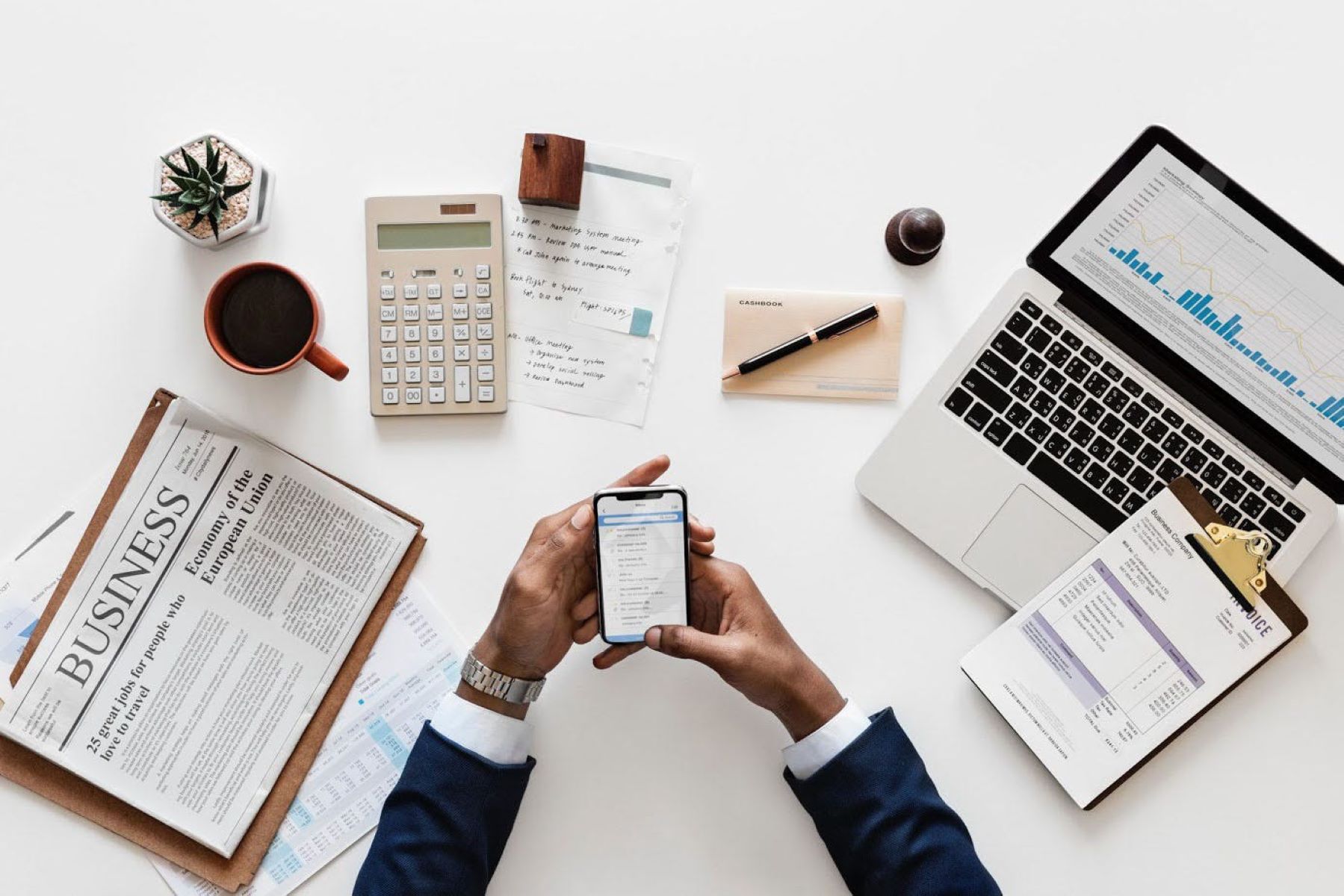
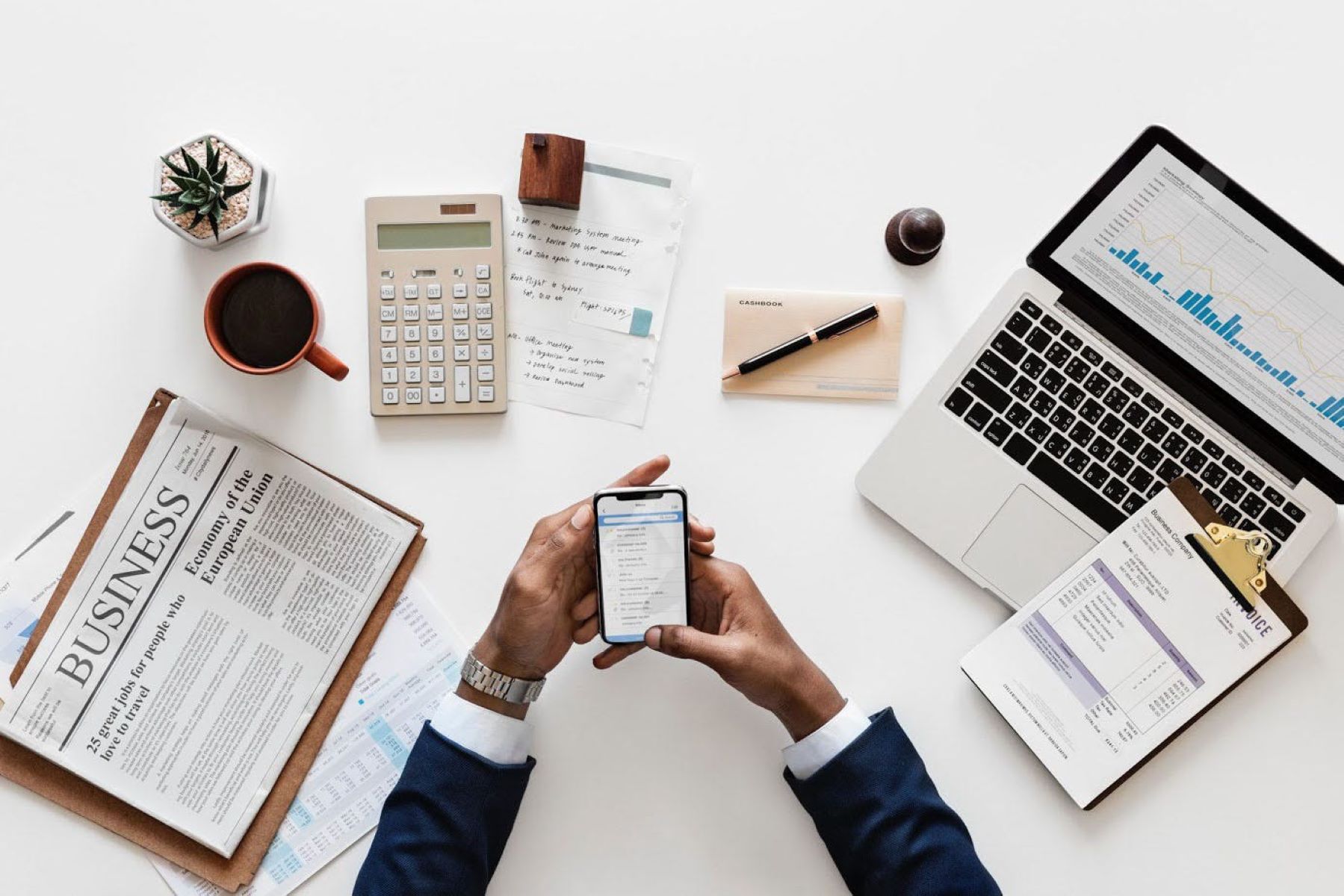
Finance
What Is A Prime Cost In Accounting
Published: October 13, 2023
Discover the essential concept of prime cost in accounting and its significance in financial management. Learn how it influences finance decisions and profitability.
(Many of the links in this article redirect to a specific reviewed product. Your purchase of these products through affiliate links helps to generate commission for LiveWell, at no extra cost. Learn more)
Table of Contents
Introduction
Welcome to the world of accounting! If you’re new to the field or just looking to expand your knowledge, you may have come across the term “prime cost.” This article will guide you through the ins and outs of what prime cost is, its components, and its importance in accounting.
In accounting, prime cost is a fundamental concept that plays a crucial role in determining the cost of producing goods or services. It serves as a basis for calculating the total cost of production and facilitates decision-making processes for businesses.
Understanding prime cost is essential for both accountants and business owners as it helps in evaluating the efficiency of operations, pricing strategies, and overall profitability. Furthermore, it aids in cost control efforts, identifying areas for cost-saving measures, and analyzing the financial health and viability of a company.
So, let’s dive into the fascinating world of prime cost and discover its significance in the realm of accounting.
Definition of Prime Cost
In accounting, prime cost refers to the total direct costs incurred in the production process of a product or service. It encompasses various elements such as direct materials, direct labor, and other direct costs. The prime cost excludes indirect costs, such as overhead expenses and administrative costs, which are allocated separately to determine the total cost of production.
Prime cost is a crucial concept because it represents the core expenses directly associated with creating a product or delivering a service. It allows businesses to understand the cost structure of their operations and make informed decisions regarding pricing, production levels, and budgeting.
To put it simply, prime cost is the sum of all expenses directly attributable to the production process. It is the foundation upon which the total cost of production is built and serves as a vital component in determining the profitability of a business.
It’s important to note that while the prime cost includes direct materials, direct labor, and other direct costs, it does not incorporate indirect costs or expenses such as rent, utilities, marketing, or administrative costs. These indirect costs are factored in separately to calculate the total cost and determine the overall profitability of the product or service.
Now that we have a clear understanding of what prime cost is, let’s delve into its components to gain a deeper insight into how it is calculated and its significance in accounting.
Components of Prime Cost
Prime cost consists of three main components: direct materials, direct labor, and other direct costs. Let’s explore each of these components in detail:
- Direct Materials: Direct materials are the tangible resources that are directly used in the production process. These can include raw materials, components, or any other materials that are essential for the creation of the final product. Examples of direct materials can range from wood and steel in construction to fabric and buttons in garment manufacturing. The cost of direct materials is easily traceable to specific products and can be measured accurately.
- Direct Labor: Direct labor refers to the wages and benefits paid to the employees who are directly involved in the production process. These are the individuals who physically handle the materials and perform the necessary tasks to transform the raw materials into a finished product. Direct labor costs can include hourly wages, overtime pay, and any additional benefits provided to the workers. Tracking direct labor costs is crucial to understanding the labor-intensive aspects of production and assessing the efficiency of the workforce.
- Other Direct Costs: In addition to direct materials and direct labor, there may be other expenses directly attributable to the production process that are included in the prime cost. These costs can vary depending on the nature of the industry and the specific production methods employed. Examples of other direct costs include the cost of energy or utilities used in the production process, equipment maintenance and repair expenses, and any other costs directly related to the production activities. It’s important to note that these costs should be directly traceable to the products or services being produced.
By accounting for these three components, businesses can accurately calculate the prime cost and gain a comprehensive understanding of the direct expenses associated with production. The prime cost serves as a foundation for various decision-making processes, cost analysis, and financial evaluations, making it a fundamental concept in accounting.
Now that we’ve taken a closer look at the components of prime cost, let’s move on to exploring how the prime cost is calculated and why it holds importance in accounting.
Direct Materials
Direct materials are a key component of the prime cost and play a crucial role in the production process. These are the tangible resources that are directly used in creating the final product. Examples of direct materials can include raw materials, components, supplies, or any other materials necessary for the production process.
The cost of direct materials is easily traceable to specific products and is measured accurately. It is essential for businesses to keep track of direct materials costs as they directly impact the overall cost of production and, consequently, the pricing and profitability of the product or service.
Tracking and managing direct materials costs involves various aspects, such as sourcing and procurement, inventory management, and cost control. Here’s a closer look at these aspects:
- Sourcing and Procurement: Businesses must carefully select their suppliers and negotiate favorable terms for acquiring direct materials. This involves assessing the quality, reliability, and pricing of potential suppliers. It’s important to establish strong relationships with suppliers to ensure consistent availability of materials and favorable pricing arrangements.
- Inventory Management: Efficient inventory management is crucial to minimize holding costs and ensure the availability of direct materials when needed. This involves striking a balance between maintaining an adequate stock level to support production without incurring unnecessary storing costs. Implementing inventory management systems and using forecasting techniques can help optimize inventory levels and reduce wastage.
- Cost Control: Controlling direct materials costs is essential to improve overall profitability. This can involve various strategies, such as negotiating better prices with suppliers, seeking alternatives or substitutes for expensive materials, minimizing waste during the production process, and implementing lean manufacturing practices. By monitoring and controlling direct materials costs, businesses can enhance their competitiveness and profitability.
Accurate tracking and management of direct materials costs not only provide insights into the cost structure of the production process but also enable businesses to make informed decisions regarding pricing, cost-saving measures, and budgeting. Understanding the impact of direct materials costs on the prime cost allows businesses to assess the efficiency of their sourcing and production processes and identify areas for improvement.
Direct materials represent a significant portion of the prime cost and have a direct influence on the overall profitability of a product or service. By effectively managing direct materials costs, businesses can enhance their financial performance and maintain a competitive edge in the market.
Now that we’ve explored the importance of direct materials in the prime cost, let’s move on to the next component: direct labor.
Direct Labor
Direct labor is another essential component of the prime cost and refers to the cost of labor directly involved in the production process. It includes the wages, salaries, and benefits paid to the employees who physically handle the materials and perform the tasks necessary to transform raw materials into a finished product.
Direct labor costs are directly traceable to specific products or services and are an important aspect of calculating the overall cost of production. Businesses need to accurately track and allocate direct labor costs to assess the labor-intensive aspects of their operations and evaluate the efficiency of the workforce.
Managing direct labor costs involves several considerations, including:
- Time Tracking: To accurately determine direct labor costs, businesses must track the time spent by employees on specific production activities. This can be done through time-tracking systems, job cards, or other methods that capture the hours dedicated to each product or service.
- Wages and Benefits: Direct labor costs encompass not only the wages or salaries paid to employees but also any additional benefits or incentives provided. These can include overtime pay, commissions, bonuses, health insurance, retirement contributions, and other benefits directly related to the employment of the workforce.
- Labor Efficiency: Analyzing labor efficiency is crucial in understanding the productivity and effectiveness of the workforce. By measuring output per unit of labor, businesses can identify opportunities for improvement, such as training programs, process optimization, or performance incentives.
Effective management of direct labor costs helps businesses optimize their cost structure, improve productivity, and enhance profitability. Some strategies to achieve this include:
- Workforce Planning: Properly analyzing and planning the required workforce can help businesses avoid labor shortages or overstaffing, ensuring optimal utilization of resources.
- Training and Skill Development: Investing in employee training and skill development programs can enhance the efficiency and effectiveness of the workforce, leading to increased productivity and reduced labor costs in the long run.
- Performance Management: Implementing performance management systems and setting clear performance goals can motivate employees to perform at their best and contribute to cost-effective production processes.
By effectively managing direct labor costs, businesses can better understand the labor-intensive aspects of their operations, make informed decisions regarding workforce allocation, and improve overall profitability. It is crucial for businesses to accurately track and allocate direct labor costs in order to have a comprehensive understanding of the prime cost.
Now that we have explored the significance of direct labor in the prime cost, let’s move on to the final component: other direct costs.
Other Direct Costs
Aside from direct materials and direct labor, there are other direct costs that contribute to the overall prime cost. These costs are directly attributable to the production process and can vary based on the nature of the industry and the specific production methods employed.
Other direct costs are the expenses incurred in addition to the cost of direct materials and direct labor. They include various elements such as:
- Energy and Utilities: The cost of energy and utilities necessary for the production process, such as electricity, water, gas, or fuel, is considered an other direct cost. These costs can vary depending on the quantity of energy consumed and the prices set by utility providers.
- Equipment and Machinery: If specific equipment or machinery is required for the production process, the costs associated with their purchase, maintenance, repairs, and depreciation are categorized as other direct costs. This can include machinery rentals, maintenance contracts, spare parts, or any other costs directly related to the operation of the equipment.
- Packaging and Freight: If packaging materials or freight services are directly linked to the production process, their costs are considered other direct costs. This includes the cost of packaging materials, shipping containers, labeling, and transportation services required to move the finished product to the distribution or customer location.
- Direct Overhead: Some expenses, although not directly associated with direct materials or direct labor, can still be categorized as other direct costs. These may include expenses such as specialized tools, specific production software, or any other costs directly related to the production process.
Tracking and managing other direct costs is essential for businesses to have a comprehensive understanding of the prime cost and evaluate the efficiency of their production processes. By closely monitoring and controlling these costs, businesses can identify areas for cost-saving measures and optimize their cost structure.
Effective strategies for managing other direct costs include:
- Supplier Negotiation: Negotiating favorable prices and terms with suppliers of energy, utilities, packaging materials, or freight services can help reduce other direct costs.
- Equipment Maintenance and Efficiency: Regular equipment maintenance and incorporating energy-efficient practices can minimize costs associated with equipment breakdowns, repairs, and energy consumption.
- Process Optimization: Analyzing the production process and identifying opportunities for efficiency improvements can lead to cost reductions in terms of energy usage, waste generation, or resource allocation.
By effectively managing other direct costs, businesses can enhance their cost control efforts, improve overall profitability, and make informed decisions regarding pricing strategies, budget allocation, and resource optimization.
Now that we have explored the components of prime cost in detail, let’s move on to understanding how the prime cost is calculated and its importance in accounting.
Calculation of Prime Cost
The prime cost is calculated by summing up the three main components: direct materials, direct labor, and other direct costs. To calculate the prime cost, follow these steps:
- Direct Materials: Calculate the total cost of direct materials used in the production process. This includes the cost of raw materials, components, or supplies directly attributed to the final product. Add up the individual costs of all direct materials used.
- Direct Labor: Determine the total cost of direct labor by considering the wages, salaries, and benefits paid to employees involved in the production process. This includes the cost of their time dedicated to producing the final product.
- Other Direct Costs: Calculate the total cost of other direct costs as discussed earlier. This includes expenses such as energy and utilities, equipment maintenance, packaging, and freight directly related to the production process.
- Prime Cost Calculation: Add up the costs of direct materials, direct labor, and other direct costs to arrive at the prime cost. The formula for calculating the prime cost can be expressed as:
Prime Cost = Direct Materials + Direct Labor + Other Direct Costs
The prime cost represents the total direct expenses incurred in the production process. It is a crucial figure that allows businesses to evaluate the cost structure, profitability, and efficiency of their operations.
By calculating the prime cost, businesses can gain insights into the cost breakdown of production, identify areas for cost savings, make informed pricing decisions, and allocate resources effectively. It provides a foundation for various financial analyses and facilitates better decision-making in managing costs and maximizing profits.
Now that we understand how to calculate the prime cost, let’s explore the importance of the prime cost in accounting and its comparison to conversion cost.
Importance of Prime Cost in Accounting
The prime cost holds significant importance in the field of accounting as it serves as a foundational concept for several crucial aspects of financial analysis and decision-making. Here are some key reasons why prime cost is important in accounting:
- Cost Analysis: The prime cost allows businesses to analyze and understand the cost structure of their operations. By tracking and evaluating the components of the prime cost, businesses can identify areas of high costs, monitor cost trends, and make informed decisions to improve efficiency and profitability.
- Pricing Strategy: The prime cost plays a crucial role in determining the appropriate pricing strategy for products or services. By accurately calculating the prime cost, businesses can set prices that cover both direct costs and contribute to desired profit margins, ensuring long-term sustainability.
- Profitability Evaluation: Examining the prime cost helps businesses assess the profitability of specific products, services, or even entire operations. By comparing the prime cost with sales revenue, businesses can understand the gross profit margin and evaluate the financial viability of their offerings.
- Cost Control: Monitoring and managing the prime cost allows businesses to implement effective cost control measures. By identifying areas of high direct costs and implementing strategies to reduce those costs, businesses can optimize their operations, improve efficiency, and increase their bottom line.
- Decision Making: The prime cost provides essential information for decision-making processes. By having a clear understanding of the direct costs involved in production, businesses can assess the financial implications of various choices, such as expanding production, introducing new product lines, or outsourcing certain production activities.
- Budgeting: The prime cost serves as a basis for budgeting and forecasting processes. By accurately calculating the prime cost, businesses can establish realistic budgets, allocate resources effectively, and track actual costs against planned costs, enabling better financial control.
- Profit Analysis: Analyzing the prime cost helps businesses analyze their profit margins, both at a product level and overall. By comparing the prime cost with sales revenue, businesses can understand the contribution margin and identify areas for improving profitability.
Overall, the prime cost is a critical element in accounting as it provides key insights into the cost structure, efficiency, and profitability of a business’s operations. By effectively managing and analyzing the prime cost, businesses can make informed decisions, optimize their cost structure, and ultimately achieve long-term financial success.
Now let’s explore the difference between prime cost and conversion cost to gain a better understanding of these related concepts.
Prime Cost vs. Conversion Cost
While prime cost and conversion cost are closely related, they represent different aspects of the cost incurred in the production process. Understanding the difference between these two concepts is essential in the realm of accounting.
Prime Cost: Prime cost, as discussed earlier, refers to the total direct costs involved in producing a product or service. It includes the cost of direct materials, direct labor, and other direct costs. Prime cost focuses on the expenses directly attributable to the production process and serves as a foundation for understanding the cost structure and profitability of a business’s operations.
Conversion Cost: Conversion cost, on the other hand, represents the expenses incurred to convert raw materials into finished goods. It encompasses the cost of direct labor and the cost of overheads directly associated with the production process, such as rent, utilities, depreciation of production equipment, and indirect labor.
The key distinction between prime cost and conversion cost lies in the inclusion of overhead expenses. Prime cost only includes direct costs, while conversion cost includes both direct costs (direct labor) and indirect costs (overhead expenses).
To simplify the difference between prime cost and conversion cost:
- Prime cost includes direct materials, direct labor, and other direct costs.
- Conversion cost includes direct labor and overhead expenses.
- Prime cost focuses on the direct expenses directly related to production.
- Conversion cost encompasses both direct and indirect expenses associated with production.
Both prime cost and conversion cost are essential measures in analyzing the cost structure and profitability of a business. While prime cost provides a more focused view on direct costs, conversion cost provides a broader perspective on the total costs involved in the production process.
Understanding the relationship between prime cost and conversion cost helps businesses make informed decisions regarding pricing, cost control, and resource allocation. It allows for a comprehensive evaluation of the expenses incurred in producing goods or services and aids in maximizing efficiency and profitability.
Now let’s explore the application of prime cost in decision-making processes within the realm of accounting.
Application of Prime Cost in Decision Making
The prime cost plays a vital role in decision-making processes within the realm of accounting. It provides valuable insights into the cost structure of production and helps businesses make informed decisions. Here are some key ways in which prime cost is applied in decision making:
- Pricing Decisions: By understanding the prime cost, businesses can determine the minimum price at which a product or service should be sold to cover the direct expenses incurred in production. This information helps in setting competitive prices while ensuring profitability.
- Product Mix Analysis: Analyzing the prime cost of different products or services allows businesses to identify which offerings are more cost-effective and contribute higher profit margins. This knowledge helps in optimizing the product mix and focusing resources on the most profitable offerings.
- Make or Buy Decisions: For businesses that have the option to produce a component or buy it from an external supplier, calculating the prime cost can aid in evaluating which option is most cost-efficient. This analysis considers the direct expenses involved in production versus the purchase cost from a supplier.
- Cost Reduction Initiatives: By closely monitoring the prime cost, businesses can identify areas of high direct costs and implement cost reduction strategies. These can include improving process efficiency, exploring alternative suppliers, or negotiating better terms with existing suppliers.
- Budget Allocation: Understanding the prime cost allows businesses to allocate resources effectively. By analyzing the direct expenses involved in various production processes, businesses can allocate funds based on the most cost-effective and profitable areas of their operations.
- Profitability Analysis: Comparing the prime cost with sales revenue helps businesses evaluate the profitability of specific products, services, or business segments. This analysis assists in identifying areas that contribute significantly to profits and areas that may require further attention or adjustments.
- Sourcing and Supplier Evaluation: By considering the prime cost, businesses can evaluate suppliers based on the direct expenses they help minimize. This analysis facilitates better supplier selection, negotiation of favorable terms, and cost-effective sourcing decisions.
By utilizing the prime cost in decision-making processes, businesses can make informed choices that positively impact profitability, cost control, and resource allocation. It provides crucial insights into the direct expenses associated with production and helps in optimizing operations for maximum efficiency and financial performance.
Understanding the application of the prime cost empowers businesses to make data-driven decisions, stay competitive in the market, and achieve long-term success.
Now, let’s conclude our discussion on the importance of prime cost in accounting.
Conclusion
The concept of prime cost is a fundamental aspect of accounting that plays a crucial role in understanding the cost structure, profitability, and efficiency of a business’s operations. It encompasses the direct costs incurred in the production process, including direct materials, direct labor, and other direct costs.
Prime cost serves as a foundation for various financial analyses and decision-making processes. By accurately calculating and analyzing the prime cost, businesses can make informed decisions regarding pricing strategies, cost control initiatives, resource allocation, and budgeting.
The components of the prime cost, such as direct materials, direct labor, and other direct costs, allow businesses to assess the efficiency of their sourcing, production, and cost management practices. It helps in identifying areas for cost reduction, improving profitability, and optimizing the allocation of resources.
Furthermore, the prime cost is crucial in evaluating the financial viability of specific products or services, facilitating make or buy decisions, assessing profitability, and evaluating supplier performance.
In summary, the prime cost is a fundamental concept in accounting that provides valuable insights into the direct expenses incurred in the production process. By understanding and effectively managing the prime cost, businesses can enhance their financial performance, make informed decisions, and achieve long-term success.
As you continue your journey in the world of accounting, be sure to keep the concept of prime cost in mind. It will serve as a valuable tool in your financial analysis, cost control efforts, and decision-making processes.