Home>Finance>How To Calculate Average Inventory From Balance Sheet
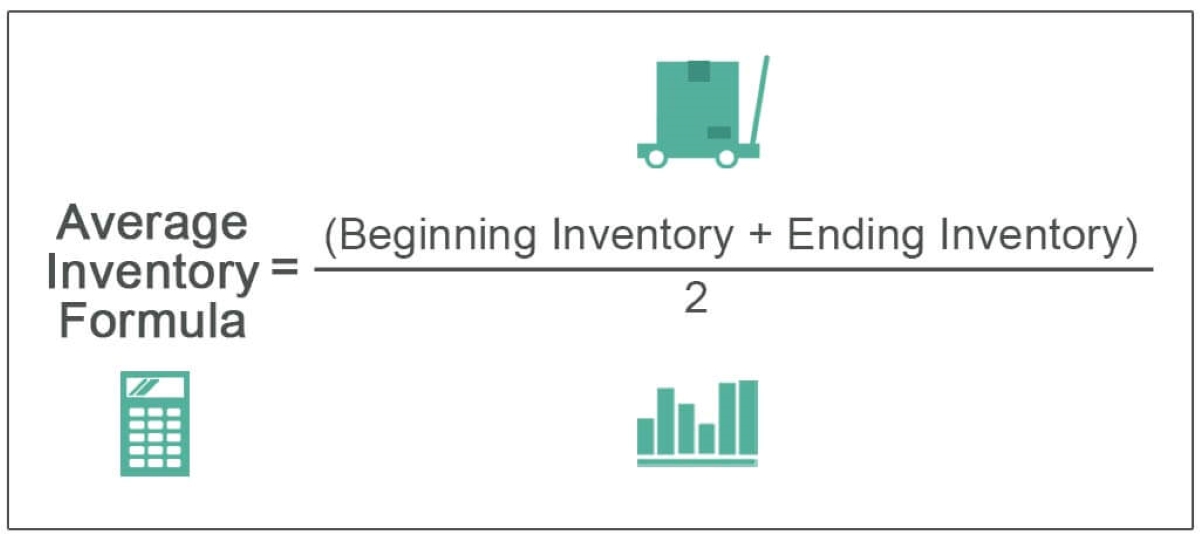
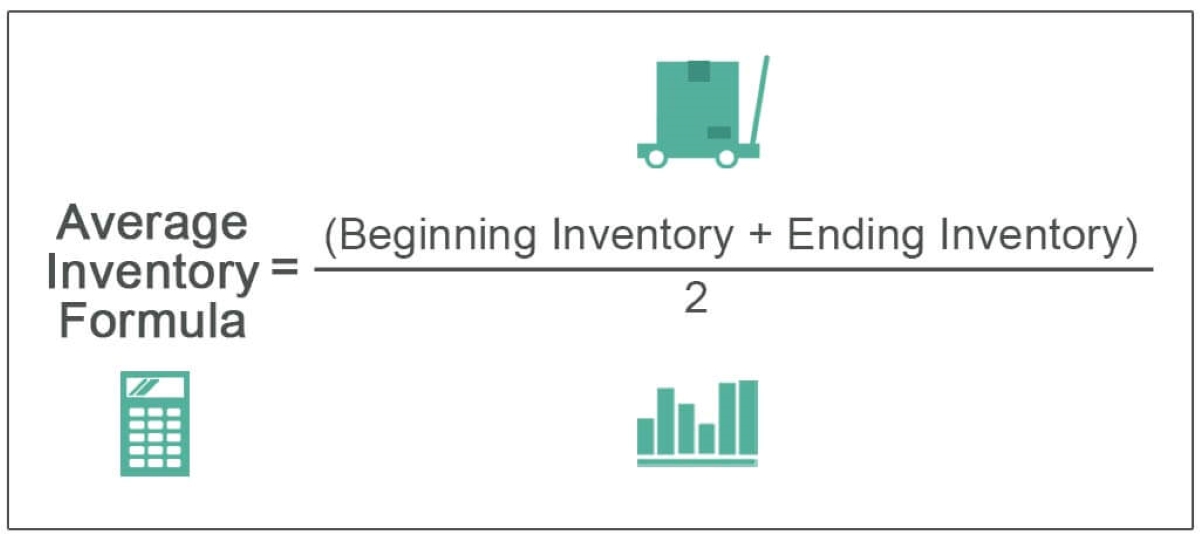
Finance
How To Calculate Average Inventory From Balance Sheet
Modified: December 30, 2023
Learn how to calculate average inventory from a balance sheet and improve your finance understanding.
(Many of the links in this article redirect to a specific reviewed product. Your purchase of these products through affiliate links helps to generate commission for LiveWell, at no extra cost. Learn more)
Table of Contents
Introduction
Welcome to the world of finance, where numbers and calculations dominate. In the realm of accounting, one crucial aspect of evaluating a company’s financial health is determining its inventory levels. The balance sheet, a key financial statement, provides valuable insights into a company’s assets, liabilities, and equity. Within the balance sheet, the average inventory plays a significant role in assessing a company’s inventory management efficiency.
So, what exactly is average inventory? In simple terms, it represents the average value of inventory held by a company during a specific period. It acts as a benchmark to evaluate the company’s inventory turnover rate and to gauge its ability to manage stock efficiently.
The calculations involved in determining average inventory can seem daunting, but fear not! In this article, we will guide you through the process step by step. We’ll break down the components of a balance sheet, explain how to determine the beginning and ending inventories, and provide an illustrative example to help solidify your understanding.
Understanding and calculating average inventory is crucial for both investors and management. Investors can use this information to assess the company’s ability to effectively manage its inventory and identify potential inefficiencies. For management, tracking average inventory aids in evaluating overall inventory performance and making informed decisions regarding purchasing, production, and pricing strategies.
Now, let’s dive deeper into the world of average inventory and discover its importance in evaluating a company’s financial health.
Definition of Average Inventory
Before we delve into the process of calculating average inventory, it’s important to have a clear understanding of what it represents. Average inventory refers to the average value of inventory held by a company over a specific period, usually a month, quarter, or year.
The calculation of average inventory involves taking into account the beginning inventory, ending inventory, and any changes in inventory levels during the specified period. By calculating the average inventory, we can gain insights into how effectively a company manages its inventory and determine its inventory turnover rate.
Inventory turnover rate, also known as inventory turnover ratio, is a measure of how quickly a company sells its inventory and replaces it with new stock. A high inventory turnover rate indicates efficient inventory management, as it implies that products are being sold quickly and that the company is not holding excessive inventory. On the other hand, a low inventory turnover rate may suggest that a business is facing challenges in selling its products or managing its inventory efficiently.
Calculating the average inventory provides a more accurate picture of a company’s inventory levels compared to using just the beginning or ending inventory. It helps to smooth out any fluctuations that may occur due to seasonal or irregular sales patterns.
By analyzing the average inventory, businesses can identify trends, manage their working capital effectively, and optimize their inventory levels. Additionally, investors can use the average inventory as a benchmark to compare a company’s inventory management performance against industry standards or competitors.
Now that we have a clear understanding of average inventory, let’s take a closer look at the components of a balance sheet, as they play a vital role in calculating average inventory.
Importance of Calculating Average Inventory
Calculating average inventory is essential for businesses and investors alike as it provides valuable insights into a company’s inventory management efficiency and financial performance. Understanding the importance of this calculation can help stakeholders make informed decisions and drive the success of a company. Here are some key reasons why calculating average inventory is crucial:
1. Evaluating Inventory Turnover: Average inventory helps businesses evaluate their inventory turnover rate, which is a measure of how quickly inventory is sold and replaced. A high turnover indicates efficient inventory management, while a low turnover can suggest excess inventory or slow sales. By calculating average inventory, companies gain a better understanding of their inventory turnover ratios, enabling them to identify potential inefficiencies, make strategic adjustments, and improve profitability.
2. Managing Working Capital: Inventory represents tied-up capital, as a significant portion of a company’s funds may be invested in maintaining stock levels. By calculating average inventory, businesses can optimize their working capital by ensuring their inventory levels are neither excessive nor inadequate. Maintaining optimal inventory levels helps companies minimize storage costs, reduce the risk of obsolete inventory, and enhance their cash flow.
3. Identifying Seasonal and Cyclical Patterns: Average inventory calculations can reveal seasonal and cyclical patterns in sales and demand. By analyzing the fluctuations in average inventory levels over time, businesses can plan their production, purchasing, and marketing strategies accordingly. This enables them to align their inventory levels with anticipated demand, preventing stockouts during peak periods and reducing excess inventory during slower periods.
4. Making Informed Pricing Decisions: Calculating average inventory helps businesses determine the true cost of goods sold (COGS) and can impact pricing decisions. By incorporating the average inventory value into COGS calculations, companies can ensure their product pricing covers the investment tied up in their inventory. This allows businesses to set competitive prices that account for their inventory costs and maximize profitability.
5. Benchmarking Performance: Average inventory provides a benchmark to compare a company’s inventory management performance against industry standards or competitors. By comparing their average inventory levels and turnover ratios with industry benchmarks, businesses can identify areas for improvement and implement best practices. This benchmarking process enables companies to stay competitive, streamline operations, and optimize their inventory management processes.
Overall, calculating average inventory provides valuable insights into a company’s inventory management efficiency, working capital management, and financial performance. By understanding and evaluating average inventory, businesses can make informed decisions, improve profitability, and gain a competitive edge in their respective industries.
Next, let’s explore the components of a balance sheet, which are essential for calculating average inventory.
Components of a Balance Sheet
A balance sheet is a financial statement that provides a snapshot of a company’s financial position at a specific point in time. It consists of three key components: assets, liabilities, and equity. Understanding these components is crucial for calculating average inventory, as they hold the necessary information related to a company’s inventory.
1. Assets: Assets represent everything that a company owns and can include tangible assets (such as inventory, property, and equipment) as well as intangible assets (such as patents and trademarks). Within the assets section of the balance sheet, we are particularly interested in the inventory, as it directly impacts the calculation of average inventory.
2. Liabilities: Liabilities are the debts and obligations that a company owes to external parties, including suppliers, lenders, and creditors. Examples of liabilities include accounts payable, loans payable, and accrued expenses. While liabilities are not directly involved in the calculation of average inventory, they are important for assessing a company’s overall financial health.
3. Equity: Equity represents the residual interest in the assets of a company after deducting its liabilities. It is often referred to as shareholders’ equity or net worth. Equity can be further broken down into retained earnings, common stock, and additional paid-in capital. The equity section of the balance sheet shows the ownership stake of shareholders and provides insights into the company’s financial stability.
By examining the assets section of the balance sheet, specifically the inventory accounts, we can determine the beginning and ending inventory levels required for calculating the average inventory.
In addition to the balance sheet components, it’s worth noting that the average inventory calculation may also be influenced by certain accounts within the income statement, such as the cost of goods sold (COGS) and purchases. These accounts provide information on the cost of inventory sold during the specified period and the value of additional inventory purchases made.
Now that we understand the components of a balance sheet, let’s move on to the process of determining the beginning and ending inventory, which are essential for calculating the average inventory.
Determining the Beginning Inventory
The beginning inventory is the value of inventory that a company has on hand at the start of a specific period, such as a month, quarter, or year. It is a critical component in calculating average inventory, as it establishes the baseline for tracking inventory changes over time.
There are various methods that businesses can use to determine the beginning inventory, depending on their accounting practices and the availability of inventory records. Here are three common methods:
1. Physical Count: The physical count method involves physically counting the inventory items on hand. This method is commonly used in businesses that have a limited number of inventory items and a relatively small inventory value. By physically counting the inventory, companies can determine the quantity and value of the inventory on hand at the start of the period.
2. Perpetual Inventory System: In a perpetual inventory system, businesses continuously track inventory levels using computerized systems or barcoding software. This system provides real-time updates on inventory quantities and values. To determine the beginning inventory, companies can simply refer to the inventory records at the start of the period.
3. Periodic Inventory System: In a periodic inventory system, businesses do not continuously track inventory levels. Instead, they conduct periodic physical counts to determine the inventory quantity and value. To find the beginning inventory, companies need to refer to the previous period’s ending inventory, as it carries over as the beginning inventory for the current period.
Once the beginning inventory value is established, it is recorded in the balance sheet as an asset. It serves as the starting point for calculating the average inventory and provides a baseline for measuring changes in inventory levels throughout the specified period.
It is important for businesses to ensure the accuracy and reliability of their beginning inventory determination method. Any errors or omissions in calculating the beginning inventory can affect the accuracy of the average inventory calculation and lead to inaccurate financial reporting.
Now that we have determined the beginning inventory, let’s explore how to determine the ending inventory, which is the other key component in calculating average inventory.
Determining the Ending Inventory
The ending inventory represents the value of inventory that a company has on hand at the end of a specific period. It is a crucial component in calculating average inventory and allows businesses to assess their inventory levels and make informed decisions about future production, purchasing, and pricing strategies.
Similar to determining the beginning inventory, there are multiple methods that businesses can use to determine the ending inventory. Here are three commonly employed methods:
1. Physical Count: The physical count method involves physically counting the inventory items at the end of the period. By physically counting the inventory, businesses can determine the quantity and value of the inventory on hand. This method is commonly used in businesses that have a limited number of inventory items and a relatively small inventory value.
2. Perpetual Inventory System: In a perpetual inventory system, companies continuously track inventory levels using computerized systems or barcoding software. By referring to the inventory records at the end of the period, businesses can obtain the accurate quantity and value of the inventory on hand. This method provides real-time updates and allows for precise determination of the ending inventory value.
3. Periodic Inventory System: In a periodic inventory system, businesses conduct a physical count at the end of the period to determine the inventory quantity and value. This method requires comparing the physical count to the beginning inventory and factoring in any purchases or changes in inventory levels during the period to calculate the ending inventory value.
Once the ending inventory value is determined, it is recorded in the balance sheet as an asset. It represents the value of inventory that a company carries over into the next period. By comparing the beginning and ending inventory values, businesses can compute the average inventory, which is an essential metric for evaluating inventory management efficiency.
Accurately determining the ending inventory is crucial for financial reporting and decision-making purposes. It ensures the accuracy of the average inventory calculation and enables businesses to calculate the cost of goods sold (COGS), assess inventory turnover, and make informed inventory management decisions.
Now that we have a clear understanding of how to determine the beginning and ending inventory, let’s move on to the calculation of average inventory.
Calculation of Average Inventory
Calculating average inventory allows businesses to assess their inventory management efficiency by determining the average value of inventory held during a specific period. The average inventory calculation takes into account the beginning inventory, ending inventory, and any changes in inventory levels that occur during the period.
The formula for calculating average inventory is as follows:
Average Inventory = (Beginning Inventory + Ending Inventory) / 2
To calculate the average inventory, businesses need to determine the beginning and ending inventory values. The beginning inventory is the value of inventory on hand at the start of the period, while the ending inventory is the value of inventory on hand at the end of the period.
Let’s break down the calculation into steps:
- Calculate the total value of the beginning inventory.
- Calculate the total value of the ending inventory.
- Sum the beginning inventory and ending inventory values.
- Divide the sum by 2 to get the average inventory.
By using this formula, businesses can obtain the average inventory value, which represents the average amount of inventory held during the specified period.
The average inventory value is crucial for various financial analyses and performance evaluations. It is used to calculate inventory turnover ratios, which measure how quickly a company sells and replaces its inventory. Additionally, the average inventory value enables businesses to assess the efficiency of their inventory management practices and make informed decisions regarding inventory control and cost optimization.
Now, let’s move on to an example calculation to illustrate the process of determining average inventory.
Example Calculation
Let’s walk through an example to illustrate how to calculate the average inventory using the formula mentioned earlier. Suppose we have a retail business that operates on a quarterly basis, and we want to determine the average inventory for the first quarter of the year.
At the beginning of the quarter (January 1st), the business had an inventory value of $50,000. As we come to the end of the first quarter (March 31st), the inventory value is $70,000. To calculate the average inventory, we’ll use the formula:
Average Inventory = (Beginning Inventory + Ending Inventory) / 2
Now let’s plug in the values:
Average Inventory = ($50,000 + $70,000) / 2
Average Inventory = $120,000 / 2
Average Inventory = $60,000
In this example, the average inventory for the first quarter is $60,000. This means that, on average, the business held $60,000 worth of inventory during that period.
Calculating the average inventory allows businesses to gain insights into their inventory management efficiency and assess their performance over a specific period. It provides a metric to evaluate the effectiveness of inventory turnover and aids in making informed decisions related to inventory control, ordering, and production planning.
It’s important to note that this is a simplified example, and in real-world scenarios, the calculation may involve more complex inventory valuation methods, such as the weighted average cost or specific identification. Furthermore, businesses may need to account for any changes in inventory levels throughout the period, such as purchases, sales, or returns.
Now that we have successfully calculated the average inventory, let’s explore the limitations of using this metric.
Limitations of Average Inventory Calculation
While calculating the average inventory can provide valuable insights into a company’s inventory management efficiency, it is important to be aware of its limitations. Understanding these limitations will enable businesses and investors to interpret the average inventory calculation accurately and make informed decisions. Here are some key limitations to consider:
1. Seasonal Variations: Average inventory does not take into account seasonal fluctuations in demand and inventory levels. If a business experiences significant seasonal variations in sales, calculating the average inventory may not reflect the true inventory levels during different periods of the year. Companies operating in seasonal industries should be cautious when relying solely on average inventory calculations for inventory management decisions.
2. Cost Variances: The average inventory calculation assumes a uniform value for all inventory items. However, in reality, inventory items may have different costs. Using a simple average may not accurately represent the value of inventory items. Some businesses opt for weighted average cost methods to overcome this limitation and calculate a more precise average inventory value.
3. Unusual Events or Changes: Average inventory calculations may not account for significant events or changes that occurred during the period, such as stockouts, product launches, or changes in production processes. These events can impact inventory levels and the accuracy of the average inventory calculation, especially if they are not evenly distributed throughout the period.
4. Inventory Turnover Variations: Average inventory alone does not provide information about inventory turnover patterns over time. While a high or low average inventory value may indicate potential issues in inventory management, it does not reveal the dynamics of inventory turnover during the period. Tracking inventory turnover ratios alongside average inventory can provide a more comprehensive understanding of inventory performance.
5. Market Conditions and External Factors: Average inventory calculations do not consider external factors such as changes in market demand, competition, or economic conditions. These factors can greatly influence inventory levels and management strategies. It is essential to consider these external factors when interpreting average inventory and making inventory-related decisions.
Despite these limitations, average inventory calculations remain a valuable tool for assessing inventory management efficiency and providing a baseline for comparison and decision-making. To mitigate these limitations, businesses should complement average inventory calculations with other inventory management tools and regularly assess their inventory performance in the context of their specific industry and market conditions.
Now that we understand the limitations of average inventory calculations, let’s conclude our discussion.
Conclusion
Calculating average inventory is a fundamental aspect of analyzing a company’s inventory management efficiency and financial performance. By determining the average value of inventory held during a specific period, businesses can gain insights into inventory turnover, working capital management, and decision-making processes.
In this article, we explored the components of a balance sheet, including assets, liabilities, and equity, which provide the necessary information for calculating average inventory. We also discussed the importance of calculating average inventory, such as evaluating inventory turnover, managing working capital, and benchmarking performance.
We highlighted the process of determining the beginning and ending inventory, discussing various methods such as physical counting, perpetual inventory systems, and periodic inventory systems. Additionally, we provided a step-by-step guide on how to calculate average inventory using the formula (Beginning Inventory + Ending Inventory) / 2.
However, it is crucial to acknowledge the limitations of average inventory calculations, such as seasonal variations, cost variances, unusual events or changes, inventory turnover variations, and external factors. By understanding these limitations, businesses and investors can make more informed interpretations of average inventory calculations and supplement them with additional analysis and considerations.
In conclusion, calculating average inventory is integral to evaluating a company’s inventory management efficiency and making informed decisions regarding inventory control, purchasing strategies, and pricing. It provides valuable insights into inventory turnover, working capital management, and financial performance. However, it is essential to consider the limitations and context-specific factors when interpreting average inventory calculations.
By leveraging the average inventory calculation along with other inventory management tools, businesses can optimize their inventory levels, improve profitability, and gain a competitive edge in their respective industries.
Thank you for joining us on this exploration of average inventory calculation. We hope this article has provided you with a comprehensive understanding of its significance and usage in the finance world.