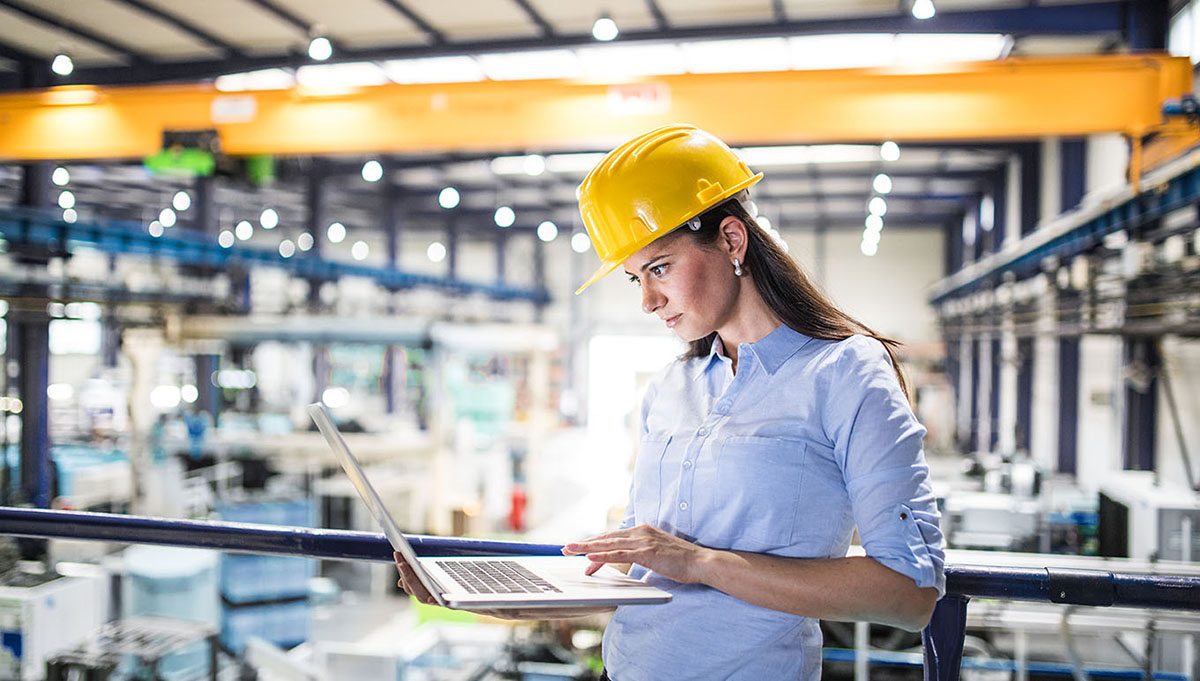
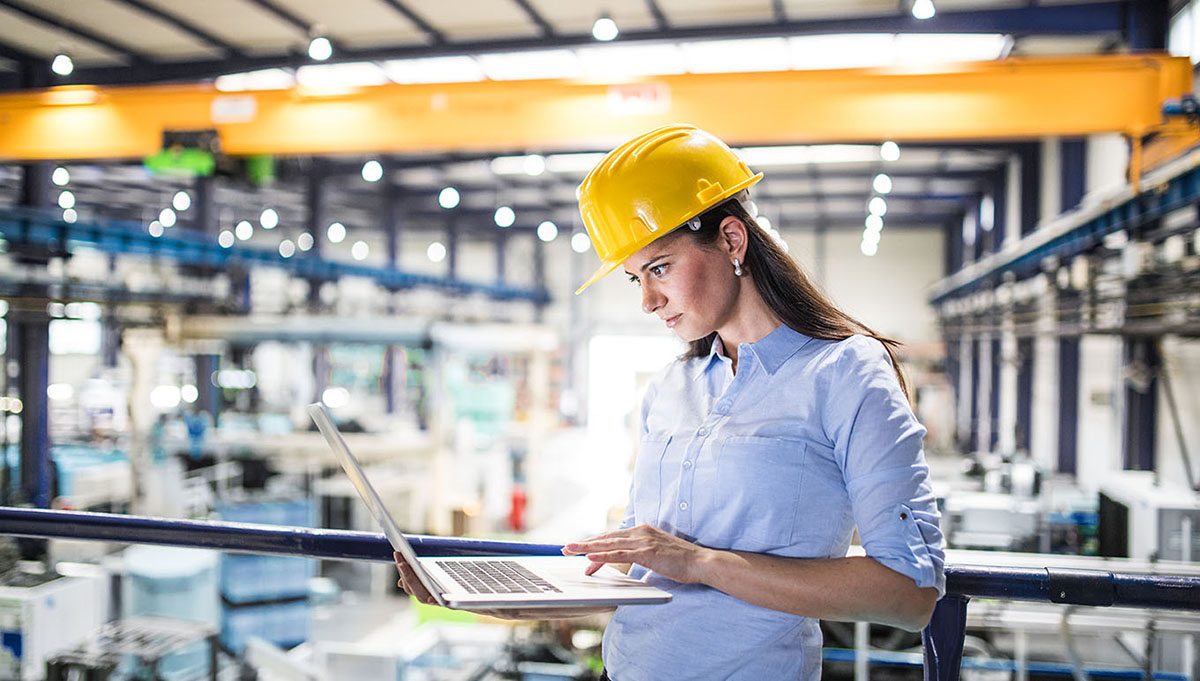
Finance
What Is MRP In Supply Chain?
Published: October 19, 2023
Learn how MRP (Material Requirement Planning) plays a crucial role in the finance aspect of the supply chain, optimizing inventory control and cost management.
(Many of the links in this article redirect to a specific reviewed product. Your purchase of these products through affiliate links helps to generate commission for LiveWell, at no extra cost. Learn more)
Table of Contents
Introduction
In today’s fast-paced and ever-evolving business landscape, efficient supply chain management is crucial for companies to stay competitive and meet customer demands. One key element of effective supply chain management is Material Requirements Planning (MRP). MRP is a systematic approach that helps businesses plan and control the procurement and production of materials needed to meet customer demand. By providing accurate inventory data, MRP enables organizations to optimize their supply chain operations, minimize costs, and streamline production processes.
At its core, MRP is a methodical way of determining what materials are needed, how much is needed, and when it is needed, aligning these requirements with production schedules and inventory levels. By accurately forecasting demand and managing inventory levels, companies can avoid stockouts, minimize excess inventory, and improve overall customer satisfaction.
Implementing an MRP system can bring numerous benefits to businesses of all sizes and across industries. By automating and optimizing the planning and synchronization of resources, MRP helps companies reduce lead times, lower production costs, and enhance operational efficiency. However, successfully implementing and managing an MRP system requires careful planning, attention to detail, and a thorough understanding of the components and processes involved.
In this article, we will delve deeper into the world of MRP in the supply chain. We will explore the definition of MRP, its importance in supply chain management, the components of an MRP system, and the planning process involved. Additionally, we will discuss the benefits of implementing MRP in the supply chain, the challenges companies may face, and best practices for successful implementation. By the end, you will have a comprehensive understanding of MRP and its role in optimizing supply chain operations.
Definition of MRP
Material Requirements Planning (MRP) is a computer-based inventory management system that aids in the planning and control of the production and procurement of materials. It is a methodical approach that calculates the quantity and timing of materials needed for production to meet customer demand. MRP is designed to ensure that the right quantity of materials is available at the right time while minimizing inventory carrying costs.
The primary objective of MRP is to strike a balance between avoiding stockouts and minimizing excess inventory. By analyzing demand forecasts, current inventory levels, and lead times, MRP generates a detailed production schedule and a list of materials to be purchased or produced. It takes into account factors such as order quantities, safety stock levels, and lead times to determine optimal inventory levels and production quantities.
An essential feature of MRP is the bill of materials (BOM). The BOM is a comprehensive list of components or raw materials required to manufacture a product. It specifies the quantity of each item and the relationship between them, allowing MRP to understand the dependencies and calculate the necessary material requirements for each product.
The heart of an MRP system is the logic that drives the calculations and generates the plans. This logic takes into account various factors such as lead times, lot sizes, minimum order quantities, and safety stock levels. By considering these factors, MRP aims to optimize production and purchasing decisions, ensuring that production runs smoothly and materials are available as needed.
MRP systems often integrate with other business systems such as Enterprise Resource Planning (ERP) and Manufacturing Execution Systems (MES) to provide a seamless flow of information and enable accurate decision-making across different departments. This integration enhances visibility, coordination, and collaboration within the organization, leading to improved supply chain efficiency.
In summary, MRP is a computer-based inventory management system that uses demand forecasts, current inventory levels, and other factors to calculate the quantity and timing of materials needed for production. It aims to optimize inventory levels, production schedules, and procurement planning, ensuring that the right materials are available at the right time to meet customer demand. MRP is a vital tool for businesses looking to streamline their supply chain operations and improve overall efficiency.
Importance of MRP in the Supply Chain
Material Requirements Planning (MRP) plays a crucial role in the efficient management of the supply chain. It provides businesses with several key benefits that help optimize operations and drive overall success. Let’s explore the importance of MRP in the supply chain:
- Improved Inventory Management: MRP enables businesses to maintain optimal inventory levels by accurately determining the quantity and timing of materials needed for production. By avoiding stockouts and minimizing excess inventory, companies can reduce carrying costs and improve cash flow.
- Enhanced Production Planning: With MRP, businesses can create detailed production schedules based on demand forecasts and material availability. This ensures efficient utilization of resources and minimizes idle time, leading to increased productivity and shorter lead times.
- Minimized Lead Times: MRP helps companies reduce lead times by synchronizing production and procurement activities. It considers factors like supplier lead times and production cycle times to ensure the timely availability of materials, avoiding delays and ensuring smooth operations.
- Effective Demand Planning: MRP relies on demand forecasts to calculate material requirements. By analyzing historical data and market trends, companies can accurately predict demand, allowing them to adjust production schedules and procurement plans accordingly. This enables organizations to meet customer demands more efficiently and avoid stockouts or overproduction.
- Optimized Resource Utilization: Through MRP, businesses can identify and allocate resources effectively. By aligning production schedules, materials, and workforce, companies can optimize resource utilization and minimize waste. This helps in cost reduction and improved operational efficiency.
Implementing MRP in the supply chain brings about a significant impact on organizations, giving them a competitive edge in the market. By streamlining inventory management, production planning, and procurement processes, companies can achieve improved customer satisfaction, reduced costs, enhanced operational efficiency, and increased profitability.
Furthermore, MRP provides real-time visibility into inventory levels, production progress, and material requirements. This enables better decision-making, proactive problem-solving, and effective resource allocation. With accurate and timely information, companies can respond swiftly to changing market conditions and customer demands, gaining a competitive advantage.
In summary, MRP is vital in the supply chain as it allows businesses to optimize inventory levels, enhance production planning, minimize lead times, streamline operations, and meet customer demands efficiently. It empowers companies to make data-driven decisions, improve resource utilization, and ultimately drive success in today’s dynamic business environment.
Components of MRP System
Material Requirements Planning (MRP) systems consist of various components that work together to ensure effective inventory management and production planning. These components include:
- Master Production Schedule (MPS): The MPS is a central component of the MRP system. It specifies what products will be produced, in what quantities, and when. The MPS serves as a roadmap for production activities and helps determine the material requirements for each product.
- Bill of Materials (BOM): The BOM is a detailed breakdown of the components, sub-assemblies, and raw materials required to build a product. It lists the quantity of each item and the hierarchical relationship between them. The BOM is essential for calculating the material requirements and ensuring that all necessary components are available.
- Inventory Status: The inventory status component of the MRP system provides real-time information about the current stock levels and availability of materials. It includes data on both raw materials and finished goods, allowing businesses to make informed decisions regarding replenishment, production, and customer orders.
- Material Requirements Planning Logic: The logic behind the MRP system calculates the material requirements based on the MPS, BOM, and inventory status. It considers factors such as lead times, order quantities, safety stock levels, and minimum order quantities to determine the optimal quantity and timing of materials needed for production.
- Purchase Order Processing: This component handles the creation, processing, and tracking of purchase orders for the procurement of materials. It ensures that the necessary materials are ordered from suppliers in a timely manner to meet production requirements.
- Capacity Planning: Capacity planning is a critical component of the MRP system, as it involves assessing the available production capacity and aligning it with the production requirements specified in the MPS. It helps identify any potential bottlenecks or capacity constraints and enables businesses to optimize resource allocation.
These components work together to create a comprehensive MRP system that efficiently manages the flow of materials, synchronizes production activities, and ensures effective utilization of resources. By integrating these components, businesses can achieve better inventory control, shorter lead times, improved production planning, and ultimately, a more streamlined supply chain.
Modern MRP systems often incorporate additional features such as advanced analytics, demand forecasting modules, and integration with other business systems like Enterprise Resource Planning (ERP) and Manufacturing Execution Systems (MES). These enhancements further enhance the capabilities and effectiveness of the MRP system, enabling businesses to make data-driven decisions and adapt to dynamic market conditions.
In summary, the components of an MRP system include the Master Production Schedule, Bill of Materials, Inventory Status, Material Requirements Planning Logic, Purchase Order Processing, and Capacity Planning. These components work together to effectively manage inventory, plan production, and ensure the availability of materials in the supply chain. By leveraging these components, businesses can optimize operations, reduce costs, and improve customer satisfaction.
MRP Planning Process
The Material Requirements Planning (MRP) planning process is a structured approach that enables businesses to determine the quantity and timing of materials needed for production. It involves several steps that work together to optimize inventory levels, production schedules, and procurement planning. Let’s take a closer look at the MRP planning process:
- 1. Master Production Schedule (MPS) Creation: The first step in the MRP planning process is the creation of the MPS. The MPS outlines the production schedule for finished goods, specifying what products will be produced, the quantities required, and the desired delivery dates. The MPS serves as a foundation for subsequent planning activities.
- 2. Bill of Materials (BOM) Analysis: Once the MPS is established, the next step is to analyze the BOM. The BOM provides a detailed breakdown of the components, sub-assemblies, and raw materials required for each finished product. By examining the BOM, the MRP system identifies the material requirements for each product based on the MPS.
- 3. Inventory Evaluation: The MRP system then evaluates the current inventory levels of each component and finished goods. It takes into account factors such as stock on hand, on order, and quantities committed to customer orders. By considering the inventory status, the MRP system determines whether there are sufficient materials available or if additional procurement is needed.
- 4. Net Requirements Calculation: Using the information gathered from the MPS, BOM analysis, and inventory evaluation, the MRP system calculates the net requirements for each component. Net requirements represent the difference between the quantity needed and the quantity already available or on order. This calculation helps determine the specific quantities of materials that need to be procured to meet production demands.
- 5. Purchase Order Generation: Based on the net requirements, the MRP system generates purchase orders for the necessary materials. These purchase orders are sent to suppliers to initiate the procurement process. The purchase order includes details such as the quantity, desired delivery date, and supplier information.
- 6. Production Planning: Simultaneously with the purchase order generation, the MRP system creates a detailed production plan. The production plan outlines the sequence, timing, and quantities of production activities for each finished product. It takes into account the availability of materials, production capacity, and other constraints to ensure an efficient production process.
- 7. Monitoring and Adjusting: The MRP system continuously monitors the progress of production activities and the status of material procurement. It compares the actual inventory levels and production progress against the planned quantities. Any deviations or changes in demand are analyzed, and the MRP system adjusts the plans accordingly to maintain optimal inventory levels and meet customer demands.
By following the MRP planning process, businesses can effectively manage their inventory, synchronize production activities, and ensure the availability of materials when needed. This allows for efficient production planning, reduced lead times, and improved customer satisfaction. Continuous monitoring and adjustment ensure that the plans remain dynamic and responsive to changes in demand and supply conditions.
In summary, the MRP planning process involves creating the Master Production Schedule, analyzing the Bill of Materials, evaluating inventory levels, calculating net requirements, generating purchase orders, planning production activities, and monitoring and adjusting the plans. This systematic approach helps businesses optimize their supply chain operations and effectively manage their materials and production processes.
Benefits of Implementing MRP in the Supply Chain
Implementing Material Requirements Planning (MRP) in the supply chain brings several significant benefits to businesses. By optimizing inventory management, production planning, and procurement processes, MRP helps companies improve operational efficiency, reduce costs, and enhance customer satisfaction. Let’s explore the key benefits of implementing MRP:
- Improved Inventory Control: MRP enables businesses to maintain optimal inventory levels by accurately forecasting material requirements. By ensuring the right amount of materials is available at the right time, companies can minimize excess inventory, reduce carrying costs, and avoid stockouts.
- Enhanced Production Planning: With MRP, businesses can create detailed production schedules based on the demand forecast and material availability. This improves production efficiency, reduces idle time, and shortens lead times. By optimizing production planning, companies can meet customer demands more effectively and allocate resources efficiently.
- Shortened Lead Times: MRP synchronizes production and procurement activities, enabling companies to reduce lead times. By accurately determining material requirements, considering supplier lead times, and aligning production schedules, businesses can ensure timely availability of materials, prevent production delays, and enhance customer satisfaction.
- Effective Resource Allocation: MRP allows businesses to optimize resource utilization by aligning production schedules, materials, and workforce. This results in improved efficiency, lower costs, and minimized waste. By allocating resources effectively and aligning them with production requirements, companies can maximize output without incurring unnecessary expenses.
- Better Decision-Making: MRP provides real-time visibility into inventory levels, production progress, and material requirements. This empowers businesses to make informed decisions based on accurate and timely information. With enhanced visibility, companies can respond quickly to changes in customer demands, supplier schedules, and market conditions, improving their agility and competitiveness.
- Improved Collaboration: MRP systems often integrate with other business systems such as Enterprise Resource Planning (ERP) and Manufacturing Execution Systems (MES). This integration enhances collaboration and communication between different departments, streamlining the flow of information and enabling effective decision-making. It fosters cross-functional coordination, reducing errors, and improving overall supply chain efficiency.
Overall, implementing MRP in the supply chain provides businesses with numerous benefits, including improved inventory control, enhanced production planning, shortened lead times, effective resource allocation, better decision-making, and improved collaboration. By leveraging these advantages, companies can achieve cost savings, increased productivity, and ultimately, a competitive advantage in the market.
It is worth noting that successful implementation and utilization of MRP require training, proper system configuration, and ongoing maintenance. MRP systems need to be regularly updated with accurate data to generate reliable plans and forecasts. With proper implementation and management, MRP can optimize supply chain operations and drive long-term business success.
Challenges in Implementing MRP
Implementing Material Requirements Planning (MRP) in the supply chain can bring significant benefits, but it also presents certain challenges that businesses need to be aware of. Successfully navigating these challenges is crucial for a smooth and effective implementation process. Let’s explore some of the common challenges in implementing MRP:
- Data Accuracy and Integrity: MRP relies heavily on accurate and up-to-date data, including inventory levels, lead times, and demand forecasts. Inaccurate or incomplete data can lead to incorrect calculations and unreliable plans. It is essential to establish data management processes and implement regular data validation procedures to ensure the accuracy and integrity of the information.
- System Integration: Integrating the MRP system with other business systems, such as Enterprise Resource Planning (ERP) or Manufacturing Execution Systems (MES), can be a complex process. Ensuring seamless data flow and compatibility between systems requires careful planning, system configuration, and testing. Lack of system integration can lead to data inconsistencies and hinder the effectiveness of the MRP system.
- Change Management: Implementing MRP often requires significant changes in existing processes, workflows, and organizational culture. Resistance to change from employees or management can hinder the implementation process. It is crucial to involve and train employees, communicate the benefits of MRP, and address any concerns or resistance to ensure a smooth transition and successful adoption of the new system.
- Resource Allocation: Implementing and managing an MRP system requires dedicated resources, including personnel, time, and financial investment. Allocating the necessary resources and ensuring that key stakeholders are involved and committed to the implementation process is essential for success. Adequate training and ongoing support for users are also crucial to maximize the benefits of the MRP system.
- Complexity and Customization: MRP systems can be highly complex, especially for organizations with intricate supply chains or unique production processes. Customizing the MRP system to accommodate specific business needs may be necessary but can pose implementation challenges. Balancing the need for customization with the practicality and simplicity of the system is crucial for a successful implementation.
- Supplier Collaboration: Engaging with suppliers and ensuring their cooperation and timely responses is critical for accurate material planning. Lack of collaboration or unreliable supplier information can disrupt the MRP process and lead to inventory shortages or production delays. Establishing strong relationships with suppliers and implementing effective communication channels can mitigate this challenge.
Addressing these challenges requires careful planning, effective project management, and ongoing monitoring and improvement. It is essential for businesses to have a dedicated implementation team, engage with experienced consultants if necessary, and continuously evaluate and refine the MRP system to ensure its effectiveness in optimizing supply chain operations.
While implementing MRP may present challenges, the benefits it brings in terms of improved inventory management, enhanced production planning, and better decision-making make it a worthwhile investment. By approaching the implementation process with a strategic mindset and proactively addressing the challenges, businesses can reap the rewards of a streamlined and efficient supply chain.
Best Practices for Successful MRP Implementation
Implementing Material Requirements Planning (MRP) in the supply chain requires careful planning, attention to detail, and a structured approach. By following best practices, businesses can maximize the benefits of MRP and ensure a successful implementation process. Here are key best practices for a successful MRP implementation:
- Establish Clear Objectives: Clearly define the objectives and expected outcomes of the MRP implementation. Identify the specific pain points and challenges you are looking to address and align your implementation plan with these objectives.
- Secure Management Support: Gain support from top management and ensure their active involvement throughout the implementation process. Management support is crucial for allocating resources, driving change, and establishing a culture of continuous improvement.
- Thoroughly Assess Readiness: Evaluate your organization’s readiness for MRP implementation. This includes assessing data accuracy and integrity, system compatibility, and employee readiness for change. Identify any potential roadblocks and address them proactively.
- Invest in Training and Education: Provide comprehensive training and education to all employees involved in the MRP implementation. This includes users, managers, and IT staff. Training should cover system functionality, data entry, report generation, and understanding the impact of MRP on various departments.
- Prioritize Data Accuracy and Maintenance: Ensure data accuracy and integrity for MRP calculations. Implement processes to regularly validate and update data, including inventory levels, lead times, and demand forecasts. Establish data maintenance protocols to ensure ongoing accuracy and reliability.
- Collaborate with Suppliers: Foster collaboration and effective communication with suppliers. Establish clear channels of communication and work together to ensure accurate and timely information exchange. Collaborating with suppliers helps mitigate risks, reduce lead times, and improve overall supply chain performance.
- Test and Validate the System: Before fully implementing MRP, conduct thorough testing and validation of the system. This includes testing different scenarios, validating system outputs, and ensuring the system aligns with the specific needs of your organization. Address any issues or gaps identified during the testing phase.
- Monitor and Measure Performance: Continuously monitor and measure the performance of the MRP system after implementation. Establish key performance indicators (KPIs) to assess the effectiveness of the system. Regularly review and analyze the data to identify areas for improvement and make necessary adjustments.
- Encourage Continuous Improvement: Foster a culture of continuous improvement within the organization. Encourage feedback from users, collect suggestions for system enhancements, and incorporate lessons learned into future iterations of the MRP system. Regularly review and update processes and procedures to optimize the use of MRP in the supply chain.
By following these best practices, businesses can set themselves up for success in implementing MRP in the supply chain. Clear objectives, management support, data accuracy, employee training, supplier collaboration, testing, and ongoing monitoring are key elements for a successful implementation. Embracing a culture of continuous improvement ensures that the benefits of MRP are realized and sustained in the long run.
It is important to note that each organization’s implementation journey may vary based on its specific needs and requirements. Therefore, adapting these best practices to fit your organizational context will help ensure a successful MRP implementation and optimize your supply chain operations.
Conclusion
Material Requirements Planning (MRP) is a critical component of efficient supply chain management. It enables businesses to optimize inventory levels, streamline production planning, and enhance overall operational efficiency. By accurately forecasting material requirements and synchronizing production and procurement activities, MRP helps businesses meet customer demands, reduce costs, and improve customer satisfaction.
We have explored the key components of an MRP system, including the Master Production Schedule (MPS), Bill of Materials (BOM), and inventory status. The MRP planning process, which involves creating the MPS, analyzing the BOM, evaluating inventory, and calculating net requirements, provides a structured approach to efficient material planning.
Implementing MRP in the supply chain brings numerous benefits. By optimizing inventory control, enhancing production planning, shortening lead times, and effectively allocating resources, businesses can achieve improved operational efficiency and cost savings. MRP also enables better decision-making and collaboration, making businesses more agile and responsive to market changes.
However, implementing MRP comes with challenges. Data accuracy, system integration, change management, and supplier collaboration are common obstacles that need to be overcome for a successful implementation. Following best practices such as clearly defining objectives, securing management support, investing in training, and fostering continuous improvement can help overcome these challenges and drive successful MRP implementation.
In conclusion, Material Requirements Planning plays a crucial role in optimizing supply chain operations. By implementing MRP and following best practices, businesses can achieve improved inventory control, production planning, and resource utilization. The benefits of MRP include reduced costs, shorter lead times, improved decision-making, and enhanced collaboration. With careful planning, attention to detail, and a commitment to continuous improvement, businesses can leverage the power of MRP to drive efficiency and competitiveness in today’s dynamic business landscape.