRO Management in Supply Chain
Effectively managing MRO activities in the supply chain requires the implementation of best practices to optimize operations, reduce costs, and ensure operational continuity. Here are some key best practices for MRO management:
- Centralize MRO Processes: Establish a centralized system for managing MRO activities, including inventory management, procurement, and maintenance planning. This allows for better visibility, coordination, and control over MRO operations.
- Implement Effective Inventory Management: Regularly assess and optimize inventory levels to strike the right balance between having necessary spare parts and minimizing excess stock. Utilize inventory management systems and techniques such as Just-in-Time (JIT) inventory to reduce carrying costs and improve operational efficiency.
- Prioritize Preventive Maintenance: Implement a proactive approach to maintenance by prioritizing preventive maintenance tasks. Regular inspections, scheduled maintenance, and predictive maintenance techniques can help identify issues before they escalate into costly breakdowns.
- Establish Robust Vendor Management: Develop strong relationships with reliable vendors and service providers. Regularly evaluate vendor performance, negotiate contracts, and establish clear communication channels to ensure timely delivery of materials and services.
- Utilize Technology and Automation: Leverage technology solutions to streamline MRO processes. Implement maintenance management systems, IoT-enabled sensors for asset monitoring, predictive analytics tools, and automated workflows to improve efficiency and accuracy in MRO management.
- Standardize Processes and Documentation: Develop standardized procedures and documentation for MRO activities. This ensures consistency in maintenance processes, facilitates knowledge sharing, and enables effective training of maintenance staff.
- Implement Effective Data Management: Maintain accurate and up-to-date data related to assets, maintenance history, and supplier performance. Utilize digital tools for data analysis, reporting, and decision-making to identify trends, optimize maintenance schedules, and predict future needs.
- Promote Cross-Functional Collaboration: Foster collaboration among various departments involved in MRO activities, including maintenance, procurement, operations, and finance. Encourage open communication, knowledge sharing, and cross-functional problem-solving to improve overall MRO management.
- Continuous Improvement and Evaluation: Regularly monitor and evaluate MRO performance using key performance indicators (KPIs). Identify areas for improvement, measure the impact of implemented changes, and continuously strive for operational excellence.
By following these best practices, organizations can significantly enhance their MRO management capabilities, minimize downtime, reduce costs, and improve overall supply chain efficiency.
Technology and Automation in MRO Management
Technology and automation have revolutionized various aspects of business operations, and MRO management is no exception. By leveraging innovative tools and digital systems, organizations can enhance efficiency, accuracy, and cost-effectiveness in managing MRO activities in the supply chain. Let’s explore the key areas where technology and automation can make a significant impact:
- Maintenance Management Systems (CMMS/EAM): Implementing computerized maintenance management systems (CMMS) or enterprise asset management (EAM) software provides a centralized platform to manage maintenance tasks, track work orders, schedule preventive maintenance, and analyze equipment performance. These systems improve work planning, streamline maintenance workflows, and enhance visibility into asset health and maintenance history.
- IoT-Enabled Asset Monitoring: Integrating IoT-enabled sensors into critical equipment allows organizations to monitor asset health in real-time. These sensors can collect data on performance, temperature, vibration, and other parameters, providing insights into asset condition and triggering alerts when maintenance is required. This enables predictive maintenance, reducing the likelihood of unplanned failures and optimizing maintenance schedules.
- Predictive Analytics: Advanced data analytics techniques, combined with machine learning algorithms, enable organizations to identify patterns, anomalies, and predict future equipment failures. By analyzing historical maintenance data, sensor readings, and other relevant factors, predictive analytics systems help optimize maintenance schedules, reduce downtime, and improve asset reliability.
- Mobile Applications: Mobile apps enable technicians to access work orders, manuals, and equipment information conveniently from their smartphones or tablets. This real-time access to data enhances collaboration, simplifies communication, and allows for timely updates on maintenance tasks and repairs. Technicians can also capture and upload photos, notes, and work details directly into the system, improving documentation and knowledge sharing.
- Automated Inventory Management: Implementing automated inventory management systems optimizes MRO inventory levels, reduces carrying costs, and ensures the availability of critical spare parts. These systems monitor inventory levels, automatically reorder items when they reach a predefined threshold, and provide real-time visibility into stock levels, usage, and reorder lead times.
- Integration and Data Sharing: Integrating MRO systems with other business systems, such as enterprise resource planning (ERP), financial management, and procurement, enables seamless data sharing and process automation. This integration streamlines workflows, avoids duplicate data entry, and ensures accurate and up-to-date information across departments.
By adopting these technological advancements and embracing automation, organizations can significantly enhance the efficiency and effectiveness of their MRO management processes. These technologies not only streamline operations but also empower organizations to make data-driven decisions, optimize maintenance schedules, reduce downtime, and achieve overall cost savings in the supply chain.
Conclusion
MRO management is an essential aspect of supply chain operations, ensuring the smooth functioning and upkeep of facilities, minimizing downtime, and optimizing overall efficiency. In this article, we explored the definition of MRO in the supply chain and highlighted its importance in maintaining equipment efficiency, minimizing downtime, enhancing safety, and controlling costs.
We discussed the key components of MRO, including spare parts, tools and equipment, maintenance supplies, safety equipment, service providers, and data and documentation. These components form the foundation of effective MRO management, enabling organizations to address maintenance and repair needs promptly and optimize asset performance.
Furthermore, we examined the challenges organizations face in managing MRO activities, such as inventory management, data and documentation, vendor management, maintenance planning, technological integration, and budget constraints. By understanding and addressing these challenges, organizations can enhance their MRO management capabilities and overcome potential pitfalls.
To ensure efficient MRO management, we discussed best practices such as centralizing MRO processes, implementing effective inventory management strategies, prioritizing preventive maintenance, establishing robust vendor management, utilizing technology and automation, standardizing processes and documentation, promoting cross-functional collaboration, and continuously evaluating performance for continuous improvement.
Lastly, we explored how technology and automation have revolutionized MRO management in the supply chain. Systems such as maintenance management software, IoT-enabled asset monitoring, predictive analytics, mobile applications, and automated inventory management have enabled organizations to enhance efficiency, accuracy, and cost-effectiveness in managing MRO operations.
In conclusion, effective MRO management plays a vital role in maintaining optimal operational efficiency, minimizing downtime, and ensuring overall supply chain success. By implementing best practices and leveraging technology and automation, organizations can optimize MRO processes, reduce costs, enhance safety, and achieve operational excellence in their supply chain operations.