Home>Finance>How Can Supply Chain Professionals Utilize A Supply Chain Strategy To Gain A Competitive Advantage?
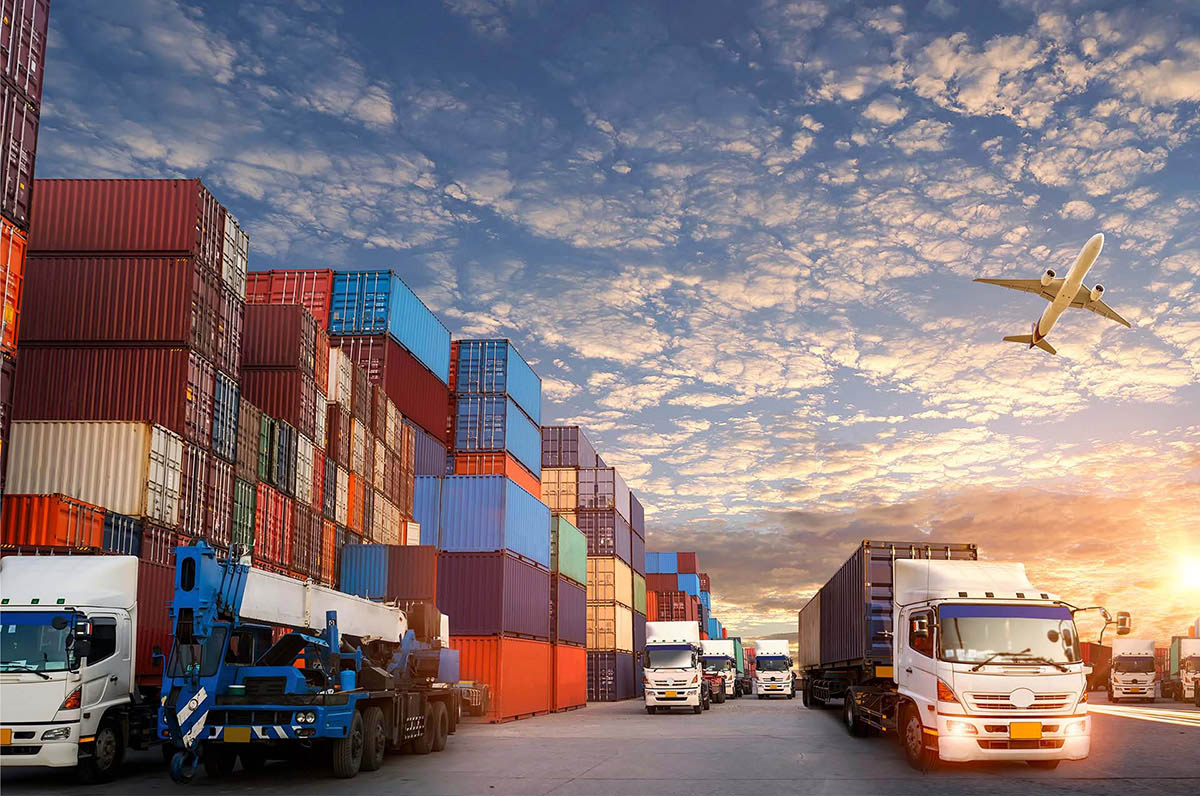
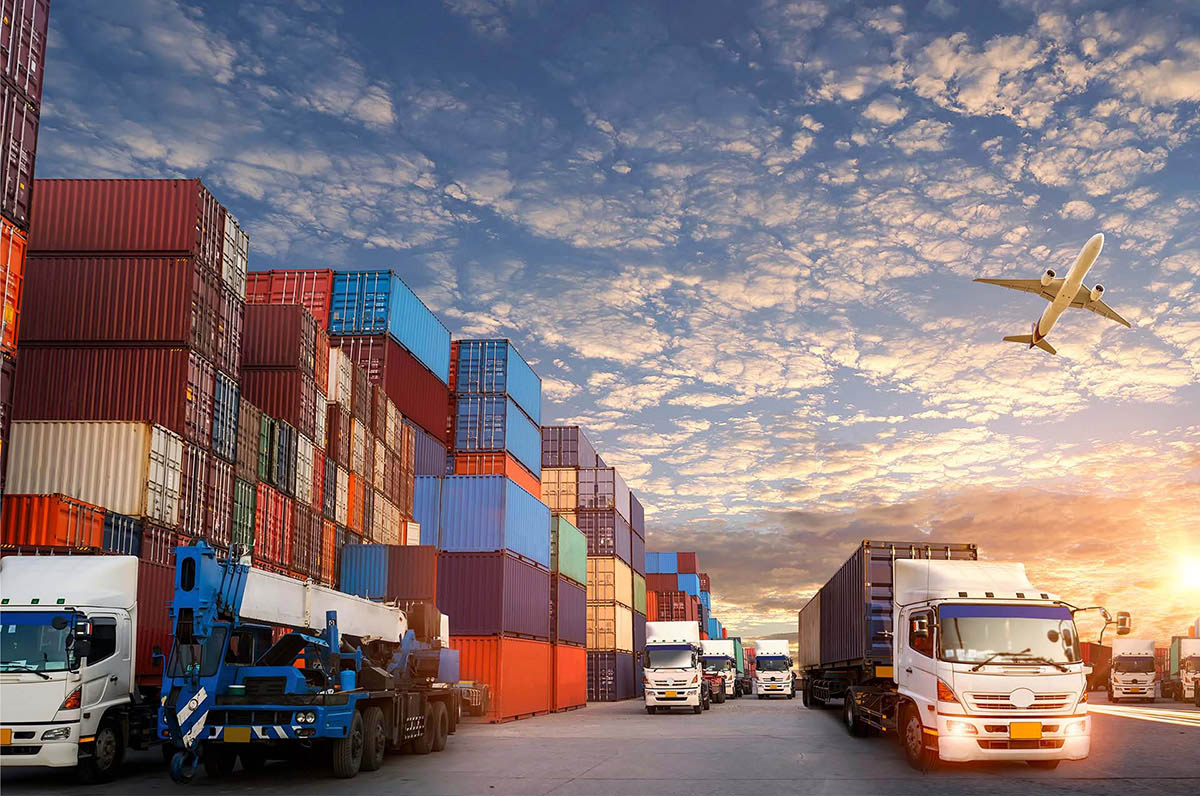
Finance
How Can Supply Chain Professionals Utilize A Supply Chain Strategy To Gain A Competitive Advantage?
Modified: February 21, 2024
Learn how supply chain professionals can leverage a strategic approach to finance in order to gain a competitive edge in the industry.
(Many of the links in this article redirect to a specific reviewed product. Your purchase of these products through affiliate links helps to generate commission for LiveWell, at no extra cost. Learn more)
Table of Contents
- Introduction
- Definition and Importance of Supply Chain Strategy
- Key Elements of a Supply Chain Strategy
- Aligning Supply Chain Strategy with Business Objectives
- Analyzing the Current Supply Chain
- Identifying Areas of Improvement
- Implementing Supply Chain Strategy
- Measuring and Evaluating Performance
- Case Studies: Successful Utilization of Supply Chain Strategy
- Conclusion
Introduction
In today’s highly competitive business landscape, having an efficient and effective supply chain is crucial for organizations to gain a competitive advantage. A well-defined supply chain strategy not only helps streamline operations, but also enables companies to deliver products or services to customers in a timely manner, optimize costs, and achieve customer satisfaction.
A supply chain strategy encompasses a set of plans, actions, and decisions that guide the flow of goods, information, and money from the supplier to the customer. It involves the integration of various processes such as procurement, manufacturing, transportation, warehousing, and distribution. By aligning these processes with business objectives, organizations can optimize their supply chain and achieve a sustainable competitive advantage.
The importance of a robust supply chain strategy cannot be overstated. It enables organizations to anticipate and respond to market demands, reduce lead times, enhance product quality, and improve customer service. Additionally, it helps minimize inventory costs, reduce operational risks, and foster collaboration and coordination with suppliers, partners, and customers.
However, developing and implementing an effective supply chain strategy is not a one-size-fits-all approach. Each organization has its unique goals, challenges, and operational dynamics. Therefore, it is crucial for supply chain professionals to assess their current supply chain, identify areas of improvement, and tailor a strategy that aligns with their specific business objectives.
This article will delve into the key elements of a supply chain strategy and provide insights on how supply chain professionals can leverage it to gain a competitive advantage. We will discuss the process of analyzing the current supply chain, identifying areas of improvement, and implementing the strategy. Furthermore, we will explore the importance of measuring and evaluating supply chain performance and showcase case studies of organizations that have successfully utilized a supply chain strategy to achieve remarkable results.
By understanding the fundamentals of supply chain strategy and its potential impact on overall business performance, supply chain professionals can unlock new growth opportunities, enhance operational efficiency, and stay ahead in today’s dynamic and global marketplace.
Definition and Importance of Supply Chain Strategy
Supply chain strategy refers to a carefully planned approach adopted by organizations to optimize their supply chain processes and achieve competitive advantage. It involves the integration of various activities such as sourcing, procurement, manufacturing, logistics, and distribution to ensure a smooth flow of goods, information, and funds from suppliers to customers.
At its core, supply chain strategy aims to align the overall business objectives with the operational activities of the supply chain. It takes into consideration factors such as customer demands, market trends, industry dynamics, and competitive landscape to create a framework that maximizes efficiency, minimizes costs, and supports the achievement of strategic goals.
The importance of supply chain strategy cannot be understated. It serves as a roadmap that guides decision-making, resource allocation, and process optimization throughout the supply chain. Here are some key reasons why supply chain strategy is vital for organizations:
- Improved Operational Efficiency: An effective supply chain strategy enables organizations to streamline their processes, eliminate bottlenecks, and reduce waste. By optimizing the flow of goods and information, companies can minimize lead times, increase productivity, and enhance overall operational efficiency.
- Cost Optimization: Supply chain costs can have a significant impact on a company’s bottom line. With a well-defined strategy, organizations can identify cost-saving opportunities, negotiate favorable contracts with suppliers, implement efficient inventory management practices, and optimize transportation and logistics to reduce costs and increase profitability.
- Enhanced Customer Satisfaction: By aligning the supply chain strategy with customer demands, organizations can ensure on-time delivery, improve product quality, and provide better customer service. This leads to enhanced customer satisfaction, repeat business, and a strong competitive edge in the market.
- Risk Mitigation: Supply chain disruptions, such as natural disasters, political instability, or supplier failures, can have severe consequences on business operations. A well-designed supply chain strategy includes risk management techniques, such as dual sourcing, contingency planning, and robust supplier relationships, to mitigate potential risks and maintain business continuity.
- Competitive Advantage: A well-executed supply chain strategy can differentiate an organization from its competitors. By optimizing processes, reducing costs, and delivering superior service, companies can gain a competitive advantage that attracts customers, builds brand loyalty, and drives growth.
In summary, supply chain strategy is a critical component for organizations looking to thrive in today’s highly competitive business environment. It enables companies to optimize their operations, reduce costs, enhance customer satisfaction, mitigate risks, and gain a sustainable competitive advantage. By developing and implementing a robust supply chain strategy, organizations can position themselves for long-term success and profitability.
Key Elements of a Supply Chain Strategy
A successful supply chain strategy consists of several key elements that work together to optimize the flow of goods, information, and funds throughout the supply chain. These elements help organizations align their operational activities with their strategic objectives, thereby gaining a competitive advantage. Let’s explore some of the key elements of a robust supply chain strategy:
- Alignment with Business Objectives: A supply chain strategy should be closely aligned with the overall business objectives of the organization. It should support and enable the achievement of strategic goals, whether they are related to cost leadership, differentiation, customer satisfaction, or expansion into new markets. This alignment ensures that the supply chain is a value-added function driving the success of the business.
- Customer Segmentation and Demand Understanding: A supply chain strategy should take into account the different needs and expectations of various customer segments. By understanding customer demands, preferences, and buying behaviors, organizations can tailor their supply chain processes to meet specific requirements. This includes factors such as order fulfillment, delivery speed, product quality, and customer service.
- Supplier Relationship Management: Building strong and collaborative relationships with suppliers is crucial for an effective supply chain strategy. Organizations should evaluate and select reliable and competent suppliers, negotiate favorable contracts, and establish clear communication channels. By working closely with suppliers, organizations can ensure timely and high-quality deliveries of goods and services, as well as facilitate innovation and continuous improvement.
- Inventory Optimization: Managing inventory levels is a critical aspect of supply chain strategy. Organizations need to strike a balance between carrying enough inventory to meet customer demands and minimizing holding costs. Utilizing techniques such as demand forecasting, safety stock planning, and just-in-time inventory management, organizations can optimize inventory levels, reduce costs, and improve operational efficiency.
- Transportation and Logistics: Efficient transportation and logistics play a key role in supply chain strategy. Organizations need to design a transportation network that ensures timely and cost-effective movement of goods from suppliers to customers. This involves selecting appropriate transportation modes, optimizing routes, leveraging technology for tracking and visibility, and collaborating with logistics partners to enhance efficiency and reduce costs.
- Information Systems and Technology: Supply chain strategy relies heavily on information systems and technology to enable effective communication, data sharing, and process integration. Implementing advanced technologies such as warehouse management systems, inventory tracking systems, predictive analytics, and supply chain visibility tools can enhance decision-making, optimize operations, and enable real-time monitoring of key performance indicators.
- Continuous Improvement and Adaptability: A supply chain strategy should never be static. Organizations need to continuously evaluate, refine, and adapt their strategies to keep up with dynamic market conditions, evolving customer demands, and emerging industry trends. By fostering a culture of continuous improvement, organizations can stay agile, identify opportunities for optimization, and proactively respond to challenges and disruptions.
These key elements provide a foundation for developing a robust and agile supply chain strategy. By considering and integrating these elements into their supply chain operations, organizations can optimize processes, reduce costs, improve customer satisfaction, and ultimately gain a competitive advantage in the market.
Aligning Supply Chain Strategy with Business Objectives
Alignment between supply chain strategy and the overall business objectives is crucial for organizations to achieve success and gain a competitive advantage. When the supply chain strategy is tightly integrated with the business objectives, it ensures that all operational activities throughout the supply chain are focused on supporting and driving the desired outcomes. Here are some key considerations to align the supply chain strategy with business objectives:
- Clearly Define Business Objectives: Organizations need to have a clear understanding of their business objectives and translate them into specific supply chain goals. These objectives could be centered around cost reduction, product differentiation, market expansion, customer satisfaction, or sustainability. By defining these objectives, organizations can design a supply chain strategy that directly supports and contributes to the achievement of these goals.
- Collaboration with Key Stakeholders: Successful alignment of the supply chain strategy requires collaboration and involvement of key stakeholders. This includes executives, managers, supply chain professionals, and cross-functional teams from various departments such as sales, marketing, finance, and operations. Engaging stakeholders early on in the strategy development process enables a shared understanding of the business objectives and ensures that everyone is on board with the strategic direction.
- Performance Metrics and KPIs: To measure the effectiveness of the supply chain strategy in achieving business objectives, it is essential to define and track performance metrics and key performance indicators (KPIs). These metrics should be aligned with the overall business goals and provide key insights into the performance of the supply chain. Examples of metrics could include on-time delivery, order fulfillment rate, inventory turnover, customer satisfaction scores, and supply chain costs.
- Integration of Supply Chain Processes: An aligned supply chain strategy requires the integration of various supply chain processes. This involves aligning procurement, production, inventory management, transportation, and distribution activities to ensure seamless flow and coordination. By integrating these processes, organizations can optimize efficiency, reduce costs, and improve overall performance.
- Flexibility and Adaptability: Business objectives may change over time due to market dynamics, customer demands, or industry disruptions. Therefore, supply chain strategies must be flexible and adaptable to accommodate these changes. It is important to regularly evaluate and revise the strategy to ensure that it remains aligned with the evolving business goals.
By aligning the supply chain strategy with the business objectives, organizations can effectively utilize their supply chain as a strategic asset. This alignment ensures that the supply chain functions as a value-added component of the overall business strategy, enabling organizations to optimize costs, improve efficiency, enhance customer satisfaction, and ultimately gain a competitive advantage in the market.
Analyzing the Current Supply Chain
Before implementing any changes or improvements to the supply chain, it is crucial to conduct a thorough analysis of the current supply chain. This analysis provides valuable insights into the existing processes, strengths, weaknesses, and opportunities for improvement. Here are the key steps involved in analyzing the current supply chain:
- Map the Current Supply Chain: Begin by mapping out the current supply chain processes, including all the key activities, stakeholders, and touchpoints involved. This step helps visualize the entire supply chain and understand how different elements interact with one another. It also provides a holistic view of the end-to-end supply chain processes, from sourcing raw materials to delivering finished products to customers.
- Identify Bottlenecks and Inefficiencies: Analyze the current supply chain processes to identify any bottlenecks, inefficiencies, or areas where delays or errors are occurring. Bottlenecks can be caused by factors such as poor inventory management, long lead times, insufficient capacity, or lack of coordination between different departments or suppliers. Pinpointing these bottlenecks is crucial for developing targeted improvement strategies.
- Assess Supplier Relationships: Evaluate the relationships with suppliers to identify any gaps or areas for improvement. Consider factors such as supplier performance, reliability, responsiveness, and innovation. Assess the effectiveness of existing contracts, terms, and negotiations. This analysis helps identify opportunities for optimizing supplier relationships and ensuring a stable and efficient supply of materials or components.
- Review Inventory Management Practices: Evaluate the current inventory management practices and assess their effectiveness. Examine inventory levels, turnover rates, stockouts, and obsolescence. Identify any excess inventory, slow-moving or dead stock, and determine their impact on costs and service levels. This analysis helps identify opportunities for optimizing inventory management, such as implementing just-in-time (JIT) practices or adopting a more demand-driven approach.
- Assess Technology and Systems: Evaluate the technology and systems currently in place for managing the supply chain. Assess the effectiveness of existing software, tools, and information systems for demand forecasting, order processing, inventory management, and logistics. Determine if the current technology is aligned with the business objectives and if any upgrades or integration are necessary to improve efficiency and visibility across the supply chain.
- Evaluate Performance Metrics: Review the performance metrics and key performance indicators (KPIs) being used to measure supply chain performance. Assess if the current metrics align with the business objectives and whether they provide a comprehensive view of performance. Identify any gaps in measurement or areas where additional metrics are needed for better visibility and decision-making.
By conducting a thorough analysis of the current supply chain, organizations can gain a clear understanding of the existing strengths and weaknesses. This analysis provides a foundation for identifying improvement opportunities and developing a targeted strategy to enhance the supply chain’s performance, efficiency, and effectiveness.
Identifying Areas of Improvement
After analyzing the current supply chain and understanding its strengths and weaknesses, the next step is to identify areas of improvement. This step involves pinpointing specific aspects of the supply chain that can be optimized to enhance performance, reduce costs, and meet the strategic objectives of the organization. Here are some key steps to identify areas of improvement:
- Prioritize Improvement Opportunities: Evaluate the findings from the analysis of the current supply chain and prioritize improvement opportunities based on their potential impact and alignment with business objectives. Consider factors such as cost savings, customer satisfaction, time-to-market, risk mitigation, and sustainability. This step helps focus resources and efforts on areas that will yield the greatest benefits.
- Reduce Lead Times: Analyze lead times across the supply chain to identify opportunities for reduction. Look for areas where delays occur, such as in procurement, manufacturing, transportation, or order fulfillment processes. By reducing lead times, organizations can enhance responsiveness, improve customer satisfaction, and gain a competitive edge in fast-paced markets.
- Optimize Inventory Management: Review the findings from the analysis of inventory management practices and identify potential areas for optimization. This could involve implementing techniques such as demand forecasting, safety stock optimization, or vendor-managed inventory. By optimizing inventory levels, organizations can improve cash flow, reduce holding costs, and ensure that the right products are available at the right time.
- Improve Supplier Collaboration: Enhance collaboration and communication with suppliers to drive improvements in the supply chain. Identify opportunities for closer integration, information sharing, and joint planning. Strengthening supplier relationships can lead to benefits such as better pricing, shorter lead times, improved quality, and increased innovation.
- Streamline Processes: Identify any bottlenecks or inefficiencies in the supply chain processes and develop strategies to streamline them. This could involve eliminating redundant or non-value-added activities, improving workflow, or implementing lean manufacturing practices. Streamlining processes improves overall efficiency, reduces wastage, and increases productivity.
- Invest in Technology: Evaluate the technology and systems currently in use and identify opportunities for technological investments to improve supply chain performance. This could include implementing advanced analytics, automation, or supply chain visibility tools. Investing in technology can enhance decision-making, provide real-time data, and facilitate better collaboration within the supply chain ecosystem.
- Enhance Risk Management: Assess potential risks within the supply chain and develop strategies to mitigate them. This could involve diversifying suppliers, creating contingency plans, or establishing robust business continuity processes. By enhancing risk management capabilities, organizations can minimize disruptions and maintain a resilient supply chain.
By identifying areas of improvement, organizations can develop targeted strategies and action plans to enhance the performance, efficiency, and effectiveness of their supply chains. Continuous improvement efforts in these areas will help organizations stay competitive, meet evolving market demands, and achieve their strategic objectives.
Implementing Supply Chain Strategy
Implementing a supply chain strategy involves putting the defined plans and objectives into action. It requires coordination, collaboration, and a systematic approach to ensure a smooth transition from the existing supply chain to the desired state. Here are key steps to successfully implement a supply chain strategy:
- Develop an Implementation Plan: Create a detailed implementation plan that outlines the specific actions, timelines, and responsibilities for each phase of the strategy. This plan should include milestones, key performance indicators (KPIs), and a clear communication strategy to keep stakeholders informed and engaged throughout the process.
- Engage and Empower Employees: Implementing a supply chain strategy requires the active involvement and support of employees at all levels of the organization. Train and educate employees about the new strategy, its goals, and the changes that will be implemented. Empower them to make decisions and provide feedback throughout the implementation process, fostering a culture of ownership and continuous improvement.
- Adopt Change Management Practices: Implementing a new supply chain strategy often involves significant changes in processes, systems, and organizational structure. Apply change management practices to guide employees through the transition. Communicate the rationale for the changes, address concerns and resistance, and provide training and support to ensure a smooth adoption of the new strategy.
- Leverage Technology: Implement technology solutions that support the objectives of the supply chain strategy. This may include implementing new software systems, upgrading existing infrastructure, or leveraging advanced analytics tools. Technology solutions can enhance agility, visibility, and collaboration within the supply chain, improving overall performance and decision-making capabilities.
- Collaborate with Suppliers and Partners: Work closely with suppliers, logistics providers, and other key partners to ensure alignment with the supply chain strategy. Collaborate on initiatives such as demand forecasting, inventory management, and logistics optimization. Foster strong relationships and open lines of communication to drive mutual benefits and continuous improvement.
- Monitor and Adjust: Continuously monitor key performance indicators (KPIs) and metrics to assess the progress of the supply chain strategy. Regularly review performance against the defined objectives and take corrective actions as needed. Stay agile and flexible, adjusting the strategy as market conditions, customer demands, or business priorities evolve.
- Communicate and Celebrate Success: Communicate the achievements and successes resulting from the implementation of the supply chain strategy. Recognize and celebrate milestones and key accomplishments. Share success stories and lessons learned throughout the organization to reinforce the importance of the supply chain strategy and motivate employees to sustain and build upon the progress.
Implementing a supply chain strategy requires a coordinated effort, commitment, and a disciplined approach. By following these key steps and continuously monitoring and adjusting the strategy, organizations can optimize their supply chain operations, enhance efficiency, and gain a competitive advantage in the market.
Measuring and Evaluating Performance
Measuring and evaluating the performance of the supply chain is crucial to ensure that the implemented strategies and improvements are effectively driving the desired outcomes. It allows organizations to assess the effectiveness of their supply chain operations, identify areas for further improvement, and make informed decisions. Here are key steps to effectively measure and evaluate supply chain performance:
- Set Clear Performance Metrics: Define and establish clear performance metrics and key performance indicators (KPIs) that align with the objectives of the supply chain strategy. These metrics may include on-time delivery, order fulfillment rate, inventory turnover, customer satisfaction scores, and supply chain costs. Clear and measurable metrics provide a basis for evaluating performance and tracking progress.
- Collect Accurate and Relevant Data: Ensure the collection of accurate and relevant data for measuring performance. This may involve implementing data collection systems, leveraging technology for real-time data, and ensuring data integrity and consistency. The data should cover all relevant aspects of the supply chain, including procurement, production, logistics, and customer service.
- Analyze Key Performance Indicators: Analyze the collected data and key performance indicators on a regular basis to assess performance trends and identify areas of strength or weakness. Use data visualization tools and techniques to gain insights into the performance of the supply chain. This analysis allows for informed decision-making and the identification of improvement opportunities.
- Benchmark Performance: Compare the supply chain’s performance against industry benchmarks or best practices to gain a broader perspective. Benchmarking helps in understanding the relative performance of the supply chain and identifying areas where improvement is required. It provides an opportunity to learn from industry leaders and adopt best-in-class practices.
- Implement Continuous Improvement Initiatives: Based on the performance analysis, develop and implement continuous improvement initiatives to address identified gaps or opportunities. This may involve process optimization, technology upgrades, supplier development programs, or employee training. Continuous improvement ensures that the supply chain remains agile, adaptable, and able to meet evolving demands.
- Engage Stakeholders: Involve key stakeholders, including supply chain professionals, executives, and departmental leaders, in the measurement and evaluation process. Collaborate with them to review performance results, discuss improvement opportunities, and align on action plans. Engaging stakeholders fosters a sense of ownership, promotes accountability, and increases the likelihood of successful improvement initiatives.
- Track and Communicate Results: Continuously track and communicate the results of the performance evaluation to relevant stakeholders. Regularly share performance reports, dashboards, or scorecards to keep stakeholders informed about the progress and impact of the implemented strategies. Transparent communication fosters trust, accountability, and collaboration within the organization.
Measuring and evaluating supply chain performance provides organizations with valuable insights to drive continuous improvement. By setting clear metrics, analyzing data, benchmarking against industry standards, and engaging stakeholders, organizations can identify areas for optimization, make informed decisions, and enhance the overall effectiveness and efficiency of their supply chain operations.
Case Studies: Successful Utilization of Supply Chain Strategy
Examining real-world examples of organizations that have successfully utilized supply chain strategies can provide valuable insights and inspiration for others looking to optimize their own supply chain operations. Here are a few case studies highlighting the successful utilization of supply chain strategies:
- Amazon: Amazon, the multinational e-commerce giant, has built its success upon a robust supply chain strategy. The company has implemented innovative practices such as predictive analytics and demand forecasting to optimize inventory management and ensure fast and reliable deliveries. Their emphasis on efficient warehousing, advanced fulfillment systems, and strong partnerships with suppliers and logistics providers has resulted in increased customer satisfaction and a competitive advantage in the market.
- Zara: Zara, the Spanish fast-fashion retailer, is renowned for its agile and responsive supply chain strategy. The company leverages real-time sales data and customer feedback to quickly identify trends and adjust production accordingly. Their strategy focuses on short lead times, rapid replenishment, and close collaboration with suppliers and manufacturers. This enables Zara to introduce new fashion collections frequently, quickly adapt to changing customer preferences, and stay ahead of competitors in the fast-paced fashion industry.
- Procter & Gamble: Procter & Gamble (P&G), a global consumer goods company, implemented a sustainable supply chain strategy called “Supplier Environmental Sustainability Scorecard.” This initiative aimed to reduce carbon emissions and promote eco-friendly practices within P&G’s supply chain. By collaborating with suppliers and setting environmental performance targets, P&G was successful in reducing greenhouse gas emissions, decreasing waste, and improving sustainability throughout their supply chain.
- Apple: Apple, the tech giant, is known for its meticulous supply chain management. The company has implemented a vertically-integrated supply chain strategy, which involves close control over manufacturing, component sourcing, and distribution. By tightly managing their supply chain and maintaining strong relationships with suppliers, Apple has achieved high-quality products, efficient production processes, and streamlined logistics, contributing to their success in delivering innovative and desirable consumer electronics.
- Toyota: Toyota, the automotive manufacturer, is recognized for its lean supply chain strategy. The company focuses on reducing waste, increasing efficiency, and continuous improvement throughout their supply chain. Toyota employs just-in-time (JIT) inventory management to minimize inventory carrying costs and optimize production. By implementing lean principles, Toyota has been able to achieve shorter lead times, reduce costs, and enhance customer satisfaction.
These case studies demonstrate that a well-executed supply chain strategy can yield significant benefits for organizations across various industries. Whether it’s through leveraging technology, optimizing inventory, adopting sustainable practices, staying agile, or maintaining control over the supply chain, these companies have successfully utilized their supply chain strategies to gain a competitive edge, enhance operational efficiency, and deliver superior value to their customers.
Conclusion
A well-defined and effectively implemented supply chain strategy is critical for organizations to gain a competitive advantage in today’s dynamic business environment. By aligning the supply chain strategy with the overall business objectives, organizations can optimize their operations, reduce costs, enhance customer satisfaction, and drive sustainable growth.
Throughout this article, we have explored the key elements of a successful supply chain strategy, including aligning it with business objectives, analyzing the current supply chain, identifying areas of improvement, implementing the strategy, and measuring and evaluating performance. Each of these steps plays a crucial role in optimizing supply chain operations and achieving desired outcomes.
We have also examined case studies of organizations like Amazon, Zara, Procter & Gamble, Apple, and Toyota, which have effectively utilized supply chain strategies to drive business success. These examples showcase how a well-executed supply chain strategy can lead to improvements in customer satisfaction, operational efficiency, product quality, sustainability, and competitive advantage.
It is essential for organizations to continuously monitor and assess supply chain performance, adapting and refining the strategy as needed. By regularly measuring key performance indicators and benchmarking against industry standards, organizations can identify areas for improvement and implement continuous improvement initiatives.
In summary, a well-designed and properly executed supply chain strategy is a powerful tool that can enable organizations to optimize their operations, reduce costs, improve customer satisfaction, mitigate risks, and gain a competitive advantage. By leveraging the key elements of supply chain strategy and learning from successful case studies, organizations can position themselves for long-term success and growth in today’s challenging business landscape.