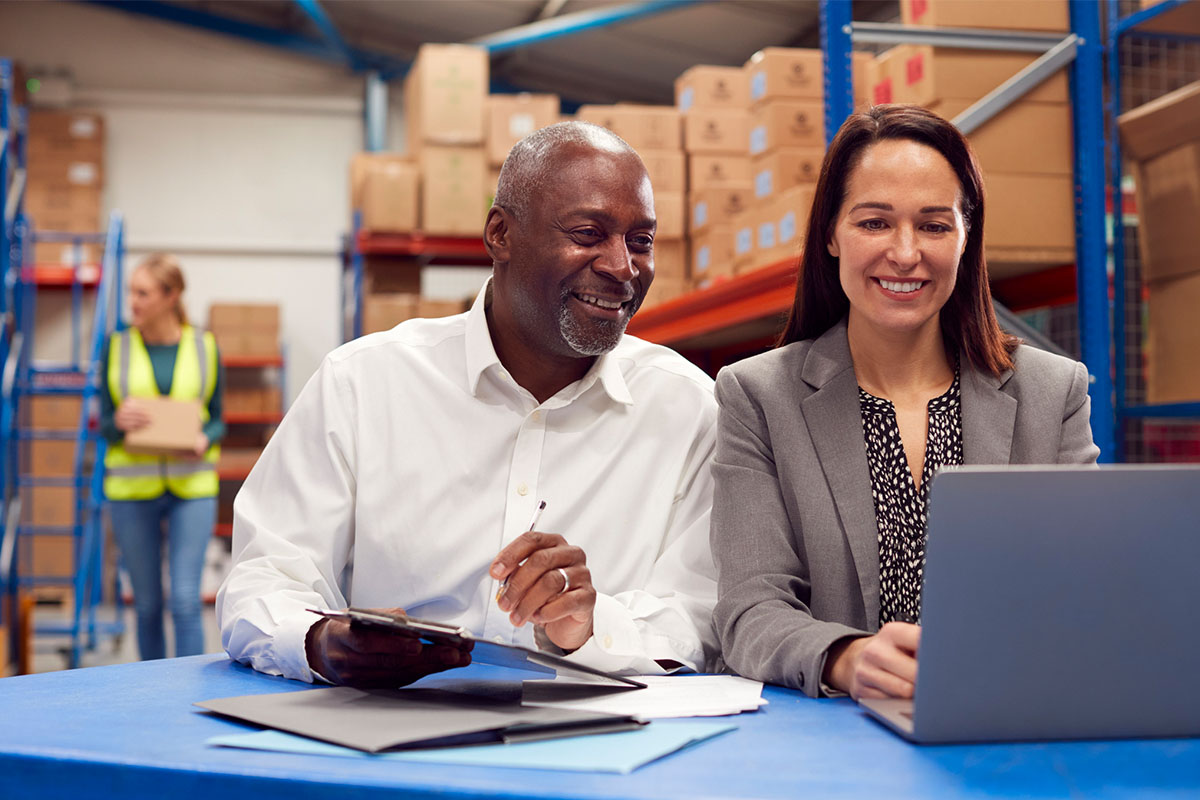
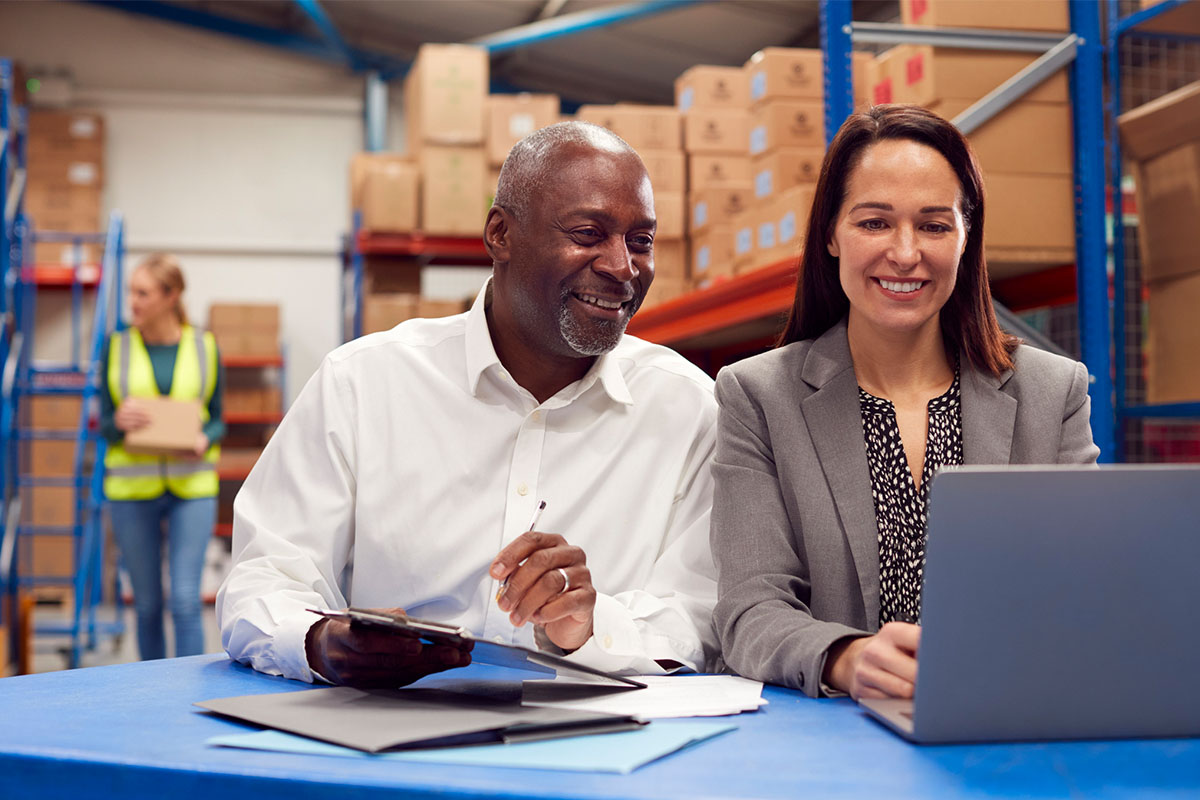
Finance
What Is A Supply Chain Planning System?
Published: October 19, 2023
Learn what a supply chain planning system is and how it can optimize finance operations. Improve efficiency and profitability with effective planning and management.
(Many of the links in this article redirect to a specific reviewed product. Your purchase of these products through affiliate links helps to generate commission for LiveWell, at no extra cost. Learn more)
Table of Contents
- Introduction
- Definition and Importance of Supply Chain Planning System
- Key Components of a Supply Chain Planning System
- Demand Planning
- Inventory Planning and Optimization
- Production Planning and Scheduling
- Distribution Planning and Logistics
- Supply Chain Analytics and Reporting
- Integration and Collaboration
- Benefits of Implementing a Supply Chain Planning System
- Challenges and Considerations in Implementing a Supply Chain Planning System
- Best Practices for Successful Supply Chain Planning System Implementation
- Conclusion
Introduction
A supply chain planning system plays a crucial role in today’s complex and rapidly changing business landscape. It provides organizations with the ability to effectively manage and optimize their end-to-end supply chain processes. From demand planning to production scheduling, inventory optimization to distribution planning, a supply chain planning system enables businesses to streamline operations, reduce costs, and improve customer satisfaction.
In essence, a supply chain planning system is a set of interconnected tools, processes, and technologies that facilitate the planning and execution of all supply chain activities. It enables organizations to forecast demand, align production capacities, optimize inventory levels, and plan efficient transportation and logistics operations. In doing so, it helps businesses achieve operational excellence, enhance supply chain visibility, and respond faster to market changes and customer demands.
In today’s highly competitive and globalized business environment, a well-designed and integrated supply chain planning system is crucial for organizations to maintain a competitive edge. It provides them with the ability to anticipate market trends, optimize their resources, and deliver products to customers in a timely and cost-effective manner.
Implementing a supply chain planning system, however, is not a one-size-fits-all approach. Each organization has unique needs, complexities, and challenges. Therefore, it is important to carefully evaluate the specific requirements of the business and select a planning system that is tailored to its needs.
In this article, we will explore the key components of a supply chain planning system, the benefits it offers, the challenges in implementing such a system, and best practices for successful implementation. Whether you are a small business or a multinational corporation, understanding the importance and functionalities of a supply chain planning system can help you optimize your operations and achieve sustainable growth.
Definition and Importance of Supply Chain Planning System
A supply chain planning system is a comprehensive software solution that enables organizations to effectively plan, manage, and optimize their supply chain activities. It encompasses a range of tools and processes that enable businesses to forecast demand, determine optimal inventory levels, plan production schedules, and coordinate logistics and distribution operations.
The importance of a supply chain planning system cannot be overstated in today’s dynamic business environment. Here are a few key reasons why organizations rely on these systems:
- Improved Forecast Accuracy: A supply chain planning system helps businesses forecast demand more accurately by utilizing historical data, market trends, and other relevant factors. This enables organizations to align their production capacities, optimize inventory levels, and eliminate stockouts or excess inventory.
- Enhanced Operational Efficiency: By automating and streamlining supply chain processes, a planning system improves overall operational efficiency. It enables businesses to optimize resource allocation, reduce lead times, streamline production schedules, and improve order fulfillment rates. This results in reduced costs, improved customer satisfaction, and increased competitiveness.
- Effective Inventory Management: Proper inventory management is critical to meeting customer demand while minimizing holding costs. A supply chain planning system helps organizations optimize inventory levels, reduce obsolescence, and ensure timely replenishment. This results in improved working capital management and increased profitability.
- Optimized Production Planning: By utilizing advanced algorithms and analytics, a supply chain planning system helps businesses determine optimal production schedules. It considers various factors such as capacity constraints, material availability, and customer demand to ensure efficient resource utilization and on-time delivery.
- Streamlined Logistics and Distribution: A planning system enables businesses to better manage transportation, warehousing, and distribution operations. It optimizes route planning, reduces transportation costs, minimizes delivery lead times, and improves overall supply chain visibility.
By implementing a supply chain planning system, organizations gain better visibility and control over their supply chain processes. They can identify bottlenecks, anticipate disruptions, and make informed decisions to mitigate risks and optimize their operations.
In summary, a supply chain planning system is an essential tool for organizations across industries. It helps them effectively manage their supply chain activities, improve efficiency, reduce costs, and enhance customer satisfaction. By leveraging the power of data analytics, automation, and optimization algorithms, businesses can gain a competitive advantage and achieve sustainable growth in today’s complex and highly demanding business landscape.
Key Components of a Supply Chain Planning System
A supply chain planning system comprises several key components that work together to enable organizations to effectively plan and manage their supply chain operations. These components include:
- Demand Planning: Demand planning is a critical component of a supply chain planning system. It involves forecasting customer demand for products or services based on historical data, market trends, and other relevant factors. By accurately predicting demand, organizations can optimize production schedules, inventory levels, and resource allocation to meet customer needs efficiently.
- Inventory Planning and Optimization: Inventory planning is another vital component of a supply chain planning system. It involves determining the optimal levels of inventory to meet customer demand while minimizing holding costs. The system takes into account factors such as lead times, demand variability, and service level targets to ensure that the right amount of inventory is available at the right time and in the right location.
- Production Planning and Scheduling: This component focuses on optimizing production schedules and resource allocation to meet customer demand efficiently. It involves considering factors such as capacity constraints, material availability, and lead times to minimize production costs, reduce cycle times, and improve overall operational efficiency.
- Distribution Planning and Logistics: Distribution planning and logistics component of a supply chain planning system helps organizations optimize their transportation, warehousing, and distribution operations. It includes tasks such as route optimization, load planning, and carrier selection to minimize transportation costs, reduce lead times, and improve overall supply chain visibility.
- Supply Chain Analytics and Reporting: Supply chain analytics and reporting provide organizations with valuable insights into their supply chain performance. This component collects and analyzes data from various sources to identify trends, monitor key performance indicators (KPIs), and generate reports and dashboards. These insights help organizations make informed decisions, optimize operations, and continuously improve their supply chain performance.
- Integration and Collaboration: Integration and collaboration are essential components of a supply chain planning system. The system should be able to integrate seamlessly with other enterprise systems, such as ERP (Enterprise Resource Planning) and CRM (Customer Relationship Management), to share data and provide a unified view of the supply chain. Additionally, it should facilitate collaboration among different stakeholders, including suppliers, distributors, and customers, to improve coordination and responsiveness across the entire supply chain.
By integrating these components into a cohesive supply chain planning system, organizations can achieve better visibility, maximize operational efficiency, minimize costs, and effectively meet customer demand. Each component plays a crucial role in optimizing specific aspects of the supply chain and contributing to overall supply chain excellence.
Demand Planning
Demand planning is a critical component of a supply chain planning system. It involves forecasting customer demand for products or services based on historical data, market trends, and other relevant factors. By accurately predicting demand, organizations can optimize production schedules, inventory levels, and resource allocation to meet customer needs efficiently.
The process of demand planning typically involves the following key steps:
- Data Collection: Organizations gather historical sales data, market research, and other relevant information to understand past demand patterns.
- Statistical Forecasting: Demand planners utilize advanced statistical models and algorithms to generate quantitative forecasts. These models consider variables such as seasonality, trends, and historical demand patterns to predict future demand.
- Collaborative Planning: Demand planners collaborate with sales teams, marketing departments, and other stakeholders to gather insights and inputs that can refine the demand forecast. This collaborative approach helps incorporate qualitative information and market intelligence into the planning process.
- Exception Management: Demand planners identify and manage exceptions or anomalies in the demand forecast. This involves adjusting the forecast based on specific events, promotions, or market fluctuations that may impact demand.
- Validation and Review: The demand forecast goes through a validation and review process. Demand planners compare the forecasted demand with actual sales data and make necessary adjustments based on any discrepancies or changes in market conditions.
- Integration with Supply Chain Operations: The demand plan is communicated to other supply chain functions, such as inventory planning, production planning, and procurement. This coordination ensures alignment between demand and supply, avoiding stockouts or excess inventory and optimizing resource allocation.
A well-executed demand planning process provides organizations with several benefits:
- Improved Customer Service: Accurate demand planning minimizes stockouts and ensures that products are available when customers need them. This results in improved customer satisfaction and loyalty.
- Optimized Inventory Levels: Demand planning helps organizations maintain optimal inventory levels by aligning supply with expected demand. This prevents overstocking or understocking and reduces holding costs.
- Enhanced Production Efficiency: By aligning production schedules with demand forecasts, organizations can optimize resource utilization, reduce setup times, and improve overall production efficiency.
- Effective Promotion and Pricing Strategies: Demand planning provides insights into market demand patterns and consumer buying behavior. This enables organizations to develop targeted promotion and pricing strategies to maximize revenue and profitability.
In summary, demand planning is a crucial component of a supply chain planning system. By accurately forecasting demand and aligning supply chain operations accordingly, organizations can optimize resource allocation, improve customer service, and achieve better overall supply chain performance.
Inventory Planning and Optimization
Inventory planning and optimization is a vital component of a supply chain planning system. It involves determining the optimal levels of inventory to meet customer demand while minimizing holding costs. The goal is to strike a balance between having enough inventory to fulfill orders promptly without excessive inventory carrying costs.
The process of inventory planning and optimization typically involves the following key steps:
- Demand Forecast: Inventory planners utilize demand forecasts generated through demand planning to estimate future customer demand. These forecasts serve as inputs for determining the desired inventory levels.
- Lead Time Analysis: Understanding lead times for procuring or manufacturing products is crucial for inventory planning. It allows businesses to factor in the time required to replenish inventory accurately.
- Safety Stock Management: Safety stock helps mitigate the risk of stockouts due to forecast errors, supply disruptions, or unexpected demand spikes. Inventory planners determine the appropriate level of safety stock to maintain based on factors such as demand variability, lead times, and desired service levels.
- Economic Order Quantity (EOQ): EOQ is a calculation that helps determine the optimal order quantity for items with steady demand. It considers factors like carrying costs, ordering costs, and demand rates to find the order size that minimizes total inventory costs.
- Reorder Point Calculation: The reorder point is the inventory level at which a new order should be placed to replenish stock. It is calculated by considering the lead time, demand variability, and safety stock requirements.
- Inventory Monitoring and Control: The supply chain planning system continuously monitors inventory levels and triggers replenishment orders when the stock falls below the reorder point. It ensures that inventory is maintained at optimal levels while avoiding stockouts or excess inventory.
- ABC Analysis: Inventory planners classify items based on their value contribution to the business, typically using ABC analysis. This classification helps prioritize inventory management efforts and ensure optimal allocation of resources.
Effective inventory planning and optimization offer several benefits to organizations:
- Improved Customer Service: Adequate inventory levels enable businesses to meet customer demand promptly and reduce the risk of backorders or stockouts. This improves customer satisfaction and loyalty.
- Reduced Holding Costs: By optimizing inventory levels, organizations can minimize holding costs associated with storage, insurance, obsolescence, and depreciation. This leads to improved working capital management and increased profitability.
- Efficient Resource Allocation: Inventory planning helps organizations allocate resources more effectively. It ensures that inventory is distributed appropriately based on demand patterns, production capacities, and customer requirements, optimizing resource utilization.
- Lower Order Processing Costs: Optimized inventory planning and order quantities can reduce order processing costs, such as purchasing, transportation, and order fulfillment expenses. This leads to overall cost savings for the organization.
- Enhanced Supply Chain Visibility: Effective inventory planning enables better visibility into the supply chain. It provides insights into inventory turnover rates, lead times, and demand patterns, allowing organizations to make informed decisions and identify areas for improvement.
In summary, inventory planning and optimization are crucial for organizations to strike the right balance between customer service and holding costs. By leveraging data-driven insights and optimization techniques, businesses can optimize inventory levels, improve resource allocation, and enhance overall supply chain performance.
Production Planning and Scheduling
Production planning and scheduling is a vital component of a supply chain planning system. It focuses on optimizing production schedules and resource allocation to meet customer demand efficiently. The goal is to ensure that production activities are planned in a way that maximizes operational efficiency, minimizes costs, and meets customer delivery requirements.
The process of production planning and scheduling typically involves the following key steps:
- Demand Forecast: Production planners utilize the demand forecast generated through demand planning to estimate the expected customer demand. This serves as the basis for planning production volumes and schedules.
- Capacity Analysis: Production planners assess available production capacities, considering factors such as equipment capabilities, labor resources, and work center availability. This analysis helps determine production feasibility and identify potential bottlenecks or constraints.
- Master Production Schedule (MPS): The MPS is a detailed plan that specifies the quantities and timing of finished goods to be produced over a specific time period. It considers factors such as demand forecasts, available capacities, and inventory levels to ensure the right products are produced at the right time.
- Material Requirements Planning (MRP): MRP is a component of production planning that focuses on managing the materials needed for production. It involves analyzing the bill of materials, determining material availability, and generating procurement or production orders to ensure timely availability of required materials.
- Finite Capacity Scheduling: Finite capacity scheduling optimizes production schedules considering capacity constraints. It takes into account factors such as available resources, production lead times, and required changeovers to create feasible and efficient production schedules.
- Real-Time Monitoring and Adjustments: Production planners continuously monitor production progress and make adjustments as needed. This may involve reallocating resources, adjusting production priorities, or rescheduling activities in response to changes in demand or unforeseen disruptions.
- Integration with Other Supply Chain Functions: Production planning and scheduling are closely integrated with other supply chain functions such as demand planning, inventory planning, and logistics. This coordination ensures that production activities are aligned with demand forecasts, inventory levels, and distribution requirements.
Efficient production planning and scheduling offer several benefits to organizations:
- Improved Operational Efficiency: Effective production planning and scheduling ensure that production resources are utilized optimally, reducing idle time and minimizing production costs. This leads to improved operational efficiency and increased productivity.
- On-Time Delivery: By aligning production schedules with customer demand, organizations can meet delivery deadlines more consistently, enhancing customer satisfaction and loyalty.
- Reduced Lead Times: Streamlined production planning and scheduling processes help shorten lead times, enabling faster response to customer orders and reducing overall cycle times.
- Optimized Resource Allocation: Production planning ensures that resources such as labor, machinery, and raw materials are allocated efficiently to maximize their utilization and minimize costs.
- Improved Quality Control: Effective production scheduling allows for better quality control by ensuring that adequate time is allocated for each process, reducing the risk of errors or defects.
In summary, production planning and scheduling play a crucial role in optimizing production processes and meeting customer demand efficiently. By leveraging advanced planning techniques and technology, organizations can achieve improved operational efficiency, reduced lead times, and enhanced customer satisfaction.
Distribution Planning and Logistics
Distribution planning and logistics are critical components of a supply chain planning system. They focus on optimizing the movement of goods, managing transportation, and coordinating warehousing and distribution activities to ensure efficient and timely delivery of products to customers.
The process of distribution planning and logistics typically involves the following key steps:
- Route Optimization: Distribution planners analyze various factors such as distance, transportation costs, and delivery time windows to optimize the routes for product distribution. This helps minimize transportation costs and reduce delivery lead times.
- Load Planning: Distribution planners determine the most efficient way to load products onto vehicles, considering factors such as product characteristics, weight restrictions, and delivery schedules. This maximizes space utilization and minimizes the number of trips required.
- Carrier Selection: Distribution planners select carriers based on specific requirements such as delivery speed, cost-effectiveness, and reliability. They evaluate factors like carrier capabilities, service levels, and performance history to make informed decisions.
- Warehouse Management: Distribution planning encompasses effective warehouse management to ensure efficient storage and retrieval of products. It involves optimizing warehouse layout, inventory placement, and order picking processes to minimize handling time and improve overall operational efficiency.
- Order Fulfillment: Distribution planners coordinate the fulfillment of customer orders by efficiently allocating inventory, picking products from the warehouse, and preparing them for shipment. This includes packaging, labeling, and documentation to ensure accurate and timely order fulfillment.
- Transportation Management: Distribution planners manage transportation activities, including arranging pickups, tracking shipments, and monitoring transportation service levels. They ensure that products are transported safely, on time, and at the lowest possible cost.
- Reverse Logistics: Distribution planning also encompasses handling returns and managing the reverse logistics process. This involves managing product returns, repairing or refurbishing returned items, and determining appropriate disposition actions such as resale, recycling, or disposal.
Efficient distribution planning and logistics offer several benefits to organizations:
- Improved Customer Service: Effective distribution planning ensures that products are delivered to customers in a timely and efficient manner. This leads to improved customer satisfaction, faster order fulfillment, and increased customer loyalty.
- Reduced Transportation Costs: Optimized route planning, load optimization, and carrier selection help minimize transportation costs. This contributes to overall cost savings for the organization and increased profitability.
- Reduced Lead Times: Streamlined distribution planning and logistics processes enable faster and more efficient delivery of products, reducing lead times and improving overall responsiveness to customer demands.
- Improved Supply Chain Visibility: Effective distribution planning provides better visibility into the supply chain by tracking shipments and monitoring transportation activities. This allows organizations to proactively identify and address potential bottlenecks or disruptions.
- Enhanced Operational Efficiency: Optimized warehouse management, order fulfillment processes, and transportation management contribute to improved operational efficiency. This includes minimizing manual handling, reducing errors, and maximizing resource utilization.
In summary, distribution planning and logistics are crucial for ensuring the efficient and timely movement of products throughout the supply chain. By focusing on optimal route planning, load optimization, warehouse management, and transportation, organizations can improve customer service, reduce costs, and enhance overall supply chain performance.
Supply Chain Analytics and Reporting
Supply chain analytics and reporting is a vital component of a supply chain planning system. It involves collecting and analyzing data from various sources to gain valuable insights into supply chain performance. These insights help organizations make informed decisions, monitor key performance indicators (KPIs), and identify areas for improvement.
The process of supply chain analytics and reporting typically involves the following key steps:
- Data Collection: Organizations collect data from various sources within the supply chain, including ERP systems, transportation management systems, inventory systems, and other relevant databases. This data includes information on sales, production, inventory levels, transportation activities, and more.
- Data Integration and Cleansing: The collected data is integrated and cleansed to ensure accuracy and consistency. This involves resolving data discrepancies, eliminating duplicate or irrelevant information, and merging datasets from different sources.
- Data Analysis: Supply chain analytics tools and techniques are used to analyze the integrated data. This includes applying statistical models, data mining algorithms, machine learning, and visualization techniques to uncover patterns, trends, and insights.
- Key Performance Indicators (KPIs) Monitoring: Supply chain analytics focuses on monitoring and tracking KPIs that measure performance across various aspects of the supply chain. This may include metrics such as on-time delivery, inventory turnover, fill rates, order accuracy, and more.
- Reporting and Visualization: The analyzed data is transformed into meaningful reports and visual representations. Dashboards, charts, and graphs are created to present the findings in a clear and concise manner, enabling stakeholders to understand the supply chain performance at a glance.
- Performance Evaluation: The supply chain analytics and reporting process enable organizations to evaluate their performance against set goals and benchmarks. It helps identify areas of improvement, set objectives for continuous improvement, and track progress over time.
- Decision Support: Insights gained from supply chain analytics and reporting provide decision-makers with the necessary information to make data-driven decisions. It helps in identifying cost-saving opportunities, improving operational efficiency, and enhancing overall supply chain performance.
Supply chain analytics and reporting yield several benefits to organizations:
- Data-Driven Decision-Making: By leveraging insights from supply chain analytics, organizations can make informed decisions based on data rather than relying solely on intuition or past experiences. This leads to improved decision-making accuracy and effectiveness.
- Improved Operational Efficiency: Supply chain analytics helps identify inefficiencies, bottlenecks, and areas for process improvement. This allows organizations to streamline operations, optimize resource utilization, reduce costs, and enhance overall operational efficiency.
- Enhanced Supply Chain Visibility: By analyzing data from different sources, supply chain analytics provides better visibility into the supply chain. It helps in identifying areas of weakness, tracking performance, and proactively managing risks or disruptions.
- Continuous Improvement: Supply chain analytics identifies trends and patterns that allow organizations to continuously improve their supply chain processes. By monitoring KPIs and performance metrics, organizations can set goals, track progress, and implement targeted improvements over time.
- Proactive Problem-Solving: Supply chain analytics enables organizations to identify issues or potential problems before they escalate. This helps in taking preventive measures, mitigating risks, and maintaining a smooth and efficient supply chain operation.
In summary, supply chain analytics and reporting play a crucial role in providing insights into supply chain performance. By leveraging data-driven insights and visualization, organizations can make informed decisions, monitor performance, and continuously improve their supply chain processes.
Integration and Collaboration
Integration and collaboration are essential components of a supply chain planning system. They involve the seamless exchange of information, data, and resources among various stakeholders within the supply chain ecosystem. By integrating different functions and fostering collaboration, organizations can achieve better coordination, visibility, and responsiveness.
The process of integration and collaboration in a supply chain planning system typically involves the following key aspects:
- Integration with Enterprise Systems: The supply chain planning system needs to integrate smoothly with other enterprise systems, including ERP (Enterprise Resource Planning) and CRM (Customer Relationship Management). This integration allows for the seamless flow of data and information across different functions and ensures a unified view of the supply chain.
- Data Integration and Sharing: Integration facilitates the exchange of data across different systems and functions within the supply chain. This includes sharing data related to demand forecasts, inventory levels, production schedules, transportation activities, and more. Data integration enables better visibility and decision-making across the supply chain.
- Collaborative Planning: Collaboration among various stakeholders within the supply chain is crucial for effective planning. This involves working together with suppliers, manufacturers, distributors, and customers to align strategies, share insights, and collaborate on demand planning, production planning, and logistics. Collaborative planning ensures that all parties are aligned and working towards common supply chain goals.
- Real-Time Communication: Integration and collaboration require real-time communication channels to facilitate quick decision-making and response to changes. This may involve using communication tools, such as web portals, mobile apps, or cloud-based platforms, that enable stakeholders to exchange information, share updates, and address issues in a timely manner.
- Shared Performance Metrics: Establishing shared performance metrics and KPIs promotes collaboration and aligns stakeholders’ goals. By defining common metrics across the supply chain, such as on-time delivery, fill rates, or inventory turns, stakeholders can work together towards achieving shared objectives and identifying areas for improvement.
- Information Transparency: Integration and collaboration promote information transparency by providing stakeholders with access to relevant data and insights. This transparency enhances trust, fosters better decision-making, and enables joint problem-solving. It also helps in identifying and addressing issues or bottlenecks more effectively.
- Shared Risk and Reward: Collaboration involves sharing risks and rewards across the supply chain. This may include sharing demand forecasts, production plans, or inventory data to enable more accurate planning and risk mitigation. It also involves implementing collaborative mechanisms, such as vendor-managed inventory or consignment arrangements, to align incentives and create win-win situations.
Integration and collaboration within a supply chain planning system offer several benefits to organizations:
- Improved Coordination: Integration and collaboration streamline communication and coordination among supply chain stakeholders. This leads to better alignment, reduced bottlenecks, and improved overall operational efficiency.
- Enhanced Responsiveness: By sharing real-time information and insights, integration and collaboration enable stakeholders to respond quickly to changes in demand, supply, or market conditions. This agility enhances the ability to meet customer needs efficiently and adapt to dynamic business environments.
- Reduced Lead Times: Seamless integration and collaboration help reduce lead times by minimizing communication delays and facilitating faster decision-making. This results in faster order processing, production, and delivery.
- Improved Customer Satisfaction: Integration and collaboration contribute to better customer satisfaction by enabling accurate and timely fulfillment of customer orders. This includes meeting customer delivery expectations, providing real-time order status updates, and resolving issues or inquiries promptly.
- Optimized Resource Utilization: Integration and collaboration enable better coordination of resources, such as inventory, production capacities, and transportation. This leads to more efficient resource allocation, reduced waste, and improved overall supply chain performance.
In summary, integration and collaboration are essential for effective supply chain planning. By integrating systems, sharing data, fostering collaboration, and promoting information transparency, organizations can leverage the collective expertise and resources of their supply chain partners to achieve better coordination, responsiveness, and customer satisfaction.
Benefits of Implementing a Supply Chain Planning System
Implementing a supply chain planning system offers numerous benefits for organizations across industries. It enables businesses to optimize their supply chain operations, improve operational efficiency, and enhance customer satisfaction. Here are some key benefits of implementing a supply chain planning system:
- Improved Demand Forecasting: A supply chain planning system helps organizations forecast customer demand more accurately. By considering historical data, market trends, and other relevant factors, businesses can optimize production schedules, inventory levels, and resource allocation to meet customer needs efficiently.
- Operational Efficiency: Implementing a supply chain planning system streamlines and automates supply chain processes, reducing manual efforts, errors, and cycle times. This results in improved operational efficiency, reduced costs, and increased productivity across the entire supply chain.
- Optimized Inventory Management: A supply chain planning system enables businesses to optimize inventory levels. By aligning inventory with demand forecasts, organizations can reduce excess inventory and avoid stockouts, leading to improved working capital management and reduced holding costs.
- Enhanced Customer Service: With a supply chain planning system in place, organizations can meet customer demands more effectively. By ensuring on-time delivery, accurate order fulfillment, and better product availability, businesses can enhance customer satisfaction and loyalty.
- Reduced Lead Times: Supply chain planning systems facilitate efficient coordination and resource allocation, resulting in reduced lead times. This allows organizations to respond more quickly to customer orders, optimize production schedules, and minimize cycle times.
- Increased Agility: Implementing a supply chain planning system allows businesses to be more agile and responsive to market changes. With better visibility and real-time insights, organizations can quickly adjust production, procurement, and distribution strategies to meet changing customer demands.
- Improved Supply Chain Visibility: Supply chain planning systems provide organizations with better visibility into their supply chain operations. Businesses can track inventory levels, monitor production schedules, and analyze performance metrics in real-time. This visibility enables proactive decision-making and better risk management.
- Cost Reduction: By optimizing inventory levels, improving resource allocation, and minimizing lead times, organizations can reduce costs throughout the supply chain. This includes lower inventory carrying costs, reduced transportation expenses, and improved overall cost efficiency.
- Better Decision-Making: Supply chain planning systems generate comprehensive analytics and reports that provide valuable insights into supply chain performance. This data-driven decision-making enables organizations to make informed choices, identify areas for improvement, and drive continuous process optimization.
- Collaboration and Integration: Supply chain planning systems facilitate collaboration and integration among various stakeholders within the supply chain network. This cohesive approach aligns goals, enables data sharing, and improves communication, leading to better coordination and operational efficiency.
In summary, implementing a supply chain planning system brings numerous benefits to organizations, including improved demand forecasting, operational efficiency, inventory management, customer service, and decision-making. It enables businesses to optimize supply chain operations, reduce costs, and enhance overall supply chain performance, ultimately leading to increased competitiveness and sustainable growth.
Challenges and Considerations in Implementing a Supply Chain Planning System
While implementing a supply chain planning system can offer significant benefits, it is important to be aware of the challenges and considerations that may arise during the implementation process. Addressing these challenges and carefully considering the following factors will contribute to a successful implementation:
- Data Accuracy and Integration: One of the primary challenges is ensuring accurate and reliable data for the system. Organizations need to invest time and effort in data cleansing, integration, and validation to ensure the system receives accurate and consistent data from various sources within the supply chain.
- Change Management: Implementing a supply chain planning system often requires changes to existing processes, workflows, and roles within the organization. This can lead to resistance from employees who are accustomed to existing ways of working. Effective change management strategies, including communication, training, and stakeholder involvement, are essential to navigate these challenges successfully.
- Technology Selection and Scalability: Choosing the right supply chain planning system from the numerous available options can be overwhelming. It is crucial to select a system that aligns with the organization’s requirements, provides a user-friendly interface, and offers scalability to accommodate future growth and evolving needs.
- Organizational Alignment: Implementing a supply chain planning system requires organizational alignment and collaboration across different functions and departments. It is important to involve stakeholders from various areas of the organization, including supply chain, finance, sales, and IT, to ensure their needs are understood and incorporated into the system design.
- Data Security and Privacy: As supply chain planning systems involve handling sensitive data, organizations must prioritize data security and privacy. Implementing appropriate security measures, such as data encryption, access controls, and regular backups, helps protect critical information from unauthorized access or breaches.
- Integration with Existing Systems: Integrating the supply chain planning system with existing enterprise systems, such as ERP or CRM, can be complex. Smooth integration requires thorough understanding of data and system requirements, seamless data flow, and careful coordination between the implementation team and IT departments.
- Process Standardization and Consistency: Implementing a supply chain planning system often involves aligning and standardizing processes across different locations or business units. Organizations need to define and enforce standardized processes to ensure consistency and avoid fragmentation or discrepancies in data and operations.
- Vendor Selection and Support: Choosing the right system vendor is crucial for successful implementation. Organizations should consider factors such as vendor reputation, industry expertise, system support, and ongoing maintenance and upgrades. Clear communication and expectations during vendor selection and contracting process are essential.
- Training and Continuous Improvement: Adequate training is necessary to ensure that employees understand the functionality of the supply chain planning system and can effectively utilize its features. Continuous improvement and ongoing training programs help employees stay up to date with system changes and optimize its usage for better supply chain performance.
By addressing these challenges and considering the relevant factors, organizations can navigate the implementation process more effectively and maximize the benefits derived from a supply chain planning system.
Best Practices for Successful Supply Chain Planning System Implementation
Implementing a supply chain planning system requires careful planning and execution. To ensure a successful implementation, organizations can follow these best practices:
- Define Clear Objectives: Clearly define the objectives and expected outcomes of implementing the supply chain planning system. Align these objectives with the overall business strategy to ensure that the system supports the organization’s goals.
- Engage Stakeholders: Involve key stakeholders from different functions and levels of the organization throughout the implementation process. Their input and involvement will help foster ownership, ensure alignment with business processes, and facilitate change management.
- Thoroughly Assess Requirements: Conduct a thorough assessment of the organization’s supply chain requirements, including current processes, pain points, and future needs. Identify the functionalities and capabilities required from the planning system to meet these requirements.
- Select the Right System and Vendor: Carefully evaluate different supply chain planning systems and vendors. Consider factors such as system capabilities, scalability, vendor support, industry expertise, and compatibility with existing systems. Choose a system and vendor that best align with the organization’s needs and long-term goals.
- Invest in Data Quality and Integration: Ensure that data used by the planning system is accurate, reliable, and integrated from various sources. Invest in data cleansing, validation, and integration to provide a solid data foundation for planning and decision-making.
- Define Clear Processes and Workflows: Clearly define and document the processes and workflows that will be supported by the supply chain planning system. Standardize these processes to ensure consistency and facilitate future system expansions or integrations.
- Provide Adequate Training and Support: Develop a comprehensive training program to educate users on how to effectively use the planning system. Provide ongoing support and encourage continuous learning to maximize user adoption and optimize system usage.
- Take a Phased Approach: Break down the implementation process into smaller, manageable phases. This allows for incremental deployment, testing, and adjustments. A phased approach minimizes disruption and allows for lessons learned to be applied in subsequent phases.
- Test and Validate: Before fully deploying the planning system, conduct thorough testing and validation to ensure its accuracy, functionality, and integration with other systems. Test the system’s performance under different scenarios to identify and resolve any issues or limitations.
- Monitor and Measure: Continuously monitor and measure the performance of the supply chain planning system against defined KPIs. Regularly review system performance, user feedback, and overall business outcomes to identify areas for improvement and implement necessary adjustments.
- Promote Collaboration and Communication: Foster a culture of collaboration and open communication among supply chain stakeholders. Encourage cross-functional collaboration, information sharing, and regular feedback to optimize system utilization and drive continuous improvement.
By following these best practices, organizations can increase the likelihood of a successful supply chain planning system implementation. It sets the foundation for effective supply chain management, better decision-making, and improved overall supply chain performance.
Conclusion
Implementing a supply chain planning system is a crucial step for organizations looking to optimize their supply chain operations, improve efficiencies, and enhance customer satisfaction. By leveraging advanced technologies, data analytics, and integration capabilities, organizations can achieve better visibility, streamline processes, and make informed decisions.
We have explored the key components of a supply chain planning system, including demand planning, inventory optimization, production planning, distribution planning, supply chain analytics, and integration. Each of these components plays a vital role in creating a cohesive and efficient supply chain that can respond quickly to customer demands and market changes.
Throughout the implementation process, it is imperative to address challenges such as data accuracy, change management, technology selection, and organizational alignment. By considering these challenges and following best practices, organizations can maximize the benefits of a supply chain planning system.
The benefits of implementing a supply chain planning system are numerous. From improved demand forecasting and operational efficiency to enhanced customer service and cost reduction, organizations can gain a competitive edge and achieve sustainable growth. The system enables businesses to optimize inventory levels, reduce lead times, and make data-driven decisions that positively impact overall supply chain performance.
In conclusion, a well-designed and effectively executed supply chain planning system empowers organizations to proactively manage their supply chains, optimize resource allocation, and deliver products to customers efficiently. By embracing innovation and leveraging technology, organizations can build robust supply chains that drive operational excellence and support business growth in today’s dynamic and competitive marketplace.