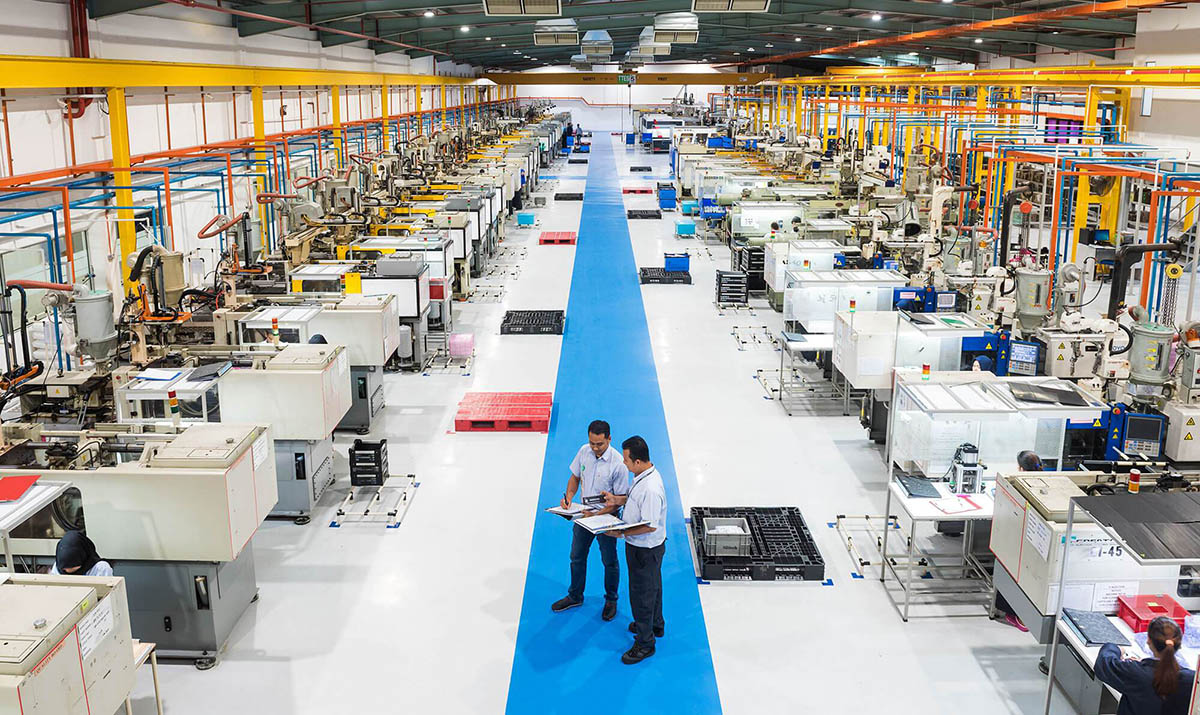
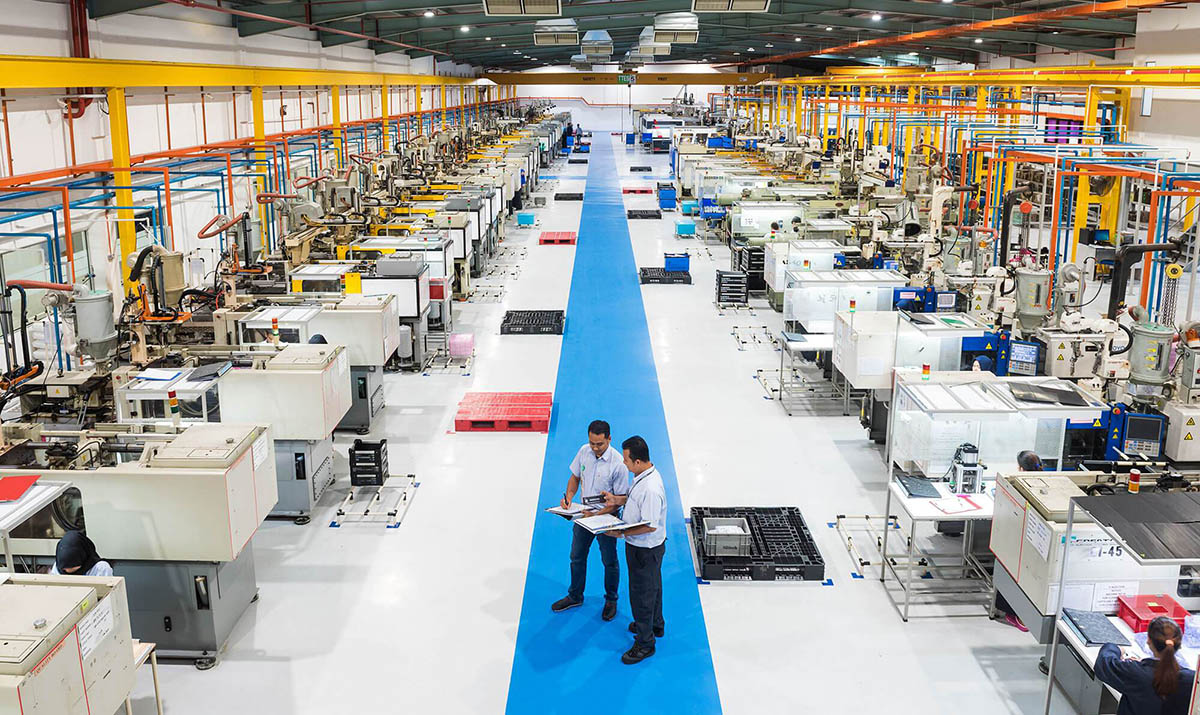
Finance
What Are Lead Times In The Supply Chain?
Published: October 19, 2023
Discover the importance of lead times in the finance supply chain. Learn how they impact efficiency, costs, and customer satisfaction.
(Many of the links in this article redirect to a specific reviewed product. Your purchase of these products through affiliate links helps to generate commission for LiveWell, at no extra cost. Learn more)
Table of Contents
- Introduction
- Definition of Lead Times in the Supply Chain
- Importance of Lead Times in the Supply Chain
- Factors Affecting Lead Times in the Supply Chain
- Types of Lead Times
- Benefits of Managing Lead Times in the Supply Chain
- Challenges in Managing Lead Times in the Supply Chain
- Strategies for Efficiently Managing Lead Times in the Supply Chain
- Conclusion
Introduction
Welcome to the world of supply chain management, where efficiency, timeliness, and cost-effectiveness are paramount. In today’s fast-paced global marketplace, businesses strive to streamline their operations and reduce lead times in order to gain a competitive edge. But what exactly are lead times in the supply chain, and why are they so important?
Simply put, lead time refers to the time it takes for a product or service to move through the various stages of the supply chain, from order placement to delivery. It encompasses every step, from procurement and production to transportation and distribution. Lead times can vary greatly depending on the complexity of the product, the availability of raw materials, and the efficiency of the supply chain processes.
Understanding and effectively managing lead times is crucial for businesses across all industries. By reducing lead times, companies can improve customer satisfaction, increase operational efficiency, reduce carrying costs, and gain a competitive advantage in the market. On the contrary, longer lead times can lead to customer dissatisfaction, increased inventory levels, and missed business opportunities.
In this article, we will delve deeper into the concept of lead times in the supply chain, explore the various factors that affect them, and discuss strategies for efficiently managing them. Whether you are a supply chain professional, a business owner, or simply curious about how the logistics of product delivery work, this article will provide you with valuable insights into the world of lead times in the supply chain.
Definition of Lead Times in the Supply Chain
Lead times in the supply chain refer to the elapsed time between the initiation of a purchase order or production order and the receipt of the finished goods or components. It encompasses the entire process from the point of order placement to the point of delivery. Understanding the different stages and components of lead times is essential for effective supply chain management.
Lead times are typically measured in units of time, such as hours, days, or weeks. They can vary significantly depending on factors such as the complexity of the product, the availability of raw materials, the distance between suppliers and manufacturers, and the efficiency of the supply chain processes.
In manufacturing, lead times involve multiple stages, including procurement, production, transportation, and distribution. Procurement lead time refers to the time it takes to source and procure raw materials from suppliers. Production lead time represents the time required to transform the raw materials into finished goods. Transportation lead time refers to the time taken for the shipment to move from one location to another. Lastly, distribution lead time refers to the time taken for the product to be delivered to the end customer.
For services, lead times can also include various stages, such as appointment scheduling, processing time, and service delivery. In industries such as healthcare and hospitality, managing lead times is crucial to ensure timely and efficient service delivery.
It is important to note that lead times are not fixed and can fluctuate based on various internal and external factors. Changes in demand, supplier availability, production capacity, transportation delays, and unforeseen disruptions can all impact lead times in the supply chain.
By closely monitoring and managing lead times, businesses can optimize their supply chain operations, improve customer satisfaction, and minimize costs. When lead times are accurately estimated and efficiently managed, companies can avoid stockouts, reduce inventory carrying costs, and respond more effectively to market demands.
Importance of Lead Times in the Supply Chain
Lead times play a vital role in the smooth operation of the supply chain and have a significant impact on a business’s overall performance. Here are several reasons why lead times are important in the supply chain:
1. Customer Satisfaction: One of the most crucial aspects of any business is meeting customer expectations. Lead times greatly influence customer satisfaction, as they determine how quickly customers receive their orders. Shorter lead times allow for faster order processing, reduced waiting times, and timely product delivery, enhancing customer satisfaction and loyalty.
2. Inventory Management: Lead times impact inventory management strategies. Longer lead times often necessitate higher levels of safety stock to prevent stockouts. On the other hand, shorter lead times enable businesses to maintain lower inventory levels, reducing carrying costs and minimizing the risk of excess stock.
3. Production Planning: Accurate lead time estimation is essential for effective production planning. By understanding lead times, businesses can efficiently schedule production runs, allocate resources, and manage production capacity. This enables them to optimize production workflows and meet customer demand on time.
4. Supply Chain Efficiency: Efficient lead time management improves overall supply chain performance. It helps to identify bottlenecks, streamline processes, and minimize delays. By minimizing lead times at each stage of the supply chain, businesses can achieve greater operational efficiency, reduce costs, and maintain a competitive edge.
5. Flexibility and Responsiveness: Shorter lead times provide businesses with greater flexibility to adapt to sudden changes in customer demand or market conditions. With shorter lead times, it becomes easier to respond to fluctuations in demand, launch new products quickly, and adjust production schedules accordingly.
6. Reduced Risk: Longer lead times introduce higher risks of disruptions, such as supplier delays or transportation issues. By managing lead times effectively, businesses can mitigate these risks and build more resilient supply chains. This includes maintaining good relationships with suppliers, having backup suppliers, and proactively addressing potential bottlenecks.
7. Competitive Advantage: In today’s fast-paced business environment, gaining a competitive advantage is crucial. Shorter lead times allow businesses to differentiate themselves by providing faster and more reliable service to customers. This can attract new customers, retain existing ones, and create a positive brand perception.
Overall, lead times are a critical metric in supply chain management. By understanding and managing lead times effectively, businesses can improve customer satisfaction, reduce costs, optimize inventory management, and enhance their overall competitive position in the market.
Factors Affecting Lead Times in the Supply Chain
Lead times in the supply chain are influenced by a variety of factors that can significantly impact the speed and efficiency of product delivery. Understanding these factors is essential for businesses to effectively manage and optimize lead times. Here are some key factors that can affect lead times in the supply chain:
1. Supplier Lead Time: The lead time set by suppliers to deliver raw materials or components is a critical factor. Longer supplier lead times can extend the overall lead time in the supply chain, causing delays in production and delivery.
2. Production Time: The time required to transform raw materials into finished goods also affects lead times. Complex manufacturing processes, high product customization, or limited production capacity can lead to longer production lead times.
3. Transportation Time: The time taken for goods to be transported from one location to another is a significant factor in lead times. Factors such as distance, transport mode, traffic conditions, and customs clearance can impact transportation lead times.
4. Quality Control: Insufficient or delayed quality control measures can lead to longer lead times. Effective quality control processes should be in place to ensure that products meet the required standards before being shipped, preventing delays due to rework or rejection.
5. Warehousing and Inventory Management: Lead times can be affected by the efficiency of warehousing and inventory management practices. Poor inventory management, stockouts, or delays in receiving and dispatching goods can result in longer lead times.
6. Seasonality: Demand fluctuations due to seasonality can affect lead times. Increased demand during peak seasons can strain the supply chain, resulting in longer lead times. Adequate forecasting and planning can help businesses mitigate the impact of seasonal variations.
7. Supplier Reliability: The reliability and performance of suppliers play a significant role in lead times. Unreliable suppliers, frequent stockouts, or delays in deliveries can disrupt the supply chain and lead to longer lead times.
8. Infrastructure: Infrastructure capabilities, such as transportation networks, ports, and warehouses, can impact lead times. Inadequate infrastructure or congestion can cause delays and lengthen lead times.
9. Global Factors: International trade and geopolitical factors can influence lead times. Customs procedures, regulations, trade disputes, or natural disasters can all lead to delays in the supply chain and increase lead times.
10. Technology: The use of advanced technologies, such as automation, robotics, and real-time tracking systems, can significantly impact lead times by improving efficiency and visibility across the supply chain.
Understanding these factors and their impact on lead times allows businesses to identify areas for improvement, optimize processes, and proactively address any bottlenecks in the supply chain. By effectively managing these factors, businesses can reduce lead times, improve customer satisfaction, and increase their competitive advantage in the market.
Types of Lead Times
Lead times in the supply chain can be categorized into different types based on the specific phase or activity they represent. Each type of lead time provides valuable insights into different aspects of the supply chain. Here are the main types of lead times:
1. Procurement Lead Time: This refers to the time it takes to source and procure raw materials, components, or finished goods from suppliers. It includes activities such as supplier selection, order placement, and order processing. Procurement lead time can vary depending on factors such as supplier responsiveness, negotiation terms, and transportation arrangements.
2. Manufacturing Lead Time: Also known as production lead time, this type of lead time represents the time required to transform raw materials into finished goods. It encompasses activities such as production planning, scheduling, and actual manufacturing processes. Manufacturing lead time can be affected by factors such as the complexity of the production process, machine availability, and workforce efficiency.
3. Transportation Lead Time: This refers to the time taken for goods to be transported from one location to another. It includes activities such as arranging shipment, loading and unloading, and actual transit time. Transportation lead time can vary depending on the distance between locations, chosen mode of transportation, and any potential disruptions or delays in the transportation network.
4. Order Processing Lead Time: This represents the time involved in processing and fulfilling customer orders. It includes activities such as order entry, order verification, and order confirmation. Order processing lead time can be influenced by factors such as order complexity, order volume, and the efficiency of order management systems.
5. Delivery Lead Time: This type of lead time focuses on the time it takes for the product to be delivered to the customer’s location. It includes activities such as order dispatch, transit time, and final delivery. Delivery lead time can be affected by factors such as the geographical location of the customer, transportation mode, and any custom clearance requirements.
6. Total Lead Time: This represents the overall lead time from the order placement to the receipt of the finished goods by the customer. It encompasses all the different types of lead times mentioned above. Total lead time is a comprehensive measure that reflects the end-to-end duration of the entire supply chain process.
Understanding the different types of lead times helps businesses identify the specific areas where they can focus their efforts on reducing delays and improving efficiency. By analyzing each type of lead time and implementing strategies to optimize them, businesses can significantly enhance their supply chain performance, reduce lead times, and provide better service to their customers.
Benefits of Managing Lead Times in the Supply Chain
Efficiently managing lead times in the supply chain offers a wide range of benefits for businesses. By effectively controlling and optimizing lead times, companies can enhance their operational performance, improve customer satisfaction, and gain a competitive edge in the market. Here are the key benefits of managing lead times:
1. Improved Customer Satisfaction: Timely delivery of products or services is crucial for customer satisfaction. By managing lead times effectively, businesses can ensure that customer orders are fulfilled on time, leading to higher customer satisfaction levels and increased loyalty.
2. Reduced Carrying Costs: Longer lead times often result in higher inventory carrying costs. By managing lead times, businesses can minimize the need for excessive safety stock and reduce inventory levels, thereby reducing holding costs and improving cash flow.
3. Enhanced Operational Efficiency: Efficient lead time management helps optimize production and logistics processes. By minimizing delays and bottlenecks in the supply chain, businesses can achieve greater operational efficiency, streamline workflows, and reduce waste.
4. Increased Responsiveness: Shorter lead times enable businesses to respond quickly to changes in customer demand or market conditions. This agility allows for faster product launches, quick order fulfillment, and swift adjustments in production schedules, ultimately leading to a competitive advantage.
5. Better Planning and Forecasting: Accurate lead time estimation enables businesses to improve their planning and forecasting processes. By understanding lead times, companies can better align their production, procurement, and inventory management activities, resulting in improved supply chain visibility and reduced uncertainty.
6. Reduced Risk of Stockouts: Effective management of lead times helps businesses avoid stockouts, where products become unavailable due to insufficient inventory. By accurately estimating lead times and implementing proactive inventory management, companies can fulfill customer demand consistently, avoiding lost sales opportunities.
7. Optimized Supplier Relationships: Managing lead times involves building strong relationships with suppliers. By fostering effective communication and collaboration, businesses can improve supplier performance, shorten lead times, and ensure a reliable and consistent supply of materials or components.
8. Improved Cash Flow: Timely order fulfillment and reduced inventory levels resulting from effective lead time management can contribute to improved cash flow. By minimizing tied-up capital in excessive inventory and reducing carrying costs, businesses can allocate resources more efficiently and invest in growth opportunities.
9. Enhanced Competitive Advantage: Shorter lead times can differentiate businesses from competitors. By providing faster delivery and responsive service, companies can attract and retain customers, gaining a competitive edge in the marketplace.
10. Better Supply Chain Resilience: Efficient lead time management improves supply chain resilience. By anticipating and addressing potential disruptions, businesses can minimize the impact of unexpected events, such as supplier delays or transportation issues, thereby ensuring uninterrupted operations.
In summary, managing lead times in the supply chain yields numerous benefits, including improved customer satisfaction, reduced costs, enhanced operational efficiency, and increased competitiveness. By focusing on lead time optimization, businesses can optimize their supply chain performance and position themselves for long-term success.
Challenges in Managing Lead Times in the Supply Chain
Managing lead times in the supply chain can be a complex task due to various challenges and obstacles that businesses may encounter. Overcoming these challenges is essential to ensure smooth operations, meet customer expectations, and maintain a competitive edge. Here are some common challenges in managing lead times in the supply chain:
1. Supplier Reliability: Suppliers play a critical role in the supply chain, and their reliability can significantly impact lead times. Dealing with unreliable suppliers, frequent stockouts, or delays in deliveries can disrupt the supply chain and cause delays in the overall lead time.
2. Forecasting Accuracy: Accurate demand forecasting is crucial for effective lead time management. Inaccurate forecasts can lead to overstocking or stockouts, affecting lead times. Errors in demand projections, market volatility, or changing customer preferences can make forecasting challenging.
3. Inventory Planning: Balancing inventory levels with lead times is a constant challenge. Maintaining optimal inventory levels is essential to meet customer demand while avoiding excess inventory carrying costs. Poor inventory planning can result in stockouts or excessive stock, impacting lead times.
4. Transportation Issues: Delays in transportation, such as customs clearance, traffic congestion, or disruptions in logistics networks, can lead to extended lead times. Managing transportation logistics and mitigating potential delays is crucial for efficient lead time management.
5. Production Delays: Unforeseen production delays, such as machinery breakdowns, labor shortages, or quality control issues, can significantly impact lead times in manufacturing processes. Ensuring smooth production operations and addressing these issues promptly is key to managing lead times.
6. Complex Supply Chains: Global supply chains often involve multiple tiers of suppliers, increased lead times, and higher complexity. Coordinating activities, managing dependencies, and ensuring collaboration among different stakeholders can be challenging, impacting lead time management.
7. Seasonal Demand Variations: Seasonal demand fluctuations can put stress on the supply chain, leading to longer lead times. Managing peaks and valleys in demand, ensuring adequate resources, and optimizing production schedules are necessary to handle seasonal variations effectively.
8. Information Sharing and Visibility: Lack of real-time visibility and information sharing across the supply chain can hinder lead time management. Efficient communication, transparency, and the use of technology and systems that provide visibility are crucial for effective lead time management.
9. External Disruptions: Unforeseen events such as natural disasters, geopolitical conflicts, or global pandemics can significantly disrupt supply chains and cause delays in lead times. Developing contingency plans, diversifying suppliers, and implementing risk management strategies can help mitigate these disruptions.
10. Cost Considerations: Balancing lead time reduction efforts with cost considerations can be challenging. Investing in technologies, infrastructures, or resources to reduce lead times can impact the overall cost structure, requiring careful analysis and decision-making.
Overcoming these challenges requires a holistic approach and proactive management of the supply chain. Close collaboration with suppliers, accurate forecasting, efficient inventory planning, improved logistics management, and agile response to disruptions are key strategies to mitigate lead time challenges and ensure efficient supply chain operations.
Strategies for Efficiently Managing Lead Times in the Supply Chain
Efficiently managing lead times in the supply chain requires a proactive and strategic approach. By implementing effective strategies, businesses can optimize their operations, reduce delays, and improve overall customer satisfaction. Here are some key strategies for efficiently managing lead times:
1. Develop Strong Supplier Relationships: Building strong relationships with suppliers is essential for efficient lead time management. Clear communication, prompt feedback, and collaboration can help establish trust and improve supplier responsiveness, leading to shorter lead times.
2. Implement Demand Forecasting and Planning: Accurate demand forecasting is critical for efficient lead time management. Utilize historical data, market trends, and customer insights to forecast demand. Combine this with effective planning to align production, procurement, and inventory management activities with anticipated demand fluctuations.
3. Optimize Inventory Management: Implement inventory management techniques, such as just-in-time (JIT) or vendor-managed inventory (VMI), to reduce lead times. This involves maintaining appropriate inventory levels to meet demand while minimizing carrying costs and the risk of stockouts.
4. Streamline Production Processes: Improve production efficiency and reduce lead times by implementing Lean or Six Sigma methodologies. Identify and eliminate non-value-added activities, optimize workflows, and implement process improvements to achieve smoother and faster production operations.
5. Invest in Technology: Leverage technological advancements in supply chain management, such as warehouse management systems (WMS), transportation management systems (TMS), and real-time tracking solutions. These technologies provide better visibility, enhance communication, and enable more accurate coordination throughout the supply chain.
6. Optimize Transportation Management: Effectively manage transportation logistics to reduce lead times. Streamline processes, collaborate with logistics providers, and leverage optimization algorithms to select the most efficient transportation routes and modes. This ensures timely and cost-effective delivery of goods.
7. Implement Agile Supply Chain Strategies: Adopt agile supply chain practices to improve responsiveness and shorten lead times. This involves quickly adapting to changes in customer demand, having flexible production processes, and maintaining real-time visibility of inventory levels and market conditions.
8. Continuous Improvement and Performance Measurement: Regularly evaluate and analyze performance metrics related to lead times. Set specific targets, monitor progress, and identify areas for improvement. Implement continuous improvement initiatives, such as Kaizen or Six Sigma, to drive efficiency and reduce lead times.
9. Collaborate with Supply Chain Partners: Foster collaboration and coordination with supply chain partners, including suppliers, distributors, and logistics providers. Share information, align goals, and establish clear communication channels to improve overall supply chain efficiency and reduce lead times.
10. Implement Risk Management Strategies: Identify potential risks and develop contingency plans to mitigate their impact on lead times. Assess risks related to suppliers, transportation, natural disasters, and other external factors. Establish alternative sourcing options, invest in supply chain resiliency, and regularly update risk management strategies.
By implementing these strategies, businesses can effectively manage lead times in the supply chain, reduce delays, enhance operational efficiency, and ultimately improve customer satisfaction. Constant monitoring, evaluation, and adaptation are necessary to ensure ongoing success in lead time management.
Conclusion
Efficiently managing lead times in the supply chain is essential for businesses to thrive in today’s competitive marketplace. By understanding the importance of lead times, businesses can implement strategies to optimize their operations, reduce delays, and enhance customer satisfaction. With shorter lead times, companies can improve inventory management, streamline production processes, and respond quickly to changes in customer demand.
Factors such as supplier reliability, accurate demand forecasting, and transportation issues can pose challenges in managing lead times. However, by building strong supplier relationships, leveraging technology, and implementing agile supply chain practices, businesses can overcome these challenges and optimize their lead times.
The benefits of efficient lead time management are substantial. Businesses that manage lead times effectively experience improved customer satisfaction, reduced carrying costs, enhanced operational efficiency, and increased responsiveness to market demands. They are better positioned to withstand disruptions and gain a competitive advantage in the industry.
Continuous improvement and performance measurement are crucial in lead time management. By monitoring key metrics, setting targets, and implementing continuous improvement initiatives, businesses can continually refine their processes and further reduce lead times.
In conclusion, effectively managing lead times in the supply chain is a complex but critical task. By implementing the strategies outlined in this article and addressing the associated challenges, businesses can optimize their supply chain operations, improve customer satisfaction, and achieve long-term success in today’s dynamic business environment.