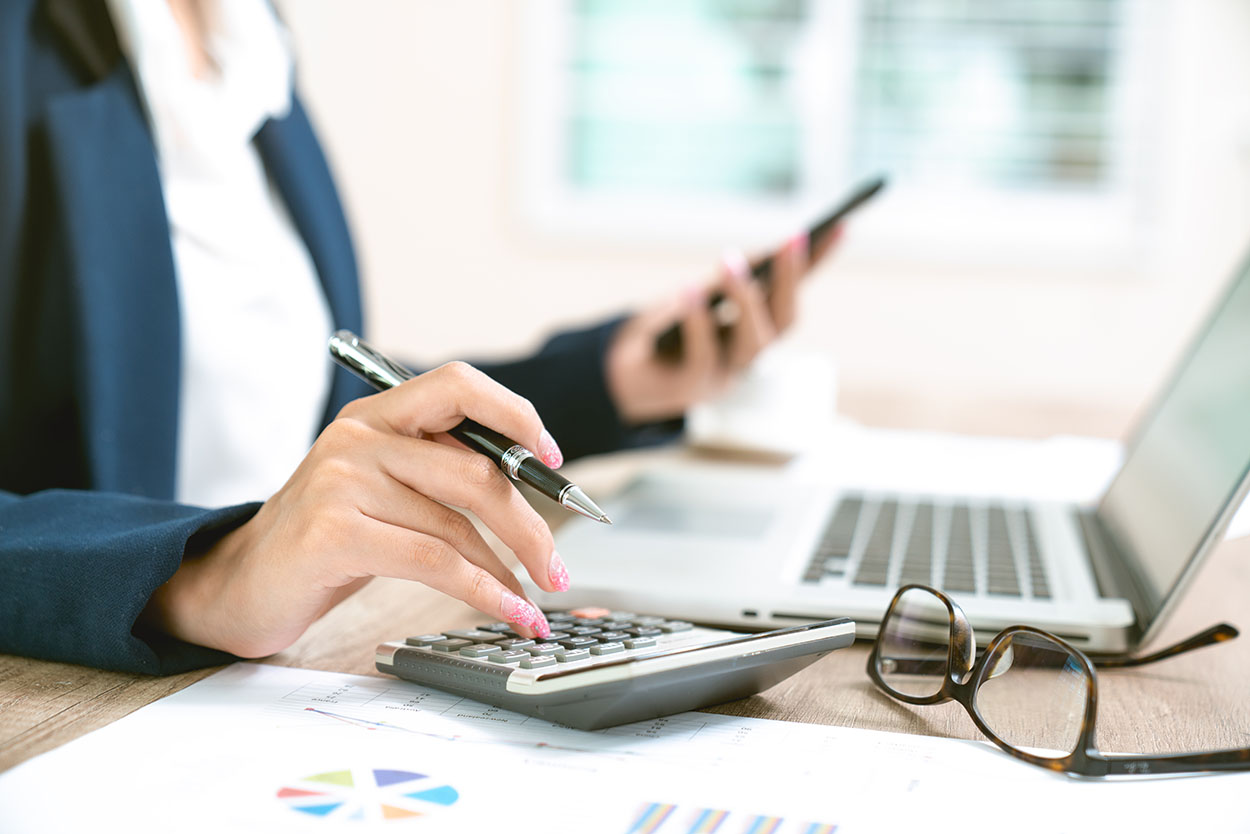
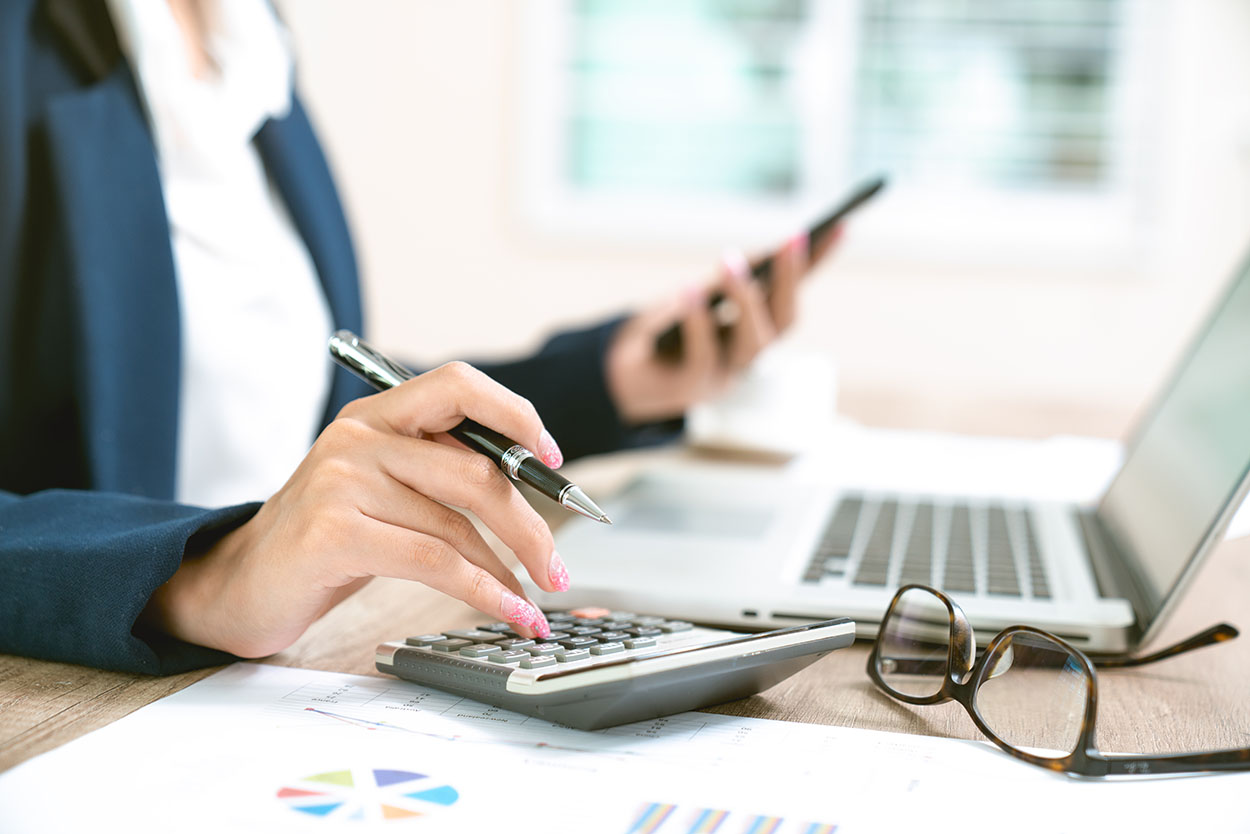
Finance
What Are Direct Materials In Accounting
Published: October 7, 2023
Learn about direct materials in accounting and their significance in finance. Gain a clear understanding of how these components impact financial statements and play a crucial role in cost analysis.
(Many of the links in this article redirect to a specific reviewed product. Your purchase of these products through affiliate links helps to generate commission for LiveWell, at no extra cost. Learn more)
Table of Contents
Definition of Direct Materials
In the field of accounting, direct materials are considered a crucial component in the production process of goods. These materials are directly incorporated into the final product and can be easily traced to it. Direct materials are typically the primary raw materials, components, or ingredients required to manufacture a product.
Direct materials play a significant role in determining the cost of production. They are tangible items that can be measured and evaluated in terms of quantity and value. These materials are essential for the creation of the end product and directly contribute to its overall quality and functionality.
The classification of materials as direct is determined by their significance and direct involvement in the manufacturing process. The usage of direct materials can vary across different industries. For example, in the construction industry, direct materials might include cement, steel, and lumber, while in the food industry, direct materials might refer to ingredients such as flour, sugar, and spices.
Direct materials are distinct from indirect materials, which are goods used in the production process but are not directly incorporated into the final product. Indirect materials, such as maintenance supplies or office supplies, do not have a direct impact on the quality or functionality of the end product but are necessary for the overall production process.
It is important to note that the classification of materials as direct or indirect can have significant implications for accounting and cost analysis. Direct materials are typically assigned to specific cost centers and can be easily allocated to individual products, allowing for accurate cost calculations and analysis of production efficiency.
Overall, direct materials are essential components that directly contribute to the creation and quality of a product. They play a pivotal role in accounting for production costs and enable businesses to accurately assess the cost of goods sold, track inventory, and make informed decisions regarding pricing and profitability.
Examples of Direct Materials
Direct materials encompass a wide range of items that are directly used in the manufacturing process of a product. Here are some common examples of direct materials:
- Raw Materials: Raw materials such as wood, steel, plastic, fabric, and glass are frequently used as direct materials in various industries. These materials are transformed and incorporated into the final product.
- Components: Components, such as electronic circuits, motors, gears, and fasteners, are considered direct materials in industries like electronics, automotive, and machinery manufacturing. These components are essential for the functioning of the final product.
- Chemicals: Chemicals play a vital role in industries like pharmaceuticals, cosmetics, and food processing. Active ingredients, solvents, additives, and preservatives are examples of direct materials used in these industries.
- Fuels and Energy: In industries that rely heavily on energy consumption, such as power generation or metal refining, fuels like coal, oil, and natural gas, as well as electricity, are considered direct materials.
- Ingredients: In the food and beverage industry, ingredients such as flour, sugar, spices, fruits, and vegetables are essential direct materials used in the production of various food products.
- Packaging Materials: Packaging materials, including boxes, bottles, labels, and wrappers, are often considered direct materials as they are necessary for the preservation and presentation of the final product.
These examples illustrate the diverse nature of direct materials and the specific role they play in different industries. The selection of direct materials is determined by the requirements of the product, its manufacturing process, and the desired quality standards.
Proper identification and management of direct materials are crucial for cost control and inventory management. By accurately tracking direct materials usage, businesses can optimize their production processes, monitor material waste, and make informed decisions about sourcing, pricing, and production efficiency.
It is important to note that the classification of materials as direct or indirect may vary depending on the industry and the specific circumstances of the production process. Therefore, businesses should carefully evaluate and categorize the materials they use based on their direct impact on the final product.
Importance of Direct Materials in Accounting
In the field of accounting, direct materials hold significant importance in terms of cost analysis, inventory management, and financial reporting. Here are some key reasons why direct materials are essential in accounting:
- Cost Determination: Direct materials are a fundamental component in calculating the cost of goods sold (COGS). By accurately tracking and assigning direct materials costs to specific products, businesses can determine the true cost of producing each unit. This information is crucial for pricing decisions, profitability analysis, and evaluating the efficiency of the production process.
- Inventory Valuation: Direct materials play a vital role in valuing inventory. The cost assigned to direct materials in inventory helps in determining the value of goods available for sale and assessing the financial position of the business. Proper inventory valuation is important for accurate financial reporting and determining the profitability of a company.
- Decision-Making: The use of direct materials provides crucial data for decision-making. By having accurate information about the costs associated with specific materials, businesses can make informed decisions about sourcing, supplier selection, and production efficiency. This helps in optimizing costs, improving profitability, and ensuring the availability of materials for the production process.
- Cost Control: Keeping track of direct materials usage and costs allows businesses to identify opportunities for cost control and waste reduction. By monitoring direct materials costs, businesses can implement strategies to minimize material waste, negotiate better prices with suppliers, and improve overall cost efficiency.
- Compliance and Reporting: Properly accounting for direct materials is essential for compliance with financial reporting standards and regulations. Accurate and transparent reporting of direct materials usage and costs ensures the integrity of financial statements and facilitates audits and regulatory compliance.
Overall, direct materials play a crucial role in accounting by providing valuable information about costs, inventory management, and decision-making. They enable businesses to accurately calculate production costs, measure profitability, control costs, and make informed decisions to enhance efficiency and drive profitability.
Direct Materials Costs Calculation
The calculation of direct materials costs is a critical aspect of cost accounting, allowing businesses to accurately determine the cost of producing goods. Here are the key components involved in calculating direct materials costs:
- Direct Materials Quantity: The first step is to quantify the amount of direct materials used in the production process. This can be measured in units, weight, volume, or any other appropriate unit of measurement. It is crucial to accurately measure and record the quantity of direct materials consumed.
- Direct Materials Price: The next step is to determine the price or cost per unit of the direct materials used. This can be obtained from purchase records or supplier invoices. It is essential to consider any discounts, rebates, or adjustments that might affect the cost per unit.
- Total Direct Materials Cost: The total direct materials cost can be calculated by multiplying the quantity of direct materials used by the cost per unit. This calculation provides the direct cost component of producing a particular quantity of goods.
- Indirect Costs Allocation: In some cases, there may be indirect costs associated with acquiring or handling direct materials, such as shipping or storage costs. These indirect costs should be allocated to the direct materials costs using an appropriate allocation method, such as a predetermined overhead rate.
- Subtracting Scrap or Waste: If there is any scrap or waste generated during the production process, the cost of these materials should be subtracted from the total direct materials cost. This adjustment ensures that only the usable direct materials are included in the calculation.
It is important to note that the accuracy of direct materials cost calculation depends on proper record-keeping, timely data entry, and a clear understanding of the specific production process and materials used.
Furthermore, businesses should regularly review and update the cost calculation methods to ensure they accurately reflect changes in material prices, supplier terms, quantity requirements, and any other factors that may impact direct materials costs.
Accurate calculation of direct materials costs provides businesses with crucial information for cost analysis, pricing decisions, inventory valuation, and overall financial management. It enables businesses to understand their production costs, ensure pricing competitiveness, and make informed decisions regarding sourcing, inventory control, and cost optimization.
Methods to Control Direct Materials Costs
Controlling direct materials costs is crucial for businesses to maintain profitability and competitiveness. Implementing effective cost control measures can help optimize resource allocation, reduce waste, and ensure efficient use of materials. Here are some methods to control direct materials costs:
- Supplier Negotiation: Engage in proactive supplier negotiations to secure the best prices and terms for direct materials. Regularly evaluate supplier performance, explore alternative suppliers, and negotiate volume discounts to reduce costs.
- Inventory Management: Optimize inventory levels to minimize holding costs and reduce the risk of spoilage or obsolescence. Implement just-in-time inventory systems to ensure a continuous flow of materials while reducing excess inventory.
- Quality Control: Ensure that direct materials meet quality standards to avoid costly defects or rework. Establish robust quality control procedures and work closely with suppliers to maintain consistent quality levels.
- Standardization: Standardize direct materials usage by identifying preferred materials, components, or suppliers. This promotes economies of scale, reduces production complexity, and enhances efficiency.
- Production Planning: Efficient production planning minimizes material waste and optimizes resource utilization. Implement lean manufacturing techniques such as just-in-time production, batch optimization, and production scheduling to reduce costs.
- Process Optimization: Continuously evaluate the production process to identify opportunities for improvement and cost reduction. Streamline workflows, eliminate bottlenecks, and optimize material utilization to minimize waste and improve efficiency.
- Employee Training: Train employees on proper handling and use of direct materials to minimize waste and ensure efficient consumption. Foster a culture of cost-consciousness and empower employees to contribute suggestions for cost-saving initiatives.
- Recycling and Waste Reduction: Implement recycling programs to extract value from waste materials. Reduce, reuse, and recycle wherever possible to minimize both environmental impact and materials costs.
- Technology Implementation: Leverage technology solutions to streamline material management processes, automate inventory tracking, and enhance supply chain visibility. This improves accuracy, reduces administrative costs, and enables better decision-making.
Implementing these methods requires a comprehensive understanding of the production process, close collaboration with suppliers, and a commitment to continuous improvement. Regular monitoring and evaluation of cost control measures are essential to ensure their effectiveness and identify areas for further enhancement.
By effectively controlling direct materials costs, businesses can enhance their bottom line, improve competitiveness, and maintain sustainable growth in the long run.
Direct Materials vs. Indirect Materials
In accounting, it is important to distinguish between direct materials and indirect materials, as they have different roles and implications in the production process. Here is a comparison between direct materials and indirect materials:
- Definition: Direct materials are tangible items that can be directly traced to the final product. They are incorporated into the product and have a direct impact on its quality or functionality. Indirect materials, on the other hand, are goods used in the production process but are not directly incorporated into the final product. They are necessary for the production process, but their absence or presence does not affect the quality or functionality of the final product.
- Traceability: Direct materials have a clear, identifiable link to the final product. They can be easily traced and assigned to specific cost centers or individual products for accurate cost calculation. Indirect materials, however, are not easily traceable to specific products or cost centers as they are used in a broader context.
- Cost Allocation: Direct materials are allocated to specific products or cost centers, allowing for precise cost tracking and analysis. Their costs are directly included in the cost of goods sold (COGS) and are considered a direct cost of production. Indirect materials, on the other hand, are allocated as manufacturing overhead or indirect costs and are typically included in the calculation of the predetermined overhead rate.
- Impact on Product: Direct materials directly contribute to the quality, functionality, and characteristics of the final product. They are key determinants of the product’s performance and customer satisfaction. Indirect materials, on the other hand, do not have a direct impact on the product itself but are necessary for the production process to occur efficiently.
- Examples: Examples of direct materials include raw materials, components, ingredients, and packaging materials that are directly transformed into the final product. Examples of indirect materials include maintenance supplies, tools, cleaning materials, and office supplies that support the production process but are not incorporated into the final product.
Understanding the distinction between direct materials and indirect materials is essential for accurate cost analysis, inventory valuation, and financial reporting. Proper classification and allocation of these materials are crucial for determining the cost of goods sold, tracking inventory, setting product prices, and evaluating production efficiency.
Furthermore, direct materials and indirect materials require different management strategies. Direct materials require careful sourcing, quality control, and efficient utilization to minimize costs and maintain product quality. Indirect materials, on the other hand, require effective procurement practices and inventory management to ensure their availability without unnecessary excess.
Overall, differentiating between direct materials and indirect materials provides valuable insights into the production process and enables businesses to make informed decisions regarding cost control, inventory management, and financial reporting.
Conclusion
Direct materials play a vital role in accounting and the production process of goods. They are the primary raw materials, components, or ingredients that are directly incorporated into the final product. Recognizing and properly accounting for direct materials is crucial for cost analysis, inventory management, and financial reporting.
In this article, we have discussed the definition of direct materials and provided examples of commonly used direct materials in various industries. We have also highlighted the importance of direct materials in accounting, including their role in cost determination, inventory valuation, and decision-making.
Additionally, we have explored the methods to control direct materials costs, such as supplier negotiation, inventory management, process optimization, and employee training. Implementing these methods allows businesses to optimize resource allocation, reduce waste, and ensure efficient use of direct materials.
Furthermore, we have compared direct materials with indirect materials, emphasizing their differences in definition, traceability, cost allocation, and impact on the final product. Understanding the distinction between direct and indirect materials is essential for accurate cost analysis and financial reporting.
In conclusion, a clear understanding of direct materials and their significance in accounting enables businesses to effectively manage costs, track inventory, and make informed decisions to enhance profitability. By implementing proper cost control measures and optimizing the utilization of direct materials, businesses can strengthen their financial position, improve operational efficiency, and maintain a competitive edge in the market.