Home>Finance>How Does PLM Relate To Supply Chain Risk Management?
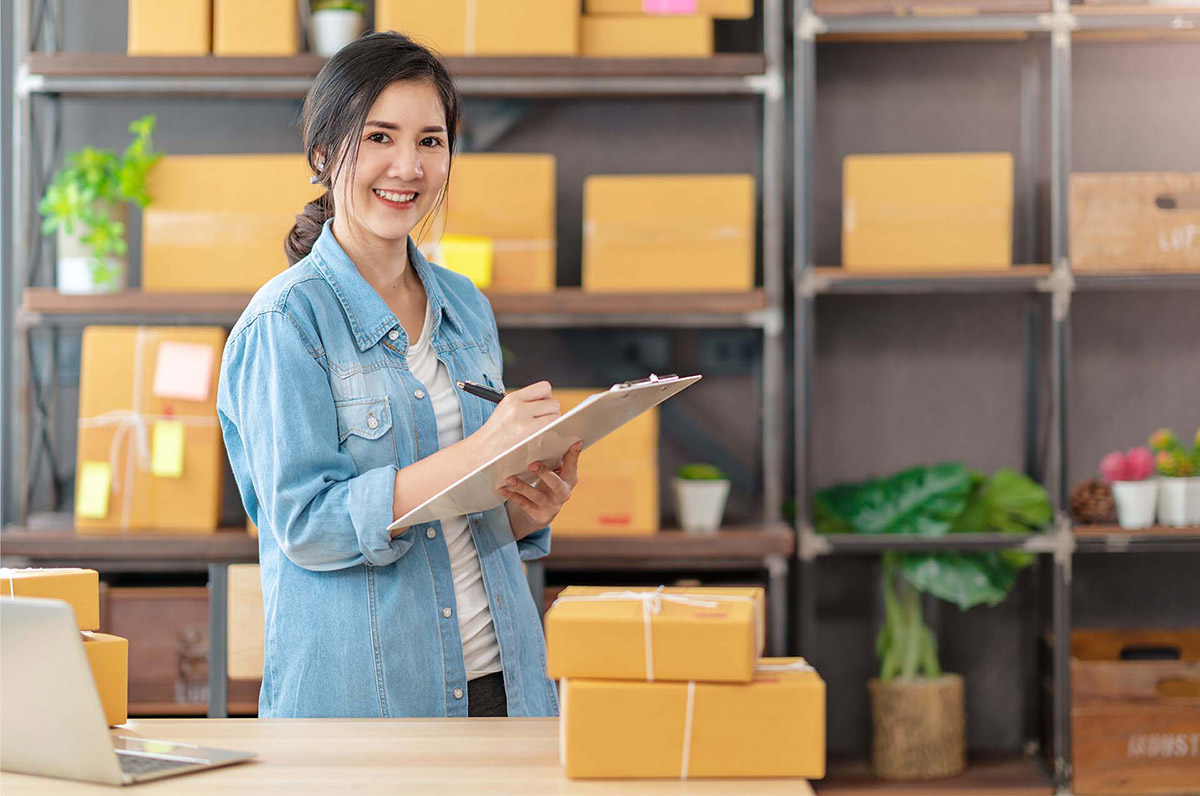
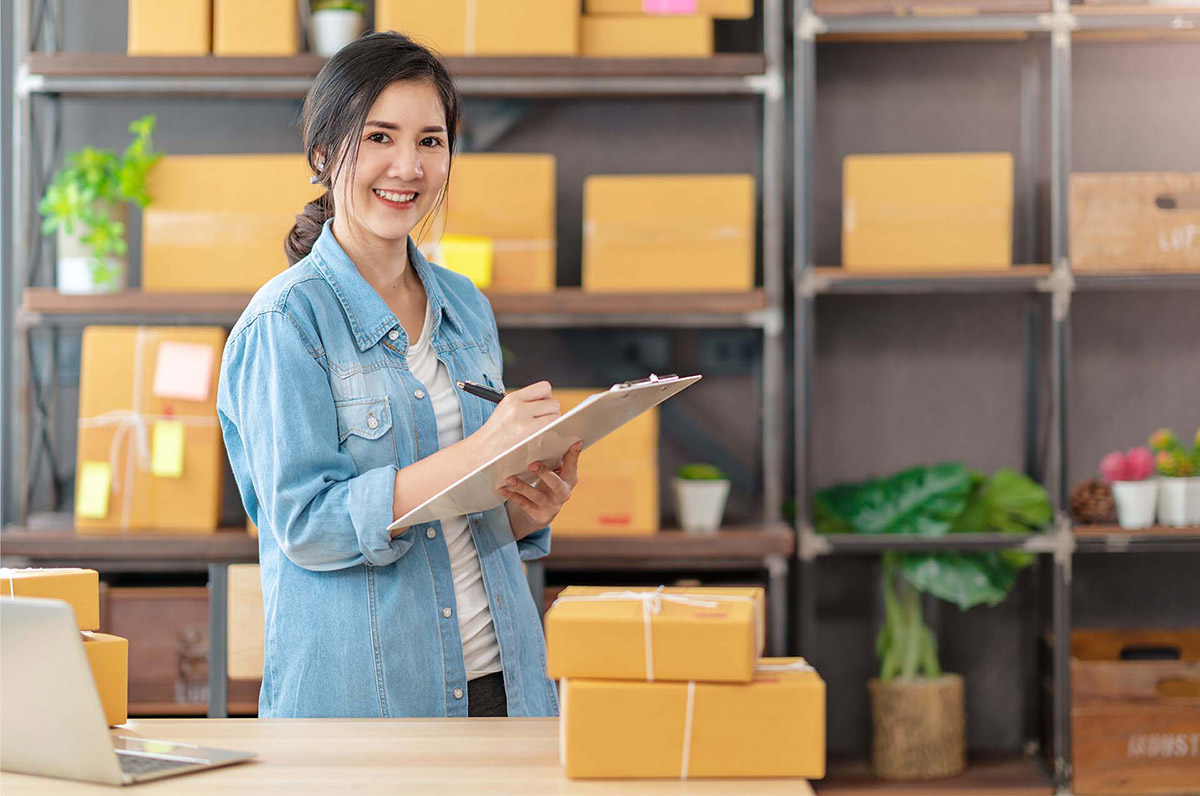
Finance
How Does PLM Relate To Supply Chain Risk Management?
Modified: December 29, 2023
Learn how PLM (Product Lifecycle Management) can help mitigate supply chain risk in the finance industry. Discover effective strategies for managing risk and optimizing financial operations.
(Many of the links in this article redirect to a specific reviewed product. Your purchase of these products through affiliate links helps to generate commission for LiveWell, at no extra cost. Learn more)
Table of Contents
- Introduction
- Definition of PLM
- Definition of Supply Chain Risk Management
- Importance of Supply Chain Risk Management
- Overview of PLM and Supply Chain Risk Management
- How PLM Supports Supply Chain Risk Management
- Benefits of Integrating PLM and Supply Chain Risk Management
- Case Studies on PLM and Supply Chain Risk Management
- Challenges and Limitations of Integrating PLM and Supply Chain Risk Management
- Strategies for Successful Integration of PLM and Supply Chain Risk Management
- Conclusion
Introduction
In today’s fast-paced and interconnected global economy, supply chain management has become increasingly crucial for businesses. Ensuring the smooth flow of products and materials across the supply chain is essential for meeting customer demands and maintaining a competitive edge. However, with the growing complexity of supply chains, the risk of disruptions and vulnerabilities has also increased.
Supply chain risk management (SCRM) is the proactive approach taken by organizations to identify, assess, and mitigate risks in their supply chains. It involves identifying potential risks, implementing risk mitigation strategies, and monitoring the supply chain for any emerging risks. The goal of SCRM is to minimize the impact of disruptions on operations, reduce costs, and maintain customer satisfaction.
Product Lifecycle Management (PLM) is a strategic business approach that focuses on managing the entire lifecycle of a product, from its design and development to its disposition. PLM software systems enable businesses to centralize and streamline product data, facilitate collaboration, and optimize processes. By integrating PLM with SCRM, companies can mitigate supply chain risks more effectively and ensure better overall product quality and reliability.
This article will delve into the relationship between PLM and SCRM, exploring how PLM supports SCRM efforts and the benefits and challenges of integrating the two. We will also examine real-world case studies highlighting successful implementations of PLM and SCRM integration and discuss strategies for achieving successful integration.
Definition of PLM
Product Lifecycle Management (PLM) is a strategic approach to managing all the information and activities related to a product throughout its lifecycle, from concept and design to manufacturing, distribution, and disposal. It encompasses all stages of a product’s lifecycle, including ideation, design, engineering, manufacturing, marketing, and maintenance.
PLM involves the use of software systems and tools to capture, manage, and share product-related data and documents across different departments and stakeholders. It provides a centralized platform for collaborating on product development, making informed decisions, and ensuring product quality and compliance.
PLM software facilitates the creation and organization of product data, including specifications, bills of materials, 3D models, technical drawings, and manufacturing instructions. It enables teams to collaborate effectively, track design changes, manage product configurations, and maintain a complete audit trail.
Key features of PLM systems include:
- Product Data Management (PDM): A central repository for storing and managing all product-related data, ensuring version control and traceability.
- Collaboration Tools: Communication and collaboration features that enable teams to work together, share information, and make collective decisions.
- Workflow Automation: Streamlining and automating product-related processes, such as change management, approvals, and documentation.
- Integration Capabilities: Integration with other enterprise systems, such as Enterprise Resource Planning (ERP) and Computer-Aided Design (CAD) tools, for seamless data exchange.
- Analytics and Reporting: Reporting and analytics capabilities to gain insights into product performance, identify bottlenecks, and drive continuous improvement.
By implementing a robust PLM solution, organizations can efficiently manage product-related data, streamline processes, reduce time-to-market, ensure regulatory compliance, and enhance collaboration across departments and external partners. PLM helps optimize the entire product lifecycle, from concept to disposal, resulting in improved product quality, cost savings, and increased customer satisfaction.
Definition of Supply Chain Risk Management
Supply Chain Risk Management (SCRM) is a proactive process that focuses on identifying, assessing, and mitigating risks within a company’s supply chain. It involves understanding the potential disruptions or vulnerabilities that could impact the flow of goods or services and developing strategies to minimize their impact.
SCRM involves the identification and evaluation of risks at all stages of the supply chain, including suppliers, manufacturers, distributors, logistics providers, and customers. Risks can arise from various sources, such as natural disasters, supplier failures, political unrest, economic fluctuations, quality issues, compliance violations, and cyber threats.
The primary objectives of SCRM are:
- Risk Identification: Identifying potential risks that could disrupt the supply chain operations and impact the delivery of goods or services.
- Risk Assessment: Evaluating the potential impact and likelihood of each identified risk to prioritize the allocation of resources for mitigation.
- Risk Mitigation: Developing strategies and implementing measures to reduce the likelihood and impact of identified risks. This could involve developing backup suppliers, diversifying the supply base, implementing business continuity plans, or strengthening supply chain visibility.
- Risk Monitoring: Continuously tracking and monitoring the supply chain for emerging risks, allowing for timely response and action.
- Risk Response: Implementing appropriate actions in response to identified risks, such as activating contingency plans, communicating with stakeholders, or adjusting inventory levels.
SCRM is crucial for maintaining the resilience and stability of the supply chain. By effectively managing supply chain risks, organizations can mitigate disruptions, minimize financial losses, maintain customer satisfaction, and uphold their reputation. Additionally, SCRM helps organizations comply with regulatory requirements, maintain supplier relationships, and optimize the overall efficiency of the supply chain.
It is important for companies to proactively integrate SCRM into their overall supply chain management strategy. By doing so, they can identify potential risks early on and develop suitable mitigation plans, allowing them to effectively minimize the impact of disruptions and maintain business continuity.
Importance of Supply Chain Risk Management
Supply chain risk management (SCRM) is of utmost importance in today’s dynamic and global business environment. The increasing complexity and interconnectedness of supply chains have made organizations vulnerable to various risks that can significantly impact their operations, financial performance, and reputation. Here are several key reasons why SCRM is essential:
- Minimizing Disruptions: SCRM helps identify and assess potential risks within the supply chain, allowing organizations to proactively implement measures to mitigate their impact. By understanding and planning for potential disruptions, companies can minimize the downtime and ensure a timely flow of goods and services.
- Protecting Financial Health: Supply chain disruptions can result in significant financial losses, including increased costs, lost sales, penalties, and reputational damage. SCRM enables organizations to identify and manage risks that could cause financial harm, ensuring the viability of their supply chain and protecting their bottom line.
- Enhancing Customer Satisfaction: Customers expect fast, reliable, and uninterrupted product delivery. Supply chain disruptions can lead to delays, stockouts, or inferior product quality, ultimately affecting customer satisfaction. Effective SCRM ensures that products are delivered on time and meet customer expectations, fostering loyalty and maintaining a competitive advantage.
- Ensuring Regulatory Compliance: Organizations operate in an increasingly regulated environment, with various industry and government compliance requirements. SCRM helps identify and mitigate risks related to compliance violations, such as supplier non-compliance, data security breaches, or environmental issues. By managing these risks, organizations can avoid costly penalties and legal consequences.
- Building Resilience: SCRM enables organizations to build a resilient supply chain that can withstand and recover from unexpected events. By developing contingency plans, implementing risk mitigation strategies, and fostering strong relationships with suppliers, organizations can respond effectively to disruptions and minimize their impact on operations.
- Improving Competitiveness: Organizations that effectively manage supply chain risks gain a competitive advantage. With a robust SCRM approach, companies can identify and capitalize on emerging opportunities, mitigate risks that competitors may overlook, and build a reputation for reliability and resilience.
Overall, the importance of SCRM lies in its ability to safeguard supply chains from disruptions, protect financial performance, enhance customer satisfaction, ensure compliance, build resilience, and improve competitiveness. By proactively managing risks, organizations can maintain a robust and flexible supply chain, enabling them to adapt to changing market conditions, enhance operational efficiency, and thrive in a volatile business landscape.
Overview of PLM and Supply Chain Risk Management
Product Lifecycle Management (PLM) and Supply Chain Risk Management (SCRM) are two distinct but interconnected disciplines that play critical roles in modern business operations. While PLM focuses on managing the entire lifecycle of a product, SCRM is dedicated to identifying and mitigating risks within the supply chain. By understanding the relationship between PLM and SCRM, organizations can unlock significant benefits and enhance their overall management strategies.
PLM encompasses processes, systems, and strategies for managing product data, collaboration, and workflow throughout a product’s lifecycle – from concept to disposal. It involves activities such as product design, prototyping, engineering, manufacturing, distribution, maintenance, and eventual retirement. PLM solutions enable organizations to centralize product information, streamline collaboration, track changes, and ensure regulatory compliance.
On the other hand, SCRM focuses on identifying, assessing, and mitigating risks throughout the entire supply chain network. It involves evaluating risks associated with suppliers, manufacturers, logistics providers, and customers, and developing strategies to minimize their impact. SCRM aims to ensure supply chain continuity, reduce vulnerabilities, and protect against disruptions that can negatively affect product delivery, financial performance, and customer satisfaction.
Both PLM and SCRM are critical for successful supply chain operations. PLM provides the foundation for effective product development and management, ensuring that products meet specifications, quality standards, and regulatory requirements. By integrating PLM and SCRM, organizations can align their product development and supply chain processes, resulting in improved overall performance.
When PLM and SCRM are integrated, the product information captured in the PLM system can be leveraged to identify potential supply chain risks. For example, by analyzing the design and engineering specifications stored in PLM, organizations can identify potential risks related to component availability, quality, or compliance. This helps in making informed decisions and mitigating risks before they impact the supply chain.
Furthermore, PLM systems can assist in managing changes and improvements to products to address supply chain risks. By using PLM’s change management capabilities, organizations can track and assess the impact of changes on the supply chain, evaluate alternative suppliers or materials, and ensure that all stakeholders are informed and engaged throughout the process. This integrated approach allows organizations to proactively address potential risks and maintain supply chain stability.
In summary, the integration of PLM and SCRM allows organizations to align their product development processes with supply chain risk management strategies. By leveraging PLM data and capabilities, organizations can identify, assess, and mitigate risks more effectively, ensuring product quality, supply chain continuity, and overall business success.
How PLM Supports Supply Chain Risk Management
Product Lifecycle Management (PLM) plays a crucial role in supporting effective Supply Chain Risk Management (SCRM) strategies. By leveraging the capabilities of PLM systems, organizations can enhance their SCRM efforts and mitigate risks within the supply chain. Here are some ways in which PLM supports SCRM:
- Centralized Product Data: PLM acts as a central repository for all product-related data, including specifications, bills of materials, design documents, and manufacturing instructions. This centralized data enables better visibility and traceability, helping organizations identify potential risks throughout the supply chain.
- Design for Supply Chain: PLM systems enable organizations to design products with the supply chain in mind. By considering factors such as component availability, lead time, and supplier capabilities during the product design phase, organizations can proactively address potential supply chain risks and improve overall resilience.
- Supplier Management: PLM systems can integrate supplier management functionalities, allowing organizations to evaluate, qualify, and manage their suppliers effectively. This includes tracking supplier performance, assessing their compliance with regulations and quality standards, and identifying potential risks associated with specific suppliers.
- Change Management: PLM facilitates efficient change management, ensuring that any updates or modifications to products are well-documented, communicated, and assessed for their impact on the supply chain. This helps organizations identify potential risks and develop appropriate mitigation plans before implementing changes.
- Product Documentation and Compliance: PLM systems assist in managing product documentation and compliance requirements, ensuring that all necessary certifications, testing records, and regulatory documents are captured and maintained. This helps organizations mitigate compliance-related risks and ensures that products meet industry standards and customer expectations.
- Collaboration and Communication: PLM fosters collaboration and communication among different stakeholders within the supply chain, including design teams, suppliers, manufacturers, and logistics providers. Improved collaboration helps identify and mitigate risks more effectively, enhance decision-making, and ensure that all parties are aligned in their understanding of potential risks.
- Root Cause Analysis: PLM systems enable organizations to conduct root cause analysis by tracing product-related issues or disruptions back to their source. This helps identify systemic issues within the supply chain and implement corrective actions to prevent similar risks and disruptions in the future.
By leveraging the capabilities of PLM systems, organizations can strengthen their SCRM efforts, enhance supply chain visibility, and proactively address potential risks. Integrating PLM and SCRM allows for a holistic approach to risk management, enabling organizations to identify, assess, and mitigate risks throughout the entire product lifecycle and supply chain network.
Benefits of Integrating PLM and Supply Chain Risk Management
Integrating Product Lifecycle Management (PLM) with Supply Chain Risk Management (SCRM) offers numerous benefits for organizations looking to optimize their product development processes and mitigate supply chain risks. Here are some of the key advantages of integrating PLM and SCRM:
- Enhanced Risk Identification: By integrating PLM and SCRM, organizations can leverage product data and insights captured within the PLM system to identify potential risks throughout the supply chain more effectively. This holistic view enables proactive risk identification, allowing organizations to develop appropriate mitigation strategies.
- Improved Risk Mitigation: The integration of PLM and SCRM allows organizations to implement targeted risk mitigation strategies. By aligning product design and development processes with supply chain risk considerations, organizations can mitigate risks at the root, reducing the likelihood of disruptions and vulnerabilities.
- Streamlined Change Management: Integrating PLM and SCRM facilitates a streamlined change management process. Organizations can assess the impact of product changes on the supply chain and proactively address potential risks associated with those changes. This enables efficient decision-making and ensures smooth implementation of product modifications.
- Optimized Supplier Management: Integration empowers organizations to effectively manage suppliers and evaluate their performance and capabilities. Organizations can assess supplier risks associated with quality issues, delivery delays, or non-compliance and take necessary actions to mitigate those risks. This enables better supplier collaboration and reduces the chances of supply chain disruptions.
- Increased Supply Chain Visibility: Integrating PLM and SCRM provides organizations with enhanced visibility into the supply chain. This visibility enables real-time monitoring of supplier performance, inventory levels, and potential risks, allowing organizations to proactively address issues and maintain supply chain continuity.
- Improved Collaboration: Integration promotes collaboration among different stakeholders involved in product development and supply chain management. With shared access to product data and risk information, teams can collaborate more effectively, share insights, and make informed decisions. This accelerates problem-solving, enhances coordination, and strengthens risk management capabilities across the supply chain.
- Cost Reduction: Integrating PLM and SCRM can lead to cost savings. By proactively identifying and addressing potential risks, organizations can prevent disruptions that could result in financial losses. Effective risk mitigation strategies reduce inventory carrying costs, expedited shipping expenses, and production delays, resulting in overall cost reduction.
- Enhanced Product Quality and Customer Satisfaction: The integration of PLM and SCRM contributes to improved product quality and customer satisfaction. By identifying and mitigating supply chain risks early in the product development process, organizations can ensure that products meet customer expectations. This results in higher customer satisfaction levels and strengthens the organization’s reputation in the market.
Integrating PLM and SCRM provides organizations with a holistic approach to risk management, enabling them to identify, assess, and mitigate risks throughout the product lifecycle and supply chain network. By leveraging product data, streamlining processes, and fostering collaboration, organizations can enhance their risk mitigation strategies, drive efficiency, reduce costs, and ultimately deliver superior products to customers.
Case Studies on PLM and Supply Chain Risk Management
Several organizations have successfully integrated Product Lifecycle Management (PLM) with Supply Chain Risk Management (SCRM), leading to improved risk mitigation strategies, enhanced supply chain resilience, and streamlined operations. Here are two case studies demonstrating the benefits of integrating PLM and SCRM:
- Case Study 1: Global Electronics Manufacturer
- Identify potential supply chain risks early in the product design phase by leveraging PLM’s centralized product data and incorporating risk assessment parameters.
- Capture and evaluate supplier performance data within the PLM system, allowing the organization to consolidate supplier information and assess their capability to manage risks.
- Implement automated change management workflows, enabling efficient assessment of risk impact and mitigation strategies when introducing design changes or modifying suppliers.
- Monitor supplier compliance by integrating regulatory requirements into the PLM system, ensuring adherence to quality and compliance standards.
- Case Study 2: Automotive OEM
- Identify potential risks related to new product designs by analyzing historical data stored in the PLM system, enabling them to make proactive decisions during the design phase.
- Optimize supplier selection and management by integrating supplier performance data with the PLM system, enabling a comprehensive evaluation of supplier capabilities, quality, and delivery reliability.
- Implement risk-driven change management processes, ensuring that any product or supply chain modifications consider potential risks and ensure continuity.
- Enhance collaboration with suppliers by providing them access to relevant PLM data, fostering real-time communication and information exchange.
A global electronics manufacturer integrated their PLM system with SCRM to mitigate supply chain risks and improve product quality and delivery. The integration enabled the organization to:
As a result of the integration, the company reduced supply chain disruptions, improved product quality, and streamlined collaboration with suppliers. By proactively identifying and managing risks through PLM and SCRM integration, they achieved higher customer satisfaction, increased market competitiveness, and better supply chain visibility.
An automotive Original Equipment Manufacturer (OEM) integrated PLM and SCRM to enhance their supply chain resilience and responsiveness to market demands. The integration allowed the company to:
The integration resulted in improved supply chain visibility, reduced disruptions, and enhanced supplier relationships. As a result, the OEM experienced faster time-to-market, cost savings through streamlined operations, and improved customer satisfaction by delivering high-quality products on time.
These case studies highlight the tangible benefits of integrating PLM and SCRM. By leveraging PLM’s capabilities and integrating them with SCRM, organizations can proactively identify supply chain risks, optimize supplier management, streamline change management, and enhance collaboration, resulting in increased resilience, improved product quality, and greater customer satisfaction.
Challenges and Limitations of Integrating PLM and Supply Chain Risk Management
While integrating Product Lifecycle Management (PLM) with Supply Chain Risk Management (SCRM) brings numerous benefits, there are also challenges and limitations that organizations may face. Understanding these challenges is essential for successful integration and implementation. Here are some key challenges and limitations:
- Complexity of Integration: Integrating PLM and SCRM involves aligning different systems, processes, and stakeholders across the organization. This integration requires careful planning, coordination, and investment in technology infrastructure, which can be complex and time-consuming.
- Data Quality and Consistency: Data integrity and consistency are crucial for effective integration. Ensuring that product data and risk information are accurate, up-to-date, and consistent across PLM and SCRM systems may pose challenges, especially when dealing with multiple data sources and legacy systems.
- Organizational Change Management: Integrating PLM and SCRM may require changes in organizational structure, roles, and processes. Resistance to change and lack of buy-in from stakeholders can hinder successful integration. Effective change management strategies and clear communication are essential to address these challenges.
- Integration Costs: Integrating PLM and SCRM involves financial costs, including investments in technology, training, and data management. Organizations should carefully assess the return on investment and develop a thorough cost-benefit analysis before embarking on integration efforts.
- Supplier Collaboration: Effective integration relies on collaboration with suppliers, who may have different systems, processes, and data management capabilities. Ensuring smooth data exchange and collaboration with suppliers can be challenging, particularly for organizations with a large and diverse supplier base.
- Data Security and Confidentiality: Integrating PLM and SCRM systems requires sharing sensitive product data and risk information across the organization and potentially with external stakeholders. Ensuring data security, confidentiality, and protection against unauthorized access can be a significant challenge that organizations need to address proactively.
- Dynamic Risk Landscape: The risk landscape is constantly evolving, with new risks emerging and existing risks evolving over time. Integrating PLM and SCRM requires organizations to stay updated with the latest risk trends and adapt their strategies accordingly to effectively address the dynamic nature of supply chain risks.
- Dependency on Technology: Integrating PLM and SCRM relies heavily on technology infrastructure and software systems. Technical issues, system downtime, or compatibility issues can pose challenges and disrupt the smooth functioning of integrated systems, highlighting the need for robust IT support and contingency plans.
Despite these challenges and limitations, the benefits of integrating PLM and SCRM can outweigh the challenges when properly addressed. Organizations should carefully plan and execute integration projects, engage stakeholders, invest in appropriate technology solutions, and continuously monitor and adapt their integrated systems to maximize the value and effectiveness of PLM-SCRM integration.
Strategies for Successful Integration of PLM and Supply Chain Risk Management
Successfully integrating Product Lifecycle Management (PLM) with Supply Chain Risk Management (SCRM) requires careful planning, coordination, and execution. Here are some strategies to ensure a successful integration:
- Define Clear Integration Goals: Clearly define the objectives and desired outcomes of integrating PLM and SCRM. Identify specific areas where integration can bring the most value, such as risk identification, change management, or supplier collaboration.
- Develop a Comprehensive Integration Plan: Create a detailed plan that outlines the integration process, including the timeline, tasks, responsibilities, and resource allocation. Ensure that the plan addresses both technical and organizational aspects of integration.
- Align Organizational Structure and Stakeholders: Evaluate the impact of integration on the organizational structure and roles. Ensure that stakeholders from different departments, including product development, supply chain, IT, and finance, are involved and aligned to support the integration effort.
- Invest in Robust and Scalable Technology: Select a PLM and SCRM solution that can seamlessly integrate, share data, and provide real-time visibility across systems. The chosen technology should be scalable to accommodate future growth and flexible to adapt to changing business needs and risk landscapes.
- Ensure Data Integrity and Consistency: Establish data governance practices to ensure the accuracy, consistency, and integrity of data across PLM and SCRM systems. Implement data validation processes, data cleansing strategies, and regular audits to maintain data quality.
- Prioritize Change Management: Develop a comprehensive change management strategy that includes clear communication, stakeholder engagement, and training programs. Ensure that employees understand the benefits of integration and are equipped with the necessary skills to navigate the integrated system.
- Promote Supplier Collaboration: Foster collaboration with suppliers by establishing clear communication channels, sharing relevant data, and aligning processes. Encourage suppliers to adopt compatible systems or provide guidelines for data exchange to enhance collaboration and enable better risk mitigation.
- Continuously Monitor and Evaluate: Regularly monitor and evaluate the integrated system’s performance, effectiveness, and alignment with the organization’s evolving needs. Incorporate feedback from stakeholders and make necessary adjustments to optimize the integration and maximize its benefits.
- Stay Updated and Adapt: Keep abreast of the latest industry trends, risk landscapes, and technological advancements. Continuously assess and update the integration strategy to incorporate emerging risks and leverage new technologies to improve risk management and supply chain resilience.
By following these strategies, organizations can overcome challenges and successfully integrate PLM and SCRM, leveraging the combined power of both disciplines to enhance risk management, optimize product development processes, and ensure a resilient and efficient supply chain.
Conclusion
Integrating Product Lifecycle Management (PLM) with Supply Chain Risk Management (SCRM) offers organizations a powerful approach to successfully navigate the complexities of product development and supply chain operations. By aligning these two disciplines, organizations can enhance risk identification, mitigation, and resilience across the entire product lifecycle and supply chain network.
PLM provides organizations with a centralized platform for managing product data, collaboration, and workflow, while SCRM focuses on identifying, assessing, and mitigating risks within the supply chain. When integrated effectively, PLM and SCRM enable organizations to proactively identify potential risks, optimize supplier management, streamline change management processes, and enhance collaboration with stakeholders.
The benefits of integrating PLM and SCRM are numerous. Organizations can effectively mitigate supply chain disruptions, reduce costs, improve product quality, enhance customer satisfaction, ensure regulatory compliance, and gain a competitive advantage. Furthermore, integration fosters better visibility, robust risk management strategies, and stronger collaboration across the supply chain ecosystem.
However, integration does come with challenges such as complexity, data consistency, organizational change management, and technology dependencies. To overcome these challenges, organizations should define clear integration goals, develop comprehensive plans, engage stakeholders, invest in suitable technology solutions, prioritize change management, and continuously monitor and adapt the integrated system to evolving needs.
In conclusion, integrating PLM and SCRM is a strategic approach that can enhance risk management capabilities, drive operational efficiency, and ultimately contribute to business success. By leveraging the strengths of both disciplines, organizations can optimize their product development processes, mitigate supply chain risks effectively, and build a resilient and future-ready supply chain.