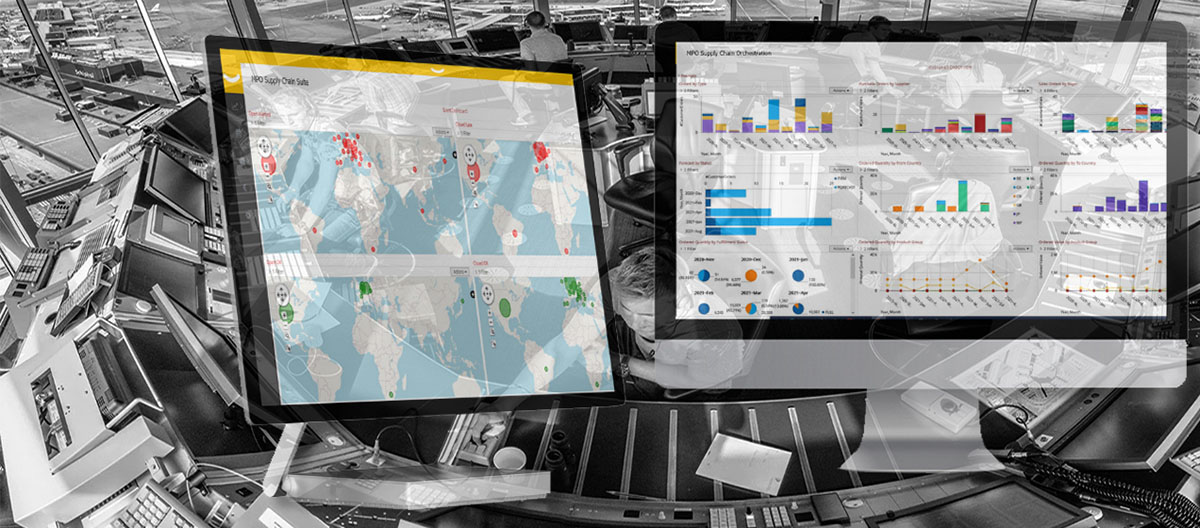
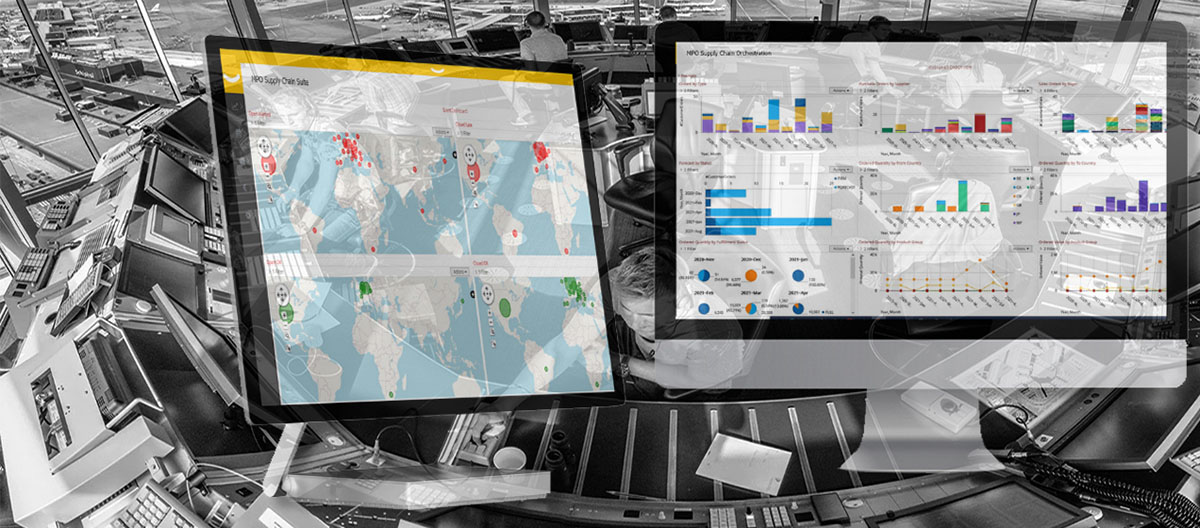
Finance
How To Map A Supply Chain
Published: October 19, 2023
Learn how to map a supply chain and optimize its finance with our comprehensive guide. Increase efficiency and profitability in your business.
(Many of the links in this article redirect to a specific reviewed product. Your purchase of these products through affiliate links helps to generate commission for LiveWell, at no extra cost. Learn more)
Table of Contents
- Introduction
- Understanding Supply Chain Mapping
- Step 1: Identifying the Key Players
- Step 2: Gathering Information
- Step 3: Visualizing the Supply Chain
- Step 4: Analyzing the Supply Chain
- Step 5: Identifying Risks and Weak Points
- Step 6: Developing an Improvement Strategy
- Step 7: Implementing Changes
- Conclusion
Introduction
In today’s complex and interconnected business landscape, understanding the dynamics of a supply chain is crucial for organizations to achieve operational efficiency and mitigate risks. Supply chain mapping is a powerful tool that allows businesses to visualize the flow of goods, services, and information from the source to the end consumer. By identifying key players, analyzing the processes, and identifying potential risks, companies can make informed decisions to optimize their supply chains.
Supply chain mapping provides a holistic view of the entire supply network, enabling organizations to identify bottlenecks, optimize inventory management, reduce costs, and enhance customer satisfaction. It helps businesses identify gaps in communication and collaboration between stakeholders, leading to improved coordination and streamlined processes.
Furthermore, supply chain mapping is essential for identifying potential risks and vulnerabilities in the supply chain. From natural disasters to geopolitical instability, any disruption in the supply chain can have severe consequences for businesses. By visualizing the flow of goods and services, companies can identify weak points and develop strategies to mitigate these risks.
Implementing supply chain mapping requires a systematic approach, starting from identifying the key players and ending with implementing changes and improvements. By following a structured process, organizations can unlock the full potential of their supply chains and gain a competitive advantage in the market.
In this article, we will explore the steps involved in mapping a supply chain, from identifying the key players to developing an improvement strategy. By understanding each step in the process, businesses can effectively optimize their supply chains and drive sustainable growth.
Understanding Supply Chain Mapping
Supply chain mapping is a comprehensive process that involves visualizing and analyzing the flow of goods, services, and information throughout the supply chain. It provides businesses with a clear understanding of how their products or services move from suppliers to customers, highlighting the various touchpoints and interactions along the way.
By mapping the supply chain, organizations can identify inefficiencies, bottlenecks, and potential risks, and devise strategies to optimize operations. It helps businesses understand the dependencies between different stakeholders, such as suppliers, manufacturers, distributors, and retailers, enabling them to foster stronger collaboration and enhance overall supply chain performance.
The primary goal of supply chain mapping is to gain visibility and transparency across the entire supply network. This involves identifying the different players involved, including suppliers, intermediaries, logistic partners, and customers. It is crucial to collect accurate and up-to-date information about each player’s role, location, capabilities, and relationships.
Another aspect of supply chain mapping involves analyzing the processes and activities that occur within the supply chain. This includes understanding the steps involved in procurement, production, transportation, warehousing, and distribution. Through this analysis, businesses can identify areas where improvements can be made, such as reducing lead times or optimizing inventory levels.
Technological advancements have greatly enhanced the ability to map and visualize supply chains. Various software tools and platforms are available that allow businesses to create detailed flowcharts, diagrams, and interactive maps. These tools enable stakeholders to have a bird’s-eye view of the entire supply chain while also being able to zoom in to specific nodes or segments for more detailed analysis.
Supply chain mapping is an ongoing process that requires constant monitoring and updating. As market conditions change, new suppliers emerge, or customer demands evolve, it is important to adapt and refine the supply chain map accordingly. This ensures that businesses stay agile and responsive to changes in the external environment.
By understanding the intricacies of supply chain mapping, businesses can gain valuable insights and make informed decisions to optimize their supply chain operations. With enhanced visibility and collaboration, organizations can drive efficiencies, reduce costs, and better serve their customers.
Step 1: Identifying the Key Players
The first step in mapping a supply chain is to identify the key players involved in the process. This includes all the stakeholders who contribute to the movement of goods, services, and information along the supply chain.
Start by identifying your suppliers, both primary and secondary. Primary suppliers are those who directly provide you with raw materials or components, while secondary suppliers may provide supporting products or services. Gather information about their location, contact details, production capabilities, and lead times.
Next, identify the intermediaries or distributors involved in the supply chain. These are the entities responsible for transporting and storing the products as they move towards the end customer. Understand their roles, geographical coverage, distribution channels, and any value-added services they offer.
Additionally, identify the internal stakeholders within your organization who play a role in the supply chain, such as procurement teams, production planners, warehouse managers, and logistics personnel. These individuals are critical for effective coordination and communication within the supply chain.
Don’t forget to consider your customers as key players in the supply chain. Understanding their needs, preferences, and buying behavior is crucial for aligning your supply chain operations to meet their expectations. Collect data on their location, order patterns, volume requirements, and any specific delivery instructions.
It is also important to consider other external factors that can influence the supply chain, such as regulatory bodies, industry associations, and technology providers. These entities may have an indirect impact on your supply chain operations, so it is important to include them in your mapping process.
While identifying the key players, it is essential to gather accurate and up-to-date information about each entity. This can be done through research, surveys, interviews, or by leveraging existing databases and industry resources. Maintaining open lines of communication with the identified stakeholders is vital for obtaining accurate information and building strong relationships.
By identifying the key players in your supply chain, you lay the foundation for mapping the flow of goods, services, and information. This step provides a comprehensive understanding of the various entities involved and their roles in the supply chain ecosystem. Once you have a clear picture of the key players, you can proceed to the next steps of the supply chain mapping process.
Step 2: Gathering Information
After identifying the key players in your supply chain, the next step is to gather relevant information about each entity. This step involves collecting data on various aspects of the supply chain, including processes, capabilities, and performance metrics.
Start by collecting information about your suppliers. This can include details such as their location, production capacity, quality control processes, lead times, and pricing. Understanding these factors will help you evaluate their suitability as suppliers and make informed decisions about sourcing and supplier partnerships.
Similarly, gather information about your distributors or intermediaries. This can include data on their geographical presence, distribution networks, storage capacity, handling processes, and value-added services they offer. Understanding these details will help you assess their capabilities and align them with your supply chain objectives.
Additionally, gather information about your internal stakeholders who play a role in the supply chain. This can include data on their responsibilities, expertise, communication channels, and decision-making processes. Having a clear understanding of the internal dynamics will enable you to identify areas for improvement and enhance collaboration within your organization.
To gather information about your customers, analyze their purchasing patterns, preferences, and requirements. This can involve market research, surveys, customer interviews, and data from sales and marketing teams. Understanding your customers’ needs will help you align your supply chain operations to deliver a superior customer experience.
Collecting data on external factors that impact the supply chain is also essential. This can include regulatory requirements, industry standards, technological advancements, and market trends. Staying up-to-date with these factors will help you identify risks, optimize processes, and leverage new opportunities.
Gathering information can be done through a variety of methods, depending on the availability and accessibility of data. This can involve conducting interviews with stakeholders, leveraging existing databases and industry reports, analyzing historical data, and utilizing technology tools for data collection and analysis.
Ensure that the data you gather is reliable, accurate, and up-to-date. Regularly review and update the information to adapt to changing market conditions and evolving business needs.
By gathering comprehensive and reliable information about the various entities and factors influencing your supply chain, you gain a solid foundation for analyzing and optimizing the flow of goods, services, and information. This information will help you make informed decisions and develop strategies to enhance the efficiency and effectiveness of your supply chain.
Step 3: Visualizing the Supply Chain
Once you have identified the key players and gathered relevant information, the next step in mapping a supply chain is to visualize the flow of goods, services, and information. By creating a visual representation, you can better understand the interconnectedness and dependencies within the supply chain.
Start by creating a flowchart or diagram that outlines the different stages and processes involved in your supply chain. This can include procurement, production, transportation, warehousing, and distribution. Map out the sequence of activities and the flow of materials and information at each stage.
Include the key players identified in the previous steps in your visualization. Use symbols or icons to represent different entities, such as suppliers, manufacturers, distributors, and customers. Connect the entities based on the flow of goods and information between them.
In addition to mapping the physical flow of goods, it is important to visualize the flow of information along the supply chain. This includes data related to orders, inventory levels, production schedules, and customer demands. Identify the communication channels and systems used to exchange information between different entities.
Consider using technology tools or software platforms to create interactive and dynamic visualizations of your supply chain. These tools can help you zoom in and out, drill down into specific nodes or processes, and simulate different scenarios to assess their impact on the overall supply chain performance.
Visualizing the supply chain enables you to identify bottlenecks, inefficiencies, and potential areas for improvement. It gives you a clear picture of the entire supply network, highlighting the interdependencies and relationships between different entities.
As you build the visualization, seek input and feedback from stakeholders involved in the supply chain. This collaborative approach helps ensure that the visualization accurately represents the actual flow of goods and information within the supply chain.
Regularly update and refine your supply chain visualization as your business evolves and market conditions change. This will help you maintain an accurate and effective representation of your supply chain, which can serve as a valuable tool for decision-making and continuous improvement.
By visualizing your supply chain, you gain a deeper understanding of the interconnections and complexities within the process. It provides a visual roadmap for analyzing and optimizing the flow of goods and information, ultimately leading to improved efficiency, reduced costs, and enhanced customer satisfaction.
Step 4: Analyzing the Supply Chain
Once the supply chain is visualized, the next step is to analyze it in-depth. This involves evaluating the performance of each entity, identifying bottlenecks, and uncovering opportunities for improvement.
Start by examining the data and information collected during the previous steps. Analyze key performance indicators (KPIs) such as lead times, cycle times, on-time delivery rates, inventory turnover, and customer satisfaction levels. This analysis will provide insights into the overall efficiency and effectiveness of the supply chain.
Identify bottlenecks and constraints within the supply chain. These can be points where delays occur, excess inventory builds up, or communication breakdowns happen. By pinpointing these bottlenecks, you can develop targeted strategies to alleviate them and improve overall supply chain performance.
Use analytical tools, such as data visualization and statistical analysis, to uncover patterns, trends, and correlations in the supply chain data. This can help identify areas of improvement, such as reducing costs, optimizing inventory levels, or enhancing production processes.
Segment the supply chain into different categories, such as product lines, customer segments, or geographic regions. Analyze each segment separately to gain a deeper understanding of the unique challenges and opportunities they present. This allows for customized strategies and tailored improvements based on specific segment needs.
Consider conducting a SWOT (Strengths, Weaknesses, Opportunities, and Threats) analysis of your supply chain. This will help you understand the internal strengths and weaknesses of your operations, as well as the external opportunities and threats in the market. Armed with this knowledge, you can develop strategies to capitalize on strengths, address weaknesses, exploit opportunities, and mitigate threats.
Engage stakeholders from different entities within the supply chain in the analysis process. Their input and perspectives can provide valuable insights and help identify areas for improvement that may have been overlooked.
Continuous monitoring and measurement of KPIs are crucial for ongoing analysis of the supply chain. Regularly review the performance metrics and compare them against benchmarks and industry standards. This will help identify deviations and areas requiring immediate attention.
Ultimately, the analysis of the supply chain should provide actionable insights and recommendations for improvement. Develop an improvement plan that outlines specific initiatives, timelines, and responsibilities for implementing changes in the supply chain.
By thoroughly analyzing the supply chain, organizations can identify inefficiencies, optimize processes, and enhance overall performance. The analysis serves as a foundation for implementing targeted improvements and achieving a more efficient and agile supply chain.
Step 5: Identifying Risks and Weak Points
Identifying risks and weak points in the supply chain is a critical step towards building a resilient and robust supply network. By proactively identifying potential disruptions and vulnerabilities, organizations can develop strategies to mitigate risks and strengthen their supply chains.
Start by conducting a comprehensive risk assessment of your supply chain. Consider both internal and external factors that can impact your operations. Internal risks can include issues like equipment breakdowns, capacity constraints, or quality control failures. External risks encompass factors such as natural disasters, geopolitical instability, or economic fluctuations.
Analyze the data collected during the previous steps to identify areas of vulnerability and weaknesses within your supply chain. Look for any gaps in communication, lack of transparency, or dependencies on a limited number of suppliers or transport routes. Understanding these weak points will help you develop strategies to fortify your supply chain.
Consider the impact of potential disruptions on your supply chain and assess their likelihood. Evaluate the severity of each risk and categorize them based on their potential impact. This will enable you to prioritize your risk mitigation efforts and allocate resources effectively.
Engage stakeholders from different entities within the supply chain in the risk identification process. Their knowledge and insights can provide valuable perspectives on potential risks that may be unique to their specific roles or industries.
Once risks are identified, develop strategies to mitigate them. This can include diversifying your supplier base, establishing backup inventory or production facilities, or implementing technology solutions to monitor and address potential disruptions. Explore partnerships or alliances with other organizations to collectively manage shared risks.
Establish clear communication channels and protocols to ensure timely information flow during times of disruption. Implement robust tracking systems that allow for real-time visibility of inventory, shipments, and customer demands. This will help in quickly identifying and responding to any deviations from the normal supply chain operations.
Regularly review and update your risk mitigation strategies as market conditions and business needs evolve. Conduct periodic assessments to identify new risks or changes in the impact and likelihood of existing risks.
By identifying risks and weak points in the supply chain, organizations can proactively address potential disruptions and vulnerabilities. This proactive approach strengthens the resilience and agility of the supply chain, enabling businesses to better navigate challenges and maintain continuity of operations.
Step 6: Developing an Improvement Strategy
Developing an improvement strategy is a crucial step in optimizing the supply chain. Based on the analysis conducted in earlier steps and the identification of risks and weaknesses, organizations can formulate a comprehensive plan to enhance the efficiency, effectiveness, and resilience of their supply chain.
Start by setting clear objectives for the improvement strategy. These objectives can include reducing lead times, improving on-time delivery rates, optimizing inventory levels, enhancing customer satisfaction, or mitigating risks. Ensure that the objectives are aligned with the overall business goals and priorities.
Based on the identified weaknesses, risks, and areas for improvement, define specific initiatives and actions that need to be taken. These can include process reengineering, technology implementation, supplier optimization, or enhancing collaboration and communication with stakeholders.
Segment the improvement strategy into short-term and long-term goals. Short-term goals can address immediate issues and vulnerabilities, while long-term goals focus on strategic transformations and sustainable improvements. This allows for a phased approach to implementation and ensures a balance between quick wins and comprehensive changes.
Assign responsibilities to individuals or teams for each improvement initiative. Clearly define roles and establish accountability for the successful execution of the strategy. Regularly review progress and provide support or resources as needed to ensure smooth implementation.
Consider leveraging technology solutions to streamline and automate processes within the supply chain. This can involve implementing inventory management systems, demand forecasting tools, or supply chain analytics platforms. Technology can greatly enhance the efficiency and visibility of the supply chain, leading to improved decision-making and performance.
Develop performance metrics and KPIs to measure the progress and impact of the improvement strategy. Monitor these metrics regularly to track the effectiveness of the implemented initiatives and identify areas that require further attention or adjustments.
Regularly communicate the improvement strategy and its progress to all stakeholders within the supply chain. Open lines of communication foster transparency, collaboration, and engagement, which are essential for successful change management and the adoption of new processes or technologies.
Continuously evaluate the improvement strategy and adjust it as needed based on changing market conditions, business priorities, and emerging opportunities. Flexibility and adaptability are key to ensuring that the supply chain remains efficient and resilient in the face of evolving challenges.
By developing a well-defined improvement strategy, organizations can enhance the overall performance and competitiveness of their supply chain. This strategic approach enables businesses to implement targeted initiatives, align the supply chain with business goals, and drive continuous improvement.
Step 7: Implementing Changes
The final step in mapping a supply chain is to implement the identified changes and improvements. This step requires effective project management, clear communication, and stakeholder engagement to ensure a smooth transition and successful implementation.
Start by prioritizing the changes based on their impact and feasibility. Determine the sequence of implementation and establish a timeline for each initiative. This helps in managing resources and ensuring a systematic approach to change.
Assign specific responsibilities and roles to individuals or teams for executing each change. Clearly communicate the expectations and objectives to ensure everyone is aligned and committed to the implementation process. Foster a culture of accountability and ownership among the stakeholders involved.
Provide the necessary support and resources required for implementing the changes. This can include allocating funds for technology investments, providing training and education programs, or reallocating personnel to support the transition. Ensure that the resources are properly allocated, and progress is regularly monitored to address any challenges or obstacles encountered during implementation.
During the implementation process, maintain open lines of communication with all stakeholders. Regularly update them on the progress, seek feedback, and address any concerns or questions. Effective communication helps to manage expectations, build trust, and ensure a smooth transition.
Conduct post-implementation reviews to evaluate the impact of the changes and make any necessary adjustments. Measure the performance metrics and KPIs defined earlier in the improvement strategy to assess the effectiveness of the implemented changes. This evaluation allows for continuous improvement and fine-tuning of the supply chain operations.
Document the changes made and document the new processes and procedures. This serves as a reference for future updates or modifications and facilitates knowledge sharing among the team members involved. Consider creating a repository or knowledge management system to store and share relevant documents and information related to the supply chain changes.
Regularly review and update the implementation plan as necessary. The supply chain is a dynamic and ever-changing environment, so it is important to stay agile and responsive to emerging trends, market demands, and new opportunities. Continuously monitor the performance of the implemented changes and explore ways to further optimize the supply chain.
Celebrate successes and recognize the efforts of individuals and teams involved in the implementation process. Positive reinforcement and recognition encourage a culture of continuous improvement and provide motivation to sustain the positive changes made.
By effectively implementing the identified changes, organizations can transform their supply chains to be more efficient, resilient, and customer-centric. This step ensures that the improvements are successfully integrated into the day-to-day operations, leading to long-term sustainability and growth.
Conclusion
Mapping a supply chain is a crucial process for businesses seeking to optimize their operations and gain a competitive advantage in today’s dynamic marketplace. By following the steps outlined in this article – from identifying key players to implementing changes – organizations can improve visibility, efficiency, and resilience throughout their supply chains.
Understanding the interconnectedness and dependencies within a supply chain is vital. By visualizing the flow of goods, services, and information, businesses can identify bottlenecks, weak points, and potential risks. This holistic view enables targeted analysis and the development of strategies to enhance performance and mitigate disruptions.
Through comprehensive data gathering, analysis, and collaboration with stakeholders, organizations can identify areas for improvement. Developing an improvement strategy allows for targeted initiatives, technology implementation, and process enhancements to optimize the supply chain. Regular monitoring and evaluation of key performance indicators ensure ongoing assessment and refinement of the strategy.
Furthermore, actively identifying risks and weak points within the supply chain allows businesses to proactively address vulnerabilities and develop risk mitigation strategies. By staying ahead of potential disruptions, organizations can build resilience and minimize the impact of unforeseen events.
Ultimately, successful supply chain mapping and optimization result in improved customer satisfaction, reduced costs, increased operational efficiency, and better overall business performance. Continuously monitoring market conditions, evolving technologies, and customer demands ensures that the supply chain remains adaptable and responsive to changing circumstances.
In a rapidly changing business landscape, the importance of supply chain mapping cannot be overstated. Organizations that take the time and effort to understand their supply chains, identify areas for improvement, and implement changes will position themselves for long-term success and growth.
By integrating these steps into the supply chain management process, businesses can unlock the true potential of their supply chains and thrive in an increasingly competitive marketplace.