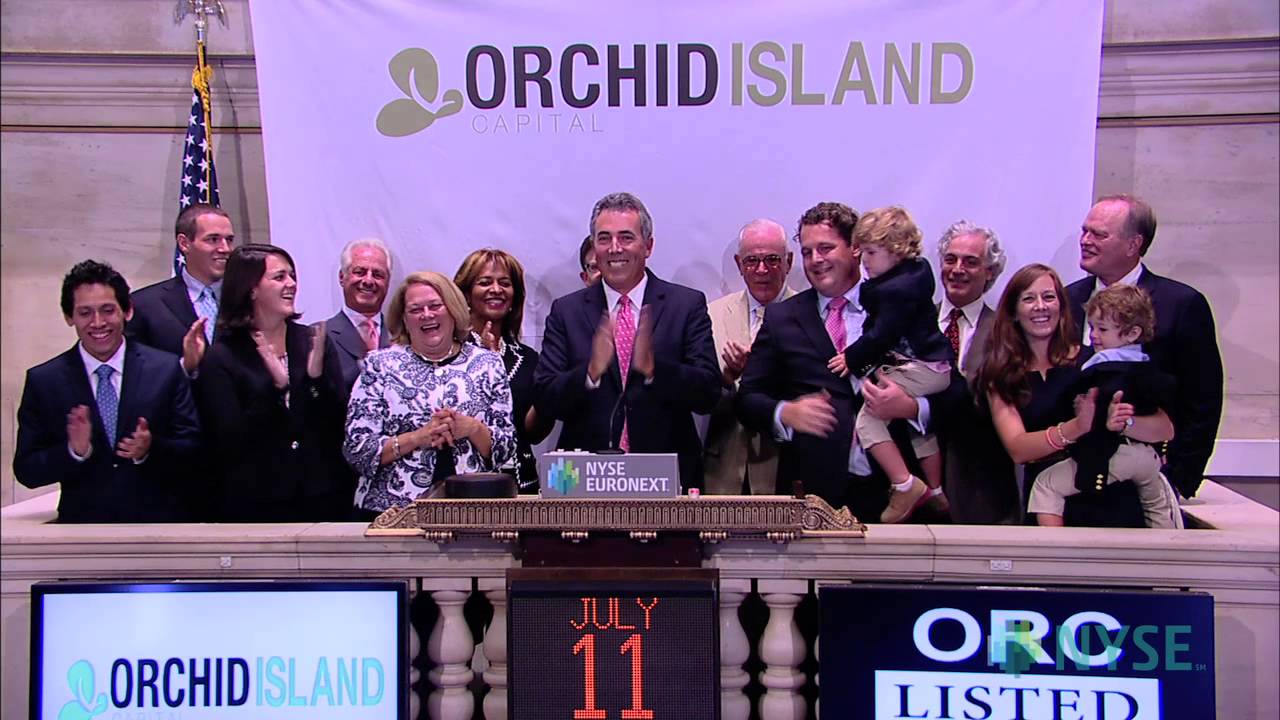
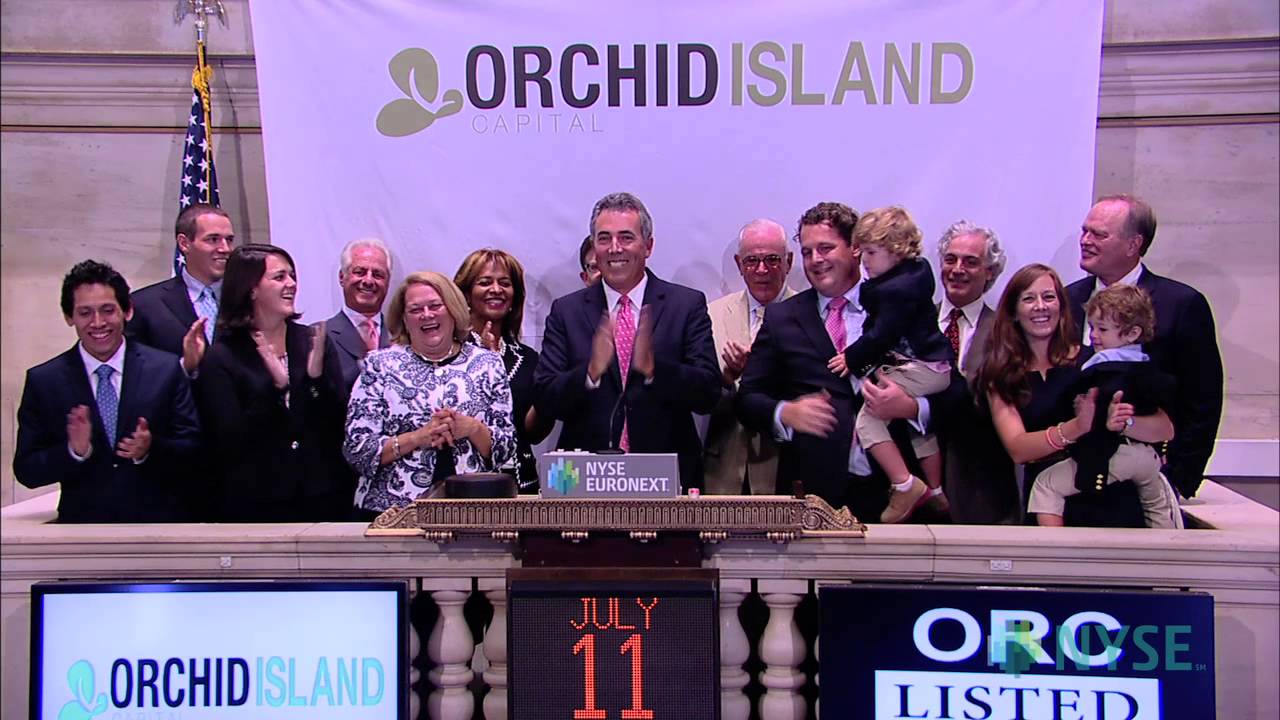
Finance
When Does ORC Pay Dividends?
Published: January 3, 2024
Discover when ORC pays dividends and maximize your financial gains. Explore the finance strategies that can help you make the most of your investment.
(Many of the links in this article redirect to a specific reviewed product. Your purchase of these products through affiliate links helps to generate commission for LiveWell, at no extra cost. Learn more)
Table of Contents
Introduction
Welcome to the world of ORC (Oxygen Reduction Reaction) dividends! In the realm of finance, dividends are a familiar concept, but when it comes to ORC, the dividends take on a whole new meaning. ORC refers to the process of converting chemical energy, often found in fuels like hydrogen or methanol, into electrical energy through the oxygen reduction reaction.
But when does ORC pay dividends? In other words, what are the factors that influence the efficiency and effectiveness of the ORC process? In this article, we will dive into the world of ORC dividends and explore the various factors that come into play.
Before we delve into the specifics, let’s briefly understand what the oxygen reduction reaction entails. The oxygen reduction reaction is a fundamental process that occurs at the cathode in a fuel cell. It involves the reduction of oxygen molecules to water, releasing energy in the form of an electrical current.
Now, let’s explore the factors that can significantly impact ORC dividends. Understanding these factors will not only increase our knowledge but also help us optimize the ORC process for maximum efficiency and productivity.
Understanding ORC (Oxygen Reduction Reaction)
ORC, also known as the oxygen reduction reaction, is a vital process that occurs in fuel cells. It plays a crucial role in converting the chemical energy stored in fuels such as hydrogen or methanol into electrical energy. This reaction takes place at the cathode of the fuel cell, where oxygen molecules are reduced to water, releasing electrons and generating an electrical current.
The ORC process involves several steps. First, oxygen molecules from the surrounding environment or an oxygen-supplying agent, such as air or a pure oxygen stream, are transported to the cathode of the fuel cell. At the cathode, these oxygen molecules encounter a catalyst, typically a material like platinum or palladium, which facilitates the reduction reaction.
Once at the catalyst surface, the oxygen molecules undergo a series of chemical reactions. The catalyst allows the oxygen molecules to dissociate into oxygen atoms and then bond with electrons from the electrode surface. The combination of oxygen atoms and electrons results in the formation of oxygen ions.
These oxygen ions then diffuse through the electrolyte, which is typically a polymer membrane or an aqueous solution. As they reach the anode of the fuel cell, they react with fuel molecules, such as hydrogen or methanol, in a separate process known as the fuel oxidation reaction. This reaction releases electrons, which travel through an external circuit, generating an electrical current that can be used to power electronic devices or recharge batteries.
The ORC process is highly efficient compared to traditional combustion methods, as it does not involve the release of harmful emissions such as carbon dioxide or pollutants. It offers a cleaner and more sustainable approach to energy conversion, making it a promising technology for various applications, including transportation, portable power systems, and stationary power generation.
Now that we have a basic understanding of ORC, let’s explore the factors that can influence the dividends generated from this process.
Factors Influencing ORC Dividends
Achieving optimal dividends from the ORC process is dependent on several factors that can influence its efficiency and effectiveness. These factors include:
- Temperature: The temperature at which the ORC process is conducted plays a significant role in its performance. Higher temperatures generally result in faster reaction rates and improved overall efficiency. However, extreme temperatures can also lead to catalyst degradation and electrolyte breakdown, compromising the long-term stability of the system.
- Catalyst Type: The choice of catalyst material is crucial for ORC performance. Catalysts such as platinum, palladium, and their alloys are commonly used due to their high catalytic activity. However, new catalyst materials are being developed to enhance performance and reduce costs. The selection of catalyst greatly impacts the ORC reaction kinetics and can significantly affect the overall efficiency of the process.
- Electrolyte Concentration: The concentration of the electrolyte solution in the fuel cell affects ion transport and the overall performance of the ORC process. Optimal electrolyte concentrations can ensure efficient ion exchange, promoting faster reaction rates and higher electrical output. However, extreme concentrations can lead to limitations in ion conductivity and system stability.
- System Pressure: The pressure at which the ORC process operates can influence its performance. Higher system pressures can enhance the mass transport of reactants and products, resulting in faster reaction rates and improved overall efficiency. However, excessive pressure levels can lead to increased system complexity and safety concerns.
- Current Density: The current density, or the amount of electrical current generated per unit area of the electrode surface, is essential for ORC performance. Higher current densities can increase power output, but they can also lead to higher voltage losses and reduced overall efficiency. Finding the right balance is crucial to maximize the dividends from the ORC process.
Additionally, the design of the fuel cell itself, including factors such as electrode structure, membrane thickness, and flow configuration, can also impact the efficiency of the ORC process. Optimizing these design parameters can enhance reactant distribution, improve mass transport, and reduce internal resistance, resulting in higher dividends.
Assessing and understanding these influencing factors is crucial for optimizing the ORC process and ensuring the maximum efficiency and productivity of fuel cells. By carefully considering and adjusting these parameters, researchers and engineers can unlock the true potential of ORC and contribute to the advancement of clean and sustainable energy solutions.
Temperature
The temperature at which the ORC process is conducted plays a crucial role in determining its efficiency and dividends. The effect of temperature on the ORC process can be seen in various aspects, including reaction kinetics, catalyst activity, and species transport. Understanding and controlling the temperature is vital for optimizing the performance of the ORC system.
Generally, higher temperatures result in faster reaction rates, as they increase the energy available for the chemical reactions to occur. The rate of the oxygen reduction reaction increases exponentially with temperature according to the Arrhenius equation. This means that even a small increase in temperature can significantly enhance the reaction rate and overall efficiency of the ORC process.
Temperature also influences the activity of the catalyst material used in the fuel cell. Most commonly, platinum-based catalysts are used in ORC systems due to their high catalytic activity. However, the effectiveness of these catalysts can be highly dependent on temperature. In certain temperature ranges, the catalyst’s activity can decrease, leading to reduced performance of the ORC process. Therefore, maintaining the optimal temperature is essential to maximize the catalyst’s effectiveness and achieve higher dividends.
In addition to reaction kinetics and catalyst activity, temperature affects species transport within the ORC system. At higher temperatures, the transport of reactants, such as oxygen and fuel, is facilitated due to increased molecular motion. This leads to faster diffusion and better access to reaction sites, resulting in improved overall performance.
However, it is important to note that extreme temperatures can have detrimental effects on the ORC system. Excessively high temperatures can lead to catalyst degradation, causing a loss in activity over time. Additionally, extremely low temperatures can slow down the reaction rates and negatively impact the overall efficiency of the ORC process.
Therefore, finding the optimal temperature range is crucial to balancing the benefits and limitations associated with temperature. This can be achieved through careful control and regulation of heating and cooling mechanisms in the fuel cell system. Maintaining a stable and controlled temperature not only enhances the performance of the ORC process but also ensures the longevity and reliability of the fuel cell system.
Overall, temperature plays a pivotal role in the ORC process, influencing reaction kinetics, catalyst activity, and species transport. By carefully managing temperature conditions, researchers and engineers can optimize the performance of fuel cells, maximize ORC dividends, and contribute to the development of sustainable energy solutions.
Catalyst Type
The choice of catalyst material is a critical factor that significantly impacts the efficiency and dividends of the ORC (Oxygen Reduction Reaction) process. The catalyst plays a crucial role in facilitating the reduction of oxygen molecules to water and improving the overall performance of the fuel cell.
One of the most commonly used catalyst materials for ORC is platinum (Pt) due to its high catalytic activity. Pt exhibits excellent electrochemical performance, promoting faster reaction rates and efficient electron transfer during the ORC process. Its ability to adsorb and dissociate oxygen molecules on its surface is essential for initiating and driving the reduction reaction.
However, platinum is an expensive and relatively scarce material, which limits its widespread use in fuel cells. As a result, researchers are actively exploring alternative catalyst materials that offer comparable performance at a lower cost. Some of these alternative catalysts include palladium (Pd), iridium (Ir), and various transition metal alloys.
Palladium, like platinum, displays excellent catalytic activity for the ORC process. It possesses a similar ability to adsorb and dissociate oxygen molecules, making it an effective catalyst. Palladium-based catalysts are also more abundant and cost-effective compared to platinum, providing a viable alternative for ORC applications.
Iridium, another precious metal, has also shown promising catalytic activity for the ORC process. Its high stability and ability to effectively reduce oxygen make it an attractive catalyst material. However, the high cost and limited availability of iridium limit its practical use in large-scale fuel cell applications.
In addition to single-metal catalysts, researchers are exploring the use of alloy catalysts to improve performance and cost-effectiveness. Catalysts such as platinum-palladium (Pt-Pd) and platinum-ruthenium (Pt-Ru) alloys exhibit enhanced catalytic activity and stability compared to pure platinum. These alloy catalysts can also promote oxygen adsorption and facilitate the reduction reaction more efficiently, resulting in improved ORC performance.
The choice of catalyst material depends on various factors, including performance requirements, cost considerations, and availability. Researchers continue to investigate and develop novel catalyst materials and structures to enhance the efficiency and effectiveness of the ORC process.
Overall, the catalyst type plays a crucial role in determining the dividends of the ORC process. The selection of an appropriate catalyst material can significantly impact the reaction kinetics and overall performance of the fuel cell. As research progresses, the development of new catalyst materials and innovative approaches will contribute to the advancement of ORC technology and its widespread adoption for clean and sustainable energy solutions.
Electrolyte Concentration
The concentration of the electrolyte solution in the fuel cell has a significant impact on the performance and dividends of the ORC (Oxygen Reduction Reaction) process. The electrolyte concentration affects various aspects of the ORC system, including ion transport, reaction kinetics, and overall efficiency.
Optimal electrolyte concentrations are crucial for facilitating efficient ion exchange, promoting faster reaction rates, and maximizing the electrical output of the fuel cell. The electrolyte serves as a medium for the transport of ions between the anode and cathode, facilitating the ORC process.
Low electrolyte concentrations can result in limited ion conductivity, hindering the movement of ions and slowing down the reaction rates. This can lead to reduced overall efficiency and lower dividends from the ORC process. On the other hand, excessively high electrolyte concentrations can increase the solution’s viscosity, impeding ion transport and decreasing the availability of reactants at the electrode surfaces.
By carefully adjusting the electrolyte concentration, researchers and engineers can optimize the ionic conductivity and ensure efficient species transport within the fuel cell. This can be achieved through the precise formulation and control of the electrolyte solution, considering factors such as the choice of electrolyte material, concentration gradients, and temperature.
In addition to promoting proper ion transport, the electrolyte concentration also affects the kinetics of the ORC process. The concentration of certain reactants, such as oxygen and fuel molecules, in the electrolyte solution can influence the reaction rates and the efficiency of the ORC process. Adequate concentrations of reactants are necessary to ensure a sufficient supply of species at the electrode surfaces for the reduction reaction to occur.
It is worth noting that the impact of electrolyte concentration can vary depending on the type of fuel cell architecture and electrolyte material used. For example, in direct methanol fuel cells (DMFCs), the concentration of methanol in the electrolyte solution directly affects the performance and power output of the fuel cell. Optimizing the methanol concentration is critical to achieving high dividends from the ORC process in DMFCs.
Overall, the concentration of the electrolyte solution plays a vital role in the ORC process. It affects ion transport, reaction kinetics, and overall efficiency. Finding the optimal electrolyte concentration involves careful consideration of factors such as ion conductivity, reactant availability, and system parameters. Through meticulous control of electrolyte concentration, researchers and engineers can enhance the performance of ORC systems, maximize dividends, and contribute to the advancement of clean and sustainable energy technologies.
System Pressure
The system pressure at which the ORC (Oxygen Reduction Reaction) process operates is a crucial factor that influences its performance and dividends. System pressure plays a significant role in various aspects of the ORC process, including reactant transport, mass transfer, and overall efficiency.
Higher system pressures can enhance the mass transport of reactants, such as oxygen and fuel molecules, within the fuel cell system. Increased pressure promotes faster diffusion and availability of reactants, leading to accelerated reaction rates and improved overall performance. This, in turn, results in higher dividends from the ORC process.
Moreover, elevated pressures facilitate efficient removal of reaction products from the electrode surfaces, preventing the accumulation of by-products that could hinder the reaction kinetics. Maintaining an optimal pressure level within the fuel cell system allows for continuous and effective reactant supply and removal, contributing to improved overall efficiency.
However, it is essential to strike a balance with system pressure, as excessively high pressures can lead to increased system complexity and safety concerns. Higher pressures may require stronger and more robust materials and components, which can add to the overall cost of the fuel cell system.
Furthermore, extreme pressure conditions may affect the stability and durability of catalyst materials and membranes used in the fuel cell. The choice of materials and design considerations must take into account the pressure range at which the ORC process operates to ensure the longevity and reliability of the system.
It is worth noting that the impact of system pressure can vary depending on the type of fuel cell and its specific requirements. For example, in certain types of fuel cells like proton exchange membrane fuel cells (PEMFCs), lower operating pressures are preferred to maintain the integrity of the membrane and minimize the risk of gas leakage.
Overall, system pressure plays a critical role in the ORC process, influencing reactant transport, mass transfer, and overall efficiency. Balancing pressure considerations is crucial to optimize the performance of the fuel cell system. Through careful design and control, researchers and engineers can leverage system pressure to maximize ORC dividends and contribute to the development of efficient and sustainable energy technologies.
Current Density
The current density, which represents the amount of electrical current generated per unit area of the electrode surface, is a critical factor that significantly influences the dividends of the ORC (Oxygen Reduction Reaction) process. It plays a key role in determining the power output and overall efficiency of the fuel cell system.
Higher current densities can lead to increased power output, as more electrons are transferred through the external circuit. This results in enhanced dividends from the ORC process. However, it is important to consider the trade-off between high current density and other factors such as voltage losses and system efficiency.
As the current density increases, the voltage losses within the fuel cell system also rise. Higher current densities can lead to higher overpotential losses, which limit the overall efficiency and reduce the dividends generated by the ORC process. Therefore, finding the optimal balance between current density and voltage losses is crucial for maximizing the overall performance of the fuel cell system.
Additionally, the choice of catalyst material and electrode design greatly impacts the maximum achievable current density. Catalysts with high electrochemical activity, such as platinum-based catalysts, are typically used to achieve higher current densities. The design of the electrode, which includes factors such as surface area, porosity, and catalyst loading, also affects the available reaction sites and the resulting current density.
It is worth noting that excessively high current densities can lead to increased temperature gradients and localized fuel starvation, limiting the overall performance of the ORC process. In contrast, very low current densities may not utilize the full potential of the fuel cell system, resulting in underutilization and reduced dividends.
The optimization of current density involves careful consideration of factors such as electrode design, catalyst selection, and system operating conditions. Researchers and engineers aim to find the right balance that allows for high power output and efficiency without sacrificing system stability and longevity.
Overall, current density plays a crucial role in determining the dividends generated from the ORC process. By carefully controlling and optimizing the current density, researchers and engineers can maximize the performance of the fuel cell system and contribute to the advancement of clean and sustainable energy technologies.
Effect of Fuel Cell Design
The design of the fuel cell system has a significant impact on the efficiency and dividends of the ORC (Oxygen Reduction Reaction) process. Various design parameters, including electrode structure, membrane thickness, flow configuration, and cell geometry, influence the performance and overall effectiveness of the fuel cell system.
One crucial aspect of fuel cell design is the electrode structure. The structure and composition of the electrodes, including the catalyst layer and gas diffusion layer, play a vital role in facilitating the ORC process. The electrode structure affects reactant distribution, gas diffusion pathways, and electrochemical reaction kinetics. Optimizing the electrode structure can improve reactant access to the reaction sites, enhance mass transport, and ultimately increase the dividends from the ORC process.
The thickness of the membrane, which separates the anode and cathode compartments, is another design parameter that impacts ORC performance. A thinner membrane provides lower resistance to ion transport and reduces voltage losses, leading to improved overall efficiency. However, thinner membranes may be more prone to flooding and require careful management of the water balance within the fuel cell system.
The flow configuration within the fuel cell, such as the type of fuel and oxidant flow, also affects the ORC process. Optimizing the flow distribution and ensuring efficient reactant transport enhances the contact between the electrodes and the reactants, promoting faster reaction rates and higher dividends.
Furthermore, the overall cell geometry can influence the performance of the fuel cell system. The shape and size of the fuel cell stack, as well as the arrangement of individual cells, impact factors such as reactant distribution, heat dissipation, and system packaging. A well-designed cell geometry can minimize pressure drops, improve thermal management, and enhance overall system performance.
The design of the reactant flow channels and the effective removal of reaction products also contribute to the effectiveness of the ORC process. Proper channel design ensures uniform reactant distribution, prevents fuel starvation, and facilitates efficient product removal, avoiding reactant crossover and potential performance degradation.
The optimization of fuel cell design parameters requires a comprehensive understanding of the ORC process, system requirements, and performance targets. Engineers and researchers continue to explore innovative approaches to fuel cell design, considering factors such as material selection, manufacturing techniques, and system integration to maximize ORC dividends.
In summary, the design of the fuel cell system plays a crucial role in determining the effectiveness of the ORC process. By optimizing parameters such as electrode structure, membrane thickness, flow configuration, and cell geometry, researchers and engineers can enhance reactant distribution, improve mass transport, and maximize the efficiency and dividends of the ORC process.
Assessing ORC Performance
Assessing the performance of the ORC (Oxygen Reduction Reaction) process is crucial for evaluating the efficiency and dividends of fuel cell systems. Several key performance metrics are used to evaluate the effectiveness of the ORC process and guide improvements in fuel cell technology.
One commonly used metric is the cell voltage, which represents the electrical potential difference between the anode and cathode of the fuel cell. Monitoring the cell voltage over time provides insights into the overall performance and stability of the ORC process. A high and stable cell voltage indicates efficient oxygen reduction and minimal voltage losses within the fuel cell system.
Power density is another important metric that quantifies the electrical power output per unit area of the electrode surface. It provides a measure of the ability of the ORC process to generate electrical energy. Higher power density indicates a more productive and efficient ORC process, resulting in increased dividends.
Efficiency is a fundamental metric used to assess the overall energy conversion efficiency of the ORC process. It is calculated by dividing the electrical power output by the total energy input, accounting for factors such as fuel consumption and reactant utilization. Higher efficiency indicates a more efficient conversion of chemical energy into electrical energy, resulting in increased dividends.
Stability is a critical factor in assessing the long-term performance and viability of the ORC process. Monitoring the stability of key performance metrics, such as cell voltage and power density, over extended periods provides insights into the durability and reliability of the fuel cell system.
In addition to these metrics, other performance parameters, such as reaction kinetics, reactant crossover, and internal resistance, are also considered when evaluating ORC performance. These parameters provide a more comprehensive understanding of the underlying processes and potential areas for improvement.
It is important to note that the assessment of ORC performance is not conducted in isolation but in comparison with industry standards and performance targets. Comparing the performance of different fuel cell systems and technologies allows for benchmarking and identifying areas for improvement and innovation.
Advanced characterization techniques, such as electrochemical impedance spectroscopy and cyclic voltammetry, are often employed to gain deeper insights into the ORC process. These techniques provide information about the kinetics, charge transfer, and mass transport processes occurring within the fuel cell system.
Overall, comprehensive assessment of ORC performance involves the monitoring of key metrics, such as cell voltage, power density, efficiency, and stability, coupled with advanced characterization techniques. By evaluating these metrics, researchers and engineers can gain valuable insights into the efficiency and effectiveness of the ORC process, leading to continuous improvement and the development of more efficient and sustainable fuel cell technologies.
Conclusion
The ORC (Oxygen Reduction Reaction) process plays a crucial role in the conversion of chemical energy into electrical energy in fuel cell systems. Maximizing the dividends from the ORC process requires a comprehensive understanding of the various factors that influence its efficiency and effectiveness.
Temperature, catalyst type, electrolyte concentration, system pressure, current density, and fuel cell design are among the key factors that significantly impact the performance of the ORC process.
Temperature affects reaction kinetics and catalyst activity, while catalyst type determines the effectiveness of the reduction reaction. Electrolyte concentration influences ion transport and species availability, while system pressure affects mass transport and reactant distribution. Current density plays a critical role in power output and efficiency, and fuel cell design impacts reactant utilization and system performance.
Evaluating the performance of the ORC process involves monitoring metrics such as cell voltage, power density, efficiency, and stability. Advanced characterization techniques provide deeper insights into the underlying processes and potential areas for improvement.
Ultimately, optimizing the performance of the ORC process requires a balance between the influencing factors and a thorough understanding of system requirements and performance targets. By continuously improving and refining these factors, researchers and engineers can develop more efficient and sustainable fuel cell technologies that contribute to the advancement of clean energy solutions.
In conclusion, the ORC process holds great promise for a wide range of applications, from transportation to power generation. Understanding and harnessing the factors that influence ORC dividends is vital for developing fuel cell systems that are highly efficient, reliable, and environmentally friendly.