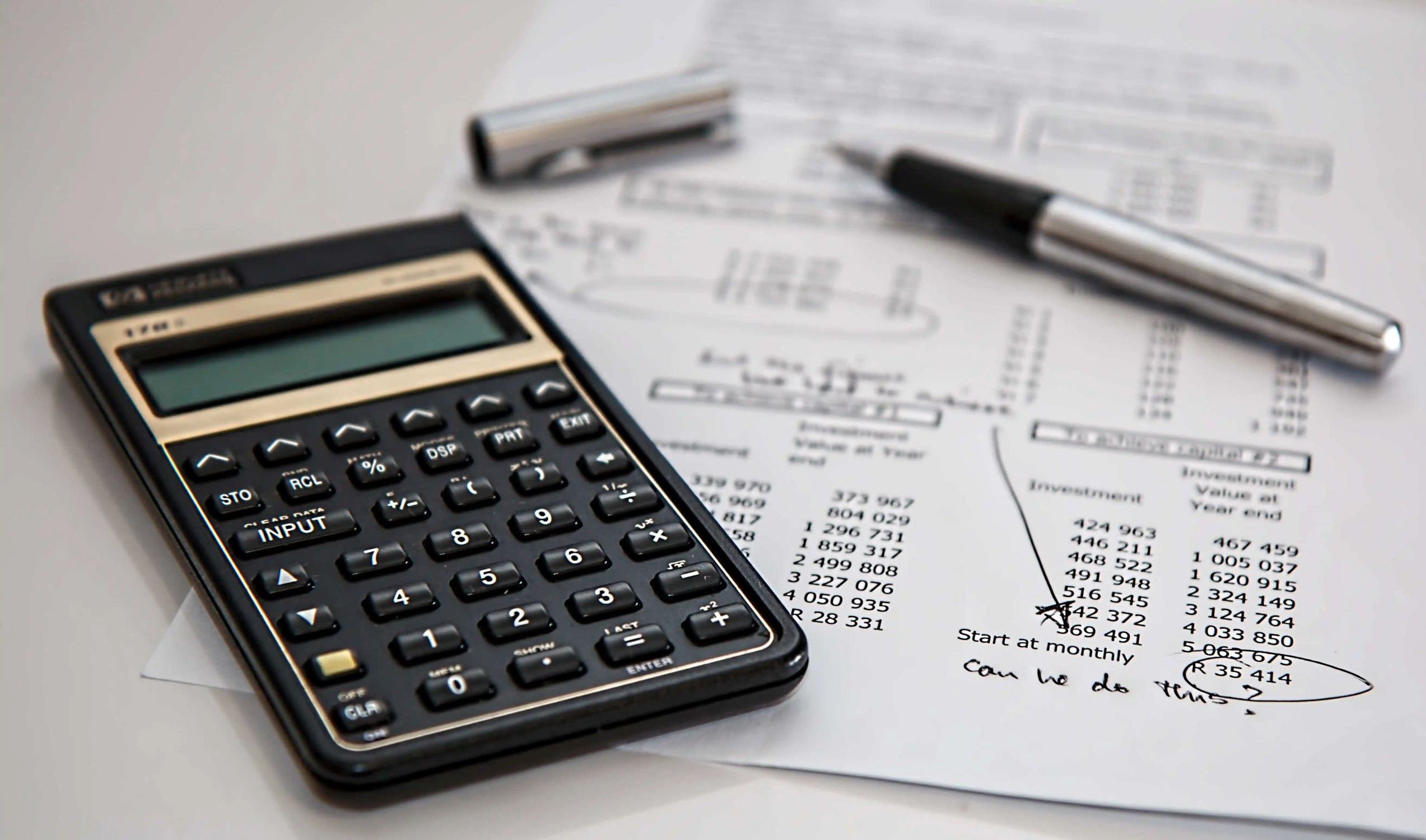
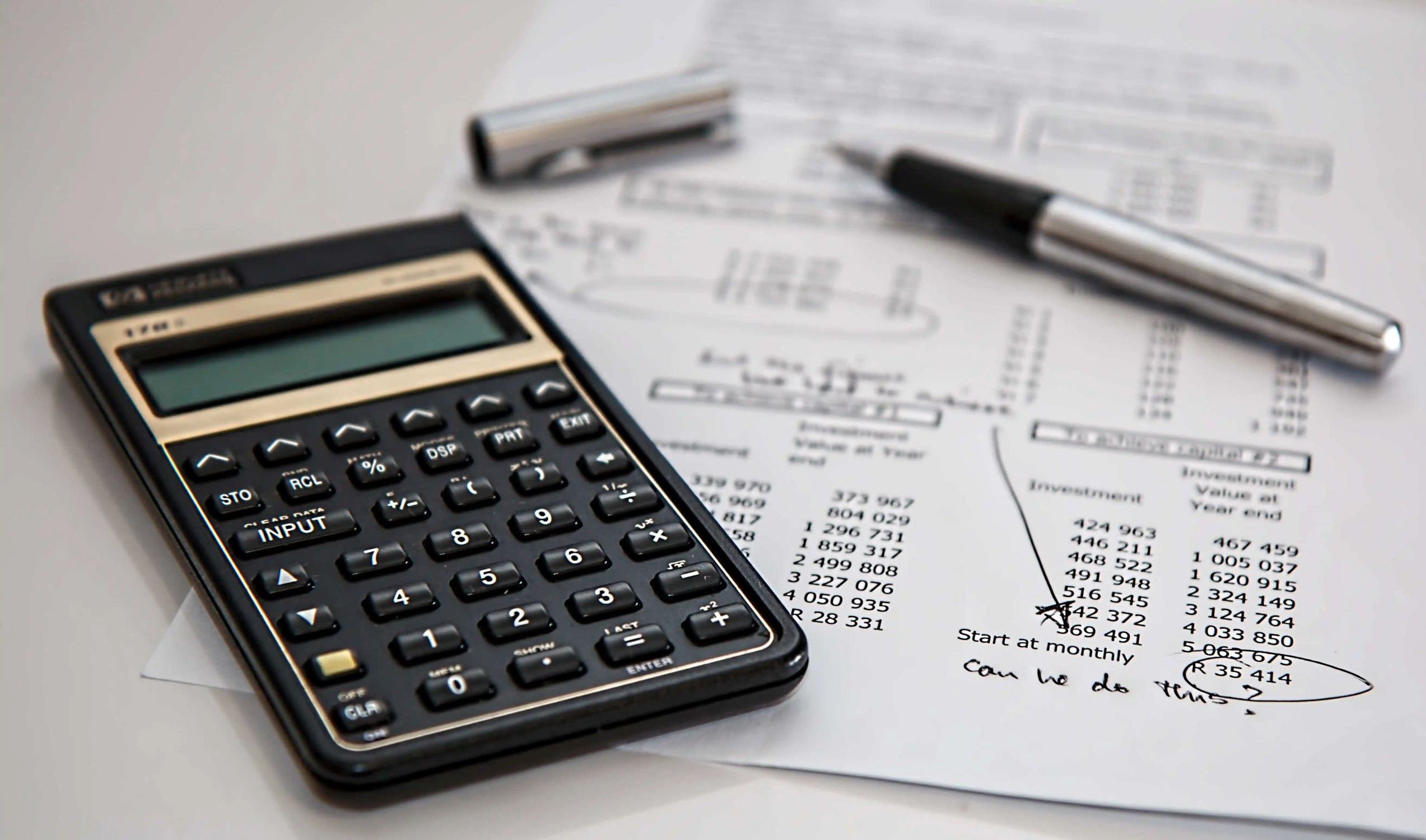
Finance
What Is A Direct Cost In Accounting
Published: October 10, 2023
Learn what a direct cost is in accounting and how it relates to finance. Gain insights into managing expenses and optimizing financial performance.
(Many of the links in this article redirect to a specific reviewed product. Your purchase of these products through affiliate links helps to generate commission for LiveWell, at no extra cost. Learn more)
Table of Contents
Introduction
In the world of accounting, understanding and effectively managing costs is essential for the success of any business. Among the various types of costs that exist, direct costs play a crucial role in financial analysis and decision-making processes.
Direct costs, also known as variable costs, are expenses that can be directly attributed to a specific product, project, or service. They are incurred as a direct result of the production process or the fulfillment of a specific customer order. Unlike indirect costs, which cannot be specifically linked to a particular activity, direct costs are traceable and can be allocated directly to the cost object.
Whether a business is involved in manufacturing, construction, or service-based industries, understanding direct costs is essential for accurate financial reporting and effective cost control. In this article, we will delve into the concept of direct costs, explore examples of direct costs, highlight the difference between direct and indirect costs, discuss the importance of tracking direct costs, and provide an overview of methods used to allocate direct costs.
By gaining a comprehensive understanding of direct costs, businesses can make more informed decisions, optimize their cost structures, and ultimately improve profitability.
Definition of Direct Cost
A direct cost is an expense that can be specifically and directly identified with a particular product, project, or service. It is a cost that is incurred due to the direct production or delivery of a specific output. Direct costs are often considered variable costs, as they tend to fluctuate with the level of production or sales.
Direct costs are usually incurred in the following areas:
- Direct Materials: These are the raw materials and components that are used in the production process. For example, in a furniture manufacturing company, the cost of wood, fabric, screws, and other materials directly used in producing a chair would be considered direct costs.
- Direct Labor: This refers to the wages and salaries paid to employees who are directly involved in the production process or providing a specific service. For example, the salary of a machine operator or the wage of a construction worker assigned to a particular project would be considered a direct cost.
- Direct Expenses: These are costs that directly relate to a specific product, project, or service and are not classified as direct materials or direct labor. Examples include fuel costs for a delivery truck, packaging materials, or a license fee for a software used exclusively for a particular project.
It is important to note that a cost may be classified as direct in one context and indirect in another. For example, the cost of a supervisor’s salary may be considered indirect if it cannot be directly attributed to a specific product or project, but it may be considered direct if the supervisor’s time is dedicated solely to overseeing a particular project.
Understanding the concept of direct costs is crucial for accurate cost allocation, budgeting, pricing decisions, and profitability analysis. By accurately identifying and tracking direct costs, businesses can have a better understanding of the true costs associated with each product, project, or service and make more informed financial decisions.
Examples of Direct Costs
Direct costs can vary depending on the nature of the business and the specific cost objects involved. Here are some common examples of direct costs:
- Raw Materials: In a manufacturing business, the cost of raw materials directly used in the production process is a prime example of a direct cost. For instance, in the automobile industry, the cost of steel, plastic, and other materials used to build a vehicle is a direct cost.
- Labor Costs: Direct labor costs include the wages and salaries of employees directly involved in producing goods or providing services. For example, in a software development company, the salaries of software developers and testers directly working on a specific project are direct costs.
- Equipment: The cost of machinery, tools, and equipment used in the production process is considered a direct cost. This includes items such as manufacturing machines, assembly line equipment, or specialized tools used to produce a specific product or service.
- Commissions: If a company pays sales commissions based on the sales revenue generated by a particular product or service, those commissions are considered direct costs. This applies to industries such as real estate, insurance, and retail.
- Direct Utilities: Utilities directly associated with a specific cost object, such as electricity consumed by manufacturing equipment or water used in a specific production process, are direct costs.
It is important to note that these examples are not exhaustive, and direct costs can vary based on the nature of the business. The key characteristic of a direct cost is that it can be directly tied to a specific cost object, whether it’s a product, service, or project.
By identifying and tracking these direct costs accurately, businesses can gain insight into the true costs associated with their offerings, allowing for better pricing decisions, cost control, and profitability analysis.
Difference Between Direct and Indirect Costs
In accounting, understanding the distinction between direct and indirect costs is crucial for accurate cost allocation and financial analysis. While direct costs are expenses that can be directly traced to a specific cost object, indirect costs are expenses that cannot be easily attributed to a specific product, project, or service. Here are some key differences between direct and indirect costs:
Traceability: Direct costs are traceable and can be directly linked to a cost object. For example, the cost of raw materials or the wages of employees directly involved in production. In contrast, indirect costs are not easily traceable or allocated to a specific cost object. For example, rent, utilities, or general administrative expenses.
Relativity: Direct costs are usually related to specific units of production or service. They tend to vary proportionally with the level of activity or output. In contrast, indirect costs are often incurred regardless of the level of production or sales. They are typically fixed or semi-fixed in nature, such as annual salaries or maintenance costs.
Allocation: Direct costs can be easily allocated to a specific cost object, making it straightforward to determine the total cost associated with a particular product, project, or service. Indirect costs, on the other hand, require an allocation process using appropriate allocation methods, such as activity-based costing or the use of cost drivers. This is because indirect costs are shared among multiple cost objects or activities.
Visibility: Direct costs are usually recognized and accounted for separately from indirect costs. They are readily identifiable in financial statements and reports, providing transparency on the costs directly incurred for a particular cost object. Indirect costs, while essential for management decision-making, may be aggregated or combined in reports, making them less visible individually.
It’s important to note that the distinction between direct and indirect costs can sometimes be subjective and depend on the specific context or industry. Costs that are considered indirect in one situation might be direct in another. Therefore, it’s crucial for businesses to carefully analyze and classify costs based on their traceability, relativeness, allocation requirements, and visibility to ensure accurate cost reporting and decision-making.
Importance of Tracking Direct Costs
Tracking direct costs is crucial for businesses as it provides valuable insights into the true costs associated with their products, projects, or services. Here are some key reasons why tracking direct costs is important:
Accurate Costing: By tracking direct costs, businesses can accurately determine the total cost of producing a specific product or delivering a service. This information is essential for setting competitive prices, evaluating profitability, and making informed pricing decisions. Without accurate cost allocation, businesses risk underpricing their offerings, leading to reduced profitability, or overpricing, which can result in lost sales.
Cost Control: Tracking direct costs allows businesses to identify areas where costs can be controlled and optimized. By monitoring the direct costs associated with each component, businesses can identify inefficiencies, reduce wastage of resources, and implement cost-saving measures. For example, tracking direct material costs can help identify opportunities to negotiate better pricing with suppliers or explore alternative sourcing options.
Profitability Analysis: Understanding direct costs is essential for evaluating the profitability of different products, projects, or services. By comparing direct costs against revenue generated, businesses can determine which offerings are more profitable and make informed decisions about resource allocation and investment. This analysis can also help identify areas where costs can be reduced or revenue can be increased to improve overall profitability.
Budgeting and Planning: Accurately tracking direct costs enables businesses to develop more realistic budgets and effectively plan for future projects and initiatives. Direct costs provide a clear picture of the resources and expenses needed for specific activities, allowing businesses to allocate funds appropriately, manage cash flow, and ensure that projects or operations are financially viable.
Financial Reporting and Transparency: Tracking direct costs ensures the accuracy and transparency of financial statements and reports. It allows businesses to present a comprehensive breakdown of the costs incurred for specific products, projects, or services, giving stakeholders a clear understanding of the financial performance of different aspects of the business. This transparency can enhance trust and credibility with investors, lenders, and other stakeholders.
In summary, tracking direct costs is vital for accurate costing, cost control, profitability analysis, budgeting, and financial reporting. It empowers businesses to make informed decisions, optimize resource allocation, and ensure the overall financial health and success of the organization.
Methods of Allocating Direct Costs
Allocating direct costs involves assigning or distributing these expenses to specific cost objects, such as products, projects, or services. This process is important for accurately determining the total cost associated with each cost object. Here are some common methods used to allocate direct costs:
- Direct Allocation: This method involves directly assigning or allocating the direct cost to a specific cost object. For example, if a manufacturing company produces three different products, the cost of direct materials and direct labor can be allocated based on the usage or time spent on each product. This method is simple and straightforward when there is a clear cause-and-effect relationship between the direct cost and the cost object.
- Step-Down Allocation: Step-down allocation, also known as the sequential allocation method, is used when there are shared resources that need to be allocated to multiple cost objects. In this method, indirect costs are allocated to intermediate cost centers based on a specific allocation basis, and then those costs are further allocated to final cost objects. This method ensures a more accurate allocation of indirect costs and takes into account the hierarchy of cost centers.
- Activity-Based Costing (ABC): ABC is a more sophisticated method of allocating direct costs that considers the activities involved in producing a product or delivering a service. This method identifies various activities and assigns costs to them based on the resources consumed by each activity. The costs are then allocated to the cost objects based on the level of activity required. ABC provides a more precise allocation of costs by considering the specific activities that drive costs within an organization.
- Cost Drivers: Cost drivers are factors that determine the level of direct costs incurred for a particular cost object. Identifying and measuring cost drivers is essential for accurate cost allocation. For example, in a manufacturing company, machine hours or labor hours can be used as cost drivers to allocate direct costs to different products. By identifying the key cost drivers, businesses can allocate direct costs more accurately based on the specific factors that influence those costs.
- Weighted Average Allocation: This method involves allocating direct costs based on weighted averages. For example, if a company has multiple projects, the direct costs can be allocated based on the percentage of resources or time devoted to each project. This method is useful when there are no clear cause-and-effect relationships between the direct costs and the cost objects, or when it is impractical to directly allocate costs.
The choice of allocation method depends on the nature of the business, the complexity of cost allocation, and the desired level of accuracy. It is important for businesses to carefully select the appropriate method to ensure that direct costs are allocated in a fair and meaningful manner, leading to more accurate cost reporting and decision-making.
Conclusion
The concept of direct costs plays a vital role in financial analysis and decision-making for businesses. Direct costs are expenses that can be directly attributed to a specific product, project, or service, and they provide valuable insight into the true costs associated with these cost objects. By accurately tracking and allocating direct costs, businesses can make more informed financial decisions, control costs, evaluate profitability, and enhance overall financial performance.
In this article, we discussed the definition of direct costs and explored examples of direct costs, such as raw materials, labor costs, and equipment expenses. We also highlighted the difference between direct and indirect costs, emphasizing the traceability, relativity, allocation, and visibility of these cost categories.
Furthermore, we emphasized the importance of tracking direct costs for accurate costing, cost control, profitability analysis, budgeting, and financial reporting. By understanding the true costs associated with their products, projects, or services, businesses can optimize pricing strategies, identify cost-saving opportunities, and effectively plan for future initiatives.
Lastly, we outlined various methods used to allocate direct costs, including direct allocation, step-down allocation, activity-based costing, and weighted average allocation. Each method offers a different level of accuracy and complexity in cost allocation, and businesses need to choose the most appropriate method based on their specific circumstances.
In conclusion, by recognizing the significance of direct costs and implementing effective cost tracking and allocation methods, businesses can gain a comprehensive understanding of their cost structures, make informed financial decisions, and ultimately achieve improved profitability and success.