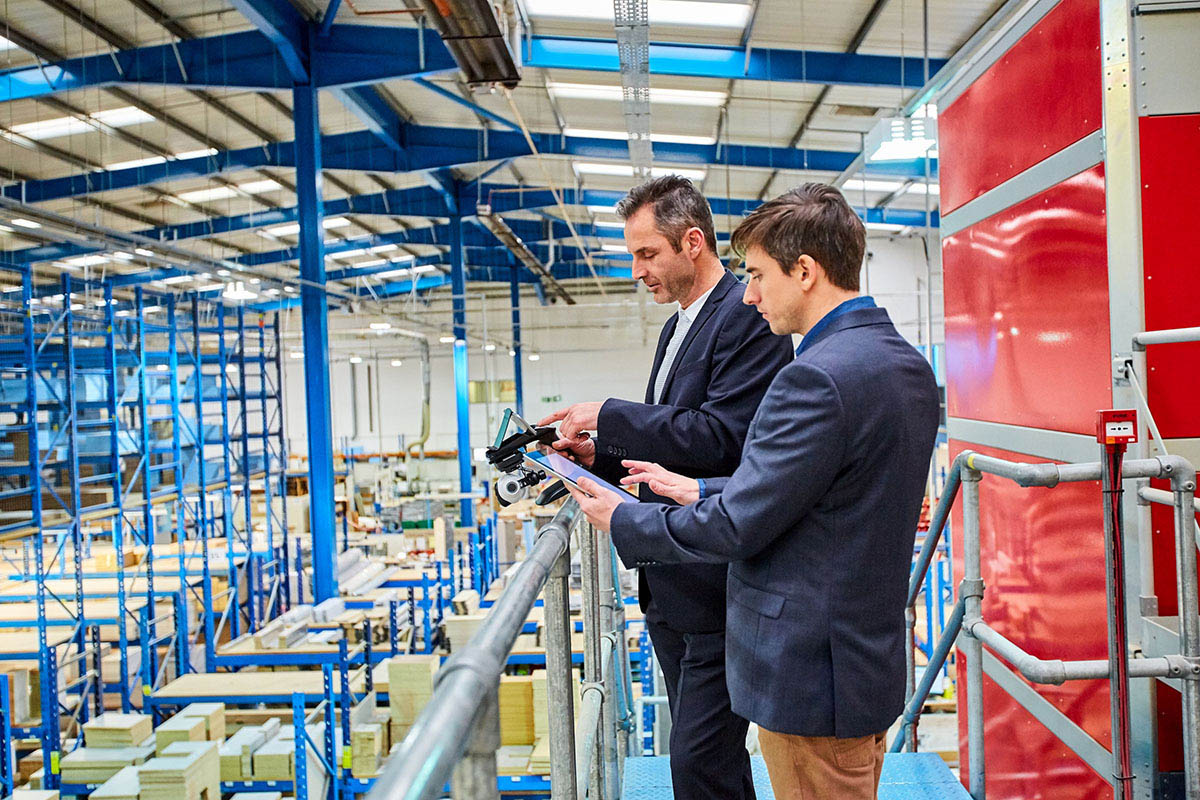
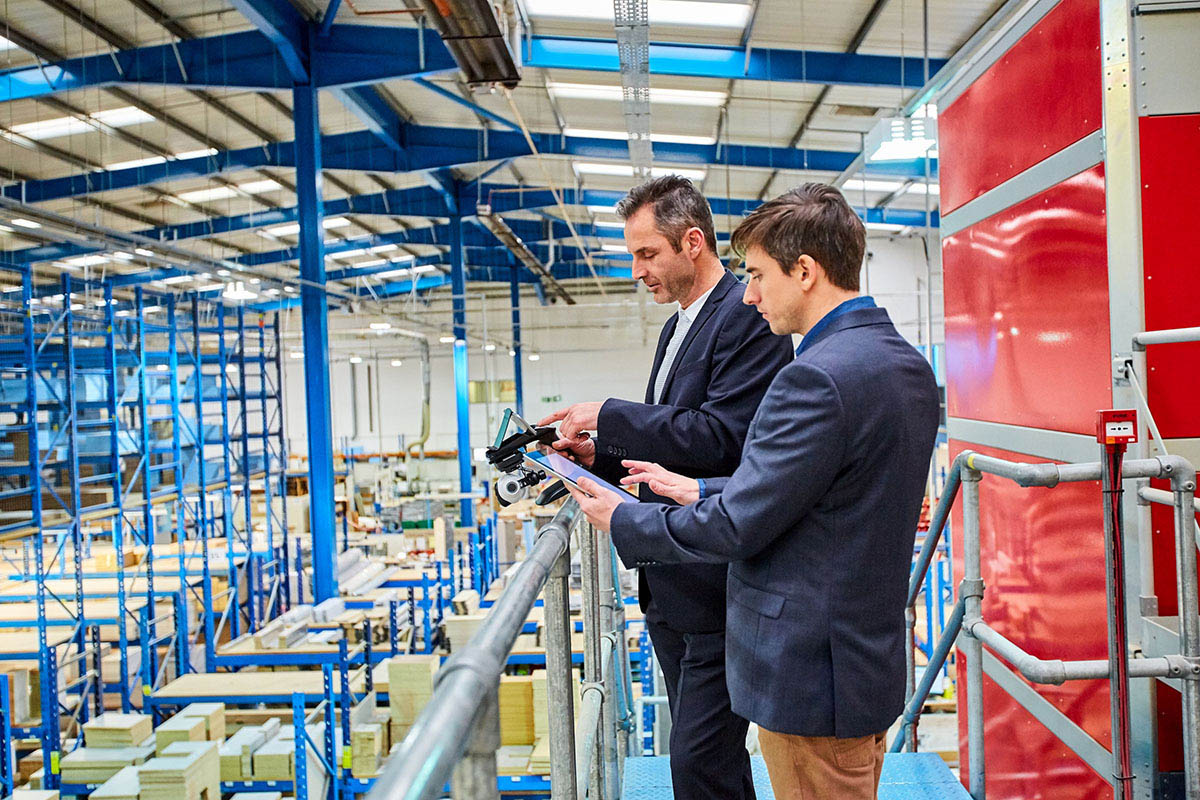
Finance
How To Reduce Supply Chain Cost?
Published: October 19, 2023
Learn effective strategies and techniques to reduce supply chain costs and optimize your finance department. Discover how to streamline processes and save money in your supply chain.
(Many of the links in this article redirect to a specific reviewed product. Your purchase of these products through affiliate links helps to generate commission for LiveWell, at no extra cost. Learn more)
Table of Contents
- Introduction
- Analyzing the Supply Chain
- Identifying Cost Drivers
- Streamlining Inventory Management
- Optimizing Transportation Processes
- Implementing Efficient Warehousing Strategies
- Harnessing Technology and Automation
- Leveraging Strategic Partnerships
- Improving Forecasting and Demand Planning
- Enhancing Supplier Management
- Enhancing Data Visibility and Analytics
- Reducing Product Returns and Reverse Logistics Costs
- Conclusion
Introduction
In today’s increasingly competitive business landscape, organizations are constantly looking for ways to optimize their operations and reduce costs. One area that offers tremendous potential for cost savings is the supply chain. The supply chain encompasses all the activities and processes involved in delivering a product or service, from sourcing raw materials to delivering the final product to the customer.
Reducing supply chain costs is crucial for businesses to maintain a competitive edge in the market. By minimizing expenses, companies can lower their overall production costs, improve profitability, and ultimately offer more competitive prices to customers. However, achieving cost reduction in the supply chain is not without its challenges. It requires a systematic approach and a deep understanding of the key cost drivers and potential areas for optimization.
In this article, we will explore some effective strategies and best practices to reduce supply chain costs. By implementing these strategies, businesses can achieve greater efficiency, improve profitability, and gain a competitive advantage in the marketplace.
Analyzing the Supply Chain
The first step in reducing supply chain costs is to conduct a comprehensive analysis of the existing supply chain operations. This analysis involves mapping out the entire supply chain, from suppliers to distributors to customers, and identifying the various stages and processes involved.
By analyzing the supply chain, businesses can identify inefficiencies, bottlenecks, and areas of potential cost reduction. This can be done through techniques such as value stream mapping, which visually represents the flow of materials and information throughout the supply chain.
During the analysis, it is important to gather data on key performance indicators (KPIs) such as lead times, transportation costs, inventory holding costs, and order fulfillment rates. This data can provide valuable insights into the current state of the supply chain and highlight areas that require improvement.
Additionally, businesses should consider conducting a cost-to-serve analysis. This involves understanding the true costs associated with serving different customers or product lines. By segmenting customers and products based on profitability, businesses can identify areas where costs can be reduced or resources can be reallocated.
Through this analysis, businesses can gain a holistic view of their supply chain and identify specific areas for improvement and cost reduction. This lays the foundation for implementing targeted strategies and solutions to optimize supply chain operations and reduce costs.
Identifying Cost Drivers
Once the supply chain has been analyzed, the next step is to identify the key cost drivers within the system. Cost drivers are the factors that directly influence the costs incurred in the supply chain.
There are several common cost drivers in the supply chain, including transportation costs, inventory holding costs, labor costs, and packaging costs. Each of these drivers can have a significant impact on the overall cost of the supply chain.
One effective way to identify cost drivers is to conduct a thorough cost breakdown analysis. This involves breaking down the total cost of the supply chain into its various components and analyzing the contribution of each cost driver to the overall expenses.
For example, in transportation, factors such as shipping distances, mode of transportation, and fuel costs can greatly impact transportation costs. By understanding these cost drivers, businesses can explore strategies such as consolidation, route optimization, or renegotiating contracts with carriers to reduce transportation expenses.
Similarly, in inventory management, factors such as carrying costs, stockouts, and obsolescence can drive up inventory holding costs. By implementing techniques like just-in-time inventory management or utilizing advanced inventory forecasting models, businesses can optimize inventory levels and minimize holding costs.
Identifying cost drivers allows businesses to prioritize their efforts and focus on the areas that have the most significant impact on supply chain costs. By understanding the key drivers, businesses can develop targeted strategies and initiatives to address these specific areas and achieve cost reduction.
Streamlining Inventory Management
Inventory management plays a critical role in the supply chain and can have a significant impact on costs. Inefficient inventory management can result in excess inventory, carrying costs, stockouts, and obsolescence, all of which contribute to increased expenses.
One strategy for streamlining inventory management is implementing a demand-driven approach. This involves using data and analytics to forecast demand accurately and aligning inventory levels accordingly. By utilizing advanced forecasting techniques and demand planning software, businesses can optimize inventory levels, reduce carrying costs, and avoid stockouts.
Another effective way to streamline inventory management is through the implementation of just-in-time (JIT) inventory practices. JIT aims to minimize inventory levels by receiving materials or components only when they are needed for production or distribution. By receiving inventory closer to the time it is needed, businesses can reduce carrying costs and free up warehouse space.
Additionally, businesses can explore vendor-managed inventory (VMI) programs. In a VMI arrangement, the supplier takes responsibility for managing and replenishing inventory at the customer’s location. This can help reduce inventory holding costs and improve supply chain efficiency, as the supplier has more visibility and control over inventory levels.
Implementing efficient inventory management systems and technology can also contribute to streamlining inventory processes. Inventory management software can automate tasks such as tracking stock levels, generating replenishment orders, and conducting real-time inventory audits. This can reduce manual errors, improve accuracy, and enhance overall inventory control.
Furthermore, businesses should regularly review and optimize their product portfolio. By identifying slow-moving or obsolete items, businesses can make informed decisions about discontinuing or discounting these products to reduce holding costs and free up warehouse space.
Streamlining inventory management is essential for reducing supply chain costs. By implementing demand-driven approaches, JIT practices, VMI programs, and leveraging technology, businesses can achieve better control over inventory levels and increase operational efficiency.
Optimizing Transportation Processes
Transportation is a critical component of the supply chain, and inefficient transportation processes can contribute significantly to supply chain costs. By optimizing transportation processes, businesses can reduce transportation expenses and improve overall supply chain efficiency.
One strategy for optimizing transportation is to consolidate shipments. Consolidation involves combining multiple smaller shipments into larger ones to achieve economies of scale. This reduces transportation costs by maximizing the use of space and reducing the number of trips required.
Businesses can also explore alternative transportation modes to find the most cost-effective option. For example, utilizing rail or intermodal transportation can be more cost-efficient for long-distance hauls compared to traditional trucking. By analyzing shipment volumes, distances, and transit times, businesses can determine the most suitable mode of transportation for their needs.
Routing optimization is another key aspect of optimizing transportation. By utilizing route planning software, businesses can efficiently plan the most optimal routes, considering factors such as distance, traffic conditions, delivery time windows, and fuel consumption. This reduces unnecessary mileage and improves delivery efficiency, leading to cost savings.
Collaboration and coordination with carriers and logistics providers is crucial for transportation optimization. Establishing strategic partnerships with reliable and efficient providers can lead to better rates, improved service levels, and increased operational flexibility. Regular communication and performance monitoring are essential to ensure carriers are meeting the agreed-upon service levels and cost expectations.
Technology can play a significant role in optimizing transportation processes. Implementing a transportation management system (TMS) can automate and streamline various transportation tasks, such as route planning, carrier selection, shipment tracking, and freight audit and payment. This improves visibility, reduces manual errors, and enhances overall transportation efficiency.
Furthermore, businesses should consider adopting sustainable transportation practices. By incorporating eco-friendly vehicles, optimizing delivery routes to minimize fuel consumption, and exploring carbon offset programs, businesses can not only reduce transportation costs but also contribute to environmental sustainability.
Optimizing transportation processes requires careful analysis, strategic partnerships, and the effective use of technology. By consolidating shipments, exploring alternative transportation modes, optimizing routes, collaborating with carriers, and embracing sustainability, businesses can significantly reduce transportation costs and enhance overall supply chain performance.
Implementing Efficient Warehousing Strategies
Efficient warehousing is crucial for reducing supply chain costs and improving overall operational efficiency. By implementing strategic warehousing strategies, businesses can optimize inventory management, reduce handling costs, and improve order fulfillment processes.
One key strategy is warehouse layout optimization. By analyzing the flow of materials and goods within the warehouse, businesses can design an efficient layout that minimizes the distance traveled and maximizes space utilization. This can improve the speed of picking, packing, and shipping processes, reducing labor costs and improving overall productivity.
In addition to layout optimization, businesses can implement advanced inventory management techniques within the warehouse. This includes employing techniques such as ABC analysis, which categorizes inventory based on its value and demand. By storing high-demand items in easily accessible locations and organizing inventory based on frequency of picking, businesses can reduce the time and effort required to fulfill orders.
Another effective strategy is the use of automation and technology in warehouse operations. Automated systems such as conveyor belts, robotic picking systems, and automated storage and retrieval systems (AS/RS) can improve efficiency and reduce human errors. Warehouse management systems (WMS) can integrate inventory data, optimize picking routes, and provide real-time visibility into inventory levels, further streamlining operations.
Businesses should also consider cross-docking as a strategy to minimize inventory holding costs and optimize the use of warehouse space. Cross-docking involves unloading incoming shipments from suppliers and immediately loading them onto outbound vehicles for distribution, bypassing the need for storage. This reduces inventory holding costs and expedites the delivery process.
Furthermore, implementing effective warehouse labor management strategies is crucial for optimizing operational costs. This includes training warehouse personnel, implementing performance metrics and incentives, and utilizing labor management systems (LMS) to monitor and improve productivity. By ensuring that the workforce is well-trained and motivated, businesses can enhance operational efficiency and reduce unnecessary labor costs.
Regular evaluation and continuous improvement are essential in implementing efficient warehousing strategies. By analyzing operational data, measuring key performance indicators (KPIs), and seeking feedback from warehouse staff, businesses can identify areas for improvement and implement targeted solutions to further optimize their warehousing operations.
Implementing efficient warehousing strategies not only reduces costs but also enhances the overall customer experience by improving order accuracy, reducing lead times, and enabling faster order fulfillment processes. By optimizing warehouse layout, utilizing technology, considering cross-docking, managing warehouse labor effectively, and fostering a culture of continuous improvement, businesses can achieve significant cost savings and operational efficiency in their supply chain.
Harnessing Technology and Automation
In today’s digital age, harnessing technology and automation is vital for reducing supply chain costs and increasing operational efficiency. By leveraging innovative technologies, businesses can streamline processes, improve accuracy, and optimize resource allocation.
One key technology in supply chain management is the use of advanced analytics and data-driven insights. By collecting and analyzing data from various sources such as sales, inventory, and operations, businesses can gain valuable insights into their supply chain performance. This enables them to identify bottlenecks, inefficiencies, and areas for improvement, leading to cost reduction and increased efficiency.
Implementing a robust enterprise resource planning (ERP) system is another crucial step. ERP systems integrate various business functions such as finance, manufacturing, and inventory management into a single platform. This allows for centralized data management, real-time visibility, and streamlined operations, resulting in improved decision-making and cost optimization.
Automation plays a significant role in reducing costs and improving productivity. Automated processes, such as order processing, inventory tracking, and invoicing, can help eliminate manual errors and streamline workflows. Robotic process automation (RPA) and artificial intelligence (AI) can further automate repetitive tasks, such as data entry and reporting, freeing up valuable time for employees to focus on more strategic activities.
The implementation of advanced technologies like Internet of Things (IoT) devices and sensors can provide real-time visibility into inventory levels, equipment performance, and transportation conditions. This improved visibility allows businesses to proactively address issues, optimize inventory levels, and improve overall supply chain efficiency.
Another technology that can be harnessed is blockchain. Blockchain technology enables secure and transparent record-keeping, ensuring trust and traceability in supply chain transactions. By using blockchain, businesses can reduce the risk of fraud, improve supply chain transparency, and optimize processes such as supplier management and product traceability.
Collaboration tools and platforms are also essential for effective communication and collaboration within the supply chain. Cloud-based platforms and digital communication tools enable real-time information sharing, collaboration, and coordination with suppliers, distributors, and other stakeholders. This improves overall visibility, reduces communication barriers, and enhances supply chain responsiveness.
However, it’s important to note that implementing technology and automation requires careful planning, resource allocation, and change management. Businesses should conduct a thorough cost-benefit analysis and invest in technologies that align with their specific needs and objectives. Additionally, ongoing monitoring and evaluation are crucial to ensure that the technology is delivering the expected benefits and making a positive impact on supply chain costs.
By harnessing technology and automation, businesses can optimize processes, improve visibility, enhance collaboration, and ultimately reduce supply chain costs. Embracing innovative technologies allows businesses to stay competitive and thrive in today’s rapidly evolving business landscape.
Leveraging Strategic Partnerships
Strategic partnerships play a crucial role in reducing supply chain costs and improving overall operational efficiency. By developing strong relationships with key partners, businesses can access specialized expertise, resources, and economies of scale, leading to cost savings and improved performance.
One key strategic partnership is with suppliers. Collaborating closely with suppliers can improve supply chain visibility, reduce lead times, and enhance product quality. By establishing long-term relationships and open communication channels with suppliers, businesses can negotiate favorable pricing, volume discounts, and improved payment terms. This not only reduces procurement costs but also ensures a reliable and high-quality supply of materials or components.
Similarly, partnering with logistics providers can result in significant cost savings. Leveraging the expertise and network of logistics providers can help optimize transportation routes, reduce shipping costs, and improve delivery times. Businesses can also benefit from negotiated rates and access to advanced tracking and monitoring technologies that enhance supply chain visibility and efficiency.
Collaboration with strategic customers is another valuable partnership. By understanding customers’ needs, businesses can align their operations and supply chain processes accordingly. This can result in improved demand forecasting, better inventory management, and reduced product returns. Working closely with customers can also lead to collaborative product development and shared cost-saving initiatives.
Cooperative partnerships with other businesses in the same industry can also yield cost-saving opportunities. By pooling resources, businesses can achieve economies of scale in procurement, transportation, and warehousing. Collaborative efforts such as shared distribution centers or joint purchasing can reduce costs and enhance operational efficiency for all parties involved.
Furthermore, partnerships with technology providers can help businesses leverage innovative tools and solutions to optimize supply chain processes. Technology providers can offer specialized software, analytics platforms, or automation systems that streamline operations and reduce costs. These partnerships enable businesses to access cutting-edge technologies without the need for significant in-house investments.
However, successful strategic partnerships require trust, clear communication, and mutual benefits. Businesses should establish well-defined goals and expectations, aligning strategies and objectives with their partners. They should also regularly assess the performance and value of partnerships, seeking continuous improvement and fostering a collaborative environment.
By leveraging strategic partnerships, businesses can tap into the expertise, resources, and efficiencies of key partners. Collaborating closely with suppliers, logistics providers, customers, and technology providers can lead to cost savings, enhanced operational efficiency, and ultimately, a competitive advantage in the market.
Improving Forecasting and Demand Planning
Accurate forecasting and demand planning are essential for minimizing supply chain costs and optimizing inventory levels. By improving forecasting accuracy, businesses can align their production, procurement, and distribution processes with customer demand, reducing inventory carrying costs and avoiding stockouts.
One key strategy for improving forecasting is to leverage historical data and analyze past trends. By examining patterns, seasonality, and historical sales data, businesses can identify demand patterns and anticipate future demand more accurately. This can be done through statistical forecasting methods, such as time-series analysis or regression models.
In addition to historical data, businesses should also consider external factors that may impact demand, such as market trends, economic indicators, and changes in customer preferences. By considering these factors, businesses can make more informed forecasts and adjust their demand planning accordingly.
Product lifecycle management is another crucial aspect of forecasting and demand planning. By understanding the stage of each product’s lifecycle, businesses can predict demand fluctuations and plan production and inventory levels accordingly. This can help minimize the risk of overstocking or obsolescence.
Collaborating closely with customers and incorporating their input into demand planning can also improve forecasting accuracy. Gathering customer insights, conducting surveys, and analyzing customer behavior can provide valuable information for demand forecasting. Additionally, establishing strategic partnerships and sharing information with key customers can help businesses align their production and inventory with customer demand.
Utilizing forecasting software and demand planning tools can greatly enhance the accuracy and efficiency of the forecasting process. These tools leverage advanced algorithms, machine learning, and statistical models to generate more precise demand forecasts. They can also facilitate collaboration and data sharing across departments, improving overall visibility and coordination in the demand planning process.
Regularly reviewing and updating forecasts based on actual demand performance is crucial. Businesses should compare actual sales data with forecasted numbers and identify any gaps or deviations. This iterative approach allows for continuous improvement and adjustment in demand planning, ensuring optimal inventory levels and minimized costs.
Furthermore, businesses should consider implementing a robust sales and operations planning (S&OP) process. S&OP involves cross-functional collaboration and regular meetings to align sales forecasts, production plans, and inventory strategies. This integrated approach enables businesses to proactively adjust their plans and resources based on changing demand patterns and market conditions.
Improving forecasting and demand planning requires a combination of data analysis, collaborative efforts, and the effective use of technology. By leveraging historical data, considering external factors, collaborating with customers, utilizing forecasting tools, and implementing a strong S&OP process, businesses can optimize inventory levels, reduce costs, and enhance supply chain efficiency.
Enhancing Supplier Management
Effective supplier management is crucial for reducing supply chain costs and ensuring a reliable and efficient flow of materials or components. By enhancing supplier management practices, businesses can optimize procurement processes, reduce lead times, and achieve cost savings.
First and foremost, businesses should establish clear communication channels with their suppliers. Open and regular communication allows for better coordination, prompt issue resolution, and alignment of expectations. This can help reduce misunderstandings, delays, and costly disruptions in the supply chain.
Developing long-term relationships with key suppliers is also essential. Building trust and fostering collaboration can lead to improved pricing, preferential treatment, and better access to critical resources. Long-term partnerships also provide opportunities for joint process improvement initiatives and cost-saving initiatives.
Businesses should regularly evaluate and assess supplier performance. Key performance indicators (KPIs) such as on-time delivery, product quality, and lead times should be monitored closely. Suppliers that consistently perform well can be rewarded with more business or partnership opportunities, while underperforming suppliers may require closer monitoring or reconsideration.
Utilizing supplier scorecards can provide a standardized and objective assessment of supplier performance. Scorecards can include various criteria, such as delivery performance, quality metrics, and responsiveness. By systematically evaluating suppliers, businesses can identify areas for improvement and work collaboratively with suppliers to drive performance enhancements.
Implementing vendor management inventory (VMI) programs can also enhance supplier management. In a VMI arrangement, suppliers are responsible for managing and replenishing inventory at the customer’s location. This can help streamline inventory management, reduce carrying costs, and improve supply chain efficiency.
Negotiating favorable terms and conditions with suppliers is another effective strategy. By assessing supplier pricing, volume discounts, payment terms, and other contractual terms, businesses can secure better pricing and favorable terms. Regular contract reviews and renegotiations can help ensure that the business is benefiting from competitive pricing and advantageous agreements.
Furthermore, businesses should consider diversifying their supplier base. Relying on a single supplier for critical materials or components can pose risks, especially if that supplier experiences disruptions or quality issues. Establishing relationships with multiple suppliers can mitigate risks, improve negotiation power, and provide flexibility in the supply chain.
Finally, businesses should proactively collaborate with suppliers on product innovation and continuous improvement initiatives. By involving suppliers in the early stages of product development, businesses can tap into their expertise and capabilities. This collaboration can lead to cost savings, improved product quality, and enhanced overall supply chain performance.
Enhancing supplier management requires proactive communication, regular evaluation, and strategic collaboration. By establishing strong relationships, monitoring supplier performance, negotiating favorable terms, implementing VMI programs, diversifying the supplier base, and involving suppliers in product development, businesses can optimize procurement, reduce costs, and ensure a reliable supply chain.
Enhancing Data Visibility and Analytics
Data visibility and analytics play a pivotal role in reducing supply chain costs and improving overall operational efficiency. By enhancing data visibility and leveraging analytics, businesses can gain valuable insights, identify areas for improvement, and make data-driven decisions to optimize their supply chain processes.
One key aspect of enhancing data visibility is integrating and centralizing data from various systems and sources. By consolidating data from different departments, such as sales, procurement, inventory, and logistics, businesses can have a holistic view of their supply chain operations. This enables improved data analysis and decision-making.
Implementing a robust data analytics infrastructure is vital for unlocking the potential of data. Advanced analytics tools and technologies, such as artificial intelligence (AI) and machine learning (ML), can analyze large datasets and identify patterns, correlations, and trends. This allows businesses to proactively address supply chain challenges, optimize processes, and identify cost-saving opportunities.
Real-time data visibility is also crucial for agile decision-making. By utilizing real-time dashboards and analytics tools, businesses can monitor key performance indicators (KPIs) and track supply chain metrics in real-time. This enables proactive intervention and quick response to any issues or bottlenecks that may arise in the supply chain.
Data visibility and analytics can also be leveraged for demand forecasting and inventory optimization. By analyzing historical sales data, market trends, and customer behavior, businesses can improve demand forecasts and align inventory levels accordingly. This reduces carrying costs, avoids stockouts, and improves overall inventory management.
Furthermore, data visibility and analytics can be used to identify opportunities for process improvement and cost reduction throughout the supply chain. For example, analyzing transportation data can reveal inefficiencies in routes or carrier performance, allowing for optimization and cost savings. Similarly, analyzing warehouse data can uncover areas for layout optimization or automation implementation, increasing efficiency and reducing costs.
Collaboration and data sharing with suppliers and customers can also enhance data visibility and promote transparency throughout the supply chain. By establishing data-sharing agreements and utilizing collaborative platforms, businesses can gain access to valuable data from external stakeholders. This enables a deeper understanding of customer demand, supplier capabilities, and overall supply chain dynamics.
Continuous monitoring and evaluation of data analytics processes are critical for improvement. Businesses should regularly assess the accuracy and effectiveness of their analytics models and refine them as needed. This ensures that the insights and recommendations derived from the data are reliable and impactful.
Enhancing data visibility and analytics requires investment in technology, data integration, and talent. By centralizing data, leveraging advanced analytics tools, utilizing real-time dashboards, optimizing demand forecasting, and promoting data sharing, businesses can gain greater visibility into their supply chain operations and make well-informed decisions to reduce costs and improve performance.
Reducing Product Returns and Reverse Logistics Costs
Product returns and the associated reverse logistics costs can have a significant impact on supply chain costs. By implementing strategies to reduce product returns and improving reverse logistics processes, businesses can lower expenses, improve customer satisfaction, and enhance overall supply chain efficiency.
One key strategy is to improve product quality and minimize defects. By ensuring that products meet high-quality standards before they are shipped to customers, businesses can reduce the likelihood of returns due to issues such as defects or malfunctions. Implementing quality control measures and conducting thorough inspections can help identify and resolve potential issues earlier in the process.
Offering detailed and accurate product information to customers can help set realistic expectations, reducing the chances of product returns due to misunderstandings or dissatisfaction. Clear and transparent product descriptions, images, and specifications can help customers make informed purchase decisions, resulting in fewer returns.
Efficient and timely customer service can also contribute to reducing product returns. Providing prompt response and resolution to customer inquiries or issues can help address concerns, resolve problems, and potentially prevent returns altogether. Clear communication channels and effective complaint handling processes are essential in ensuring customer satisfaction and minimizing returns.
Implementing a well-designed and user-friendly returns process is crucial. Simplifying the returns process, providing clear instructions, and ensuring ease of return can encourage customers to follow through with returns instead of seeking alternative channels (e.g., reselling or disposal). Streamlined returns processes can also expedite the processing and restocking of returned products, reducing the time and costs associated with reverse logistics.
Effective reverse logistics management is essential for reducing costs associated with product returns. By optimizing the processes for receiving, inspecting, and restocking returned products, businesses can minimize the time and effort required for reverse logistics. Automating these processes and utilizing barcode or RFID technology can improve accuracy, reduce errors, and enhance overall efficiency.
Another strategy for reducing reverse logistics costs is exploring opportunities for refurbishment, repair, or resale of returned products. By evaluating the condition of returned items and determining if they can be refurbished or repaired, businesses can recover value from these products instead of incurring the full cost of replacing or disposing of them. Implementing a robust product disposition strategy can minimize waste and maximize recovery value.
Collaboration with suppliers and logistics partners is crucial for optimizing reverse logistics processes. Establishing clear guidelines and agreements regarding returns, warranties, and disposition processes can improve efficiency, reduce costs, and minimize confusion. Close collaboration enables smoother coordination, timely information sharing, and better management of returned products throughout the supply chain.
Analytics plays a significant role in reducing product returns and reverse logistics costs. By analyzing data on returned items, reasons for returns, and customer feedback, businesses can identify patterns and root causes. This data-driven insight can drive improvements in product design, manufacturing processes, packaging, and overall customer experience.
By implementing strategies to reduce product returns and improving reverse logistics processes, businesses can minimize costs and enhance customer satisfaction. Improving product quality, facilitating an efficient returns process, optimizing reverse logistics management, exploring refurbishment opportunities, and leveraging data analytics are all key components in achieving these objectives.
Conclusion
Reducing supply chain costs is vital for businesses to maintain a competitive edge and improve profitability. By implementing various strategies and best practices, businesses can achieve greater efficiency, optimize processes, and enhance overall supply chain performance.
Analyzing the supply chain provides a foundation for identifying areas for improvement. By mapping out the supply chain, analyzing cost drivers, and understanding the flow of materials and information, businesses can uncover opportunities for cost reduction.
Streamlining inventory management is crucial for minimizing costs. Efficient inventory management practices such as demand-driven approaches, just-in-time inventory, and vendor-managed inventory can result in lower carrying costs, improved order fulfillment rates, and optimized inventory levels.
Optimizing transportation processes can yield significant cost savings. Strategies like consolidation, utilizing alternative transportation modes, optimizing routes, and establishing strategic partnerships with carriers can reduce transportation costs and improve delivery efficiency.
Implementing efficient warehousing strategies, such as layout optimization, automation, and labor management, can result in improved productivity and reduced handling costs.
Harnessing technology and automation enables businesses to streamline processes, enhance data visibility, and make informed decisions to reduce costs and improve operational efficiency.
Leveraging strategic partnerships with suppliers, logistics providers, customers, and technology vendors can result in favorable pricing, improved service levels, and access to specialized expertise, driving down costs and enhancing supply chain performance.
Improving forecasting and demand planning accuracy can lead to optimized inventory levels, reduced carrying costs, and increased customer satisfaction.
Enhancing supplier management practices through clear communication, evaluating supplier performance, negotiating favorable terms, and promoting collaboration can result in cost savings and a reliable supply of materials or components.
Enhancing data visibility and leveraging analytics enables businesses to make data-driven decisions, identify improvement areas, and optimize supply chain processes.
Reducing product returns and effectively managing reverse logistics processes can lower costs and improve customer satisfaction. Strategies such as improving product quality, streamlining returns processes, optimizing reverse logistics operations, and exploring product refurbishment can all contribute to cost reduction.
In conclusion, implementing the right strategies in supply chain management can significantly reduce costs and improve overall efficiency. By continuously analyzing, optimizing, and leveraging partnerships and technology, businesses can achieve a streamlined supply chain that drives profitability and sustained competitive advantage in the market.