Home>Finance>What Is The Downside Of A Reverse Supply Chain System?
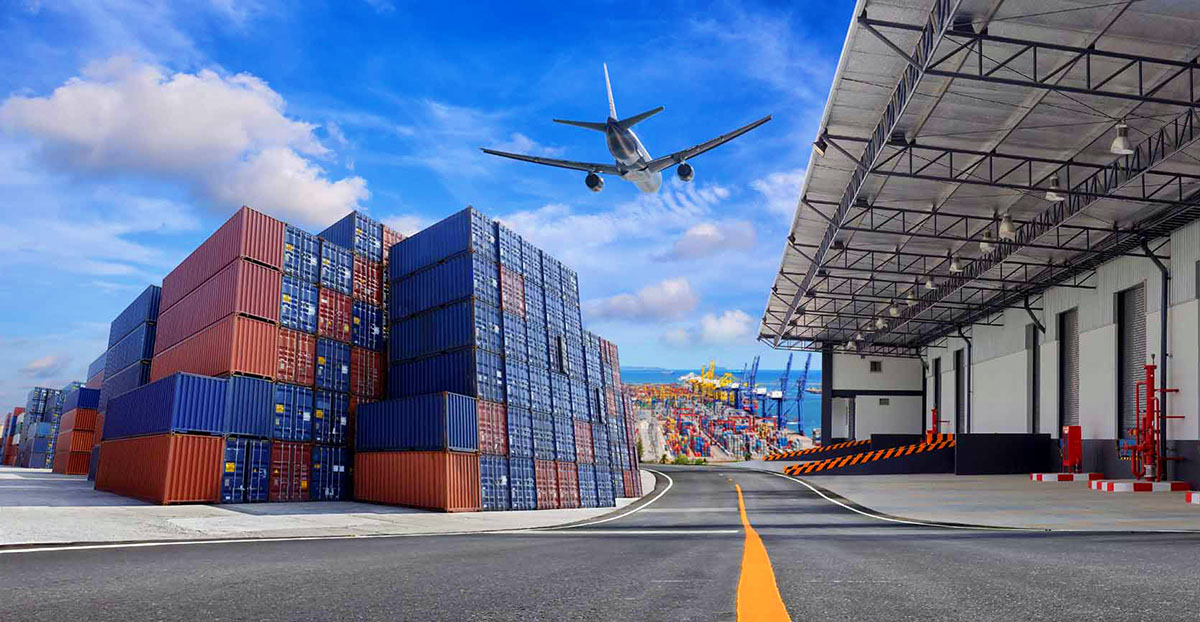
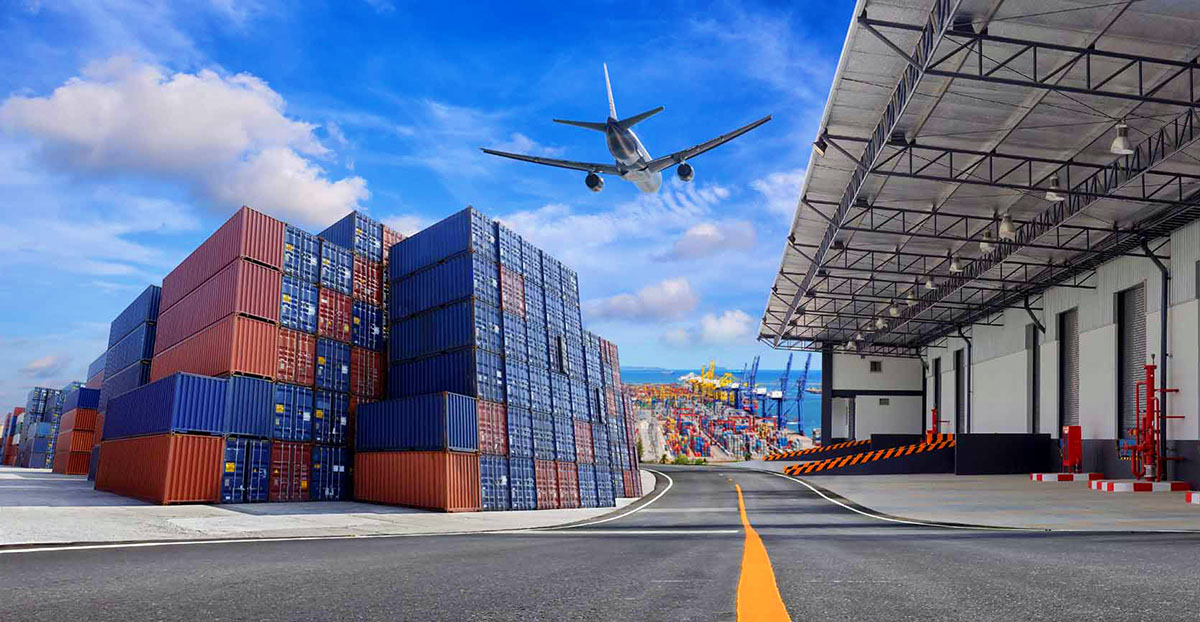
Finance
What Is The Downside Of A Reverse Supply Chain System?
Published: October 20, 2023
Learn about the potential drawbacks of implementing a reverse supply chain system in your finance operations. Find out how it can impact your bottom line and overall efficiency.
(Many of the links in this article redirect to a specific reviewed product. Your purchase of these products through affiliate links helps to generate commission for LiveWell, at no extra cost. Learn more)
Table of Contents
- Introduction
- Definition of a Reverse Supply Chain System
- Benefits of a Reverse Supply Chain System
- The Downside of a Reverse Supply Chain System
- Increased Complexity
- Higher Operational Costs
- Difficulty in Managing Multiple Stakeholders
- Risk of Product Contamination or Counterfeit Items
- Environmental Impact
- Conclusion
Introduction
A reverse supply chain system is a strategic process that manages the flow of goods and materials in the opposite direction of a traditional supply chain. While a traditional supply chain focuses on the movement of products from the manufacturer to the end consumer, a reverse supply chain system deals with the return, recycling, or disposal of products after they have been used by the consumer.
This system has gained significant attention in recent years due to its potential to reduce waste, improve sustainability, and create a circular economy. By implementing a reverse supply chain system, companies can recover value from returned products, minimize their environmental impact, and meet customer demands for responsible business practices.
Reverse supply chain management involves several key processes, including product returns, repairs and refurbishment, recycling, remanufacturing, and disposal. The goal is to optimize the entire lifecycle of a product and extract as much value as possible from its post-consumer phase.
While a reverse supply chain system offers numerous benefits, it is important to note that it also comes with its downsides. Companies must carefully consider these drawbacks and devise strategies to mitigate their impact. In this article, we will explore the downside of a reverse supply chain system and how companies can effectively address these challenges.
Definition of a Reverse Supply Chain System
A reverse supply chain system refers to the management and coordination of activities involved in the movement of products, materials, and information in a direction opposite to that of a traditional supply chain. While a traditional supply chain focuses on delivering products from the manufacturer to the end consumer, a reverse supply chain system deals with the reverse flow of goods.
This system encompasses various processes, such as product returns, repairs, recycling, remanufacturing, and disposal. It aims to optimize the value recovery and minimize the environmental impact of products after they have been used by consumers. A reverse supply chain system typically involves multiple stakeholders, including customers, retailers, manufacturers, logistics providers, and recycling facilities.
One of the key components of a reverse supply chain system is the product return process. This involves the handling and processing of returned products, including determining the reason for return, inspecting the condition of the items, and deciding on appropriate actions such as refurbishment, repair, or recycling. Companies must establish efficient reverse logistics processes to facilitate the smooth flow of returned products back into the supply chain.
In addition to the product return process, a reverse supply chain system also focuses on recycling and remanufacturing. Recycling involves the extraction of valuable materials from returned products for reuse in the production of new products. Remanufacturing, on the other hand, involves the disassembly, repair, and reassembly of returned products to extend their lifecycle and create a secondary market for refurbished items.
Overall, a reverse supply chain system aims to create a closed-loop system where resources are conserved, waste is minimized, and value is recovered from post-consumer products. It is an integral part of sustainable business practices and aligns with the principles of a circular economy.
Benefits of a Reverse Supply Chain System
A reverse supply chain system offers several benefits for companies and the environment. By implementing effective reverse logistics processes and incorporating sustainable practices, businesses can unlock the following advantages:
-
Cost Savings: One of the primary benefits of a reverse supply chain system is the potential for cost savings. By efficiently managing product returns, companies can reduce the financial impact of returned or defective items. They can also recover value from returned products through refurbishment, remanufacturing, or resale, thus generating additional revenue.
-
Sustainable Practices: Adopting a reverse supply chain system enables companies to embrace sustainable business practices. By reusing, recycling, and refurbishing products, they can minimize waste generation and reduce their environmental footprint. This not only contributes to a cleaner and greener environment but also enhances the company’s reputation as a socially responsible organization.
-
Customer Loyalty: Implementing an efficient reverse supply chain system can boost customer satisfaction and loyalty. By providing a hassle-free product return process and offering options for repair, replacement, or refund, companies can enhance the overall customer experience. This, in turn, strengthens customer loyalty and encourages repeat purchases.
-
Improved Inventory Management: A well-designed reverse supply chain system allows companies to gain better visibility and control over their inventory. By analyzing the reasons for product returns, businesses can identify patterns and address underlying issues, leading to improved product quality, reduced returns, and optimized inventory levels.
-
Circular Economy: Implementing a reverse supply chain system aligns with the principles of a circular economy, which aims to minimize waste and promote resource efficiency. By diverting products from landfills and incorporating them back into the supply chain through recycling or remanufacturing, companies contribute to the creation of a more sustainable and circular economy.
These benefits highlight the significance of a reverse supply chain system in driving financial and environmental sustainability. By effectively managing the reverse flow of products, companies can unlock new opportunities, reduce costs, and make a positive impact on the environment.
The Downside of a Reverse Supply Chain System
While a reverse supply chain system offers numerous benefits, it is essential to acknowledge the potential downsides and challenges associated with its implementation. Companies must be aware of these drawbacks to effectively address them and mitigate their impact. The primary downsides of a reverse supply chain system include:
-
Increased Complexity: Managing the reverse flow of products adds complexity to the supply chain. Reverse logistics processes involve multiple steps, such as product inspection, refurbishment, and disposal, requiring careful coordination and efficient handling. The complexity can be further amplified when dealing with different types of products, varying return reasons, and managing multiple stakeholders in the reverse supply chain.
-
Higher Operational Costs: Implementing a reverse supply chain system can lead to higher operational costs. The processes involved, such as product inspection, testing, and refurbishment, require additional resources and manpower. Reverse logistics also involve transportation, storage, and disposal expenses, adding to the overall operational costs for companies.
-
Difficulty in Managing Multiple Stakeholders: A reverse supply chain system involves collaboration among various stakeholders, including customers, retailers, manufacturers, and recycling facilities. Coordinating and aligning the efforts of these stakeholders can be challenging, especially considering different priorities, systems, and communication channels. Efficient communication and collaboration are critical to ensure a smooth reverse supply chain process.
-
Risk of Product Contamination or Counterfeit Items: When products are returned, there is a risk of receiving contaminated or counterfeit items. This poses a challenge for companies in terms of product quality control and consumer safety. It requires robust inspection and testing processes to ensure that returned products are genuine and meet the required standards.
-
Environmental Impact: While a reverse supply chain system aims to reduce waste and promote sustainability, there are still environmental considerations. Transportation of returned products, especially over long distances, contributes to carbon emissions and energy consumption. Companies must balance the environmental benefits of recycling and remanufacturing with the potential downsides of transportation and energy usage.
It is important for companies to carefully analyze these challenges and develop strategies to mitigate their impact on the reverse supply chain system. This may involve leveraging technology for improved communication and visibility, optimizing processes to reduce complexity and costs, and establishing stringent quality control measures to ensure product authenticity and safety.
Ultimately, by addressing these downsides, companies can harness the full potential of a reverse supply chain system and reap the benefits of increased sustainability, cost savings, and customer loyalty.
Increased Complexity
One of the downsides of a reverse supply chain system is the increased complexity it brings to the overall supply chain management. Managing the reverse flow of products requires careful coordination and efficient handling of various processes, including product inspection, refurbishment, and disposal.
Firstly, the complexity arises from the need to accurately and efficiently handle returned products. Each returned item must be inspected to determine its condition and the reason for return. This process can be time-consuming and labor-intensive, especially when dealing with a large volume of returns. Companies need to establish robust processes and utilize technology to streamline the inspection and sorting of returned products.
Additionally, the reverse supply chain system may involve different types of products, each requiring specific handling and processing methods. For example, perishable goods may have a shorter timeframe for inspection and disposal, while electronic products may require thorough testing and potential refurbishment. Managing this complexity requires specialized knowledge and expertise in handling diverse product categories.
Furthermore, the complexity is compounded by the involvement of multiple stakeholders in the reverse supply chain. Collaboration among customers, retailers, manufacturers, and recycling facilities is crucial to ensure smooth operations. However, each stakeholder may have different priorities, systems, and communication channels, making it challenging to align efforts and coordinate activities effectively. Clear and efficient communication, as well as the use of technology platforms that enable collaboration, are essential to mitigate the complexity introduced by multiple stakeholders.
To address the increased complexity, companies can implement advanced technologies such as barcode or RFID tracking systems to improve visibility and traceability of returned products. Automating certain processes, such as product inspection or sorting, can also help streamline operations and reduce manual errors. Moreover, investing in training programs to enhance employees’ skills and knowledge in reverse supply chain management can improve the efficiency and effectiveness of handling returned products.
By proactively addressing the complexities of a reverse supply chain system, companies can ensure smoother operations, minimize process bottlenecks, and optimize resource utilization. This, in turn, leads to improved customer satisfaction, reduced costs, and increased overall efficiency within the reverse supply chain.
Higher Operational Costs
Implementing a reverse supply chain system can lead to higher operational costs for companies. While the system offers various benefits, it requires additional resources and investments to handle the reverse flow of products efficiently.
Firstly, managing product returns involves various activities such as inspection, sorting, and processing. Companies need to allocate additional labor and time for these operations, increasing their overall operational costs. This includes investing in trained personnel who can properly handle returned items, conduct inspections, and make decisions regarding product disposition.
In addition to labor costs, there are expenses associated with transportation and storage. Returning items from various locations back to the appropriate processing centers or facilities can be costly, especially when dealing with a large volume of returns. Moreover, companies need to ensure proper storage facilities for returned items, which can require additional warehouse space and incur extra costs.
Furthermore, the reverse supply chain system may require specialized equipment or technology to handle specific product categories. For example, electronic devices may require diagnostic tools or testing equipment for assessment and refurbishment. Investing in such equipment adds to the operational costs and requires ongoing maintenance and updates to remain effective.
It is important for companies to carefully evaluate the potential return on investment (ROI) in implementing a reverse supply chain system. While the operational costs may increase initially, there are opportunities to recover value from returned products through refurbishment, remanufacturing, or resale. By effectively managing the reverse flow of products, companies can generate additional revenue and offset some of the operational costs.
To minimize the impact of higher operational costs, companies can focus on optimizing the reverse logistics processes. This includes identifying cost-effective transportation options, streamlining product inspection and sorting procedures to minimize labor and time, and leveraging technology to improve overall efficiency. Collaborating with third-party logistics providers or recycling facilities can also help reduce costs by utilizing their specialized expertise and infrastructure.
By carefully managing and controlling operational costs, companies can effectively balance the benefits and expenses associated with a reverse supply chain system. Through efficient cost management and value recovery, businesses can still achieve long-term financial viability while embracing the environmental and customer satisfaction advantages provided by the reverse supply chain.
Difficulty in Managing Multiple Stakeholders
A significant challenge in implementing a reverse supply chain system is the complexity of managing multiple stakeholders involved in the process. Collaborating and aligning efforts among customers, retailers, manufacturers, and recycling facilities can be a daunting task, as each stakeholder has different priorities, systems, and communication channels.
Firstly, customers play a crucial role in the reverse supply chain system as they initiate product returns. However, customers may have different expectations, return policies, and methods of communicating their return requests. Managing and responding to various return scenarios requires effective communication channels and the ability to adapt to diverse customer needs.
Additionally, retailers serve as the intermediaries between customers and manufacturers. They are responsible for accepting returned products from customers, conducting initial inspections, and forwarding the items to the appropriate processing centers or facilities. Coordinating with retailers to ensure smooth and timely return processes is essential to avoid delays or miscommunication.
Manufacturers are another key stakeholder in the reverse supply chain system. They must be able to effectively handle returned products, determine the appropriate actions (such as refurbishment, repair, or disposal), and communicate with customers and retailers regarding the resolution. Aligning manufacturer processes with the expectations of customers and retailers can be challenging, as they may have different priorities and operational procedures.
Lastly, recycling facilities or third-party logistics providers may be involved in the handling and processing of returned products, especially for recycling or disposal purposes. Collaborating with these stakeholders adds another layer of complexity, as the requirements and capabilities of recycling facilities may differ based on the products being returned.
To address the difficulty in managing multiple stakeholders, clear and efficient communication channels are essential. Implementing a centralized system or platform that allows all stakeholders to access and exchange information can streamline the communication process. This helps ensure that everyone involved is aware of the necessary details, such as product condition, return reason, and next steps in the reverse supply chain process.
Furthermore, establishing clear roles and responsibilities for each stakeholder can improve coordination and minimize potential conflicts. Regular communication and feedback sessions can foster collaboration and address any issues or concerns that arise during the reverse supply chain process.
By effectively managing multiple stakeholders, companies can enhance the efficiency and effectiveness of their reverse supply chain system. Collaboration, open communication, and alignment of processes contribute to improved customer satisfaction, streamlined operations, and successful implementation of sustainable business practices.
Risk of Product Contamination or Counterfeit Items
One of the downsides of a reverse supply chain system is the risk of product contamination or counterfeit items entering the supply chain. When handling returned products, there is always a possibility of receiving items that are unsuitable for resale due to contamination or being counterfeit.
Product contamination can occur when returned items have been damaged, mishandled, or exposed to potentially harmful substances during their use by the consumer. This includes products that may have expired, been tampered with, or have been contaminated with hazardous materials. If not properly identified and separated, these contaminated items can pose risks to both the company and the end consumers.
The risk of counterfeit items being reintroduced into the supply chain is another concern. Counterfeit products are replicas of genuine products, often made with inferior materials and quality. They can be challenging to detect, and if they enter the reverse supply chain, they may find their way back into the market as refurbished or resold items. This can damage the reputation of a company and compromise consumer trust in their products.
To minimize the risk of product contamination or counterfeit items, companies must establish robust inspection and testing processes. These processes should include thorough examination of returned products to check for any damage, signs of tampering, or expiration. Implementing quality control measures, such as scientific testing or inspections by trained professionals, can help identify any potential health hazards or counterfeit items.
Utilizing technology solutions, such as barcode scanning or serial number verification, can also aid in identifying counterfeit items and ensuring the authenticity of returned products. By tracking and tracing product information, companies can verify the origin and history of returned items, reducing the risk of counterfeit products being reintroduced into the supply chain.
Additionally, collaborating with trusted partners, such as authorized service centers or recycling facilities with established protocols for handling returned products, can help mitigate the risk of contamination or counterfeit items. Working with reputable vendors and implementing strict supplier qualification processes can minimize the likelihood of receiving compromised or counterfeit goods.
By prioritizing product safety and authenticity, companies can protect their reputation, ensure consumer trust, and maintain a high level of quality in their reverse supply chain system.
Environmental Impact
While a reverse supply chain system aims to reduce waste and promote sustainability, it is important to consider its environmental impact. The reverse flow of products involves transportation, processing, and disposal, all of which can contribute to environmental challenges.
One aspect to consider is the transportation of returned products. Transporting these items back to the appropriate processing centers or facilities can result in carbon emissions and energy consumption. Long-distance transportation of returns can increase the overall carbon footprint of the reverse supply chain system. To mitigate this impact, companies can focus on optimizing transportation routes, consolidating shipments, and utilizing more eco-friendly transportation options, such as electric vehicles or alternative fuel sources.
Another environmental consideration is the processing and recycling of returned products. Depending on the type of items being returned, there may be energy and resource requirements for recycling or remanufacturing processes. While recycling and remanufacturing can help divert products from landfills and conserve resources, they still require energy and may generate waste in the process. Companies should strive to minimize the environmental impact by adopting sustainable practices during processing, such as implementing energy-efficient technologies or using eco-friendly materials whenever possible.
Additionally, improper disposal of returned products can have negative environmental consequences. If products are not disposed of correctly, they may end up in landfills, potentially releasing harmful substances into the environment. Companies should prioritize proper disposal procedures, such as partnering with recycling facilities that adhere to strict environmental regulations and guidelines.
To counteract the environmental impact of a reverse supply chain system, companies can focus on implementing circular economy principles. This includes designing products with recyclability in mind, employing eco-friendly packaging materials, and encouraging consumers to participate in product take-back programs. By designing products for easy disassembly and incorporating recycled materials into new products, companies can reduce their reliance on virgin resources and minimize the overall environmental impact of the reverse supply chain system.
By investing in sustainable practices, collaborating with environmentally responsible partners, and continuously improving processes, companies can mitigate the environmental downsides of a reverse supply chain system. Striving for a balance between economic benefits and environmental sustainability is key to ensuring the long-term success and positive impact of the reverse supply chain system.
Conclusion
A reverse supply chain system offers numerous benefits, including cost savings, sustainability, improved customer loyalty, and optimized inventory management. However, it also comes with its downsides that require careful consideration and mitigation.
The increased complexity of managing the reverse flow of products necessitates efficient handling, coordination among stakeholders, and specialized knowledge for different product categories. Higher operational costs associated with additional resources, transportation, storage, and specialized equipment are challenges that should be addressed to maximize the potential benefits.
Managing multiple stakeholders can be challenging due to different priorities, systems, and communication channels. Effective communication and collaboration are vital to ensure smooth operations and customer satisfaction. Furthermore, there is a risk of product contamination or counterfeit items entering the supply chain, which requires rigorous inspection, testing, and collaboration with trusted partners.
Lastly, the environmental impact of a reverse supply chain system should not be overlooked. Optimization of transportation, adoption of sustainable practices in processing and recycling, and proper disposal procedures can help mitigate the environmental downsides.
In conclusion, while there are challenges to overcome, a well-implemented reverse supply chain system brings significant benefits to companies, the environment, and customer satisfaction. By addressing the downsides and implementing strategies to mitigate their impact, companies can unlock the full potential of a reverse supply chain system while minimizing costs, achieving sustainability goals, and fostering strong customer relationships. With careful planning, collaboration, and a commitment to continuous improvement, companies can shape a reverse supply chain system that provides a competitive advantage and contributes to a more sustainable and circular economy.