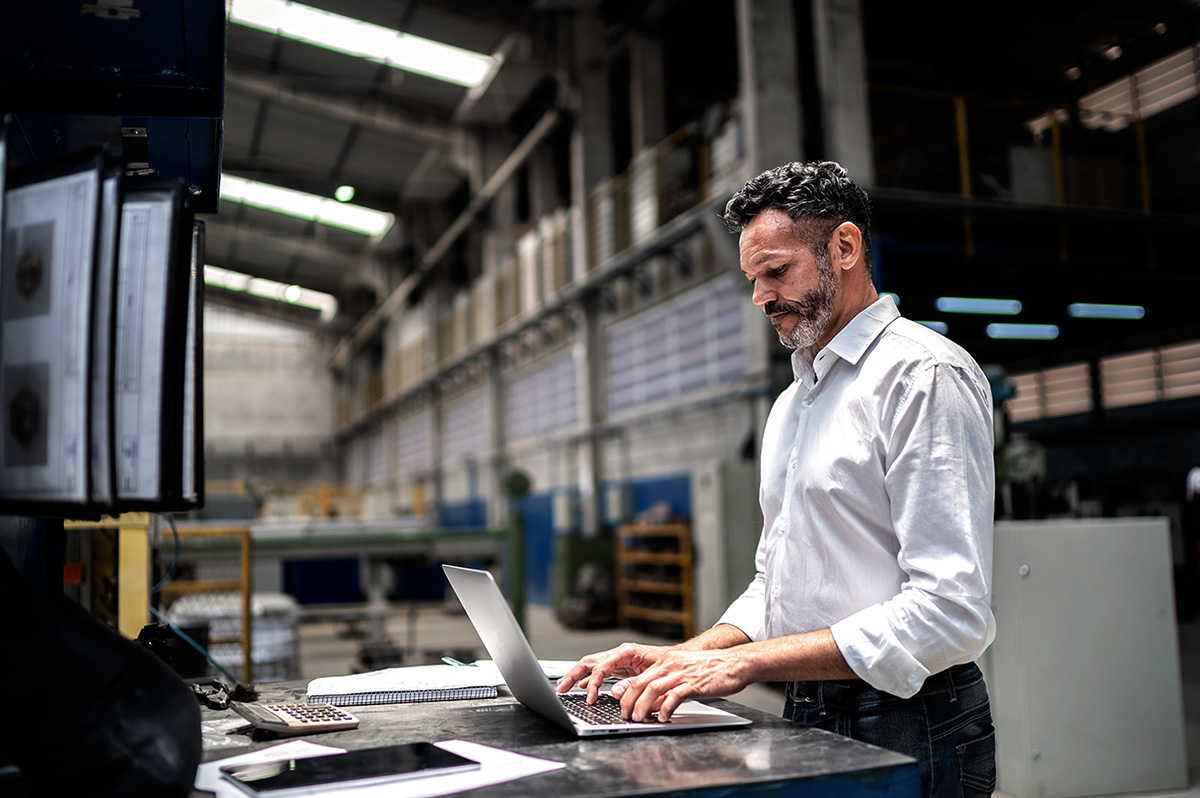
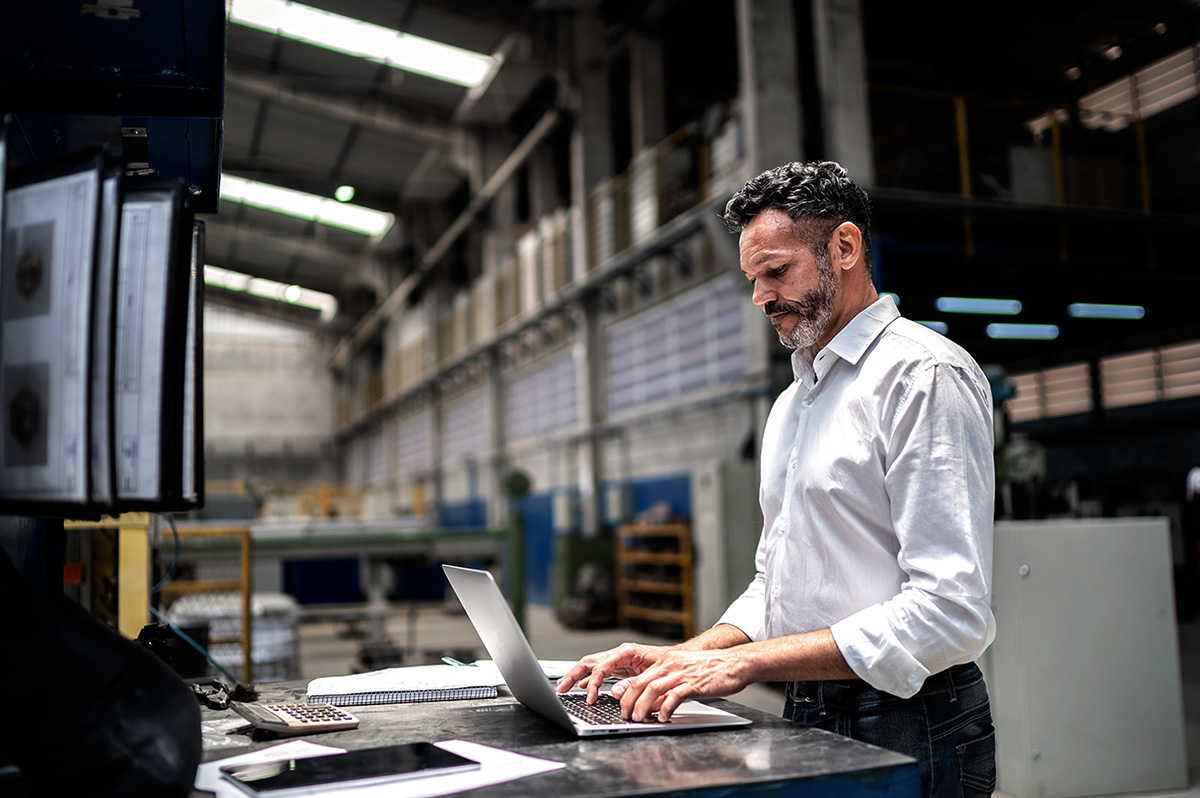
Finance
How To Set Up A Supply Chain
Published: October 19, 2023
Learn how to set up a supply chain for your business, with a specific focus on finance. Gain insights into optimizing financial aspects and improving efficiency in your supply chain management.
(Many of the links in this article redirect to a specific reviewed product. Your purchase of these products through affiliate links helps to generate commission for LiveWell, at no extra cost. Learn more)
Table of Contents
- Introduction
- Step 1: Identifying your supply chain objectives
- Step 2: Selecting the right suppliers and vendors
- Step 3: Establishing effective communication channels
- Step 4: Creating and implementing a planning and forecasting system
- Step 5: Managing inventory and optimizing storage facilities
- Step 6: Implementing efficient transportation and logistics strategies
- Step 7: Monitoring and evaluating supply chain performance
- Step 8: Continuously improving and adapting your supply chain
- Conclusion
Introduction
Welcome to the world of supply chain management, where businesses strive to optimize their operations and achieve seamless coordination between suppliers, manufacturers, distributors, and customers. A well-designed supply chain can make a significant difference to a company’s bottom line, ensuring timely delivery of products, minimizing costs, and maximizing customer satisfaction.
Setting up an efficient supply chain is crucial for businesses of all sizes, from small startups to large multinational corporations. It involves a careful analysis of your business objectives, identifying appropriate vendors and suppliers, establishing effective communication channels, implementing planning and forecasting systems, managing inventory, optimizing storage facilities, and ensuring a smooth transportation and logistics process.
In this article, we will guide you through the essential steps to set up a successful supply chain. Whether you are starting a new business or looking to improve your existing operations, these steps will help you streamline your processes, reduce costs, and enhance customer service.
Before diving into the details, it’s important to note that every supply chain is unique and should be tailored to the specific needs of your business. The steps outlined here provide a general framework that can be customized and adapted to fit your industry, product, and market conditions.
Now let’s explore the key steps to set up a supply chain that will drive efficiency, cost savings, and customer satisfaction.
Step 1: Identifying your supply chain objectives
Before you start setting up your supply chain, it’s crucial to define your objectives and understand what you hope to achieve. This step will serve as a roadmap for the rest of the process and help you make informed decisions.
Start by asking yourself some key questions. What are your overall business goals and how can a well-designed supply chain support them? Are you looking to minimize costs, improve delivery times, increase product quality, or enhance customer service?
Once you have a clear understanding of your objectives, break them down into specific, measurable targets. For example, if your goal is to improve delivery times, you might set a target of reducing lead times by a certain percentage or implementing a same-day delivery service.
Identifying your supply chain objectives will also involve considering the needs and preferences of your customers. Conduct market research to understand customer expectations, preferences, and purchasing patterns. This will help you align your supply chain strategy with customer demands and enhance customer satisfaction.
Additionally, consider any industry-specific challenges or regulations that may impact your supply chain. For example, if you are in the food industry, you may need to comply with strict quality control and safety regulations.
Overall, the key to successful supply chain objectives is to make them relevant, achievable, and aligned with your overall business goals. By having a clear vision of what you want to achieve, you can effectively design and implement a supply chain that will support your growth and success.
Step 2: Selecting the right suppliers and vendors
Selecting the right suppliers and vendors is a critical step in building a successful supply chain. The quality and reliability of your suppliers directly impact the efficiency and effectiveness of your operations. Here are some key factors to consider when choosing your suppliers and vendors:
- Quality and Reliability: Look for suppliers who have a track record of providing high-quality products and services. Evaluate their reputation, certifications, and testimonials to ensure they are reliable and capable of meeting your business needs.
- Price and Cost Structure: While cost is an important factor, it should not be the sole determining factor. Consider the overall value you will receive from the supplier in terms of quality, reliability, and additional services they can provide.
- Capacity and Scalability: Assess the supplier’s capacity to meet your demand both in terms of production capacity and ability to scale up as your business grows.
- Location: Consider the geographical proximity of the supplier to your business to reduce transportation costs and lead times. However, also evaluate factors such as political stability and infrastructure to ensure a smooth supply chain flow.
- Supplier’s Financial Stability: Evaluate the financial stability and long-term viability of your potential suppliers. This will help mitigate the risk of disruptions to your supply chain in case of any financial challenges.
- Collaboration and Communication: Seek suppliers who are willing to collaborate and develop strong communication channels. Effective communication is vital for maintaining transparency, resolving issues, and aligning strategies.
- Ethical and Sustainability Considerations: Do your research to ensure that your suppliers adhere to ethical and sustainable practices. This could include fair labor practices, environmental sustainability, and responsible sourcing.
It is important to conduct thorough due diligence when selecting suppliers and vendors. Request proposals, visit their facilities, and establish mutual expectations and performance metrics. This will help you build strong partnerships and ensure the smooth flow of materials and services through your supply chain.
Step 3: Establishing effective communication channels
Effective communication is a cornerstone of a well-functioning supply chain. It ensures that relevant information flows smoothly between all parties involved, facilitating coordination, problem-solving, and decision-making. Here are some key steps to establish effective communication channels in your supply chain:
- Define Communication Protocols: Establish clear guidelines and protocols for communication. Determine the preferred method of communication for different types of interactions, such as email, phone calls, or video conferences. Clearly define roles and responsibilities, including who should be contacted for specific issues.
- Centralize Information: Implement a centralized system or platform where all relevant information related to the supply chain can be accessed by authorized stakeholders. This could include information such as purchase orders, inventory levels, production schedules, and delivery status. Ensure that all parties have access to this system and are trained on how to use it effectively.
- Regular Meetings: Schedule regular meetings with key stakeholders, such as suppliers, vendors, and internal teams. These meetings can be in-person or virtual, depending on the geographical locations involved. Use these meetings to discuss performance, address issues, share updates, and align strategies.
- Real-time Tracking and Visibility: Implement technologies that provide real-time tracking and visibility of the supply chain process. This could involve using barcode scanning, RFID tags, or advanced software systems. Real-time visibility helps identify bottlenecks, anticipate delays, and take proactive measures to ensure smooth operations.
- Feedback Mechanisms: Establish feedback mechanisms to gather input from all stakeholders in the supply chain. Encourage suppliers, vendors, and customers to provide feedback on their experiences, suggestions for improvement, and any issues they may have encountered. This feedback can help identify areas for optimization and build stronger partnerships.
- Addressing Language and Cultural Barriers: If you operate in a global supply chain, be mindful of language and cultural differences. Ensure that communication is clear and that all parties understand each other. Provide language support if necessary and be sensitive to cultural nuances to foster effective collaboration.
Establishing effective communication channels will enhance transparency, enable efficient problem-solving, and foster strong relationships with suppliers, vendors, and other stakeholders. It will also help you adapt quickly to market changes and ensure that your supply chain operates smoothly and efficiently.
Step 4: Creating and implementing a planning and forecasting system
A robust planning and forecasting system is crucial for optimizing your supply chain. It enables you to estimate demand, plan production, anticipate inventory needs, and make informed decisions. Here are the key steps to creating and implementing an effective planning and forecasting system:
- Collect Data: Gather historical sales data, market trends, and other relevant information to analyze patterns and make accurate forecasts. Utilize data from various sources, such as sales records, customer feedback, industry reports, and market research.
- Select Forecasting Techniques: Choose appropriate forecasting techniques based on your industry, product type, and available data. Common methods include time series analysis, moving averages, regression analysis, and predictive modeling. Consider using a combination of techniques for more accurate forecasts.
- Collaborate with Stakeholders: Involve key stakeholders, such as sales and marketing teams, production managers, suppliers, and vendors, in the forecasting process. Their insights and expertise can provide valuable inputs to improve the accuracy of your forecasts.
- Establish Lead Time: Consider the lead time required for procurement, production, and delivery when creating your planning system. This will help you ensure that you have sufficient inventory to meet demand without overstocking or causing delays.
- Integrate with Suppliers and Vendors: Share your forecasted demand with your suppliers and vendors to enable them to align their production and inventory levels accordingly. Establish strong communication channels to receive updates on their capacity, lead times, and any potential disruptions.
- Monitor and Adjust: Continuously monitor your actual sales and compare them with your forecasts. Identify any discrepancies and analyze the reasons behind them. Use this information to refine your forecasting models and adjust your planning accordingly. Regularly review and update your forecasts as market conditions, customer demand, and other factors change.
A well-implemented planning and forecasting system will help you optimize inventory levels, prevent stockouts or overstocking, reduce costs, and improve customer service. By accurately anticipating demand, you can align your procurement, production, and distribution processes, ensuring smooth operations throughout your supply chain.
Step 5: Managing inventory and optimizing storage facilities
Managing inventory efficiently is crucial for maintaining a smooth supply chain and meeting customer demands. It involves ensuring the right quantity of products is available at the right time while minimizing costs and avoiding stockouts or excess inventory. Here are key steps to effectively manage your inventory and optimize storage facilities:
- ABC Analysis: Classify your inventory items based on their value and prioritize them accordingly. This helps in allocating resources and attention to high-value items while reducing effort on low-value items.
- Implement Just-in-Time (JIT) System: Adopt a JIT approach to inventory management, where you receive goods from suppliers only when they are needed for production or customer demands. This reduces carrying costs and minimizes the risk of obsolete inventory.
- Utilize Inventory Management Software: Invest in inventory management software that provides real-time visibility of stock levels, tracks movement, and generates reports. This software can help streamline inventory processes and ensure accurate inventory counts.
- Implement Demand-Driven Replenishment: Base your replenishment decisions on actual demand rather than forecasts. Utilize data from sales and customer feedback to optimize reorder points and quantities, keeping inventory levels in line with demand fluctuations.
- Establish Reorder Points: Set reorder points for each inventory item based on lead times, demand variability, and desired service levels. This ensures that you reorder items before they run out, minimizing stockouts.
- Optimize Storage Facilities: Analyze your storage facilities to ensure they are organized and structured for efficiency. Maximize the use of available space through proper shelving, labeling, and categorization. Consider implementing automation and technology, such as barcode scanning or RFID, to streamline inventory management processes.
- Implement Quality Control Measures: Regularly inspect and assess the quality of inventory items to prevent storing defective or damaged products. This reduces the risk of returns, waste, and customer dissatisfaction.
- Embrace Lean Principles: Apply lean principles, such as reducing waste and improving efficiency, to your inventory management processes. Implement practices like Kanban, 5S, and continuous improvement to optimize storage space and enhance overall supply chain performance.
By effectively managing inventory and optimizing storage facilities, you can reduce carrying costs, improve order fulfillment, and ensure timely delivery to customers. It also fosters better coordination between suppliers, manufacturers, and distributors, resulting in a more efficient and effective supply chain.
Step 6: Implementing efficient transportation and logistics strategies
Efficient transportation and logistics are essential for ensuring the smooth movement of goods throughout the supply chain. It involves optimizing transportation modes, routes, and processes to minimize costs, reduce delays, and meet customer expectations. Here are the key steps to implementing efficient transportation and logistics strategies:
- Transportation Mode Selection: Evaluate different transportation modes, including road, rail, air, and sea, to determine the most suitable option for your products. Consider factors such as distance, speed, cost, reliability, and the nature of your goods. Choose a mode that offers the best balance between cost and service level.
- Route Optimization: Utilize route optimization tools and software to determine the most efficient routes for product deliveries. Consider factors such as distance, traffic conditions, fuel efficiency, and delivery windows. By minimizing travel time and fuel consumption, you can reduce costs and improve delivery performance.
- Collaborate with Carriers: Develop strong partnerships with carriers and logistics providers. Maintain open communication channels, share information on shipment volumes and timing, and negotiate favorable contracts.
- Utilize Warehouse Management Systems (WMS): Implement a robust WMS that integrates with transportation management systems. This enables you to track inventory, manage orders, and coordinate transportation activities in real-time. By having visibility across the supply chain, you can optimize transportation schedules and minimize delays.
- Embrace Automation and Technology: Make use of emerging technologies, such as GPS tracking, telematics, and Internet of Things (IoT) devices, to monitor shipments, track delivery status, and proactively address any issues. Automation can also streamline processes, reduce manual errors, and improve overall efficiency.
- Collaborate with Suppliers and Vendors: Coordinate with your suppliers and vendors to synchronize transportation activities. Consolidate shipments whenever possible, optimizing the use of transportation resources and reducing costs. Collaboration can also help in aligning production and delivery schedules for better efficiency.
- Implement Reverse Logistics: Develop a reverse logistics strategy to handle product returns, repairs, or recycling. Efficient reverse logistics reduces waste, improves customer service, and provides opportunities for cost recovery or value addition.
- Continuous Monitoring and Evaluation: Regularly monitor transportation and logistics performance through key performance indicators (KPIs). Evaluate metrics such as on-time delivery, shipment accuracy, and cost per unit transported. Identify areas for improvement and make adjustments to enhance efficiency and customer satisfaction.
By implementing efficient transportation and logistics strategies, you can reduce costs, improve delivery times, enhance customer service, and strengthen your overall supply chain operations. It enables you to effectively manage the movement of goods, reduce disruptions, and optimize resources for a competitive advantage.
Step 7: Monitoring and evaluating supply chain performance
Monitoring and evaluating the performance of your supply chain is crucial for identifying areas of improvement, recognizing successes, and ensuring that you are meeting your goals and objectives. By regularly assessing the performance metrics, you can make data-driven decisions to optimize your supply chain. Here are the key steps to effectively monitor and evaluate supply chain performance:
- Establish Key Performance Indicators (KPIs): Determine the KPIs that align with your supply chain objectives. These could include metrics such as order fulfillment cycle time, inventory turnover, on-time delivery, customer satisfaction, and cost per order. Establish targets and benchmarks for each KPI.
- Collect and Analyze Data: Gather relevant data from different stages of the supply chain, including procurement, production, transportation, and customer service. Utilize data analytics tools to identify trends, patterns, and areas of improvement. Compare actual performance against the set targets.
- Regularly Review Performance: Conduct periodic reviews of supply chain performance, analyzing the data collected. This could be done monthly, quarterly, or annually based on the frequency of your operations. Identify any gaps or discrepancies and understand the root causes behind them.
- Identify Improvement Opportunities: Use the insights gained from the performance reviews to identify areas for improvement. This could involve streamlining processes, reducing costs, improving collaboration with suppliers, or enhancing customer service. Prioritize the improvement opportunities based on their impact and feasibility.
- Implement Continuous Improvement Initiatives: Develop action plans to address the identified improvement opportunities. Assign responsibilities, set timelines, and track progress. Consider implementing Lean Six Sigma or other process improvement methodologies to drive continuous improvement in your supply chain.
- Seek Feedback from Stakeholders: Collect feedback from suppliers, vendors, and customers to understand their satisfaction levels and gather suggestions for improvement. This feedback can provide valuable insights into areas that may not be captured by data alone.
- Embrace Technology: Leverage technology such as supply chain management software, analytics tools, and real-time tracking systems to monitor and evaluate supply chain performance more effectively. These tools can provide actionable insights and automate data collection for more accurate analysis.
- Monitor Industry Trends and Best Practices: Stay updated on industry trends and best practices in supply chain management. Attend conferences, join industry associations, and participate in relevant forums to gain knowledge and learn from others in your field.
By monitoring and evaluating supply chain performance, you can drive continuous improvement, optimize processes, and stay ahead of the competition. Regular assessment ensures that your supply chain is agile, responsive, and aligned with your business goals.
Step 8: Continuously improving and adapting your supply chain
Supply chain management is an ongoing process that requires continuous improvement and adaptation to changing market conditions, customer demands, and technological advancements. By continuously reviewing and refining your supply chain, you can stay agile, efficient, and competitive. Here are the key steps to continuously improve and adapt your supply chain:
- Encourage a Culture of Innovation: Foster a culture that embraces innovation and encourages employees to share ideas for improvement. Create a safe environment where individuals feel empowered to suggest changes and experiment with new approaches.
- Embrace New Technologies: Stay updated on emerging technologies and trends that can enhance your supply chain. This could include automation, robotics, artificial intelligence, blockchain, or predictive analytics. Assess their potential impact and consider implementing those that align with your objectives.
- Seek Collaboration and Partnerships: Collaborate with suppliers, vendors, and logistics partners to explore opportunities for improvement. Share best practices, exchange insights, and work together to develop more efficient processes. Consider strategic partnerships to gain access to specialized expertise or technologies.
- Stay Agile and Flexible: Anticipate and adapt to changes in market demand, customer preferences, and regulations. Build flexibility into your supply chain processes, allowing you to quickly respond to fluctuations in demand or unexpected disruptions. Consider implementing agile and lean principles to improve responsiveness.
- Invest in Training and Development: Provide ongoing training and development opportunities for your supply chain team. Equip them with the knowledge and skills required to address new challenges and leverage emerging technologies. Encourage cross-functional collaboration and knowledge sharing.
- Regularly Review Supplier Performance: Continuously evaluate the performance of your suppliers and vendors. Set performance expectations, monitor their adherence to quality standards and delivery schedules, and address any issues promptly. Consider conducting periodic supplier reviews or audits to ensure alignment with your supply chain goals.
- Prioritize Sustainability and Ethical Practices: Incorporate sustainability and ethical considerations into your supply chain. Seek eco-friendly alternatives, promote fair labor practices, and ensure responsible sourcing. Monitor the environmental and social impact of your supply chain and seek opportunities to reduce waste and improve social responsibility.
- Monitor Competitive Landscape: Stay informed about your competitors’ supply chain strategies and practices. Regularly benchmark your performance against industry leaders and identify areas where you can gain a competitive edge. Learn from their best practices and adapt them to your own supply chain.
By continuously improving and adapting your supply chain, you can proactively respond to market changes, enhance efficiency, and capitalize on opportunities. Embracing innovation and remaining flexible will position your business for success in an ever-evolving business landscape.
Conclusion
Setting up and managing a successful supply chain is a complex and ongoing process. It requires careful planning, collaboration with stakeholders, and continuous improvement. By following the steps outlined in this article, you can establish an efficient and effective supply chain that drives cost savings, enhances customer satisfaction, and strengthens your competitive advantage.
It all begins with identifying your supply chain objectives and aligning them with your overall business goals. This provides a clear direction and helps you make informed decisions throughout the process. Selecting the right suppliers and vendors, establishing effective communication channels, and implementing planning and forecasting systems are critical to ensure smooth operations.
Managing inventory, optimizing storage facilities, and implementing efficient transportation and logistics strategies enable you to minimize costs, reduce delays, and meet customer demands. Monitoring and evaluating supply chain performance help you identify areas for improvement, foster continuous improvement, and adapt to changing market conditions.
Lastly, maintaining a mindset of continuous improvement and adaptability ensures that your supply chain stays agile and responsive. Embrace new technologies, seek collaboration, invest in training, and prioritize sustainability to stay ahead of the competition.
Remember, every supply chain is unique, and it’s important to tailor the strategies and approaches to fit your specific industry, product, and market conditions. Regularly review and adjust your supply chain strategies to ensure they remain relevant and aligned with your business objectives.
By following these steps and continuously refining your supply chain, you can optimize operations, reduce costs, and enhance customer satisfaction. A well-designed and effectively managed supply chain is not just a business advantage, but a key driver of long-term success.